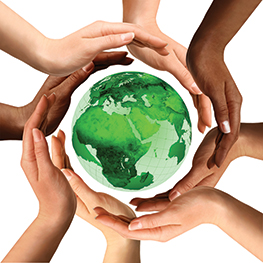
Operating and maintaining equipment in accordance with standards and recommended practices, especially in a global marketplace, can be a challenge. Many organizations produce standards, guidelines, and practices for safe design, operation, and maintenance of equipment, creating a cacophony of standards that often causes confusion.
Harmonization of standards — one of the societal themes of Vision 20/20 — aims to simplify equipment operation and maintenance by encouraging organizations to produce unified standards and practices. The quality of equipment operation and maintenance affects process safety, and improving process safety is a joint stakeholder responsibility. Companies, academia, and regulatory agencies need to work together to harmonize standards on a global level.
Streamlining the regulatory requirements for process safety and risk management is essential to eliminating redundancies, inefficiencies, and confusion. By developing standards that consider the global marketplace, we can improve understanding, use, and efficiency of standards.
Harmonization makes it easier for local, national, and global commerce to conform to applicable standards. Organizations that issue standards, guidelines, and practices should work jointly to align and streamline practices, eliminate redundancy, and cooperate to address emerging issues.
What Does It Mean?
- A variety of standards can apply to a single operation, including local, industry, national, and international standards, and some may conflict.
- Harmonized standards provide consistent guidance for design, operations, and maintenance to support effective understanding of process safety risk.
- It is important to communicate requirements consistently, whether that means down the street, across the country, or around the world.
What Is the Value?
- Harmonization ensures that users can efficiently conform to applicable standards in local, national, and global commerce.
- It supports a partnership to deliver great process safety performance.
What Can I Do?
- Recognize the diversity in standards, be open-minded, and work to harmonize standards.
- Promote harmonization by participating in standard and practice writing groups.
What Does It Look Like?
Harmonize equipment standards company-wide. Start by identifying the equipment used at different sites throughout your company. Determine the similar equipment that is used by multiple sites and collect the standards for that equipment from each site. Once you have collected the various standards for a type of equipment, create a unified standard that will appropriately address necessary information.
Harmonizing standards for all existing equipment can be daunting. Instead, identify a single type of critical equipment and harmonize the expectations for its design, operation, and maintenance. Consider starting with simple equipment that can provide a quick win.
Openly communicate updates to standards and practices across the company. After you establish standards, ensure project or operations management follow the requirements of the standards or seek approval to use alternatives from appropriate leadership. Make sure employees are aware and proficient on the standards and practices in their disciplines. Confirm that engineers and other personnel responsible for equipment design and integrity have access to the applicable standards, understand the content, and know how to apply it to their equipment and operations.
After the standard for a piece of equipment has been harmonized, be sure that the updated standard is accessable at all sites. As standards change over time, personnel should be made aware of changes and how they relate to current operations.
Stay informed as standards are updated by regulatory agencies. Standards, guidelines, and practices for safe design, operation, and maintenance of equipment may be updated by regulatory agencies. Be aware of the regulatory agencies your company is affected by and the standards that apply to your company. Check for updates to applicable standards and guidelines, so as changes are published, company standards can be updated to comply.
Copyright Permissions
Would you like to reuse content from CEP Magazine? It’s easy to request permission to reuse content. Simply click here to connect instantly to licensing services, where you can choose from a list of options regarding how you would like to reuse the desired content and complete the transaction.