The world is not on track to achieve the United Nations (UN) sustainable development goal of clean water for all by 2030. Population growth, urbanization, and climate change aggravate water scarcity. The current devastating drought in the western U.S. is a result of these factors coupled with long-term over-withdrawals of freshwater resources. To meet potable water needs, communities are turning to non-freshwater sources. Today’s best technological solution to purify non-freshwater sources into potable water is reverse osmosis (RO), the most cost-effective and energy-efficient method of desalination.
RO systems apply pressure to filter water through RO membranes to remove practically everything, including salts and other contaminants. RO systems are used to purify many sources of water including tap water, seawater, and wastewater, but they are complex and expensive to build and operate. Current RO membranes are based on polyamides that are highly susceptible to fouling and chemical degradation, and are damaged by common effective water disinfectants like chlorine. To protect the vulnerable membranes, the systems are robustly designed and operated with a careful balance of pretreatment processes, chemicals, cleaning, and monitoring, all of which can be responsible for 30–50% of annual operating costs. This limits broader adoption of RO technology. The development of durable chlorine-tolerant RO membranes with the potential to eliminate biofouling is considered the holy grail of this industry.
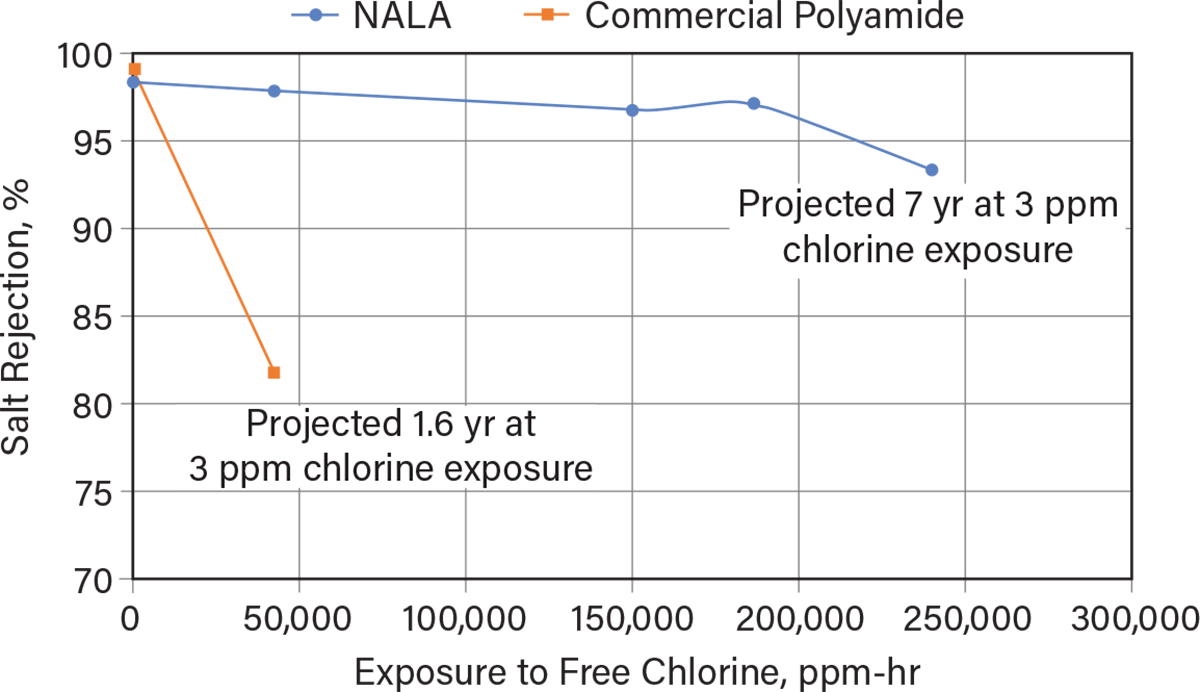
▲ Average salt rejection as a function of exposure to free chlorine (ppm-hr) illustrates the greater durability of NALA membranes compared to commercial membranes. Membranes were tested on a flatsheet cross-flow measurement system with conditions of 2,000 ppm sodium chloride in the feed water and 225 psi pressure.
With funding from the National Science Foundation (NSF), NALA Systems is developing a new class of game-changing chlorine-resistant membranes that promises to provide an estimated 20–30% savings on operating expenses by reducing RO system downtime, cleaning costs, and membrane replacement frequency. Judy Riffle and Sue Mecham founded NALA Systems to make RO membranes with polymers that Riffle had invented as a professor at Virginia Tech in collaboration with Professor Benny Freeman at the Univ. of Texas at Austin.
“Current RO systems cannot retain residual protective disinfectants, so the membranes exposed to water without any disinfectants biofoul, and the caustic cleaning chemicals that are used to remove biofouling degrade the membranes,” says Riffle. “NALA is pioneering next-generation RO membranes with chlorine resistance to eliminate biofouling.”
NALA’s membranes can handle pressures from 225 psi for brackish water (up to 2,000 ppm salt) to 800 psi for seawater (up to 32,000 ppm salt). The new polymers and membranes, based on patent-pending compositions of ionic poly(arylene ether sulfone)s, are produced using established commercially relevant processes. “The NALA membrane product will function better and form a drop-in replacement into existing RO system technology,” says Mecham.
“A chlorine-tolerant desalination membrane would not only reduce treatment costs but also simplify management of water treatment systems. [NALA’s membranes] are of great interest to us and they could very well revolutionize the RO industry,” says Dileep Agnihotri of Water Surplus, a full-service solution provider for the water treatment industry.
Glenn Walker, Water Resources Manager at Brunswick County Public Utilities, NC, says, “I have seen the effects of membrane degradation due to chlorine use; being able to retain a chlorine residual in the pretreatment systems will reduce or eliminate biofouling in the cartridge filters and in the membrane elements themselves, thus saving time, labor, and money from having to clean and replace filters and elements.”
NALA’s commercialization strategy includes engaging industry partners to rapidly develop and scale the new membrane technology to establish its value and utility as a drop-in replacement membrane. The company will roll out a study-pilot-design initiative in 2022 to co-develop application-specific solutions using its membrane platform.
This technology was funded through the NSF Small Business Innovation Research (SBIR) Program.
This article was prepared by the National Science Foundation in partnership with CEP.
Copyright Permissions
Would you like to reuse content from CEP Magazine? It’s easy to request permission to reuse content. Simply click here to connect instantly to licensing services, where you can choose from a list of options regarding how you would like to reuse the desired content and complete the transaction.