Many distributed natural-gas-containing resources, which include natural gas, landfill gas, and biogas, contain significant amounts of sulfur (mainly as hydrogen sulfide). The sulfur content in these gases, which can range from several hundred parts per million to several percent, must be reduced to acceptable levels (e.g., 1 ppm for demanding catalytic processes and several hundred ppm for internal combustion engines or boilers) before these gases can be utilized.
Small-scale desfulfurization processes typically rely on adsorbents to remove sulfur from a feed gas stream. These processes are expensive and generate significant quantities of waste. Catalytic processes (e.g., the Claus process), on the other hand, which are used at large scales, are too complex and capital-intensive for distributed applications.
Without a low-cost process to desulfurize small-scale resources, small-scale sour natural gas is often vented, flared, or simply capped, and not utilized. The estimated amount of methane vented or flared from the oil and gas industry and from landfills in the U.S. in 2012 was 213 billion ft3 and 243 billion ft3, respectively. The methane emissions associated with venting and the CO2 produced during flaring of natural gas pose a significant greenhouse gas burden. Low-cost and environmentally friendly desulfurization is required to simultaneously unlock these underutilized resources and protect the environment.
With funding from the National Science Foundation, IntraMicron, Inc., an Auburn Univ. spin-off and small business located in Auburn, AL, has developed a low-cost desulfurization method called SourCat to sweeten sour gas resources. The technology includes a patented oxidative sulfur removal (OSR) process that involves a supported base-metal-salt catalyst.
“Laboratory testing on sour gas has verified that the OSR catalyst is highly active,” says Hongyung Yang, SourCat coinventor and senior research and development engineer at IntraMicron. “It can selectively oxidize H2S, COS, and simple mercaptans in the presence of low-concentration oxygen into elemental sulfur with negligible SO2 production because these molecules are more active on the catalyst surface than elemental sulfur,” Yang says.
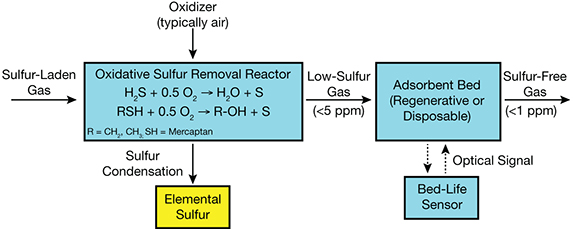
▲ In the SourCat system, a sulfur-rich gas stream is fed into the oxidative sulfur removal (OSR) reactor, where it reacts with oxygen over a supported base-metal-salt catalyst. The oxidized sulfur is condensed to form elemental sulfur, and the low-sulfur gas is fed into an adsorbent bed for applications that require sulfur levels below 1 ppm.
The SourCat process can effectively remove sulfur in sour gas. One OSR stage can remove up to 98% of the sulfur in sour gas; two stages in series can reduce the sulfur level to a few ppm, low enough to meet pipeline standards and combustion requirements. SourCat has the potential to eliminate the need for adsorbent beds in applications with high sulfur thresholds. The elemental sulfur condensed in the SourCat process can be used to produce sulfuric acid, rubber, polymers, and fertilizers.
For applications with extremely low sulfur requirements (<1 ppm), such as gas-to-liquids (GTL) and fuel cell applications, gas exiting the OSR unit can be fed into a polishing adsorbent bed. The beds are outfitted with patent-pending bed-life sensors that predict adsorbent breakthrough, eliminating the need to oversize the bed or prematurely replace/regenerate the adsorbents. And, because of the high efficiency of the SourCat catalyst, the polishing beds only need to remove 1–10% of the inlet sulfur. Thus, these systems consume 0.5–5% of the amount of adsorbent required by conventional approaches.
SourCat systems are up to 85% less expensive and generate up to 99% less waste than existing state-of-the-art approaches. At a scale of 5 million ft3/day, desulfurization of a sour gas with several thousand ppm of sulfur using the SourCat process would cost $0.13/thousand ft3. The cost to desulfurize that same amount of sour gas by incumbent technologies could be in excess of $1/thousand ft3, says Paul Dimick, general manager at IntraMicron.
IntraMicron recently formed Sour Gas LLC to sell and lease skid-mounted SourCat systems capable of desulfurizing streams with flowrates of 300,000 to 10 million ft3/day and sulfur contents up to 1%. Sour Gas LLC is conducting a major field demonstration of the SourCat technology.
This technology was funded through the NSF Small Business Innovation Research Program.
This article was prepared by the National Science Foundation in partnership with CEP.
Copyright Permissions
Would you like to reuse content from CEP Magazine? It’s easy to request permission to reuse content. Simply click here to connect instantly to licensing services, where you can choose from a list of options regarding how you would like to reuse the desired content and complete the transaction.