Use advanced scheduling and enterprise resource planning applications to optimize your manufacturing schedule and improve profitability, operational efficiency, and sustainability.
Production scheduling focuses primarily on fulfilling customer orders on time. However, how customer orders are fulfilled can have a significant impact on profitability, operational efficiency, and sustainability. The way in which production scheduling is implemented can also help increase energy efficiency and optimize the use of production equipment in chemical process industries (CPI) facilities.
Advanced production scheduling (APS) software and applications use advanced mathematical algorithms and logic to perform optimization and/or simulation in order to solve scheduling problems. APS simultaneously considers a range of constraints and business rules and provides planning, scheduling, and decision support (1). And, it integrates smart manufacturing principles and technologies to help schedule production.
APS offers many benefits when it is used for complex production systems that handle a range of products and that have significant changeover times and significant variation in demand. Simpler production-scheduling applications may suffice for less-complex systems, such as discrete manufacturing processes, eliminating the need to undertake a time-consuming or expensive project associated with APS.
This article describes the benefits of production scheduling, such as improved overall equipment effectiveness (OEE), reduced changeover and startup times, and improved supply chain analysis. It also discusses the integration of APS with enterprise resource planning (ERP), load leveling, and preventive maintenance. The scheduling improvements suggested in this article are based on our experience with production scheduling, supply chain optimization, and other operations management activities at Rohm and Haas Co. The article concludes with a discussion of that company’s approaches to production scheduling.
How to approach production scheduling
Before initiating a project to improve production scheduling, consider the potential benefits, which will be related to the complexity of the production scheduling method that is implemented. There are three general methods to improve production scheduling in a facility:
- Perform an analysis along the lines of Lean Six Sigma to develop standard operating procedures (SOPs) and associated training to assist personnel in making manual scheduling changes. Benefits to this method include: standardization, which reduces variations; bottleneck identification; shorter changeover times; less-complex shutdown and startup; less downtime; and higher product quality. Product changeover time and costs can be minimized, which makes a pull scheduling system — in which manufacturing starts only after a customer’s order is received — more effective.
- Develop or purchase applications that are not complex. Certain production scheduling applications designed for less-complex systems are available. Examples include production scheduling modules within an ERP system and a computerized maintenance management system (CMMS). In addition, simulation of the production process can allow improvements to be made to reliability, availability, and maintainability.
- Develop or purchase APS applications. For complex production systems that could reap substantial benefits, this option is worth investigating.
Batch vs. continuous processing. In the chemical industry, there are several key differences between scheduling for batch and continuous production processes. Continuous processes operate 24 hours a day, seven days a week, except for occasional downtime for maintenance. And, they often require substantial time and energy for equipment shutdown and startup. However, these processes are often energy-intensive, so the potential energy savings are also large.
Batch process equipment shutdown and startup can vary significantly depending on the process. But, they typically take less time to start up and consume less energy than equipment in continuous processes.
Enterprise resource planning overview
ERP manages core business processes and information — such as marketing data, sales forecasts, purchase orders, and inventory data — in real time to aid production. It is often facilitated by software or a suite of integrated applications. ERP can reduce the occurrence of production schedule interruptions because a product is out of stock, for example, due to fluctuation in demand.
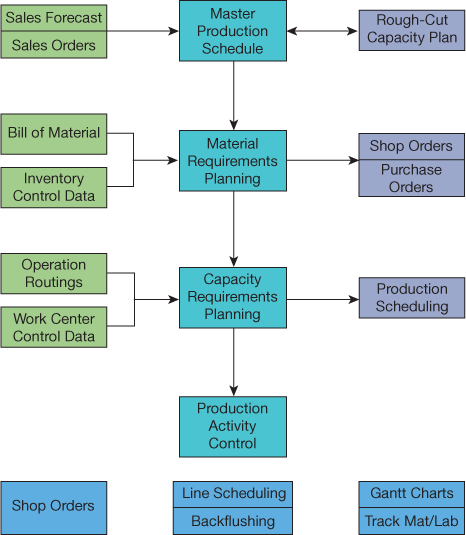
▲Figure 1. Production scheduling can be integrated with enterprise resource planning (ERP). This ERP flowchart includes many modules that receive continuous updates. The primary modules that can be enhanced with advanced production scheduling (APS) include material requirements planning, sales forecast, and sales orders.
Figure 1 is a typical ERP flowsheet (2). The master production schedule (MPS) represents the products the company plans to produce expressed in specific configurations, quantities, and dates. Material requirements planning (MRP) uses bill of material data, inventory data, and the MPS to calculate required amounts of materials and create purchase orders and shop orders based on those results. Capacity requirements planning (CRP) uses rough-cut capacity loading to calculate work center operation start and finish dates by job. CRP ensures that the production schedule is appropriate for the capacity of the facility.
Using the CRP data, the ERP system determines the production schedule and implements production activity control (PAC), the purpose of which is to:
- release manufacturing orders or production schedules
- issue materials consumed in the production process
- post labor time consumed in the production process
- track work in progress and report finished production
- take measurements to evaluate profitability and productivity.
ERP can also generate work order packets and perform line scheduling and backflushing. Additional applications that track materials consumed and labor time can be provided with the production schedule Gantt charts. Tracking labor time may only be required for facilities where demand and products can have variable labor requirements.
An ERP system can help avoid lower productivity and profitability due to:
- poor inventory control resulting in shortages and oversupplies of raw materials and finished goods
- poor material and capacity planning resulting in long lead times and late deliveries
- poor workforce planning resulting in erratic labor requirements and excessive overtime costs.
Many types of supply chain energy savings can be achieved using ERP. For example, reducing the amount of inventory stored on-site can help reduce required warehouse space and energy required to light, heat, and cool that warehouse space. Reduced inventory can also reduce working capital and free up cash for investment in the business.
ERP can help optimize the supply chain — for example, by organizing product shipping locations related to customer locations and transporting goods in full trucks rather than partial loads. Optimizing the supply chain can also help reduce the risk of input material shortages, which often create idle time. Supply chain optimization and inventory reduction are further explored later in this article.
There are opportunities to employ ERP to improve sales forecasting using big data and analytics, which can enhance demand planning. ERP-integrated production scheduling can be appropriate, but is not as sophisticated as the APS needed by many facilities.
Advanced production scheduling
The benefits of deploying APS include:
- resource and materials management
- energy management
- higher overall equipment effectiveness
- more effective demand side management
- higher capacity utilization
- more efficient maintenance scheduling
- optimal equipment loading.
APS relies on a suite of technologies that implement smart manufacturing (3). Smart manufacturing is the application of networked data and information technologies, and includes advanced sensors, controls, platforms, and modeling for manufacturing (4).
The APS system depicted in Figure 2 interacts with ERP. ERP provides the order plan based on the many analyses illustrated in Figure 1. APS then performs the...
Would you like to access the complete CEP Article?
No problem. You just have to complete the following steps.
You have completed 0 of 2 steps.
-
Log in
You must be logged in to view this content. Log in now.
-
AIChE Membership
You must be an AIChE member to view this article. Join now.
Copyright Permissions
Would you like to reuse content from CEP Magazine? It’s easy to request permission to reuse content. Simply click here to connect instantly to licensing services, where you can choose from a list of options regarding how you would like to reuse the desired content and complete the transaction.