Paints and coatings play a significant role in modern society. In addition to providing aesthetic appeal, they also protect valuable assets, including buildings, bridges, aircraft, ships, cars, trucks, pipelines, and more, from damage and prolong their useable life.
While paints and coatings are complex mixtures of ingredients, the binder largely determines the utility of the coating for a given application. The most common binder for high-performance coatings consists of two or three components that undergo a chemical reaction on the surface of the freshly coated object. The multiple components must be mixed at the appropriate ratios and appropriate time before application in order to achieve the desired coating properties. Often, the curing temperature of these binders is high, and reaching those temperatures requires energy.
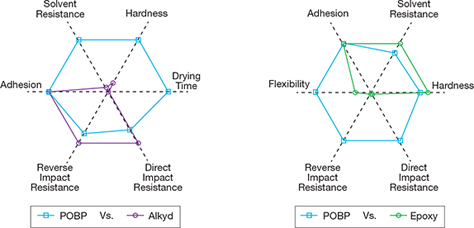
▲ Plant-oil-based polymer (POBP) coatings were compared to an alkyd coating (left) and a two-component epoxy coating (right). Each axis represents one property tested, with relative performance increasing from the center of the plot outward. The new POBP coating exhibits much better solvent resistance, hardness, and drying time than alkyd coatings, and better flexibility and impact resistance than epoxy coatings.
An alternative to multi-component binders for high-performance coatings is alkyd resin. Alkyd resins, which are thermoplastic polyesters derived from petroleum, cure at ambient conditions without the need for mixing multiple components prior to application. Alkyd resins can cure at ambient conditions because they contain unsaturated fatty chains that undergo oxidation reactions when exposed to air.
However, alkyd resins have several disadvantages. The polymer backbone of alkyds is a polyester chain, which is less hydrolytically stable than other classes of coating binders, such as acrylics and epoxies.
In addition, it is difficult to produce high-performance alkyd coatings that meet stringent regulations on volatile organic compound (VOC) content. To reduce VOC content, a lower-molecular-weight binder is often needed. When low-molecular-weight alkyd resins polymerize, they generate very-low-molecular-weight species (e.g., monomers, dimers, trimers, etc.) that significantly diminish coating hardness and increase the amount of time it takes for the coating to become a tack-free solid.
Finally, because the synthesis of alkyd resins takes place at high temperatures, the resins are relatively dark and have limited utility for the production of white and pale-colored coatings.
With funding from the National Science Foundation (NSF), Renuvix, LLC, headquartered in Fargo, ND, has developed a novel plant-oil-based polymer (POBP) technology that enables the production of one-component, ambient-cure coatings that overcome the issues associated with alkyd resins. The POBP technology produces polymers that do not contain hydrolytically labile moieties in their backbone. In addition, because they polymerize by a different mechanism, the polymers are very light in color and largely free of low-molecular-weight species that are detrimental to coating properties. The polymers used in the POBP technology are proprietary.
Data comparing POBP-based coatings with commercial alkyd and two-component epoxy coatings (figure) were shared with several major coating producers and their responses were very positive.
“The ability to produce a one-component coating with the hardness and chemical resistance of a two-component epoxy and the flexibility and impact resistance of an alkyd is a potential game-changer for the coatings industry,” says Zhigang Chen, senior technology manager at Rust-Oleum, a manufacturer of protective paints and coatings for home and industrial use.
The Renuvix team is currently developing POBP-based binder systems that will enable coatings that require little to no solvent and contain at least a 70% renewable content. The company has successfully produced POBP resin monomer and polymer at the 10-L scale and is planning to build a world-class manufacturing plant in the U.S. in 2017.
This technology was funded through the NSF Small Business Innovation Research Program.
This article was prepared by the National Science Foundation in partnership with CEP.
Copyright Permissions
Would you like to reuse content from CEP Magazine? It’s easy to request permission to reuse content. Simply click here to connect instantly to licensing services, where you can choose from a list of options regarding how you would like to reuse the desired content and complete the transaction.