*This article is based on a paper presented at the AIChE 2016 Spring Meeting and 12th Global Congress on Process Safety, April 2016.
It’s important to consider process safety early in the innovation process. Use a success modes and effects analysis to ensure your innovation can be safely and economically commercialized.
As engineers, we are trained to succeed by determining the right process design, the right application strategy, and the right diagnostic test, while remaining cognizant of process safety. Of necessity, process safety broadly focuses on failure — what happens when things do not go as expected, and what should be done to prevent or mitigate possible negative outcomes. As such, there is a natural tension between process safety and other aspects of process engineering.
There is one area where these two seemingly mutually exclusive concepts align — the innovation and development process by which scientists and engineers try to innovate and find new products, new pathways to existing products, or simply better ways of making products. However, when moving an innovation from the laboratory to the pilot plant or a production unit, we sometimes forget to ask, “What happens if we succeed?” What are the consequences — from raw materials procurement, through the production process, and to waste disposal — that we will face if our innovations succeed as we had first envisioned them?
This article explores the concept of a “success modes and effects analysis” to identify and address the consequences of success in the innovation process, and how application of such a tool can both direct and accelerate the introduction of new and different processes into the marketplace.
Success modes and effects analysis
“This is a great idea …What could possibly go wrong?” How often have seemingly strong, innovative products foundered in the transition from the lab to the manufacturing unit? Surprisingly, the culprit behind this failure is often the way we deal with our own success.
Innovators tend to be an optimistic lot. Process safety professionals tend to be more pessimistic, as that is the nature of their business. The two outlooks must be melded so that innovative new products can be brought to market safely and efficiently.
Hence, there is a strong need, from both a business standpoint and a safety standpoint, for a success modes and effects analysis (SMEA) at a very early stage in the development process. SMEA is the logical converse to a well-known and often used hazard assessment technique, the failure modes and effects analysis (FMEA).
At its most basic level, the SMEA asks the question “What if your proposal succeeds just as you anticipate?” Several potential issues are contained within this one simple question, which, if dealt with early in the process, can prevent the misdirection of resources. Those resources are better applied to the problems and questions that matter most rather than on a product that cannot be economically commercialized.
Phased gate process

▲Figure 1. The phased gate process for innovation projects. In order to pass on to the next gate, the proposed project must meet the requirements of all previous gates.
Many organizations use a variant of the phased gate (or stage-gate) process (1) to manage development projects (Figure 1). Each gate has a “gatekeeper,” which may be an individual or a team who evaluates the requirement for the project to pass through the gate and to the next stage. Requirements for each gate may include business, technical, regulatory, or policy specifications, depending on the nature of the project. The number and complexity of the gates used varies from one organization to another, but all methods usually contain the following stages:
- Invention or discovery — Something new has been found!
- Business case — What unmet customer or market needs will this product fulfill?
- Technical feasibility — By what route, mechanism, or process can this product be made?
- Commercial feasibility — Can this product be made profitably? Will people buy it for a price that makes it commercially attractive?
- Product launch/commercialization — Where will this product be made, and in what quantities?
Too often, process safety is not considered until Stage 4. However, waiting until this late in the development process can be very expensive (or even a complete show-stopper) if changes are needed (2, 3). By completing the SMEA in Stages 1 through 4 in a thorough and timely manner, the information gathered will determine whether Stage 5 (Product Launch) should be undertaken.
Stage 1. Invention or discovery
Of necessity, the innovation process begins with the discovery or development of something novel or unique that appears to meet a commercial or technical gap in the market. Once such a discovery is made, Stages 2 through 5 are intended to shepherd it through the development and commercialization process.
Even at this early stage of innovation, the SMEA process will help guide laboratory decisions on solvents, raw materials, synthesis pathways, and other technical issues that may have a major impact on commercial and technical viability. What you may be willing to deal with on a microgram scale may not be something you want to handle in railcar quantities. Operating conditions that are routinely and easily achievable in the laboratory may not be easily replicated in a commercial facility. Laboratory hoods provide a level of spill containment and ventilation — including odor control and respiratory protection — that may not be economically possible at larger scales. Small-scale equipment installations in high-pressure cubicles allow safe exploration of potential synthesis routes without having to fully understand or address the potential hazards.
To lead your project to a successful commercialization, you must acknowledge these issues during Stage 1 and develop a plan to address them through additional laboratory and piloting studies as needed.
Stage 2. The business case
The next step in the development process of any novel idea or product is determining whether there is a viable business case for the product. Until you know what your market is, who your customers and competition are, and how much of the product you can reasonably be expected to sell and at what price, detailed analyses are often not warranted. However, even at this early stage, you should be asking many technical questions, such as:
- Do we understand the inherent risks of the process as proposed (e.g., solvents, raw materials, etc.)? If so, are we willing to accept those risks? If not, what information will need to be generated to make such a determination?
- Are there externally imposed limitations on key utilities (e.g., water usage or waste treatment) that impact commercialization at the proposed scale?
- Are we willing and able to build new equipment or a facility to house this product, or is this slated for existing assets?
- Is this a brand new product line for us, or is it an extension of existing products?
- Who else makes this product?
- Is there information about this product already in the literature?
Answers to such questions, even if only qualitative, uncovered at this stage will be critical to a successful SMEA.
Example 1. A process for which Stage 1 development efforts had been funded and staffed for some time was presented to site management for full funding and implementation in an existing commercial-scale facility. While working to obtain approvals to move forward with the piloting efforts to support an aggressive commercialization schedule, the project team determined that several raw materials and solvents that were being used could not be adequately handled by onsite waste-disposal facilities. This significantly slowed implementation and required substantial rework to identify and vet acceptable alternatives to allow piloting to proceed.
Lesson learned. Identification and review of the overall process chemistry is crucial before the technology exits the laboratory. Such requirements are particularly important when using existing facilities that were not specifically designed for the proposed chemistry, versus greenfield construction. Even for greenfield construction, the cost of accommodation for risk mitigation may make the project economically unattractive.
Stage 3. Technical feasibility
At this stage in the development process, laboratory work is directed at finalizing the synthesis routes and process conditions to produce the desired material at the specifications and purity required to meet the business case. This sets the basis for the piloting efforts to follow in Stage 4.
The SMEA can most effectively be initiated at this point in the development process. The fundamental question to ask is: “With the basic process developed in Stage 1, and the business requirements set forth in Stage 2, are we willing to proceed with the next stages?”
You can often convince yourself that a process can be safely run at pilot scale due to the limited quantities of materials involved. An effective SMEA extends this analysis to the proposed commercial stage, even though at this stage, the analysis will need to remain at a high level.
SMEA questions at Stage 3 must focus on five issues for the commercial facility — not simply the pilot or demonstration facility. These five issues are:
- raw materials
- processing conditions and hazards
- products, byproducts, and waste streams
- storage and warehousing issues
- transportation issues.
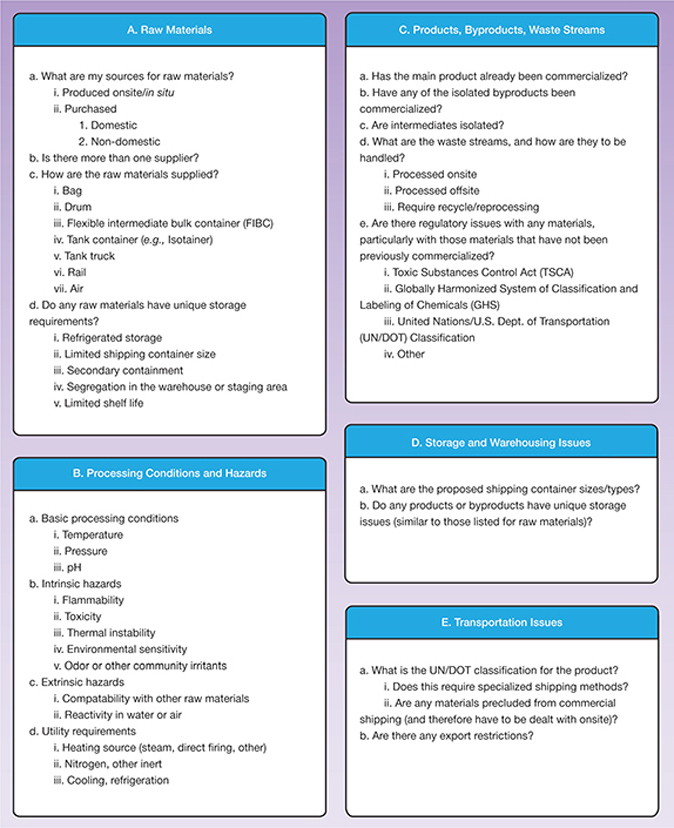
▲Figure 2. Ask these questions, among many others, when conducting a success modes and effects analysis for innovation projects.
Figure 2 provides a detailed list of typical questions to ask in the SMEA process.
While not all of these questions can be answered completely at Stage 3, they will provide significant insight and lay the foundation for what will be needed at Stage 4 (commercial feasibility). In the extreme, certain answers at Stage 3 may constitute a showstopper, including:
- waste that cannot be economically handled
- lack of reliable raw material supply
- utility requirements beyond the site’s capabilities
- products, intermediates, or wastes that fall outside the company’s risk tolerance guidelines.
Often, the answers to the questions in Figure 2 will trigger parallel efforts at Stage 4 — for example, initiating the development of documentation to meet Globally Harmonized System of Classification and Labeling of Chemicals (GHS) requirements for the product in parallel with process development, so as to not delay the overall commercialization timeline. Or, the answers may prompt you to investigate inherently safer options, such as alternative chemistries and/or processing conditions (e.g., a different catalyst to allow milder reaction conditions suitable for existing metallurgy, or a different solvent to alter waste stream properties, etc.).
The answers at Stage 3 also provide the framework for the hazards assessment necessary to move from laboratory to pilot plant or demonstration plant, where both equipment and procedures more closely mimic full-scale production.
Example 2. An innovative process with a strong business case based on laboratory data was moving toward piloting. Based on the overall flowsheet for the proposed full-scale process, the engineers determined that the volume of solvent necessitated major changes in the type of filtration equipment. This change required significantly more add-on safety equipment than anticipated, which increased capital costs and caused a schedule delay due to equipment procurement difficulties. The commercial feasibility was greatly impacted by consideration of both the additional cost and protracted schedule delays.
Lesson learned. Evaluation of full-scale manufacturing capabilities needs to be initiated very early in the process to ensure that any shortcomings do not delay or halt commercialization.
Stage 4. Commercial feasibility
By Stage 4, the technical veracity of the process should be well-developed; processing conditions and overall composition ranges should be established to the point where processing equipment can be selected and (if necessary) designed to determine commercial feasibility.
Stage 4 is the point at which engineers and the innovation team must determine and optimize yields, space-time ratios, and recycle and purge stream flowrates through piloting efforts. Variations in the chemistry should be minimal at this stage.
Another important task in the piloting efforts is the identification of potential safety concerns during upset conditions. A working knowledge of the intended chemistry is not sufficient to ensure that reactive hazards are adequately addressed. Unintended chemistry, such as side reactions, decompositions, and the formation of unidentified inter-mediates, can create unsafe conditions. The process safety engineer can help identify hazards and generate data for process safety evaluations during the design of the manufacturing facility (4).
The results of the SMEA performed in Stage 3 can now be rolled into the hazard assessment for the pilot or demonstration facility. Each of the five SMEA categories listed in Figure 2 can be incorporated into the appropriate process node, regardless of hazard assessment technique (e.g., What-If, HAZOP, Checklist, etc.). The information generated by the hazard assessment can be used either to address the potential hazard directly, or to propose a plan that will generate the required information for a full assessment.
At this stage, more quantitative answers will be needed in order to proceed. Extrinsic factors (such as specific facility siting issues, design of processing and storage equipment, and specific transportation options) will need to be assessed and addressed. The hazard assessment should include solutions for both the pilot and full-scale facilities, with particular attention on areas where the solutions for the pilot and full-scale operations differ significantly. For example, while a small refrigerator might be an acceptable, cost-effective solution for the relatively small quantities of material handled in a pilot facility, large-scale refrigerated storage in a commercial facility (the “success” scenario from Stage 1) may render the project economically infeasible, and if this is the case, it should be addressed before proceeding with the piloting effort.
Example 3. A process that had been fully vetted from a safety and regulatory standpoint was ready for commercialization. However, the engineers had estimated, rather than measured, basic design information (e.g., pure component physical properties, vapor-liquid equilibrium [VLE] data, etc.) in order to allow the engineering design process to begin. The equipment sizing was based on ideal properties. On startup, the plant did not perform to expectations, and additional investment was required to correct design issues uncovered in the initial product runs, delaying product delivery at the projected sales volume.
Lesson learned. Identify those raw materials, inter-mediates, and products for which basic design data are not available, and begin a parallel laboratory effort to generate the needed information.
Stage 5. Product launch/commercialization
If Stages 1–4 are successful, Stage 5 is a straight-forward matter of using the technical outputs from Stages 1 through 3 along with the commercial and regulatory outputs of Stage 4 to determine whether the product can be commercialized successfully.
All successful launches must meet the same basic criteria (5):
- commercially viable — there are customers willing to pay for what you are making
- profitable — customers are willing to pay enough to provide a reasonable rate of return
- legal — all regulatory and statutory requirements are being met
- socially acceptable — the community in which the product is being made is willing to accept its presence
- safe — the safety risks (personnel and process) have been identified and addressed.
Successful use and implementation of the SMEA concept will ensure that all of these criteria are met in a satisfactory and timely manner.
Closing thoughts
Consistent and systematic use of the SMEA concept during innovation and process development efforts can greatly enhance the probability of overall product success, while minimizing both time-to-market (for successful innovations) and unproductive application of resources (for unsuccessful innovations). Potential problem areas are identified early, when alternatives can be investigated relatively quickly and inexpensively. In addition, areas where parallel efforts are needed (e.g., physical property measurement, toxicological testing, compliance with regulatory requirements, etc.) can be identified, highlighted, and initiated as soon in the development process as feasible.
Literature Cited
- Cooper, R. G., and S. J. Edgett, “Lean, Rapid, and Profitable New Product Development,” Product Development Institute, www.stage-gate.com/resources_stage-gate.php (2005).
- Center for Chemical Process Safety, “Inherently Safer Chemical Processes: A Life Cycle Approach,” American Institute of Chemical Engineers, New York, NY, and John Wiley and Sons, Hoboken, NJ, p. 24 (2009).
- Mary Kay O’Connor Process Safety Center, “Challenges in Implementing Inherent Safety Principles in New and Existing Chemical Processes,” Texas A&M Univ., College Station, TX, p. 3 (2008).
- Mize, J. F., “Process Safety: From Concept to Commissioning,” Proceedings of the 9th Global Congress on Process Safety, San Antonio, TX (Apr. 28 – May 1, 2013).
- Lodal, P. N., “Take the FUN out of Process Safety,” Chemical Engineering Progress,110 (2), pp. 26–29 (Feb. 2014).
Copyright Permissions
Would you like to reuse content from CEP Magazine? It’s easy to request permission to reuse content. Simply click here to connect instantly to licensing services, where you can choose from a list of options regarding how you would like to reuse the desired content and complete the transaction.