Wires and optical fibers are covered with coatings to protect them against harsh environmental conditions. These coatings often serve as the last line of defense against damage, and their protective capability can define the lifetime of a product.
For decades, these coatings have been based on polyimide materials because of their exceptional thermal durability, chemical resistance, mechanical toughness, and dielectric properties. However, wires and optical fibers coated with existing commercial polyimide coatings are limited to a maximum temperature of 300°C for continuous operation with short excursions up to 400°C.
The need for higher-temperature polyimides is growing. The oil and gas industry, for example, needs electronics and sensors as it continues to explore deeper (and hotter) oil, gas, and geothermal wells. And, fiber optic sensors and electronics are being incorporated into hotter environments in automobile and aerospace engines. Polymer coatings that can withstand extended use at temperatures above 350°C and pressures up to 10,000 psi are required to enable the next generation of devices. However, under these conditions current polyimide coatings rapidly fail due to thermal and hydrolytic decomposition. In spite of continuous development by polyimide manufacturers over the past six decades, higher-temperature polyimides are still not available.
That is about to change. With a grant from the National Science Foundation (NSF), Tetramer Technologies LLC, a Pendleton, SC-based small business, has developed advanced polyimide coatings to operate at higher temperatures. Through fundamental studies of the chemical reaction that forms polyimides, the company has identified the right conditions to make an optimal coating.
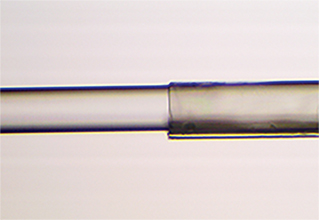
▲ Tetramer’s polyimide coating (shown here on a fiber) can be stripped from fibers using a non-flammable, low-toxicity solvent. Conventional polyimides require hot sulfuric acid for removal.
Polyimides are formed via a reversible reaction between a diamine and a dianhydride. The reaction first creates a polyamic acid intermediate, which is converted either chemically or thermally to the polyimide. The performance of the polyimide is determined by a combination of reactant architecture and process conditions that include the nucleophilicity of the amine, the electrophilicity of the anhydride, the concentration of the monomers and their order of addition, the dipolar aprotic solvent that is used, the viscosity change during the reaction, the temperature profile of the thermal imidization reaction, and how well reverse reactions and unwanted byproducts are controlled.
Polyimide Coating Lifetime | ||
Projected Useful Life in Air, days | ||
Temperature, °C | Commercial Coatings | Tetramer Coating |
250 | 1,495 | 41,034 |
275 | 320 | 6,165 |
300 | 78 | 1,093 |
325 | 22 | 224 |
350 | 7 | 52 |
With an understanding of the structure-property relationships of polyimides, the company was able to optimize these factors to produce a coating that could withstand high temperatures and pressures. The new coating can last ten times longer than existing coatings when operating at temperatures between 300°C and 350°C in air.
Existing commercially available polyimide coatings are difficult to strip from wires and fibers and require expensive stripping equipment or chemical stripping with hot (150°C) sulfuric acid. Because of this difficulty, the aerospace industry terminates polyimide fibers without stripping the coating — a practice that prevents the use of single-mode fibers. Tetramer’s polyimide coatings are soluble in benign solvents, which facilitates easy stripping and termination.
Tetramer is commercializing its polyimide coatings with strategic partners in specialty optical fiber and wire applications. The company can currently produce a sufficient amount of coating to supply target fiber and wire customers and plans to expand production to meet the growing market needs.
This technology was funded through the NSF Small Business Innovation Research Program.
This article was prepared by the National Science Foundation in partnership with CEP.
Copyright Permissions
Would you like to reuse content from CEP Magazine? It’s easy to request permission to reuse content. Simply click here to connect instantly to licensing services, where you can choose from a list of options regarding how you would like to reuse the desired content and complete the transaction.