Sections
At the U.S. Dept. of Energy’s Argonne National Laboratory, scientists drive innovations that are ushering in a plastics circular economy.
“I just want to say one word to you. Just one word. Are you listening? Plastics.” In a memorable scene from the 1967 film The Graduate, Dustin Hoffman’s character Benjamin Braddock is given some unsolicited career advice on the eve of his transition into the working world: “There’s a great future in plastics.”
That little tip, which the film offers up as a sort of punchline, turned out to be quite prescient. During the half century since the movie’s release, plastics have grown into what market researchers estimate to be a trillion-dollar industry. Some 380 million m.t. of plastics are created worldwide each year for use in a wide range of applications, from grocery bags and water bottles to biomedical devices and military aircraft. And, as it happens, there’s still a great future in plastics — analysts predict that by 2050, production of plastics will quadruple to as much as 1.5 billion m.t. per year (1–3).
But the great emphasis on plastics for the past 50 years has also created problems that are piling up. Plastics accumulate in landfills, make their way into the environment, and leach into our water and food. More than 75% of plastics produced annually are discarded after a single use. Some of this waste is incinerated in power plants to produce electricity, which generates greenhouse gases and toxic byproducts. In 2018, 35 million tons of plastics were produced in the U.S. — but only 9% were recycled (4). At present, plastic recycling is economically inefficient, and the resulting product is generally of lower quality and value than the original polymer.
These problems must be met with innovative solutions and state-of-the-art technologies, as well as a dramatic societal shift away from a waste-producing linear economy, in which a product is tossed after its initial use. The solutions must promote a circular economy of products that are designed to be reused and recycled (Figure 1).
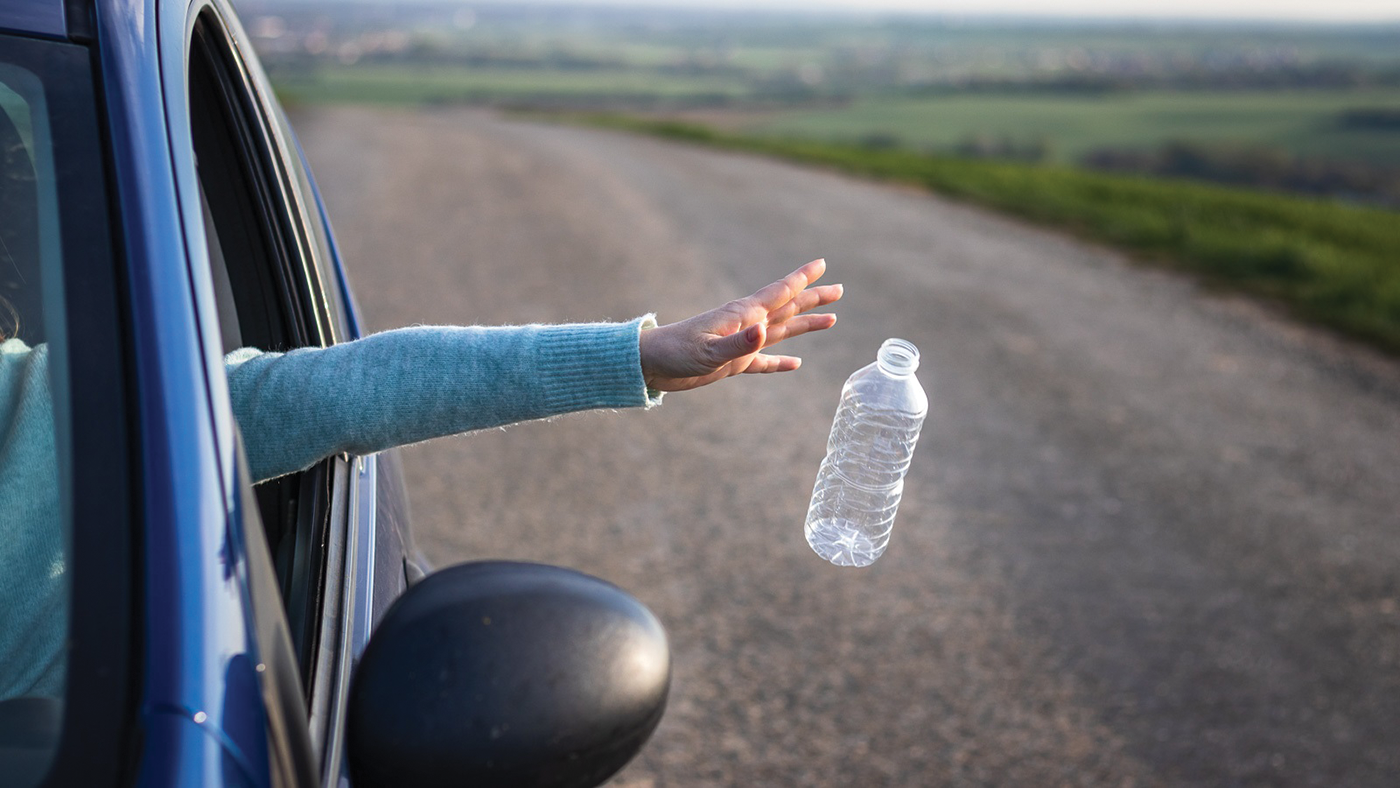
▲Figure 1. Plastics are made of many different types of materials, each with features that determine how long it will last in a specific environment. Circular economy initiatives aim to eliminate waste by developing materials that are easily reused and recycled.
The U.S. Dept. of Energy’s (DOE) Argonne National Laboratory is proving itself to be a major hub of scientific progress toward a circular economy. Located in the southwest suburbs of Chicago, the lab is a hive of activity. Engineers, chemists, biologists, materials experts, and computer and environmental scientists have joined forces — often alongside partners in academia and industry — to solve the world’s most complex problems. They are conducting cutting-edge research and development (R&D) to determine how to use sustainable manufacturing practices to reduce environmental impact.
This article describes the work of three of the lab’s principal investigators and their colleagues. It details how the lab is directly addressing the problem of waste plastics — from the upcycling of polyethylene plastic waste, to an environmental impact analysis tool for novel sustainable polymers, to efforts to make recycling plastics, at long last, a financially viable enterprise.
The plastic bag reincarnate
Anyone who has admired a plastic bag dancing in the breeze has managed to spot some potential, and maybe even an odd sort of beauty, in a piece of trash. In a similar sense, seeing the inherent value in waste plastics is part of Massimiliano “Max” Delferro’s job. As group leader of Argonne’s Catalysis Science Program in the Chemical Sciences and Engineering Division, his research begins with a single question: “What can we do about plastic in terms of chemical recycling?”
In the search for an answer, Delferro and his Argonne associates have teamed up with researchers from DOE’s Ames Laboratory, Cornell Univ., Northwestern Univ., the Univ. of Illinois Urbana-Champaign, the Univ. of South Carolina, and the Univ. of California, Santa Barbara, to form the Institute for Cooperative Upcycling of Plastics (iCOUP).
The collective is investigating how to upcycle discarded single-use plastics into more valuable commercial products (Figure 2) (5). For instance, Delferro says, “We can take a plastic bag and make a synthetic lubricant that performs, in some cases, better than the 5W-30 motor oil on the shelf at Walmart.”
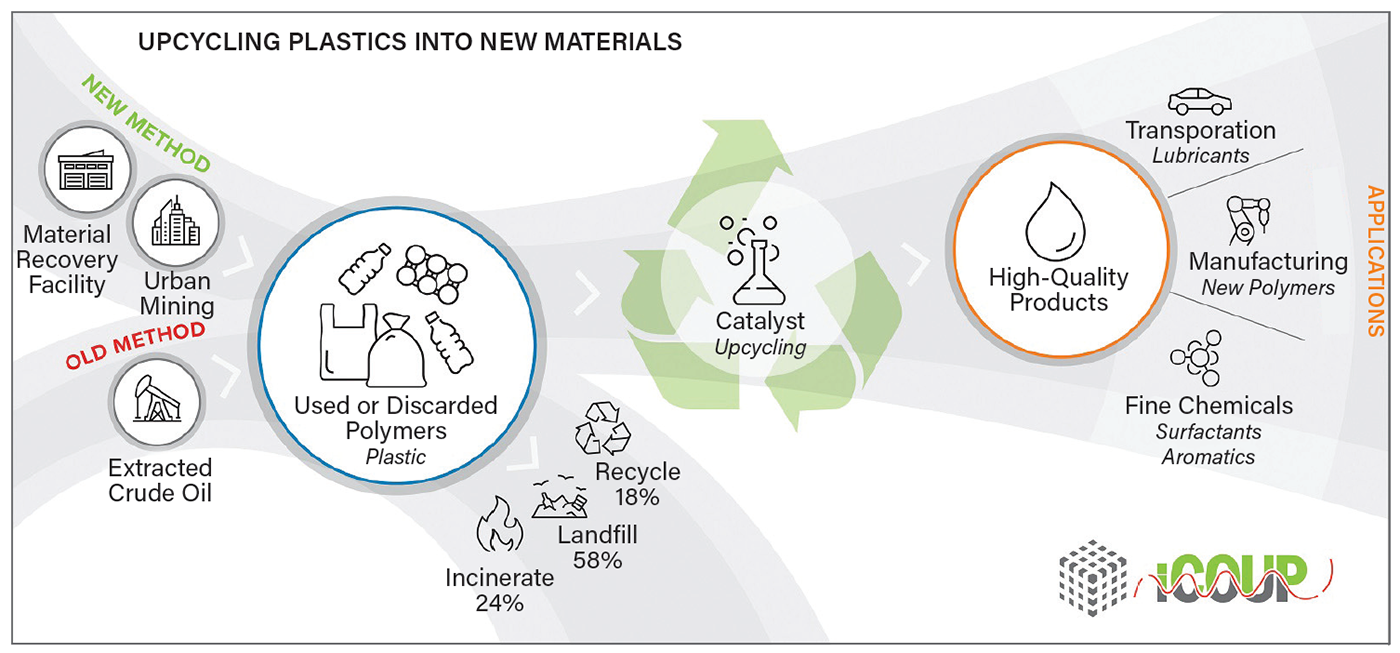
▲Figure 2. The Institute for Cooperative Upcycling of Plastics (iCOUP) is investigating how to use the building blocks of discarded plastics to make something of greater value, like turning plastic bottles into automotive lubricants. Image courtesy of Argonne National Laboratory.
They are focusing primarily on polyethylene and polypropylene, which account for almost 50% of the total polymers produced every year and do not degrade easily because of their strong carbon-carbon bonds.
So, how, exactly, does a grocery store bag become motor oil? The iCOUP team uses a process called hydrogenolysis, which involves breaking bonds through the addition of hydrogen. The waste plastics and a catalyst, in this case platinum, go into a sealed reactor, where they are heated and stirred together. Hydrogen is added, and the catalyst breaks the polyethylene’s long polymer chains into smaller segments, producing the upcycled product — high-quality liquid hydrocarbons.
This process differs from a more common method called pyrolysis, the heating of plastic at high temperature in the absence of oxygen, which has been popularized in recent years as a way of making alternative fuels.
“For me, pyrolysis is a short-term solution, because you never close the loop that is central to a circular economy,” Delferro says. “You take shale gas, from that you make olefin, from that you make polyethylene. You use that plastic product, then you heat it through pyrolysis to make the fuel, then you burn that, which produces CO2. So, in the end, you never really close the loop.”
According to Delferro, hydrogenolysis can be used on polyolefin blends. The polyethylene and polypropylene solid feedstocks do not need to be sorted prior to being processed, he says; however, other polymers, such as polystyrene and polyethylene terephthalate, do need to be separated. One key challenge to widescale implementation of hydrogenolysis is designing a highly efficient reactor, which Delferro and his colleagues are currently working on. Catalyst cost, he adds, is not a significant hurdle, provided that the process creates a high-value product, such as synthetic lubricants (Figure 3). In addition to lubricants, iCOUP has found hydrogenolysis can upcycle plastic bags into waxes that can be further refined into laundry detergents and cosmetics.
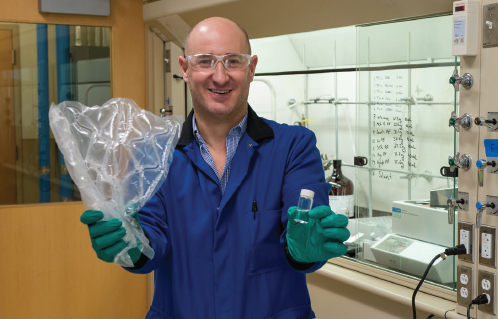
▲Figure 3. Chemist and group leader Max Delferro holds high-quality hydrocarbon liquid product (in vial) obtained by treating plastic bags with a new catalytic process. Image courtesy of Mark Lopez and Argonne National Laboratory.
These advances have allowed Delferro to imagine a time in the near future in which the world’s trash heaps no longer brim with single-use plastics. “The ultimate vision for the iCOUP team is to make it possible for society to go back into the landfill and recoup all the plastics,” he says. “Because now we have processes that can transform these plastics (that wouldn’t otherwise biodegrade) into a product that can naturally break down.” In other words: loop closed.
Designing plastics for sustainability
Cristina Negri likes to say that plastics, despite their advantages, are one of the worst misdesigns in history. “We’ve designed something that is meant to last for a century, yet much of it is used one time, thrown away, and then it stays with us for a lifetime,” says Negri, the director of Argonne’s Environmental Science Division. What we should be doing, she adds, is designing plastics and all other products to account not just for immediate use, but for the whole lifecycle of the product.
“It’s about making sure that whenever the primary intended use is finished, there is a viable pathway for that product not to accumulate in the environment, and not to be toxic or otherwise troublesome to the environment and human health,” Negri says. “We need to know from the start what the potential consequences are, and how to remedy them and build better materials that don’t have those concerning characteristics.”
To that end, Negri is directing a project at Argonne known as Responsible Innovation for bioPlastics in the Environment (RIPE). One of the project’s key tasks is to create a computer-based tool that will allow designers of new things, particularly plastics, to conduct an environmental risk assessment of materials and account for sustainability at the onset of development.
“Typically, people developing new molecules or new polymers are focused on meeting a need for a particular use, but thinking past that use time to the environmental liabilities is not a widespread proposition,” she says. “Part of the problem is that useful and dynamic tools that would allow that analysis are not easy to find.”
Several specific databases, for example, focus mainly on toxicity, and are often poorly populated for common products. RIPE’s more dynamic decision-making tool will be powered by the fusion of many databases, models, publications, and computational data. This will allow designers to ask and answer specific questions, such as:
- What polymer composition is most biofriendly for a new single-use plastic?
- What byproducts should be anticipated from the manufacturing process for a new polymer and could they be hazardous?
- Will a new polymer naturally degrade, and in what settings (e.g., inland surface water, silty soil, ocean floor)?
- Over what time span will a polymer degrade?
- What components will it degrade into and could those products cause harm to certain organisms or systems?
If the answers to those and other questions are not favorable, the designer will be able to tweak the molecule, then run the new composition back through the tool. “If a bond is added, the degradation time might increase,” Negri says. “Or if one is taken away, maybe that makes it more sensitive to ultraviolet light, allowing the product, if it ends up in the ocean, to degrade from sunlight and saltwater, turning it into food for animals.”
The tool will not only help designers determine the properties that a new plastic can provide (e.g., a better oxygen barrier or greater physical resistance), it will also allow them to add parameters, such as a demand that the item break down into nontoxic byproducts in five years.
RIPE’s development of the environmental risk-assessment tool dovetails with the work Negri and some of her colleagues are doing with Northwestern Univ. in a project called Responsible Innovation for Highly Recyclable Plastics (ResIn). Led by Linda Broadbelt, a professor of chemical and biological engineering at Northwestern Univ., the project uses computer modeling and laboratory fabrication to develop new, environmentally benign, biobased alternatives to polyurethane, which is used in everything from construction materials and insulation to furniture and textiles.
“When Linda’s team conceives of a product, we can help the team screen it from our environmental-risk perspective and give them the toxicological implications, environmental persistence implications, degradation rates, and mobility in the environment, for example,” Negri explains. “We aim to be able to tell them, ‘This molecule generated is going to be benign in the environment, or be a problem, because it’s very similar to something else, which has proven to be good or bad for, say, humans or fish.’”
Connecting environmental risk-assessment with polymer development and manufacturing will be key to developing the circular economy. “This is really a unique time for close coordination between the people who develop new polymers and the people who understand the future impact of them right in the design phase,” Negri says.
Making the economics of plastic recycling work
Jeffrey Spangenberger is a chemical engineer by training. But in his work as the leader of the Materials Recycling Group with Argonne’s Applied Materials Division, he often feels like an economist. Ask him why plastics are being recycled at such dismal rates, and he will talk about dollars and cents.
“If it’s not profitable to recycle a material, then it’s always going to be difficult to be done. You need the economic incentive to get people to actually do it,” he says. “A process has to be created that’s economical, and it needs to be revenue-positive. Unless we’re just going to pay taxes to drive plastics recycling — which is what we do now — it’s got to be economical. It ultimately costs money to recycle the plastics in the blue bins at our curbs. So, we need cost-effective tools to improve on that.”
For many recycling facilities, metal is by and large the product that pays the bills. They tend to look at a truckload of polymer-heavy waste and see it as “metal poor.” It is Spangenberger’s desire to get recyclers to see the same items as “plastic rich” — something with intrinsic value.
“If you put metal scrap out at your curb, someone is likely to come by and pick it up. If you do that with plastic scrap, it’s just going to sit there until the garbage man comes,” he says. “That’s why we have this huge problem with plastics ending up in our landfills. We really need to make it so someone will pick up the plastic at your curb and scrap it because there’s value to it. Developing value in these streams is going to take creativity and technology.”
That need has driven Spangenberger and his colleagues to create various patented technologies that separate different types of plastics and filter out contaminants to facilitate recycling. At the Argonne campus, three wet separation tanks of various sizes utilize the kinetics of water to separate solid particles based on density, shape, and size. The largest of the tanks can process up to two tons of materials per hour.
The process, based on a phenomenon known as elutriation, is an economical way of sorting materials. Instead of using salts dissolved in water to adjust a separation solution’s density, flowing water creates apparent density differences, which enables separation of waste plastic particles based on their size, shape, and density. The machinery is also very simple to operate and yields very little waste, if any, notes Spangenberger.
The process could be a boon to recyclers, particularly auto shredders (Figure 4). More and more plastics are replacing metal in automobiles, which means an increasing amount of plastic is going to the landfill after the metal in those vehicles is recycled. Less metal, of course, also means less money for the shredder companies. Spangenberger’s group has proven that auto shredder residue (ASR) can be a rich source of durable polypropylene — a potentially valuable material when it can be salvaged. In the early 2000s, during a project with the Big Three automakers, Spangenberger and his colleagues recovered and recycled ASR plastics to make new automotive parts, including a steering column cover and a battery tray.
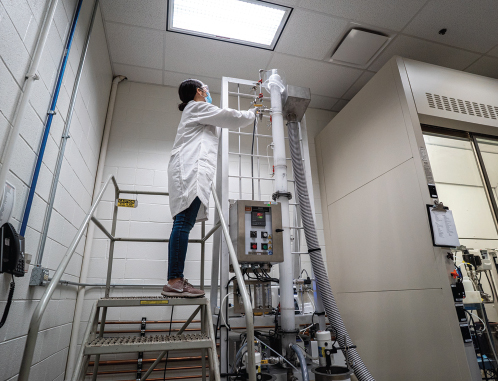
▲Figure 4. Argonne scientists use several methods to separate plastic battery components, with the aim of finding a profitable way to recycle them.
So what is keeping this method of recycling plastics from becoming more widely adopted? “In talking to folks in the industry, it’s kind of a chicken-or-egg problem,” Spangenberger says. “There are no buyers of the recycled plastic because there are no producers demonstrating consistent quality and quantity of the plastic, and there are no producers of the plastic because there are no buyers.”
To resolve this stalemate, he hopes to perform a trial run in which a team made up of Argonne researchers and industry partners would produce around 500,000 lb of ASR recycled plastic as a demonstration of consistent quality and quantity. At such large production rates, he believes that recycled plastics could be sold at a cheaper price than virgin material. A typical target price that Spangenberger aims for is half that of a virgin resin.
Ultimately, he hopes the test will help break down some of the real or perceived barriers that need to be addressed before companies are willing to build recycling plants. “I’m just hopeful that we don’t landfill this stuff, that we can actually recycle it,” he says. “So I keep pressing forward.”
Beyond the lab
The work the aforementioned scientists are doing to address the critical problem of waste plastics accumulation is important. But as all of them will attest, the effort of a single laboratory, even one full of ambition, is not enough. Fixing this global crisis and instituting a plastics circular economy will ultimately require exceptional collaboration between scientists, universities, public officials, and private industry, as well as unprecedented participation by consumers. The only way the loop will finally close, it seems, is if we close it together.
Literature Cited
- U.S. Environmental Protection Agency (EPA), “Advancing Sustainable Materials Management: 2014 Fact Sheet,” EPA530-R-17-01, Office of Land and Emergency Management (2016).
- Hopewell, J., et al., “Plastics Recycling: Challenges and Opportunities,” Philosophical Transactions of the Royal Society of London, Series B, Biological Sciences, 364 (1526), pp. 2115–2126 (2009).
- Rahimi, A., and J. M. García, “Chemical Recycling of Waste Plastics for New Materials Production,” Nature Reviews Chemistry, 1, #0046 (2017).
- U.S. Environmental Protection Agency (EPA), “Advancing Sustainable Materials Management: 2018 Fact Sheet,” EPA530-F-20-009, Office of Land and Emergency Management (2020).
- Delferro, M., et al., “Upcycling Single-Use Polyethylene Into High-Quality Liquid Products,” ACS Central Science, 5 (11), pp. 1795–1803 (2019).
Copyright Permissions
Would you like to reuse content from CEP Magazine? It’s easy to request permission to reuse content. Simply click here to connect instantly to licensing services, where you can choose from a list of options regarding how you would like to reuse the desired content and complete the transaction.