Global demand for crude oil was 96 million bpd in 2016, and the International Energy Agency forecasts demand to grow by 0.6% annually through 2040. As sweet crude oil stocks deplete, the average quality of crude oil is becoming more sour, with sulfur content greater than 0.5%.
While sulfur content in crude oil is increasing, many countries are requiring that sulfur levels in on-road diesel fuel be limited to 15 ppm or less. Furthermore, the presence of sulfur, even at levels as low as 1 ppm, can poison the catalysts used in fuel cells, as well as hydrogenation and gas-to-liquid conversion processes.
Stringent sulfur requirements present a major technological and economic challenge for both the petroleum refining and chemicals industries. According to some estimates, desulfurization makes diesel fuel between $0.40 and $0.60 per gallon more expensive than gasoline.
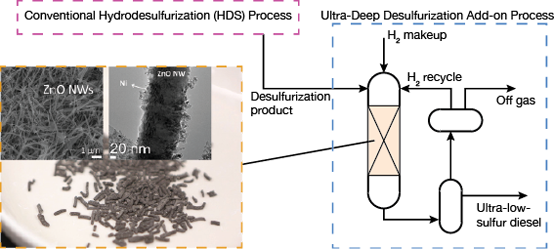
▲ Nickel nanoparticles are loaded onto zinc oxide (ZnO) nanowires to form catalytic adsorbents. Refineries can install a polishing step that uses these catalysts to reduce ultra-deep desulfurization costs and the environment impact of diesel production.
Crude-oil-derived fuels contain aromatic compounds such as thiophene and its derivatives, which are forms of sulfur that are difficult to remove. Hydrodesulfurization (HDS) is a catalytic chemical process used to remove sulfur from refined petroleum products. Typical catalysts used in HDS include sulfided Ni-Mo and Co-Mo active components supported on alumina. Traditional HDS processes create H2S gas that needs to be scrubbed downstream.
To produce ultra-low sulfur diesel, HDS must be run at high temperatures and pressures (i.e., 320–400°C, 30–80 bar), but these operating conditions cause traditional catalysts to lose activity over time because of sintering.
With funding from the National Science Foundation (NSF), Advanced Energy Materials (AdEM), a Univ. of Louisville, KY-based startup, is commercializing nanowire-based catalysts and adsorbents. Researchers at the startup have developed two catalytic adsorbents — AdE-Sorb and AdE-Sulfur — for ultra-deep desulfurization of diesel. Ultra-deep desulfurization reduces the sulfur content in diesel to less than 15 ppm. These adsorbents consist of clusters of catalytic metals, such as Ni, supported on zinc oxide (ZnO) nanowires.
The metallic clusters act as a catalyst to remove sulfur from aromatics. Sulfur that is adsorbed by the metal clusters is transferred to the ZnO nanowires, allowing the clusters to remain in a zerovalent state. The desulfurization reaction can only occur when the metallic clusters are in a zerovalent state.
Using a continuous, drymanufacturing process, researchers convert zinc metal to ZnO nanowires by exposing the zinc to a plasma-hydrocarbon flame. The company is now producing 50 kg/day of ZnO nanowires and expects to increase production to 1 ton/day by January 2018.
To produce the catalytic adsorbents, researchers load the nanowires with active metals, mix them with binder, and then extrude the mixture to achieve a high crush strength. The resulting nanowire-based catalyst can reduce the sulfur content of fuels from 200 ppm to 1 ppm, even under mild temperatures and pressures (i.e., 220–290°C, 15–30 bar). In addition, the process does not generate H2S.
The company’s AdE-Sorb catalyst can remove sulfur in diesel at atmospheric pressure without hydrogen. This option could be useful for small-to-medium-scale refineries that do not have access to a hydrogen supply.
Existing refineries could add the AdE-Sulfur ultra-deep HDS process as a polishing step to reduce sulfur content to less than 5 ppm. For a refinery with a capacity of 6,000 bpd, the process would cost $0.036/gal or less.
Using AdE-Sorb, desulfurization without hydrogen would cost $0.034/gal and reduce sulfur content of diesel from 600 ppm to less than 15 ppm for a 6,000-bpd refinery. In addition, this process would reduce CO2 emissions by about 320 tons/day. Independent Oil Corp. in Canada has recently tested this process in one of its pilot facilities.
This technology was funded through the NSF Small Business Innovation Research Program.
This article was prepared by the National Science Foundation in partnership with CEP.
Copyright Permissions
Would you like to reuse content from CEP Magazine? It’s easy to request permission to reuse content. Simply click here to connect instantly to licensing services, where you can choose from a list of options regarding how you would like to reuse the desired content and complete the transaction.