
What if Your Agitator Fails?
A German manufacturer employed a process that reacted o-chloronitrobenzene with caustic soda dissolved in methanol in a 36-m3 (9,500-gal) batch reactor to produce o-nitroanisol. The reaction is exothermic, and the addition of caustic soda normally took place at about 80°C over five hours.
Although the batches typically required cooling, a batch being processed in 1993 surprisingly did not but, instead, required steam heating to maintain the batch temperature. It was found that the agitator was not running during caustic addition and, as a result, the reactants were not properly mixed (Image 1a). When the agitator was started, the unreacted chemicals were mixed (Image 1b) and the batch temperature quickly increased, exceeding 160°C (320°F). At the elevated temperature, a different but also exothermic reaction occurred, which forced a pressure relief valve to vent 10 m³ (2,650 gal) of reactor contents to the atmosphere. A large area, including nearby residences, was contaminated. No one was injured, but concerns related to the health of the surrounding community remain. Direct costs were about DM 40 million (equivalent to about $38 million today).
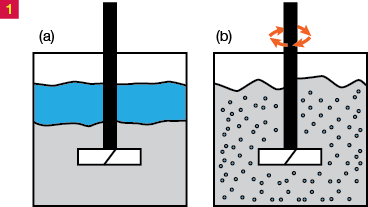
Did you know?
- If agitation fails, the reaction will be slow or stop and unreacted chemicals will accumulate. This is a serious hazard for exothermic reactions. Once the agitator is restarted, the accumulated unreacted material may react very fast and the cooling system may not be able to remove the heat fast enough to control the reactor temperature.
- Mixing is important not only to multiphase mixtures. It is also important in vessels that contain materials that are mutually soluble. Balsamic vinegar, for example, is completely soluble in water. Image 2 shows balsamic vinegar added to water without mixing. The vinegar sinks to the bottom of the glass and does not form a uniform solution until the mixture is stirred with a spoon.
- Heating or cooling a vessel without agitation is typically inefficient, and temperature measurements may be inaccurate if vessel contents are not mixed.
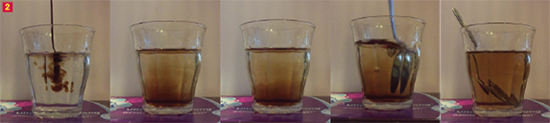
What can you do?
- Ensure operators understand that if reactor agitation is lost, they should seek technical assistance before restarting the agitator. Ask for data related to how long the agitator was off, what was added to the vessel while it was off, the temperature and pressure history of the vessel, etc.
- Recognize that loss of agitation can be a problem even if there is no intended reaction. Without agitation, large temperature and concentration differences can occur in the vessel. This can cause freezing on cooling surfaces, boiling near heating surfaces, precipitation of solids from a solution, or settling of solids from a slurry. Variation in composition of materials fed from an improperly mixed vessel to other equipment can cause operating or safety issues in downstream process units.
Reference: Gustin, J. -L., “How the Study of Accident Case Histories Can Prevent Runaway Reaction Accidents to Occur Again,” IChemE Symposium Series, No. 148, pp. 27–40 (2001).
Keep your reactor agitated for safe operation!
©AIChE 2018. All rights reserved. Reproduction for non-commercial, educational purposes is encouraged. However, reproduction for any commercial purpose without express written consent of AIChE is strictly prohibited. Contact us at ccps_beacon@aiche.org or 646-495-1371.
Copyright Permissions
Would you like to reuse content from CEP Magazine? It’s easy to request permission to reuse content. Simply click here to connect instantly to licensing services, where you can choose from a list of options regarding how you would like to reuse the desired content and complete the transaction.