
The August 2018 Beacon described an incident involving a runaway reaction in a batch reactor that occurred because of agitator failure. During normal operation, the reactor needed cooling to maintain the required temperature. However, the batch involved in the incident did not require cooling but, instead, heating. The process was acting notably different, but nobody noticed or took action to investigate the abnormal behavior.
A refinery explosion in Texas City in 2005 followed a similar pattern, in which the process was acting abnormally but no one noticed or intervened. A distillation column was overfilled and overpressurized (Images 1 and 2). Flammable hydrocarbons were released through a relief valve, which discharged to a stack (Image 3). The flammable vapor cloud ignited. Material was being fed to the column, while no material was being removed (Image 4), but the level instrument indicated the column level was decreasing. The level instrument had not failed, but was operating beyond its design range. (The March 2007 Beacon offers more details on this incident and why this level instrument gave an incorrect reading.)
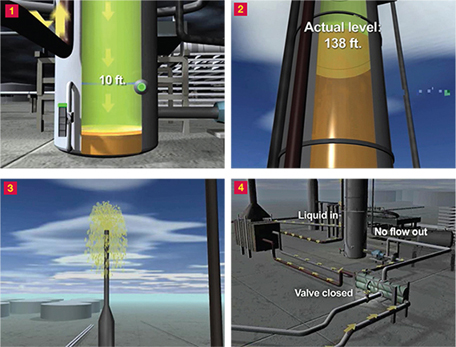
In another similar case, a batch specialty chemical process included a batch distillation step to remove a reaction byproduct. This step normally took about 10 hours. The temperature at the top of the column indicated the completion of the distillation, and once it reached a specified value, the process could proceed to the next step. The temperature sensor failed during one batch. The column top temperature indicator incorrectly indicated the completion temperature in only 15 minutes. The process continued to the next step, but nobody questioned the unusual behavior. Fortunately, there were no safety consequences, but the batch had to be discarded.
Did You Know?
When you work in a plant, you learn a lot about how it normally behaves. You get to know the length of time it takes to complete various process steps, the amount of heating or cooling that is required for a particular step, the level change in various vessels when material transfers from one place to another, the color of materials through a sightglass, the normal sound and look of the plant, as well as hundreds of other factors that you can see and experience as you complete your daily tasks. If you observe something you think is abnormal based on your past experiences, something has likely changed, and it is possible the change is hazardous.
What Can You Do?
- Be observant. Learn how your plant normally behaves and look for differences.
- If you observe any kind of unusual behavior in your plant, speak up. Investigate the unusual behavior to determine if it is a symptom of a hazardous condition or a change in the integrity status of the equipment. Work with management to fix any problems.
- Read the December 2015 Beacon for more examples of hazardous incidents that were avoided because somebody reported an abnormal situation, as well as some examples of unusual things to look for at work.
Report and investigate unusual process behavior!
©AIChE 2018. All rights reserved. Reproduction for non-commercial, educational purposes is encouraged. However, reproduction for any commercial purpose without express written consent of AIChE is strictly prohibited. Contact us at ccps_beacon@aiche.org or 646-495-1371.
Copyright Permissions
Would you like to reuse content from CEP Magazine? It’s easy to request permission to reuse content. Simply click here to connect instantly to licensing services, where you can choose from a list of options regarding how you would like to reuse the desired content and complete the transaction.