Batch tolling facilities can use process safety management techniques to meet regulatory standards and minimize risks.
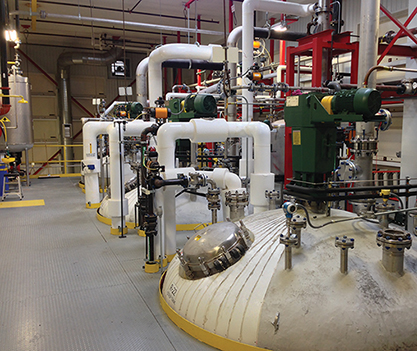
▲Figure 1. A batch tolling facility, or toller, manufactures many products for its customers. The toller must be able to safely and efficiently change between processes.
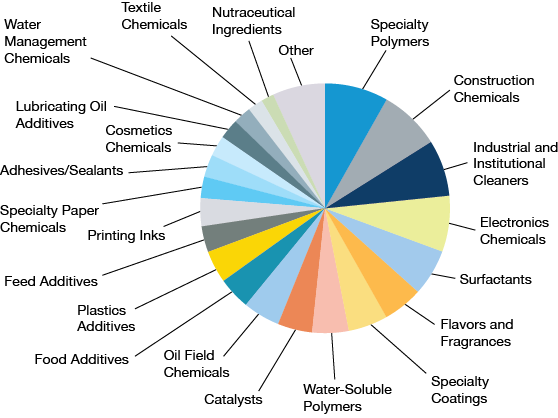
▲Figure 2. A variety of specialty chemicals can be manufactured via batch or semibatch processing. This pie chart shows the relative global consumption in 2014 of various specialty chemicals manufactured via these processes.
Operations in the chemical process industries (CPI) can be run in continuous, semibatch, or batch mode (Figure 1). In 2014, $345.5 billion in specialty chemicals were manufactured via batch or semibatch processing (Figure 2) (1).
Batch processing can be used when demand for a product is too low to justify manufacturing it continuously, or when batch operations will deliver better product quality than a continuous process. Batch processing can also be more practical for multistep processes, to maximize product yield and reduce waste (1).
Batch tolling
Batch processing may be handled by a manufacturer in-house, or outsourced to a batch tolling facility (also known as a toller), which manufactures products for customers based on their specifications. Customers may decide to use toll manufacturing for a variety of reasons:
- to increase production capacity
- to save money (when outsourcing costs are less than the cost to produce on-site)
- to make a new product (when the customer does not have the required equipment or processing capacity)
- to avoid taking on the risk of manufacturing a product.
Customers provide tollers with the desired product and quality specifications, including the type and quantity of raw materials, batch time, temperatures, pressures, flowrates, and other critical process parameters that are required to produce the product.
For toll manufacturers to remain competitive, they must be able to produce new products quickly while maintaining the flexibility required to produce existing products and accommodate future products from various customers. Toll processors must handle continually changing products, raw materials, processing conditions, chemical hazards, and manufacturing equipment. A product may be run in one vessel or multiple vessels, or may require the use of different or additional equipment.
Because of this continual change, toll facilities can face a higher potential for adverse chemical reactions and chemical and equipment incompatibilities. Industry experience has shown that a facility must review chemical reactive hazards and the potential for runaway reactions in batch operations. If left unexamined, these issues can lead to serious process safety incidents (2, 3, 4).
A chemical process may also be subject to many different environmental, health, and safety (EHS) regulations. One regulation batch tollers may be subject to is the Occupational Safety and Health Administration’s (OSHA’s) Process Safety Management (PSM) regulation to manage hazardous chemicals and prevent their release. PSM is made up of 14 elements that each facility must comply with, but it is a performance-based regulation. This means that, although companies must meet PSM requirements, how they comply with the regulations is at their discretion.
Meeting PSM requirements can be difficult when working with any type of process, but batch-tolling operations must also properly manage a changing slate of products, raw materials, hazards, and processing conditions. This article examines some best practices for managing PSM for batch-tolling operations, focusing on three of the PSM elements and some of the challenges that each poses. Examples show how one toller has successfully addressed PSM challenges.
Process safety information
One of the PSM elements that is critical to batch tolling operations is process safety information (PSI). As defined by OSHA in PSM regulation 29 CFR 1910.119 (d), PSI includes information pertaining to:
- highly hazardous chemicals used in the process; this information can include, but is not limited to, toxicity, physical, chemical, reactivity, and corrosivity data as well as personal exposure limits
- process technology, such as block or process flow diagrams, process chemistry, safe upper and lower process limits, and explanations of the consequences of deviating from those limits
- process equipment, such as materials of construction, piping and instrumentation diagrams (P&IDs), information on relief-system design and basis, and mass and energy balances for all relevant processes at the facility.
Screening process
Because tollers have a constant influx of new and varying products being manufactured alongside existing products, it is critical that any batch tolling facility review the new products and associated PSI closely to determine whether it can even produce the new product safely at the facility.
This review, or screening process, must include a review of raw materials and their associated chemical hazards. The review must also examine data for the compatibility of those chemicals with the equipment that will be used to run the process. Failure to perform this screening carefully could result in a catastrophic incident.
To evaluate the PSI and determine whether they can safely manufacture a new product, or make changes to an existing product, tollers must obtain relevant product and process information from its prospective customer, including:
- chemical reactions and any subsequent side reactions involved in the process
- safety data sheets (SDSs) and other pertinent information relating to chemical hazards (e.g., combustible dust information) for raw materials and the final product
- reaction kinetics and stability data
- analytical methods
- process and quality specifications for the raw material and final product.
Once the toll manufacturer has acquired all of the required process information and other critical information, it must use the information to screen the new product to determine not only the hazards that may be associated with the product, but also whether manufacturing that product is technically and economically feasible. The screening is performed in phases: a Level 1 evaluation, a process lab study, and a Level 2 evaluation.
In the Level 1 phase of the process safety evaluation, on-site lab and safety personnel determine whether the product can be used safely in the lab to perform a process lab study. If the product cannot make it through a Level 1 screening, it cannot be produced at the facility.
After this initial screening, the process lab study examines the reaction(s) in the process to determine whether the process can be scaled to a trial batch or to full production. This study will also look at the economics of production. Once the product passes the lab study, or if the facility already has documented experience with this product, screening moves to the next phase, Level 2.
The Level 2 screening involves site safety and process engineering personnel, who perform a full assessment of the product. This assessment uses the results from the process lab study to determine whether existing plant equipment can manufacture the product within the guidelines established by the facility’s environmental permits and any other facility processing constraints.
During the Level 2 screening, a toller should evaluate the hazards of the chemicals and their effects. To perform the evaluation, consider:
- How will the chemicals affect the employees who will work with or be around the new chemicals?
- What personal protective equipment (PPE) will be required for this material, and will existing PPE adequately protect employees?
- Is the existing equipment-relief-vent sizing adequate to produce the product?
- What fire-protection equipment is needed, or would existing equipment be adequate if a fire broke out that involved any of the new chemicals?
- Are the foam systems for fire protection compatible with the new chemicals, or might they create additional hazards?
- Is the facility capable of safely storing, moving, and handling the raw materials, and will employees be exposed to any potentially harmful effects when they transfer materials in and out of the plant?
- Are current emergency response equipment and procedures adequate? Does new equipment need to be purchased? Do emergency response procedures and action plans need to be revised to accommodate new chemical hazards?
Evaluating the compatibility of the chemical and process equipment during the screening process is important to prevent potential safety issues, as well as poor product quality. Consider this example: A batch toller was considering manufacturing a new product that required the use of a glass-lined reactor. Previous repairs on the reactor included the use of Hastelloy patches. While reviewing the chemical product information and associated SDSs, the toller noticed that the main raw material to be used in the product was incompatible with Hastelloy. The toller realized the potential impact of this incompatibility, and therefore, did not manufacture that product at the plant. If this screening had not been performed thoroughly, this incompatibility might not have been identified and the vessel could have been seriously compromised, causing a catastrophic release.
Another example of a compatibility review involved a product that used a pyrophoric material (i.e., a material that can ignite spontaneously when exposed to air). During the screening process, the pyrophoric nature of the material was acknowledged. After seeking operator input, the plant determined that the product would not be safe to manufacture with existing processing conditions and equipment.
In another example, careful screening prevented a toller from manufacturing a catalyst that could generate hydrogen gas. Some customers will purchase raw materials, like catalysts, for a toller to use, but in this particular case, the customer asked if the toller could produce the catalyst instead. The toller discovered that the process would generate hydrogen gas while reviewing the process used to produce the catalyst. Because the tolling facility was not adequately equipped to handle hydrogen gas, manufacturing the catalyst was found to be unsafe and economically unfeasible.
During the Level 2 screening, the toller must also generate process flow diagrams, mass and energy balances, and any other required PSI, if the customer did not already provide them. The toller will also determine raw materials and equipment that will be used, as well as intermediates, byproducts, and wastes that will be generated. All this information, in addition to determining process conditions, will be used to create the standard operating procedures (SOPs) used to manufacture that product.
Once the toller determines that the product can be made safely and economically, the product must then go through the management of change (MOC) process. Within the MOC process, a process hazard analysis (PHA) is performed.
Process hazard analysis
A PHA is another element of PSM that evaluates the potential hazards of a process. This evaluation considers the hazards associated with chemicals, processing conditions, modes of process operation, and equipment used to make the product, as well as other potential hazards.
This analysis can be challenging for batch tolling operations, where the number of new product trials and processes run in the facility can exceed 100 per year. This can strain a facility’s resources, making it difficult to conduct the PHAs and manage the subsequent five-year revalidations needed for each PHA.
However, in the Process Safety Management Guidelines for Compliance document (5), OSHA notes that similar processes can be evaluated under one PHA. In some cases, the only similarity between products’ processes may be the vessel in which they are run. In a batch tolling facility, products can be run in a single, dedicated vessel or in multiple vessels. One way to streamline the PHA process is to perform a baseline PHA for a vessel that will cover all the products that are run in that vessel, the vessel itself, and other associated equipment (6). When a new process, or a variation of an existing process, needs to be run in that vessel, the plant can review the baseline PHA for that vessel to determine whether the new process might introduce any new hazards that are potentially more dangerous than what was already covered in the PHA.
Because various products are typically run one after another, the baseline PHA also provides the opportunity to review the potential hazards posed by residual material from a prior batch left in the vessel or system. The review can examine whether the residue could be hazardous during vessel cleaning or react with chemicals in the next batch.
Other important aspects of conducting PHAs for batch operations include determining which type of PHA to perform and how to set it up. There are different PHA methods that can be used to evaluate the hazard of batch operations: The hazard and operability study (HAZOP) and the what-if method are two popular methods. Although the what-if method may be a shorter PHA, this method is better for evaluating simpler steps of the process. Using the HAZOP method can take longer, but proper setup and accurate operating procedures can provide a more thorough hazard analysis (7).
A batch operation process might have hundreds of steps run in sequence that each serve a specific purpose. In a batch process, typical steps can include:
- preparing the system (e.g., verifying that it is clean and ready for the next batch or campaign; verifying that material charge lines are routed properly; performing flushes and/or nitrogen purging if needed)
- charging raw materials, followed by reinerting the vessel with nitrogen if applicable
- heating the reactor and/or feeding and metering raw materials into the vessel, while closely monitoring the heat of reaction
- adding other materials or making batch adjustments
- decanting or cooling the product
- transferring the new product to another vessel (e.g., a storage tank, a tanker truck or rail car, totes, drums).
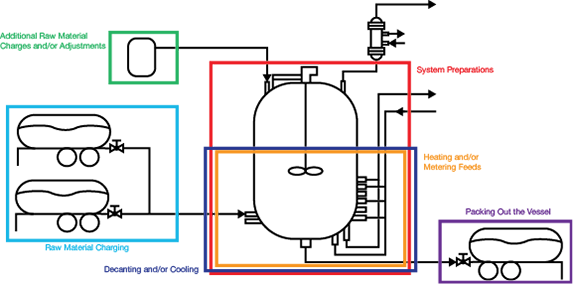
▲Figure 3. A manufacturer must set up a process hazard analysis (PHA) to evaluate the safety of its operations. One way to do this is to define nodes for each major process step. In this example, the first node includes the system preparations (red box), node two includes charging of raw materials (light blue box), node three includes the heating and/or metering feeds (orange box), node four includes any additional raw material charges and/or adjustments (green box), node five includes decanting and/or cooling (dark blue box), and node six includes the packing out of the vessel (purple box).
One facility found it easiest to set up the PHA for batch processes by defining the nodes of the PHA based on each major process step (Figure 3).
Operating procedures and supporting information
Batch tolling operations may require continual process observation and adjustments based on raw materials being fed to the vessel, reaction rates of the processes, and the steps involved in the process. These adjustments require the operator to have the knowledge required to interact with control systems, supervise the process, and maintain the process within safe operating limits. In addition, he or she should be able to act quickly to bring the process back to a safe state should the situation warrant it. This knowledge depends on well-written operating procedures (8). The PSM regulation states what information is required in operating procedures, but it is up to each facility to determine how best to create operating procedures that comply with the regulations.
One way to meet PSM requirements for operating procedures in batch tolling is to create a set of operating procedures required to make each individual product. These operating procedures, often referred to as process SOPs, batch records, or batch tickets, provide instructions for making a product. The SOPs also serve as training documents to teach operators how to run the process, as well as how to maintain the batch record for that particular product.
One SOP format that has worked well for one batch toller consists of multiple sections that contain essential information pertaining to EHS and production considerations for the product. Since the facility is also regulated by applicable environmental permits, the SOP also contains information and documentation required to run the process within the constraints of those permits.
Cover page. The first section is the SOP’s cover page. This page lists:
- the name of the product and the production vessel
- the SOP and current revision number
- a designation of whether or not the process is covered by PSM
- the original creator of the SOP, when it was created, and the MOC number the product was created under.
Applicable company officials, who must authorize a new product SOP, are listed on the cover page. If the SOP is changed per an MOC, the cover page also lists the change author, the MOC number for the revision, and appropriate personnel approvals. The cover page also reflects the personnel who performed and approved the annual recertification, along with the date on which the SOP was recertified.
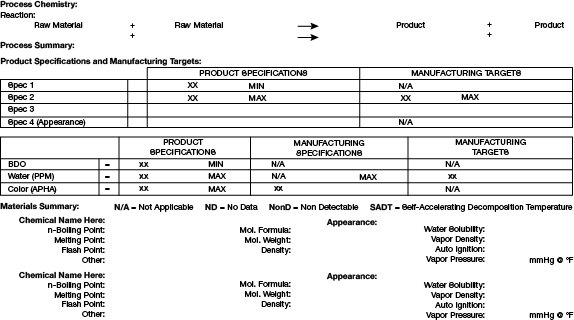
▲Figure 4. The product specification table provides the operators with important information about the process chemistry. This includes a description of the reaction(s), process summary, quality specifications for the product, and information on potential reaction hazards. The materials summary lists data for the materials used in the reaction, including critical information, such as a self-accelerating decomposition temperature (SADT).
Product specification table. Operators must have information on the chemicals that will be used in the process, and this information is also placed in the SOP (Figure 4). This section contains information on the process chemistry, including a description of the reaction(s), process summary, and quality specifications for the product. This section may also include applicable information regarding any pertinent chemical reaction hazards, as well as any side reactions that could occur and their associated hazards.
The product specification table, along with displaying product quality specifications, provides information that will help an operator determine whether a product is out of specification. A product outside the specification range could be a leading indicator to a potential adverse chemical reaction or other problem (e.g., incorrect raw material, contamination, or equipment malfunction). This information can help an operator identify an issue before it becomes a more serious problem.
Materials summary. The materials used in a process are contained in a materials summary section that contains pertinent information on the chemicals from the SDS. If critical information, such as a self-accelerating decomposition temperature (SADT) or an autoignition temperature, must be noted, it is typically listed both in the chemical information and in other pertinent sections of the SOP.

▲Figure 5. The alarm table can be customized to include information on the alarms, alarm limits, and actions that occur once an alarm limit is reached.
Alarms and interlocks. The SOP also incorporates a section with a customizable table (Figure 5) that lists the equipment alarms, alarm limits, and actions that occur once an alarm limit is reached. This includes any interlocks and their actions associated with an alarm.
Critical process parameters. Another important part of the SOP is a section that lists the critical process parameters. The information contained in this section informs the operator of critical process parameters, other process hazards, or important aspects of the process to adhere to. The critical process parameters include pertinent PSI, as well as information on how to operate the process within the facility’s air, hazardous waste, and wastewater permits.
This section also provides information on triggers (specific temperatures, pressures, or temperature rate-of-change information) to determine when and how to perform a normal process shutdown and an emergency shutdown, and how to start up after an emergency shutdown. Consequences of deviating from specified operating limits — such as pressure, temperature, flow, or order of addition — in the critical process parameters are detailed in this section or in the individual steps of the batch procedure.

▲Figure 6. The batch procedure steps are the instructions for making the product. The operator can verify that the correct material is charged by checking the material resource number listed in the step, and a second operator or supervisor can also cross-check the material. Each step must be initialed after it is completed.
Batch procedure steps. The main section of the SOP provides the individual steps required to manufacture the product. Figure 6 shows an example of the format of the individual procedure steps in the SOP. Each process section and step is listed and numbered, with a place for the operator to initial the step upon completion. Each step provides relevant information that will help the operator perform that particular task.
The procedure step also lists the resource number for the raw material charged, which allows the operator to verify that the correct material is being charged. A second operator and supervisor can also cross-check the raw material charging for the correct chemical, amount, and routing to help prevent mischarges. Any safety notes or critical hazards or parameters particular to a step, when warranted, can also be added to individual process steps.
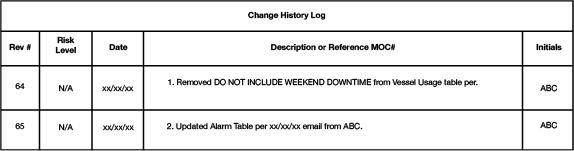
▲Figure 7. The change history log details the changes that have been made to the standard operating procedure (SOP). Each change includes a revision number, date, and initials of who made the change.
Change history log.Figure 7 illustrates a log that conveys what changes have been made to the SOP, including a revision number, when the change was made, and who made the change. An operator can use this log to see when the SOP was last revised and what changes were made. If an MOC is involved with the change to the SOP, the MOC number will be added to the change entry and the operator will receive training or notification of that change, depending on its complexity.
Closing thoughts
While batch operations play a significant role in providing the products society needs, these operations can present process safety challenges. As this article shows, batch tolling facilities can implement procedures to streamline process safety evaluations and manage risks from product conception to production. By addressing and managing hazards, utilizing experienced personnel, and implementing process safety management (PSM) processes, tollers can help prevent chemical accidents and releases and maintain profitability.
Literature Cited
- Society of Chemical Manufacturers & Affiliates, “Batch Processing and Process Safety,” presented to the U.S. Environmental Protection Agency, Washington, D.C., (May 16, 2016).
- U.S. Chemical Safety Hazard and Investigation Board, “Investigation Report: Chemical Manufacturing Incident,” Morton International, Paterson, NJ (2000).
- U.S. Chemical Safety and Hazard Investigation Board, “Investigation Report: Toxic Chemical Vapor Cloud Release,” MFG Chemical, Dalton, GA (2006).
- U.S. Chemical Safety and Hazard Investigation Board, “Case Study: Runaway Chemical Reaction and Vapor Cloud Explosion,” Synthron, Morganton, NC (2007).
- Occupational Safety and Health Administration, “Process Safety Management Guidelines for Compliance,” www.osha.gov/Publications/osha3133.html (1994).
- Center for Chemical Process Safety, “Guidelines for Hazard Evaluation Procedures,” John Wiley & Sons, Hoboken, NJ (2008).
- Bridges, W., and D. T. Clark, “How to Efficiently Perform the Hazard Evaluation Required for Non-Routine Modes of Operation (Startup, Shutdown, Online Maintenance),” presented at the American Institute of Chemical Engineers (AIChE) Spring Meeting, Chicago, IL (2011).
- Center for Chemical Process Safety, “Guidelines for Process Safety in Batch Reaction Systems,” American Institute of Chemical Engineers, New York, NY (1999).
Additional Reading
Center for Chemical Process Safety, “Guidelines for Engineering Design for Process Safety,” 2nd Ed., John Wiley & Sons, Hoboken, NJ (2012).
Copyright Permissions
Would you like to reuse content from CEP Magazine? It’s easy to request permission to reuse content. Simply click here to connect instantly to licensing services, where you can choose from a list of options regarding how you would like to reuse the desired content and complete the transaction.