Static mixers can efficiently and effectively accomplish an increasing number of process objectives, expanding the opportunities to apply them for process intensification.
Mixing is a common operation in the chemical process industries (CPI), and is critical to the success of many processes. The cost of poor mixing — in the form of lower yields, difficulties in process development and scaleup, and lost opportunities to commercialize new products — has been estimated to be in the billions of dollars (1). Improvements in mixing can enable the manufacture of new and better products, reduce the generation of unwanted byproducts, allow the use of smaller equipment, and reduce energy requirements.
In the 50 years since their commercial introduction, static mixers (also called motionless mixers) have become established throughout the CPI in numerous operations, including blending, phase contacting, chemical reaction, and heat transfer. Their low cost, small size, and lack of moving parts, as well as other performance characteristics, make their use advantageous in many instances. Over time, numerous designs have been developed to provide enhanced performance in a widening array of applications, such that static mixers should be routinely considered for process intensification of mixing-sensitive operations.
This article explains how static mixers work, describes the most common types of static mixing elements, and discusses how static mixers can be used in laminar- and turbulent-flow applications.
How static mixers work
The most common mixing apparatus is the agitated tank, which is used to accomplish a diverse array of process objectives. These dynamic agitators use rotating impellers to produce flow in the material to be mixed.
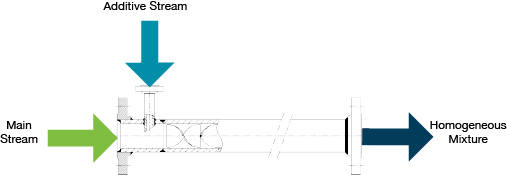
▲Figure 1. A common static mixer application is the blending of an additive into a stream to produce a homogeneous mixture. Although the elements do not move, there are energy requirements associated with static mixers, since they increase pressure drop relative to that of an open conduit, increasing pumping costs.
Conversely, static mixers (Figure 1) consist of stationary elements that are placed in a conduit to obstruct and direct the flow that is driven by another device, usually a pump. These stationary elements induce motion in the flowing fluid that is a function of element design and varies according to flow regime and process objectives.
In either case, the fluid motion caused by the mixing device, whether rotating impellers or static mixer elements, is responsible for achieving the desired mixing results.
When are static mixers the right choice?
Tank-mounted agitators are well-suited for use in batch and semibatch processes, while static mixers, because they are placed in conduits, are generally used in continuous processes. The advantages of static mixers can be realized in batch processing by connecting a static mixer pumparound loop to an agitated vessel.
While stirred tanks are a good option in many mixing operations, static mixers may often be a better choice. The large volumes of stirred tanks usually provide residence times on the order of hours, days, or even weeks. On the other hand, because most conduits have much smaller volumes, static mixers typically have residence times on the order of seconds or minutes. For products that degrade over time, long residence times should be avoided, making static mixers an attractive alternative to stirred tanks.
Additionally, the blending of material throughout a large stirred tank often requires minutes, making it difficult to achieve good performance when rapid mixing is required. This is the case when fast competitive reactions are being carried out, and in these applications static mixers that can achieve blending within seconds provide better performance.
In stirred tanks, energy is imparted to the agitated material via rotating impellers that typically occupy a small fraction of the vessel volume. This creates a broad distribution of energy dissipation rates throughout the vessel, with the dissipation rate in the impeller zone being orders of magnitude higher than the lowest energy dissipation rates. On the other hand, static mixers occupy a significant portion of the conduit volume and provide a significantly more uniform energy dissipation rate.
Similarly, stirred tanks have a wide range of residence times, and if poorly designed, stirred tanks are subject to the possibility of material bypassing the more-intense mixing in the impeller region or of material being trapped in sluggish or stagnant zones. Static mixers provide narrower residence time distributions that can create more-uniform product properties while also limiting the possibility of bypassing and stagnancy.
An open conduit with no mixing device is another alternative to static mixers. In laminar flow in open conduits, radial transport occurs solely by diffusive mechanisms, which translates to very slow rates of mixing and heat transfer, long conduit lengths, and broad residence time distributions. When flow is turbulent, some mixing processes can be accomplished in an open conduit; however, this may require an excessively long conduit, perhaps as long as hundreds of pipe diameters. In addition to extreme length, the slower mixing occurring in an open conduit can be detrimental when other processes (e.g., fast competitive reactions) occur faster than mixing.
Numerous static mixer element designs are commercially available, and a complete review would be quite extensive. This article focuses on four of the most widely used element types. Motivation for these element designs stems from two basic factors: the flow regime (laminar or turbulent) and the difficulty of the mixing task.
Routine tasks in laminar flow
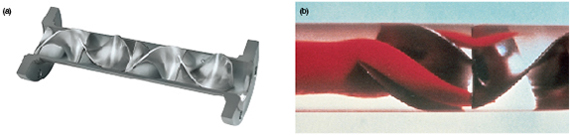
▲Figure 2. (a) Helical static mixer elements divide the flowing fluid into semicircular regions that are rotated and then recombined. (b) Fluid at the conduit centerline moves to the wall while fluid at the wall moves to the centerline.
One of the earliest commercial applications of static mixers used the helical elements shown in Figure 2 for the laminar mixing of materials with similar properties (helical elements are also used in the blending operation of Figure 1). Each element divides the flowing fluid into semicircular regions that are rotated and then recombined at the end of the element, where the next element divides the flow again. Each flow division is perpendicular to the preceding division and each rotation is in the direction opposite the preceding rotation. Passing miscible fluids through a series of elements creates striations of continually decreasing thickness. In creeping flow (Reynolds numbers less than about one), this reduction in striation thickness is the primary blending mechanism, until the striations are thin enough that molecular diffusion can aid in the elimination of composition variations. At higher Reynolds numbers, secondary flows develop that also impact the blending process.
The rotation that the elements impart to the flowing fluid causes radial redistribution of material. As shown in Figure 2b, fluid at the conduit centerline moves to the wall and fluid at the wall moves to the centerline; this exchange is completed over approximately every two elements in laminar flow. This behavior makes helical elements effective for thermal homogenization and heat-transfer enhancement.
In laminar flow in an open conduit, fluid remains on a streamline at a fixed radial location, and molecular diffusion, a slow process in viscous fluids, is the only mechanism for radial transport of mass and energy. Thus, use of static mixers can substantially increase the heat-transfer rate and reduce the required heat-transfer area. Additionally, in laminar flow in an open conduit, fluid near the centerline has significantly higher velocities than material near the conduit wall, creating a very broad distribution of residence times and thermal histories.
The radial redistribution provided by helical static mixer elements moves fluid back and forth between regions with higher and lower velocities, significantly narrowing the residence time distribution and providing a more uniform thermal history.
While helical static mixer elements promote blending and heat transfer in laminar flow, where accomplishing these operations is not easy, this performance comes with a price. Although designed to limit pressure drop, for Reynolds numbers less than ten, the pressure drop with helical static mixers is about six times that in an open conduit.
More-demanding tasks in laminar flow
Mixing tasks become progressively more difficult as differences in the physical properties, most notably viscosity and density, of the materials to be blended increase. Blending also becomes more difficult as the ratio of the materials’ flowrates increases.
To minimize their impact on pressure drop in laminar flow, the helical elements discussed previously occupy a small fraction of a conduit’s cross-sectional area. For difficult tasks such as uniformly blending a small amount of lowviscosity coloring agent into a high-viscosity polymer, lowpressure-drop elements such as helical elements allow the additive to snake through as...
Would you like to access the complete CEP Article?
No problem. You just have to complete the following steps.
You have completed 0 of 2 steps.
-
Log in
You must be logged in to view this content. Log in now.
-
AIChE Membership
You must be an AIChE member to view this article. Join now.
Copyright Permissions
Would you like to reuse content from CEP Magazine? It’s easy to request permission to reuse content. Simply click here to connect instantly to licensing services, where you can choose from a list of options regarding how you would like to reuse the desired content and complete the transaction.