Characterizing the structure and activity of next-generation heterogeneous catalysts will be critical to unlocking more sustainable reaction-driven processes.
More effective reaction control has a vital role to play in our transition to a sustainable future. Catalysis can accelerate a reaction to make a new route viable or an existing process more efficient, as well as promote one reaction over another to reduce waste. Catalysts will play a role in tackling major issues such as energy consumption and environmental degradation. For example, the catalytic reduction of CO2 to fuels or chemical building blocks has the potential to recycle and valorize a problematic waste gas (1). Similarly, catalytic oxidation is a well-established technique for the removal of pollutants such as NOx and volatile organic compounds (VOCs) from waste streams (2).
Heterogeneous catalysts offer some inherent advantages over their homogeneous counterparts when it comes to improving sustainability. Heterogeneous catalysts are easy to separate from unreacted reagents and products, which reduces complexity and cost of separation processes. In addition, the catalysts themselves can deliver high performance over long lifetimes if they are regenerated appropriately. Despite these considerable advantages, reaction rates with heterogeneous catalysts tend to be slower. Developing heterogeneous catalysts with the reaction performance of homogeneous systems remains a longstanding goal.
Choosing an optimal catalyst for an application and commercializing new, higher-performance heterogeneous catalysts relies on developing a detailed knowledge of the structure of the catalyst and exerting precise control over interactions at a molecular level. Effective characterization and testing techniques provide the information required to develop this understanding.
This article examines how to gather critical data to guide efficient and effective catalyst development. The article begins with a discussion of gas adsorption, which allows probing of the catalyst texture to determine key parameters such as specific surface area and number of active sites. It then explains how representative, pilot-scale tests under closely controlled conditions can be used for catalyst stability and lifespan testing. A key focus of the article is how different techniques fit together to provide the information required to drive progress.
An understanding of heterogeneous catalysis
Industrial heterogeneous catalysts take a wide variety of forms, from fine particles to pellets to the larger honeycomb structures found in catalytic converters. While they may consist predominantly of active catalyst, such catalysts more commonly take the form of an active or bound metal dispersed across a support that has a high specific surface area. The characteristics of the active catalyst site and the support affect the heterogeneous reaction.
Heterogeneous reactions proceed via five sequential processes:
- diffusion of the reactants to the catalyst surface
- adsorption of the reactants onto the catalyst surface
- reaction
- desorption of the products
- diffusion of the products away from the catalyst surface.
These steps highlight the complexity of heterogeneous catalysis relative to an analogous homogeneous system and the vital role of mass transfer. In a heterogeneous system consisting of fine particles, significant reaction may be associated with the external surface of the catalyst. However, typically, the surface area associated with the internal structure or porosity of the support dwarfs the external surface area.
Modern supports are selected and designed to have specific surface areas and pore sizes to control the delivery of reactant molecules to the active catalyst center and regulate local reactant concentrations. For example, with metal organic frameworks (MOFs), a relatively new class of materials with considerable potential as catalysts and supports, it is feasible to flexibly tune mesoporous and microporous structure and the size and functionality of pores (3).
At the active site, reactants physically and chemically adsorb onto the catalyst surface. Chemisorption involves the formation of chemical bonds between the catalyst surface and the reactant (e.g., hydrogen bonding) and is the precursor to reaction. This reaction takes place in a highly localized environment; therefore, localized hydrophilicity, hydrophobicity, and acidity, along with stereochemical effects, may impact activity and selectivity (4). Once the reaction is complete, the product — which is preferably only weakly adsorbed onto the catalyst surface — desorbs and diffuses back into the bulk fluid, leaving the catalyst intact.
The fixed nature of the catalyst sites within a heterogeneous catalyst and the fact that reactants and products transfer to and from them will be a key advantage in building sustainable processes. At the end of a heterogeneously catalyzed reaction, the product is already in a different phase and detached from the catalyst. In contrast, a homogeneous catalyst may be intimately bound and mixed with the product, and separation and recovery may be a complex energy-consuming process that suffers appreciable levels of catalyst loss. An optimized heterogeneous catalyst virtually eliminates the need for complex catalyst recovery and may last for many conversion cycles, performing successfully for years with minimal loss. Gradual loss of activity may be addressed through regeneration, which, although it can be a relatively simple process, requires careful consideration during the catalyst development stage.
As mentioned previously, heterogeneous catalysts tend to have lower reaction rates than their homogeneous counterparts. To exploit their full potential, the performance of heterogeneous catalysts will need to be improved, which can be achieved in part by:
- measuring surface area (5) to address the issue of catalyst dispersion and accessibility
- quantifying the internal structure (6, 7) of the catalyst to elucidate and control reactant and product mass transfer
- characterizing active catalyst sites, especially in terms of their reactivity with reactants and other molecules that may be present
- rigorously understanding potential deactivation mechanisms and how to reverse them.
The following sections give an overview of the characterization tools used to understand and develop heterogeneous catalysts, the information they provide, and how to build a knowledge base for successful commercialization.
Physisorption
Gas adsorption is a classical technique for catalyst characterization. Physisorption studies involve the use of a chemically inert gas sorbent such as nitrogen, krypton, or argon, which reversibly adsorbs to quantify defining physical characteristics such as surface area and porosity, parameters that define access to the catalyst site (Figure 1).
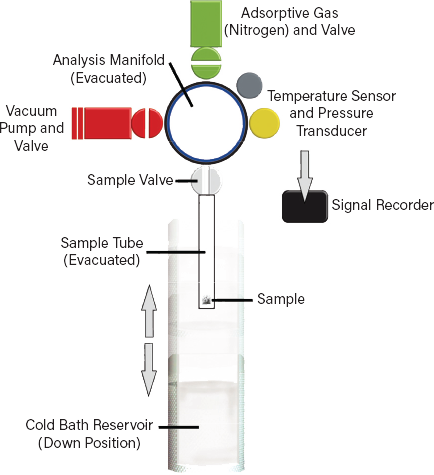
▲Figure 1. A volumetric gas adsorption analyzer can determine pore size, pore volume, and active surface area of a catalyst.
Sample degassing is the primary preparation step for a physisorption measurement. The sample is held at ambient temperature and connected to an evacuated gas manifold to remove any adsorbed contaminants from the sample surface. The manifold is then charged to a known pressure to introduce a defined quantity of sorbent into the apparatus (Figure 2). The quantity of gas is calculated from the gas law based on the (calibrated) volume of the manifold and measurements of temperature and pressure. The sample is cooled prior to measurement by immersing the sample tube in a cold bath, typically containing liquid nitrogen.
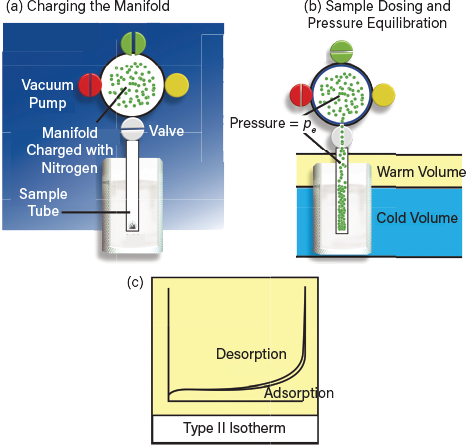
▲Figure 2. (a) Charging of the manifold to a known pressure introduces a defined quantity of sorbent into the apparatus. (b) Opening the manifold to the sample tube allows physisorption onto the sample and (c) the determination of a single point on the adsorption isotherm.
Connecting the sample tube to the manifold allows gas adsorption onto the surface of the sample, and pressure in the system re-equilibrates to a new value, pe. The number of moles of gas in the system, ne, can be determined from the gas law, given an appropriate knowledge of the larger volume (manifold + sample tube and associated tubing), the relative size of the warm and cold volumes of the sample cell or tube, and the temperature of each. The amount of gas adsorbed, nads, is calculated by difference.
One set of pe and nads values makes up a single point on the adsorption isotherm, a plot of quantity adsorbed versus relative pressure, where relative pressure is the equilibrium pressure over the sample, pe, divided by the saturated vapor pressure of the sorptive gas, p0. Additional points are produced by repeating the process at progressively higher pressures. Physisorption is a reversible process involving weak bonding with the sample surface, so desorption behavior can be studied in an analogous way by carrying out measurements at progressively lower pressures.
The molecular processes that take place during physisorption and the resulting adsorption isotherms generate information about surface area and porosity (Figure 3). At low pressures, gas molecules adsorb on just a few sites across the surface of the sample (Stage 1 in Figure 3). As pressure increases, so does coverage, to the point where a complete monolayer forms (Stage 2). At relative pressures as low as ~0.1, multilayer coverage may begin as smaller pores are already starting to fill (Stage 3), and at a certain pressure there is sufficient gas to fill all of the pores (Stage 4).
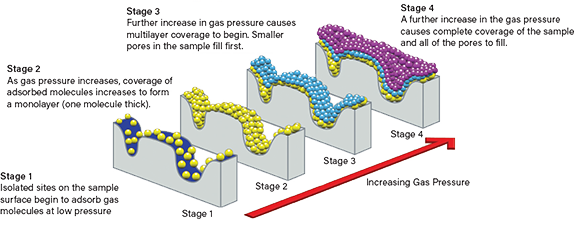
▲Figure 3. Looking at gas adsorption at the molecular level can reveal information about the surface area and porosity of a catalyst.
The adsorption isotherms for three zeolites — ZSM-5, Beta, and Faujasite (Y) — demonstrate the significant interaction between the zeolite and a typical inert fluid such as argon (Figure 4) (8). Even at 0.001 relative pressure, large quantities (mmol/g) of gas are adsorbed.
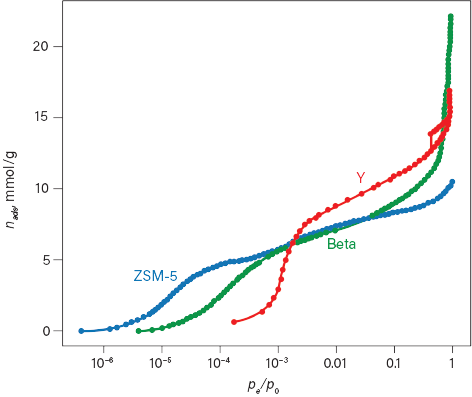
▲Figure 4. Argon adsorption isotherms for three different zeolites reveal significant differences in the total quantity adsorbed and the pressure at which the pores are filled. Data from (8).
Microporosity (pore size <2 nm) is typically observed by examining the adsorption isotherm at these very low relative pressures. For crystalline microporous materials, the entrance to the pore is often referred to as the pore window; using adsorption to characterize these materials provides the size of the pore window. The relative pressure at which the argon is adsorbed to the zeolite and the regions of increasing nads are consistent with the pore window for these zeolites. ZSM-5 has pores approximately 0.53 nm, Beta has pores of around 0.65 nm, and Faujasite (Y) has pores of 0.74 nm. These materials feature similar surface chemistry and bulk composition, but the smaller pore windows enhance the interaction between the argon and the surface. This enhancement promotes sorption of argon at lower relative pressures. Examining the full isotherm reveals that as the pore window size increases, the relative pressure at which the pores fill with argon follows the same trend — the average relative pressures observed for pore filling is approximately 10–6 for ZSM-5, 10–4 for Beta, and 10–3 for Y.
The relationship between pore window size and relative pressure for the sorption enables modeling of the pore volume. The relationship between pore size and pore volume is commonly plotted as the frequency of pores (dV/dD) vs. pore size (D) (Figure 5) (8). Calculating pore size distributions has continually advanced from early models based on the capillary condensation and behavior of bulk fluids such as nitrogen or argon to modern methods that utilize molecular modeling to develop theoretical isotherms that consider surface heterogeneity, pore shape and size, and accurate properties of confined fluids. The pore size distributions for these three zeolites were calculated using model isotherms developed for alumino-silicates used for acid-catalyzed reactions. Pore size of a zeolite is a critical parameter that must be considered to realize the benefits of shape-selective catalysis in the geometrically tailored environment of a zeolite.
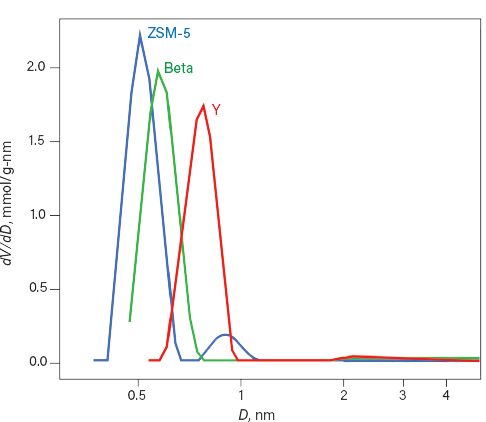
▲Figure 5. There are significant differences in the pore size distributions of the three zeolites. Data from (8).
Chemisorption
While the success of physisorption relies on selecting a sorbent that is inert with respect to the sample, chemisorption uses a chemically active sorbent to gather information about the active catalyst site. Selecting a sorbent that interacts solely with the active site of interest is therefore crucial. Researchers routinely choose hydrogen and carbon monoxide for this purpose. Gas sequencing is also an option, for example, a hydrogen-oxygen titration. The controlled dosing of a reactive gas to a sample can be implemented with a volumetric gas adsorption apparatus (as described earlier) to carry out chemisorption analyses and quantify the molecular interactions (Figure 6).
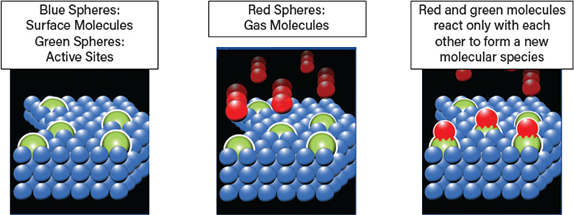
▲Figure 6. Chemisorption yields information about the active sites on a catalyst, notably the number of accessible active sites.
Chemisorption involves a strong, irreversible interaction between sorbent molecules and surface molecules of the active site and the formation of chemical bonds with the solid surface. It is a highly selective process that increases with increasing temperature and stops when access to the site is impeded. The key metric generated from chemisorption measurements, provided the stoichiometry of the surface interaction is known, is the number of accessible active sites.
Chemisorption data can allow researchers to:
- determine whether one catalyst has more active sites that are accessible than another
- differentiate the impact of a change with respect to increasing the activity of the same number of sites or increasing the number of sites, to support performance enhancement strategies
- assess whether deactivation is associated with the loss of active sites or a reduction in activity across all sites to elucidate poisoning mechanisms.
Furthermore, chemisorption measurements can also quantify a variety of other useful parameters, including:
- active surface area
- metal dispersion — the ratio of the number of active metal atoms to the total amount of metal in the catalyst
- active particle or crystallite size, assuming a regular geometry.
The chemisorption experiments described thus far involve static equilibrium gas adsorption, but dynamic chemisorption analysis is also widely applied. A basic dynamic system consists of: a precise gas control system, to accurately meter the flow of gas into the system; temperature and pressure control to maintain the sample under well-defined conditions; and a detector, typically a thermal conductivity detector (TCD), to monitor the changes in gas composition associated with adsorption.
The measurement principle remains essentially the same — i.e., detecting adsorption by difference — but characterization is typically carried out using the technique of pulse chemisorption, which can be a faster, easier alternative to volumetric gas adsorption. With pulse chemisorption, as the name suggests, pulses of chemically active sorbent are introduced as the sample is held under an inert gas flow and uptake of the reactive gas is monitored in real-time by a composition analyzer.
Systems specified for dynamic chemisorption also offer the capability for temperature-programmed analyses, an additional, powerful tool for catalyst characterization. Such analyses include temperature-programmed reduction (TPR), temperature-programmed oxidation (TPO), and temperature-programmed desorption (TPD). In these analyses, the composition of the flowing gas is monitored during a well-defined temperature change. For TPR and TPO analyses, gas composition is controlled to maintain a reductive or oxidative atmosphere, respectively. In TPD, the desorption of gas from the sample surface is monitored as a function of temperature.
Data from temperature-programmed experiments can be extremely helpful in elucidating reaction mechanisms and catalyst performance. For example, TPR can be used to investigate the influence of support materials, pretreatment procedures, and promotors on the reducibility of the catalyst surface, which can in turn directly impact reaction performance (9).
Screening trials
The preceding techniques directly support a knowledge-led approach to the development of a high-performance catalytic system, but the proof of that performance is ultimately how the catalyst behaves with respect to the reaction system for which it will be used. Representative screening with minimal amounts of catalyst is highly desirable, since availability may be scarce and costs high. This is where microreactors have a role to play, but the design and construction of a suitable system can be a significant challenge. Off-the-shelf solutions are often the most cost-effective choice (Figure 7).
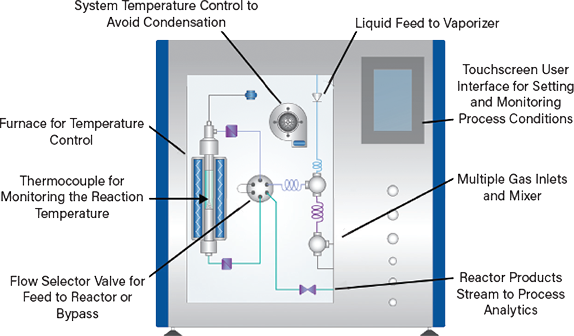
▲Figure 7. Microreactor systems have a small-scale tubular reactor, complex temperature control mechanisms, and appropriate sensors and analyzers for automation.
Microreactor screening systems contain small tubular reactor(s) with diameters of around just 10 mm, so testing can proceed with just a few grams of catalyst. Temperature control is critical. Ceramic fiber furnaces offer the very low thermal inertia required for responsive temperature control up to the high temperatures required (~1,000°C depending on the chemistry of interest). Rapid heat-up with minimal overshoot is highly desirable. Accurate pressure control is equally crucial, potentially up to pressures in the region of 100–200 bar, depending on the process under investigation.
In a microreactor, the catalyst is tested under the conditions that it will endure during use to generate a mass balance for the reacting system, which requires:
- precise metering of all gas feeds, which are typically under mass flow control
- pumped delivery of any liquid feed, often at very low volumetric flowrates
- the capture and splitting of condensable and gaseous products
- rapid compositional analysis of the exiting products.
Maintaining feeds and the reactor in a hot box at a temperature in the region of around 200°C avoids condensation in the gas delivery system. Liquid feeds are typically vaporized and mixed with reactant gases in the hot box prior to their introduction into the reactor.
Figure 8 demonstrates the type of data that can be collected from microreactor trials. The valorization of glycerol to allyl alcohols is a demanding reaction that requires precise control of both liquid (glycerol) and gas (hydrogen) feeds and produces a mixture of products (10). Several operational parameters were evaluated to map the performance of a catalyst for the valorization, including: (a) reaction temperature, (b) hydrogen partial pressure, (c) weight hourly space velocity (WHSV), (d) and time on-stream.
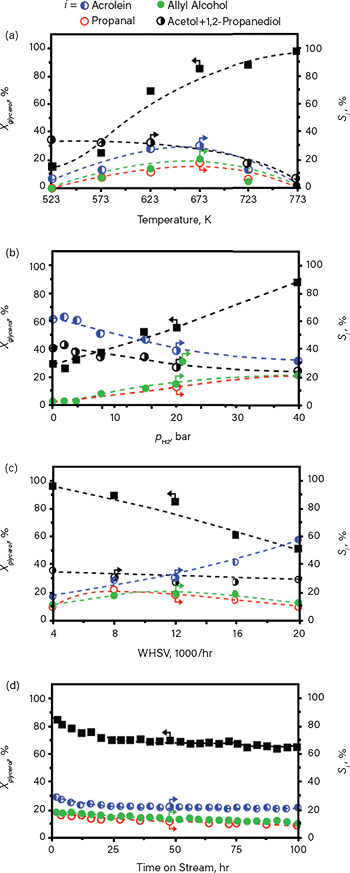
▲Figure 8. Microreactor trial data indicate the impact of (a) temperature, (b) hydrogen partial pressure, and (c) weight hourly space velocity (WHSV) on the conversion of glycerol (Xglycerol) and selectivity (S) to allyl alcohol, the desired product (and other byproducts), for a catalyst composed of silver (Ag) nanoparticles supported on a modified hierarchical ZSM-5 zeolite. (d) Extended testing provides insight regarding catalyst lifetime. Reference 10 provides full details of the study.
Before products can be analyzed, streams that contain both liquids and gases must pass through a low-volume separator. The condensate and gaseous products (or unreacted feeds) are typically analyzed by liquid and gas chromatography (LC and GC), respectively; online mass spectrometry is a faster, more responsive alternative that some vendors offer.
Microreactors enable the determination of the rate of reaction and can quantify turnover frequency (TOF), a performance-defining parameter. TOF is the number of moles of reactant converted into the desired product by each active site per hour. It is calculated from the rate of reaction and the number of active sites (as quantified by chemisorption). TOF directly quantifies reaction productivity in a way that the number of active sites cannot. A catalyst with more active sites will not necessarily be more productive for a given reaction. TOF is therefore extremely valuable for the direct comparison of alternative catalyst candidates.
Screening trials with a microreactor make the representative testing of catalysts far more accessible in terms of cost and logistics than pilot-scale trials that may require around 5–20 kg of catalyst. Furthermore, with appropriate configuration, it is possible to extend the application of microreactors to the detailed study of deactivation and regeneration. For example, dual microreactors can be operated in parallel or in series to study regeneration strategies. Complementary accessories can allow researchers to integrate chemisorption and microreactor studies to elucidate the impact of a reaction on catalyst activity. Such testing is helpful in determining reaction conditions that will maintain catalyst activity and in investigating deactivation mechanisms.
In summary, microreactor studies generate the TOF, yield, activity, and selectivity data required for the robust evaluation and comparison of catalysts for a specific application. They also enable the investigation of significant issues such as catalyst stability and lifetime and regeneration strategies. The resulting information directly supports cost-efficient catalyst development and provides a secure foundation for pilot-plant studies.
Toward commercialization: Pilot-plant studies and the challenge of scale-up
To move forward with heterogeneous catalyst candidates, two facets of scale up must be considered: commercial manufacture of the catalyst and behavior of the catalyst within an integrated process.
In a research laboratory, heterogeneous catalysts tend to be used in powder form. These research catalysts can be differentiated from industrial or technical catalysts that are shaped and structured to perform successfully in a commercial-scale fixed or fluidized bed (11). In addition to the support and active component that constitute a research catalyst, a technical catalyst may incorporate additives such as fillers, binders, porogens, plasticizers, lubricants, and/or modifiers. These additives may facilitate the catalyst manufacturing process, maintain catalyst longevity or physical stability, deliver key process performance characteristics such as pressure drop across the reactor bed, or otherwise help to optimize the potential of a promising laboratory candidate for a specific process.
Scale-up of the catalyst can directly impact mass transfer and the accessibility of catalyst sites. Porosity and surface area measurements remain critical throughout catalyst development. However, the catalyst must ultimately be tested in pilot-plant studies. These not only afford an opportunity to test the catalyst in the form in which it will be used, in a reactor with representative geometry, but also to generate a wealth of additional information that significantly reduces the risks associated with commercialization. In particular, pilot studies at an appropriate scale can (12–14):
- address concerns about heat transfer. As reactor scale increases, the surface-area-to-volume ratio decreases, which increases the potential for poor thermal management and, in the worst case, reaction runaway. Pilot-scale studies can be the best way to generate the information required to secure a robust commercial-scale heat balance.
- investigate the impact of feedstock impurities. The gases (and liquids) used in a laboratory tend to be of higher purity than commercial feedstocks. Trials with realistic feedstocks enable rigorous assessment of the potential for catalyst poisoning or unforeseen side reactions.
- assess the rate of corrosion. The cost penalties associated with using a more expensive material of construction than required are considerable. Testing over many hours under representative conditions enables the quantification of corrosion rates and determines the impact of corrosion metals on catalyst performance.
- help establish recycling strategies. If a commercial process will incorporate recycle streams, pilot studies elucidate requirements for any purge or bleed streams to maintain reaction performance.
The complexity of pilot plant design is often underappreciated. Heterogeneous catalysis is widely used for production of bulk chemicals and oil processing applications, which makes large-scale pilot studies highly desirable. Heterogeneous reactors present a complex scale-up challenge, primarily because of exacting requirements for mass transfer and the difficulty of modeling and/or predicting exactly how they will scale. Thus, it can be beneficial to solicit help from companies that are experienced in scaling up from microreactor trials.
In conclusion
Understanding the information that can be gathered with different characterization techniques and testing strategies is the key to choosing the optimal heterogeneous catalyst for a specific application. While pilot studies remain an essential element of most catalyst development cycles, the effective use of physisorption, chemisorption, temperature-programmed analyses, and microreactor trials can transform their efficiency. Lab-scale testing with small quantities of catalyst is relatively inexpensive and can generate the knowledge required to develop a robust understanding of catalyst behavior and optimize performance. Such knowledge supports better industrial catalyst and pilot plant design, shorter and more-targeted pilot-scale studies, and educated analysis of the resulting data. The characterization techniques and scale-up expertise associated with heterogeneous catalysis have advanced considerably in recent years, creating a strong foundation for the further advancement of this critical technology for sustainable processing.
Literature Cited
- Aitbekova, A., et al., “Low Temperature Restructuring of Ce-O2 Supported Ru Nanoparticles Determines Selectivity in CO2 Catalytic Reduction,” Journal of the American Chemical Society,140, pp. 13736−13745 (2018).
- Dai, H., “Environmental Catalysis: A Solution for the Removal of Atmospheric Pollutants,” Science Bulletin,60 (19), pp. 1708–1710 (Oct. 2015).
- Jiao, L., “Metal Organic Frameworks as Platforms for Catalytic Applications,” Advanced Materials,30 (37), 1703663 (Nov. 2017).
- NRSC-Catalysis, “Future Perspectives in Catalysis,” Report from the Dutch National Research School Combination Catalysis Controlled by Chemical Design, www.vermeer.net/pub/communication/downloads/future-perspectives-in-cata.pdf (accessed Dec. 4, 2020).
- Brunauer, S., et al., “Adsorption of Gases in Multimolecular Layers,” Journal of the American Chemical Society,60, pp. 309–319 (1938).
- Barrett, E. P., et al., “The Determination of Pore Volume and Area Distributions in Porous Substances: I. Computations From Nitrogen Isotherms,” Journal of the American Chemical Society,73 (1), pp. 373–380 (1951).
- Micromeritics, “The Definitive Guide to Porosity,” https://www.micromeritics.com/Product-Showcase/Porosity/Porosity-Characterization-whitepaper-sign-up.aspx?no_redirect=true (accessed Dec. 4, 2020).
- Micromeritics, “Micropore Analysis of Zeolites Using the ASAP 2420,” https://www.micromeritics.com/Repository/Files/ap139_0.pdf (accessed Dec. 4, 2020).
- Subramanian, S., “Temperature Programmed Reduction of Platinum Group Metals Catalysts,” Platinum Metals Review,36 (2), pp. 98–103 (1992).
- Giacomo, M. L., “Bifunctional Hierarchical Zeolite-Supported Silver Catalysts for the Conversion of Glycerol to Allyl Alcohol,” ChemCatChem, 9, pp. 2195–2202 (2017).
- Mitchell, S., et al., “From Powder to Technical Body: The Undervalued Science of Catalyst Scale Up,” Chemical Society Reviews,14, (2013).
- Royal Society of Chemistry, “Safety Issues in the Scale-Up of Chemical Reactions,” Environment, Health and Safety Committee, www.rsc.org/globalassets/04-campaigning-outreach/realising-potential-of-scientists/regulations-health-safety/safety-issues-in-the-scaleup-of-chemical-reactions.pdf (Jan. 2013).
- Laird, T., “How to Minimize Scale-Up Difficulties,” Chemical Industry Digest, pp. 51–56 (July 2010).
- Gertenbach, D., and B. L. Cooper, “Scale-Up Issues from Bench to Pilot,” Paper 509f presented at the AIChE Annual Meeting, Nashville, TN (Nov. 12, 2009).
Copyright Permissions
Would you like to reuse content from CEP Magazine? It’s easy to request permission to reuse content. Simply click here to connect instantly to licensing services, where you can choose from a list of options regarding how you would like to reuse the desired content and complete the transaction.