Follow this advice if you are considering implementing the ISO 50001 energy management system to improve the energy performance of your sites.
Energy management should be the cornerstone of every corporate sustainability plan. Many types of energy reduction and continuous improvement programs exist. ISO 50001 is an energy management system developed by the International Organization for Standardization (ISO) and, while the U.S. offers no tax credits or incentives for earning this certification, ISO 50001 compliance does help companies improve their energy performance. As we implemented ISO 50001, we realized the value it offers in ways we expected, as well as in ways we did not anticipate. This article introduces ISO 50001 and offers lessons and examples that illustrate the difference an energy management system can make.
Corporate sustainability

▲Figure 1. Absolute greenhouse gas (GHG) emissions globally have risen as BASF’s have fallen. If BASF were to continue normal operation, its GHG emissions would begin to rise (dotted line). The company set a goal for CO2-neutral growth until 2030, aided by ISO 50001.
Corporate sustainability is critical not only for climate protection, but also for achieving competitive economic advantage and conserving resources. Approximately half of BASF’s greenhouse gas (GHG) emissions can be attributed to energy consumption, making improving energy efficiency key to carbon management. Since 1990, process optimization, energy efficiency improvements, and portfolio management have helped us cut GHG emissions in half, while doubling production. But, more work must be done to meet a new company climate protection goal of CO2-neutral growth until 2030 (Figure 1). To continue to grow while realizing this goal, we set out to earn ISO 50001 certification for all relevant production sites by the end of 2020.
Pursuing ISO 50001 certification required transitioning from a traditional project-based energy management program to an energy management system. The previous project-based energy management program consisted of periodic energy assessments at the site level, led by a corporate energy management specialist, that created lists of prioritized energy opportunities. The program is referred to as project-based because the energy assessments were not completed routinely but, instead, executed on an as-needed basis, with a finite beginning and end. Occasionally, some improvement opportunities identified during an assessment would appear again on the next assessment. While successful, the project-based program lacked ongoing accountability. A formal energy management system incorporates focus and accountability to maintain energy improvements.
ISO 50001 primer
The ISO 50001 energy management system is an international standard based on the plan-do-check-act continuous improvement framework. When implemented and followed, this framework enables companies to improve their energy performance.
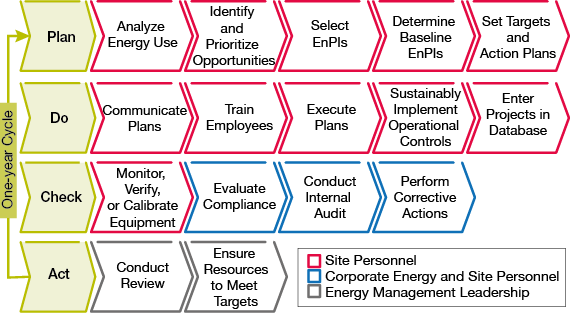
▲Figure 2. ISO 50001 follows a plan-do-check-act model. Each color indicates the party responsible for carrying out the component.
ISO 50001 employs classic improvement steps: analyze, improve, and control. As is the case with many standards, ISO 50001 does not set a target for the user, but rather forces the user to set a personalized target. The standard also does not dictate the cycle time. We selected a one-year timeline because a shorter cycle was too resource-intensive and a longer cycle would be difficult to manage. Figure 2 is a high-level map of how we implemented the standard; tasks include selecting energy performance indicators (EnPIs), conducting internal audits when necessary, and carrying out a corporate management review.
A key aspect of the ISO 50001 standard is naming a site energy manager and forming site energy teams. The site energy manager is responsible for ensuring the energy management teams are empowered to act and have the resources they need to be successful, as well as serves as the voice of the program. The energy teams meet regularly and are responsible for tracking the improvements, creating awareness of the program, and sharing successes among the team. The formality of the team, instilled by the energy management system, helps reinforce the importance of energy awareness and efficient energy use at the impacted sites.
When considering how to implement ISO 50001 across multiple sites, there are two options: a single-site certificate, for which every site to be certified is audited individually, or an enterprise (or multisite) certificate, which applies to all of the sites even though only a sampling of the sites are audited. An enterprise certificate minimizes the impacts to the sites and the overall cost. The risk of an enterprise certificate, however, is that if one site fails an audit, the entire corporate certificate can be lost. We chose to pursue an enterprise certificate because it would be the most cost-effective, as we needed to certify 11 sites in North America.
What we learned
The obvious difference between our existing structure and the ISO 50001 energy management system was the trigger for conducting energy assessments and their frequency. Instead of conducting energy assessments as needed, we conduct them annually. Once the energy management system took root, however, we realized additional key differences between the management programs.
Awareness pays
The ISO 50001 standard emphasizes the need for awareness of how energy is used. As part of the certification process, site energy teams helped spread the need for awareness to all colleagues. However, we underestimated the time it would take to build awareness and engagement. As engagement increased, participation and suggestions for implementing solutions from energy assessments increased.
We found that many of the existing continuous improvement projects positively impacted energy performance, but we were not disciplined in calculating the energy benefits. The rigor that an energy management system brings ensures that energy is considered during most projects.
One of the most valuable aspects of the energy management system is a structure that allows plant energy managers to share their challenges, successes, and concerns. Sharing updates and best practices in an open forum provides fertile ground for identifying and leveraging opportunities. This is especially valuable at large sites with multiple plants in operation.
Biannual regional ISO 50001 teleconferences serve as a forum for open discussion and sharing between BASF sites. During a recent call, one site shared that it is investigating a project to automate shutting down non-heated equipment for short outages, and a sister plant expressed interest in duplicating these efforts. To overcome hurdles associated with solids measurement, another site is using a software system that allows production data to be combined with utility data to assess energy efficiency. Not only is this valuable for other sites handling solids, but also for sites that collect data in different locations, as the software aggregates data, enabling users to identify correlations. Multiple sites are now exploring how this best practice can help them in similar situations.
Start where you are
ISO 50001 is flexible, so we did not have to start from scratch building new systems and identifying projects to establish an energy management system. We were able to leverage existing reports, databases, and processes to lower the learning curve and increase acceptance of the new system. Using existing data, the corporate energy management team could calculate energy intensities of sites and identify projects with an energy impact before we had to engage and request support from site personnel. The ability to do this initial work before engaging the sites was critical, displaying our commitment to implementing ISO 50001, our active support in achieving certification (rather than serving as just consultants), and that certification would not create additional site work. The importance of using existing systems cannot be emphasized more: It is vital to implementation and makes gaining buy-in to the ISO 50001 process easier at all levels, as well as reduces the overall effort.
We also worked with the sites to meet their needs or requests. Some sites use one software program to track nonconformances, while other sites use a different program tracker. ISO 50001 does not specify a specific program, so sites use what makes sense for them. Not being bound by a one-size-fits-all approach has made implementation smoother across individual sites.
The importance of KPIs
Strong operational controls alert the appropriate person of the necessary information at the appropriate time, enabling them to keep key performance indicators (KPIs) in the desirable range. Operational controls were the most impactful outcome of implementing the ISO 50001 energy management system, helping to safeguard energy improvements. Keys to great operational controls are appropriate KPIs, visual KPIs, and control of KPIs at the lowest possible level.
It may seem unnecessary to point out the importance of appropriate KPIs, but selecting the wrong KPI could have a negative impact on your overall goal. For example, we had two plants identify great opportunities to improve their energy performance, but when we looked at the overall KPI, their energy performance seemed to actually decrease. After some investigation, we realized the energy intensities of the two plants were very different, so the KPI was not telling the story accurately. The demand was increasing for the more-energy-intensive product, so the product mix was impacting the calculation.
Once the two plants’ energy intensities were calculated separately and then summed, it was clear that the amount of energy required per unit of production had decreased. We decided this energy intensity calculation should be done at the plant level, as these calculations are used to detect anomalies in energy efficiency, not to measure energy performance.
There is a tradeoff between simplicity and accuracy. While it is easy to lump all the energy together and divide it by the production, use caution to ensure that it will give a reasonably accurate picture.
It is also important to select the correct KPIs to define a unit operation. For example, consider an incinerator that processes aqueous waste and produces heat that can be used to generate steam. The efficiency calculations would typically be the output divided by the input, where the output is the steam generated in the incinerator and the input is the natural gas to the incinerator. However, for this unit operation, the goal was not to generate steam, but to efficiently combust aqueous waste. A KPI associated with steam production would drive behaviors on the plant floor to maximize steam production from the incinerator, rather than minimize the natural gas used to process the waste. The appropriate KPI is pounds of waste processed per cubic foot of natural gas, not steam generated per cubic foot of natural gas.
Energy managers at the plant level should support the development of meaningful KPIs and ensure that awareness of the value of the KPI is understood. Displaying KPIs, especially values that update automatically, is a powerful way to drive the right behaviors.
Learn from us
Even the most seasoned plants and sites have room to learn and change in the name of sustainability. ISO 50001’s goal of efficient energy use may not be new, but its structured, systematic approach can shed light on areas where more focus is needed. No matter where your organization is in the implementation process, learn from our experience.
ISO 50001 increased the awareness at plants of how energy is consumed and what drives energy consumption. A platform for sharing this information, as well as best practices, has helped site energy managers and energy teams reduce any duplicate efforts, saving time and money. The flexibility of ISO 50001 enables sites to tailor the system to their needs and use existing systems, processes, and databases, which reduces the demands of implementation and enhances employee acceptance and engagement. Finally, ISO 50001 formalizes the important task of energy management by requiring KPIs that build a framework for the system.
Copyright Permissions
Would you like to reuse content from CEP Magazine? It’s easy to request permission to reuse content. Simply click here to connect instantly to licensing services, where you can choose from a list of options regarding how you would like to reuse the desired content and complete the transaction.