This article is based on Baldea, M., T. F. Edgar, B. L. Stanley, and A. A. Kiss, “Modular Manufacturing Processes: Status, Challenges, and Opportunities,” AIChE Journal, doi: 10.1002/aic.15872, 63, pp. 4262–4272 (201
Most high-margin growth opportunities lie in high-grade specialty chemicals. To realize these opportunities, manufacturers are looking to distributed modular production facilities. Process intensification could help to enable these new technologies.
Two fundamental tenets have driven chemical engineering over the last century. The first is economy of scale — which reasons that constructing larger chemical plants improves capital efficiency and resource utilization, thereby reducing operating costs and product price, as well as increasing profit.
The second is unit operations — which are a consistent set of building blocks that can be used to design a plant. The unit operations framework was defined to provide method and structure to the synthesis and analysis of chemical plants, as well as a rational and systematic path for performing process design calculations. This framework was particularly critical when the slide rule, not the computer, was the dominant tool for performing calculations. While slide rules have become obsolete, unit operations remained the central paradigm in the design, simulation, and optimization of chemical processes.
These principles — economy of scale and unit operations — have not persisted without challenge. The concept of process intensification (PI), for example, has been around since the mid-20th century (1), but has received increased attention in the past two decades. The objective of PI is to design substantially smaller plants, while improving operational safety, environmental performance, and energy efficiency. The Rapid Advancement in Process Intensification Deployment (RAPID) Manufacturing Institute, supported by the U.S. Dept. of Energy (DOE), has recently placed the spotlight on PI in the U.S. RAPID’s aim is to target and promote major advances in energy efficiency and productivity in the process industries. It supports research on related topics ranging from PI fundamentals, modeling and simulation, and module manufacturing, to applications in chemical and commodity processing, natural gas upgrading, and renewable bioproducts.
PI challenges the conventional approach of “one unit, one operation” by combining multiple unit operations in the same physical device. Intensified systems minimize transfer and transport limitations by bringing multiple physical and chemical processes in close physical proximity. Phenomena such as catalytic reactions, for example, are governed by their intrinsic rates, rather than by diffusion through the catalyst structure. Intensified devices tend to be smaller and more efficient than their conventional counterparts. Smaller equipment also has safety advantages, such as minimizing the holdup of potentially harmful chemicals.
Physical dimensions often play an important role in the conception and construction of intensified systems, because some intensification approaches may only be viable at certain length scales. For example, the capacity of dividing-wall columns can typically be scaled effectively, but the height of microchannel-reactor channels cannot exceed a few millimeters without risking the occurrence of homogeneous reactions (i.e., combustion). This limits the processing capacity of individual intensified processes, although capacity can be increased by increasing the number of devices operating in parallel (i.e., numbering up) (1).
Numbering up indirectly challenges the established principle of economy of scale. Conventional scale-up techniques increase capacity by increasing the size of a device or process, while maintaining the basic design and function. Plant capacity can be chosen from a continuous range of sizes, but the optimal size typically requires a trade-off among market demand, capital expenditure, and operating cost. Numbering up affords only discrete choices of capacity, that is, the number of processing devices or modules must be an integer. In addition, facilities can expand their product portfolio by adding different modules that perform other functions.
Modularity is not entirely new to the chemical process industries (CPI). However, it is not nearly as prevalent as it is in other manufacturing sectors, such as electronics and automotive manufacturing. This article discusses the status of modular manufacturing developments, analyzes their role in the CPI, and identifies challenges and opportunities to guide progress. We categorize resources and markets in terms of a newly defined metric — value density — and argue that the opportunities for modular manufacturing are tied to this metric. Moreover, we posit that PI enables modular manufacturing, but is not a necessary condition.
What is a module?
Because unit operations are modules in their own right — deliberately standardized units that work together — the distinction between modules and unit operations can be fuzzy. In this article, we look beyond the conventional unit operations framework. For instance, modules based on process intensification may combine fundamental operations or tasks into a single piece of equipment (e.g., reactive distillation, spinning-disk reactors, membrane distillation, heat-integrated reactors, or advanced distillation columns) (2). While PI techniques and modular manufacturing can be used independently, it is beneficial to use them in concert: PI can be applied to various sections of a process, and then the PI solutions can be combined into modules (3).
We consider three categories of modularity as applied to CPI facilities: modular fabrication and construction, modular design, and modular manufacturing.
Modular fabrication and construction
Modular fabrication and construction is one of the first attempts at applying modularization principles to chemical processing. A single facility of annual capacity P is built from factory-preassembled blocks or modules (which are not necessarily identical). The preassembled modules are then interconnected in the field, which requires minimal effort compared to field-erected (i.e., stick-built) structures. These modules may comprise one conventional unit operation, several unit operations, or only part of a unit operation.
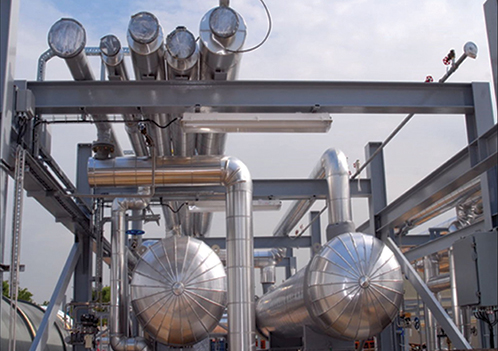
▲Figure 1. This module consisting of two heat exchangers is the size of a standard shipping container. The top of the module serves as a pipe rack.
Process design for a facility constructed of modules ensures that the functionality of the process is exactly the same as a conventional facility. Connections for piping, tubing, wiring, and control are all complete at the module level. Modules communicate via junction boxes for power and control wiring, and instrument air is fed from a header. In many cases, the pipe rack is integrated into the module, with the top portion of the module carrying the aforementioned ducts and piping (Figure 1).
The detailed engineering and mechanical design of each module should consider the module’s weight and dimensions, which are constrained by the intended transportation method and size of the installation location, the necessary strength of the frame materials to support the equipment weight, the need for a foundation, and other factors.
Modular construction offers several advantages that outweigh potential (or perceived) increases in upfront cost (4, 5).
Enhanced quality control and safety. Assembly in a factory setting allows control of factors that affect product quality and employee safety. Shop personnel are able to work in an environment with a controlled flow of personnel and materials, as well as access to overhead cranes; for example, most of the welding on a distillation tower can be performed with the column in the horizontal position, thereby avoiding elevated work. Personnel remain in a relatively small area and work is brought to their workstations. Workers become more familiar with this limited environment, including locations of tools, industrial gases, and electrical supply points needed to perform their jobs. Personnel also become more familiar with their coworkers and develop working relationships that promote safety and efficiency.
An employee in the field, however, must move around a construction site or plant environment to the work location, moving necessary equipment with them as well. Elevated work on scaffolds and work with mobile cranes are common, and carry inherent safety risks. Personnel may also be subjected to inclement weather conditions that could increase risk. Teams are frequently assembled for each individual job, which hinders workforce cohesion.
Capital cost savings. Modular units are less capital intensive, largely due to more-efficient labor. For many projects, large portions of the capital costs are related to welding. A welder in a shop is considerably more efficient than a welder in the field because a shop welder can remain in the same location, completing welding tasks for a majority of their time. In 2016, in the Houston area, a productive hour for a welder (i.e., one weld on a 6-in. Schedule 40 carbon steel pipe) cost about $50. The cost of field fabrication is typically at least twice that of shop fabrication, and could increase by up to a factor of six, depending on the skill level and availability of the workers.
Material cost savings. Modules can require extra steel, but in most cases, the cost is offset by eliminating the need for a foundation. Pipe racks built into the modules also help to minimize costs by reducing the amount of piping required at the plant level.
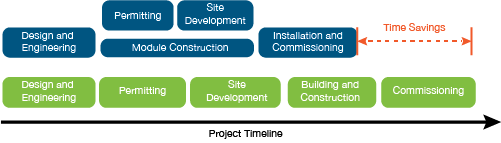
▲Figure 2. The timeline for a modular construction project (blue) is shorter than the timeline for a conventional construction project (green), which helps to save time.
Deployment cost and project timeline savings. Assembling modules requires fewer hours of skilled labor than building a plant in the field (Figure 2). The amount of work that can be performed in the shop relative to the field varies from project to project, but shifting the majority of the work into the shop can have significant benefits, especially when qualified labor and expertise are in short supply.
For a typical modular-construction refinery project, for example, about 65% of the labor is performed in the shop. Considering the labor savings and the economics of these initial stages, the total cost of a project can be reduced by about 30%. Projects that employ extensive modularization can be completed faster. For example, a project that would typically take three years can be completed in about two years, enabling an early startup, reducing overhead costs, and shortening the financing period.
Transportation is one of the challenges of modular construction. As module size increases, so do the logistic difficulties of delivering modules to the plant site. Furthermore, modules may require more upfront engineering than conventional unit operations. Modules that are ordered from external fabricators typically require very detailed design packages (5).
Modular construction can be applied to almost any part or type of plant. The literature provides numerous examples of modular construction, including catalytic cracking units (6), steam methane reformers (4), landfill gas processing plants (6), petrochemical facilities (6), and chlor-alkali plants (7).
The constraints of...
Would you like to access the complete CEP Article?
No problem. You just have to complete the following steps.
You have completed 0 of 2 steps.
-
Log in
You must be logged in to view this content. Log in now.
-
AIChE Membership
You must be an AIChE member to view this article. Join now.
Copyright Permissions
Would you like to reuse content from CEP Magazine? It’s easy to request permission to reuse content. Simply click here to connect instantly to licensing services, where you can choose from a list of options regarding how you would like to reuse the desired content and complete the transaction.