Sections
This article discusses the chemical incident and resulting trip to the emergency room (ER) that set one engineer’s career in motion toward process safety.
Process safety in the chemical industry is paramount. Our understanding of its importance often comes through personal experience; the day process safety hits home will vary from person to person. For me, it was the time I spent the night in a hospital as a young industry professional after acute phosgene exposure.
The exposure occurred at an off-site incinerator while attempting to dispose of an experimental toluene diisocyanate (TDI) residue-solvent mixture produced at a TDI plant in Lake Charles, LA. Phosgene inhalation can lead to pulmonary edema and possible fatality (1). The symptoms do not manifest until 24 to 48 hours after exposure. For one who has had an acute exposure above the immediately dangerous to life and health (IDLH) value, that 24-hour wait can seem like an eternity.
As an early-career engineer in the mid 1980s, I found myself in an emergency room (ER) in an unfamiliar Texas city, coughing so hard I couldn’t catch my breath. I had a phosgene badge that indicated significant exposure and all I could do was wait to see if pulmonary edema would manifest, and quite frankly, if I would die. Despite this hospitalization, an investigation was not performed, nor was a process hazard analysis (PHA) completed.
From 1986 to 1996, residue storage to overcome other reliability problems became the norm at the facility, accumulating 128 tank cars over that decade. A change in ownership of the isocyanate assets in 1996 halted the residue storage practice in railcars, and a program for off-site disposal began. About 80 cars were shipped to a cement kiln in Indiana, where most were offloaded and destroyed. In 1999, a railcar exploded at the kiln due to the reactivity of the waste and relief device fouling.
This article describes my Friday night in the ER and the site’s failure to learn from that incident, consequently leading to a catastrophic off-site railcar explosion. It was the first of many process safety events that defined my early career and set me on the path of process safety engineering.
TDI process
TDI is produced by the phosgenation of toluenediamine (TDA) in a monochlorobenzene (MCB) solvent. Phosgene is produced by reacting carbon monoxide (CO) and chlorine over a carbon catalyst. TDA is produced by the hydrogenation of dinitrotoluene. The main byproducts of the TDI reaction are anhydrous hydrogen chloride (HCl) and heavy byproducts known as TDI residue. The U.S. Environmental Protection Agency (EPA) has TDI residue listed as K027 hazardous waste by reactivity and toxicity (2). A simplified process flow diagram of the process is shown in Figure 1.
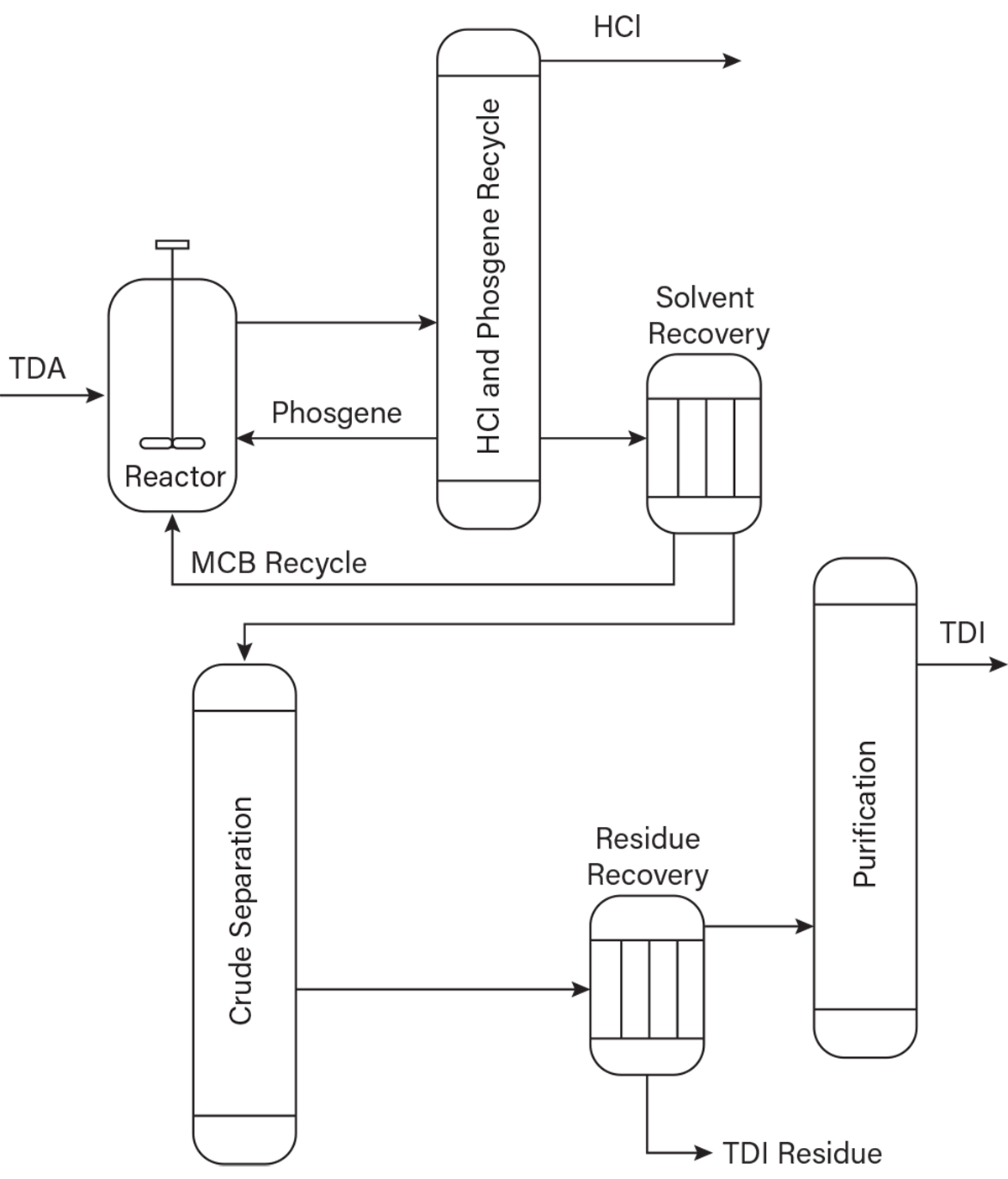
▲Figure 1. Toluene diisocyanate (TDI) is produced by the phosgenation of toluenediamine (TDA) in a monochlorobenzene (MCB) solvent. The main byproducts of the TDI reaction are anhydrous hydrogen chloride (HCl) and heavy byproducts known as TDI residue.
TDI process hazards. Phosgene, chlorine, and HCl present toxic inhalation hazards (TIH). Inhalation exposure to each of these chemicals can cause pulmonary edema, a condition caused by the acid gases reacting with water in the lungs and filling the air sacs, thereby cutting off oxygen to the body. Pulmonary edema caused by phosgene, chlorine, or HCl exposure may take 24–48 hours to manifest (3).
TDI vapors are poisonous and acute exposure can be fatal (4). TDA is a suspected carcinogen and mutagen. MCB is flammable and TDI is combustible. When combined with air, byproduct solids produced in the process, especially when saturated with MCB, can extract enough energy from the environment to combust by way of autooxidation.
Acid gases and TDI are water-reactive. Phosgene, chlorine, and HCl react with water to form muriatic acid, which is highly corrosive to carbon steel, other non-compatible metals, and lung tissue. TDI reacts with water to form carbon dioxide (CO2) and solid urea. When contained, CO2 liberation can cause physical overpressure of the container.
Although TDI residue is an EPA-listed hazardous waste due to reactivity, little was known about the reactivity in the company I worked for in the early 1980s. Verbal process safety information (PSI) gave little indication of the hazards other than rapid polymerization to a solid when concentrated above ~70 wt% in TDI. It was well understood that the rate of polymerization is a function of increasing time and temperature.
TDI residue chemistry. For most of the 35-year history of TDI manufacture in Lake Charles, LA, the main assumption in TDI residue formation was that TDI reacted with ortho-TDA to form urea in the reactor section of the plant (Figure 2). The active isocyanate (NCO) group in the urea continued a polymerization reaction with other TDI and TDA molecules, rapidly increasing molecular weight and viscosity. Other residue reactions can also occur, such as TDI self-polymerization, TDA tar polymerization, and TDI-urea polymerization. The reaction rate is a function of time, temperature, and residue concentration, increasing with each parameter.
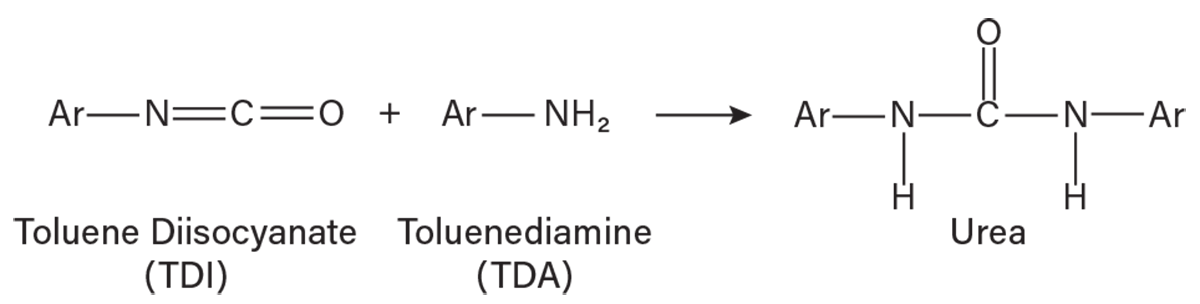
▲Figure 2. TDI and TDA react to form urea. “Ar” represents the toluene aromatic.
As the excess reactant phosgene is recovered and recycled in the process, and the MCB solvent is purified and recycled, the residue becomes more concentrated. Residue recovery involves an evaporator that separates solvent from crude TDI and residue (Figure 1). A TDI residue mixture is fed to a wiped film evaporator (WFE) designed to recover crude TDI, leaving a 70–73 wt% residue mixture for disposal. The 30 wt% TDI associated with the residue is a yield loss. It is therefore economically attractive to recover as much TDI as possible and dispose of the highest residue concentration possible. It is important to note that the process thermodynamics indicate there should be no phosgene in the residue recovery or TDI purification portion of the process.
Changes from landfill to incineration. Until 1985 at the Louisiana facility, the ~70% residue mixture was pumped to a partitioned residue shed. There, the mixture continued to polymerize rapidly, forming a crystalline solid. The solid residue was removed and transported to an open landfill located on 700 acres of marsh south of the facility. This TDI process also had an incinerator to process some of the residue. Since residue rapidly solidified, it would often plug up the 1-in. disposable carbon steel tubing between the WFE pump and the 50 ft or so to the incinerator. Furthermore, the various interlocks on the incinerator led to the frequent diverting of residue to the shed. During this time, the incinerator reliability was, at best, 50–70%.
In 1984, the Federal Hazardous and Solid Waste Amendments (HSWA) to the Resource Conservation and Recovery Act (RCRA) were passed with the intention of phasing out land disposal of hazardous waste such as TDI residue (5). By 1985, the residue shed was phased out, relying solely on incineration for residue disposal. Given the poor incinerator reliability, this severely impacted production.
Residue storage. Recognizing that residue solidification was a strong function of concentration, a team was assembled to devise a way to store residue by dissolving it in solvent so that production would not be interrupted for incinerator trips. The new process was piloted on the bench and the first trailer of stored residue was produced in 1985. At that time, residue dilution in solvents was on an early learning curve. The trailer’s contents became quite viscous, prompting the plant to dispose of the material (and the trailer) at a landfill. Similarly, the first railcar filled with stored residue became hard to pump due to increasing viscosity, so the car was sent to a Texas incinerator with instructions to dispose of the contents as quickly as possible and to not add heat to the car. We clearly understood that viscosity was a function of time and temperature.
Friday night in the ER
Off-site incineration. The plant received a call from the incineration company on the Friday of the railcar’s arrival. They requested additional information on why the car was “steaming.” I was sent to investigate. I should point out that I had less than two years of experience in industry at this time. The company had experienced trouble pumping the viscous residue mixture to the incinerator and added steam to “melt” the material, despite our warnings. When I arrived, they characterized the material venting from the top of the car as steam. I decided to climb the railcar to block it off.
I soon learned that the vapor escaping the car was not steam, but phosgene emitted from an open vent valve. I had inhaled at least two full breaths. My phosgene badge immediately turned bright red. I couldn’t catch my breath and couldn’t stop coughing. The company transported me and a few others from the area to the hospital for treatment.
Phosgene exposure. Fortunately, none of the workers in the immediate area were exposed. Unfortunately for me, the emergency room doctors didn’t have experience with phosgene. The ER had no protocol for acid gas exposure. So, I waited. They took chest X-rays every two hours and frequently listened to my breathing. By the next day, my cough had slowed, and they released me to drive home to Louisiana. Knowing about pulmonary edema and delayed exposure symptoms made this one of the longest nights of my life. This hospitalization was not considered a U.S. Occupational Safety and Health Administration (OSHA)-recordable injury by my company.
Failure to learn
We did not have management of change (MOC) in 1985. My company did have an extensive hazard review program that included technology, capital, and operating reviews. Unfortunately, we did not do a hazard review for this project. While we did have incident investigation, it was not formal root cause analysis, and my phosgene exposure incident was not investigated.
This incident illustrates significant weakness in the leadership and management systems. While leadership was curious about phosgene association with residue, they didn’t investigate to determine how it was there and how it caused a hospitalization.
Rather than focusing on improving the incinerator reliability, the focus was on improving the residue dilution process. The optimum recipe was soon found, which kept the residue in a liquid state, and two 23,000-gal residue storage tanks were installed. Continued poor incinerator reliability eventually led to moving excess stored residue to railcars with the intention of reprocessing the material to recover solvent and crude TDI and later dispose of the remaining residue. The site even considered the TDI content of the stored residue as work-in-process material for accounting purposes.
Warning signs. Details of the reactivity of the residue should have been investigated long before the storage project. Residue diverted to the shed often had phosgene vapor over the solid, and a blower was used to capture the acid gas to a scrubber. Residue deposited in the open landfill would often catch fire, like a coke or coal pile. Once moved to the marsh and upon exposure to air and water, the solids continued to react and extract enough energy from the environment to support combustion.
Other warning signs included periodic high phosgene concentrations in the product TDI. This was baffling at the time because thermodynamically, phosgene should not have been present in this part of the process. The problem was eventually solved by changing upstream operating parameters, but the cause of phosgene was not investigated.
Attempts to recover crude TDI by concentrating residue above 73 wt% led to frequent explosions in the WFE bottoms gear pump. Rather than return to normal operating conditions, a “catcher’s mitt” was constructed to prevent injuries and damage to surrounding equipment from the shrapnel. Other process warning signs included frequent 1-in. tubing pluggage from the WFE bottoms to the incinerator at the high residue concentration.
A concerning warning sign for stored TDI residue is the observed fact that the material in railcars continued to become more viscous and change composition over time, indicating a reactive polymerization continued while stored in solvent. Despite this observation, the shelf life of the stored residue was not set, and the company continued to attempt to recover solvent, TDI, and residue by rework. Rework of the reactive material proved to be difficult as the material balance simply didn’t support increased solvent and residue loading in the residue recovery section of the plant. This caused more incinerator trips, more equipment fouling, and poorer reliability. The cycle of operation continued for nearly 11 years, eventually amassing 128 railcars of stored residue.
Residue railcar explosion. Fortunately, a company with a very low risk tolerance acquired the isocyanate assets in 1996. There was a strong focus on operational excellence, process safety, and reliability. Soon after acquisition, the practice of storing TDI residue in railcars was stopped. Teams were assigned to fix incinerator reliability problems and dispose of the stored TDI residue off-site.
Explosion at Essroc. Prior to the 1996 acquisition of the isocyanate assets, the facility attempted to dispose of some of the residue-filled railcars, as reworking the material to recover TDI often created reliability problems within the process. The Essroc Cement plant in Indiana was one outlet for disposal, as they used the material’s heating value in their cement kilns.
One railcar had been in storage for five years and was heated at Essroc for a week due to the high viscosity of material and trouble offloading. This led to an explosion of the railcar. On the night of the explosion, witnesses reported fireballs and flaming debris. Following the initial explosion, three secondary explosions occurred. Fortunately, there were no injuries or fatalities.
The National Transportation Safety Board (NTSB) determined that the probable cause was the failure of Essroc to develop and implement safe procedures for offloading these wastes, resulting in the overpressurization of the tank car from “chemical self-reaction and expansion of the toluene diisocyanate matter wastes” (6). Exponent published the results of this investigation and expanded on the cause as “the failure of the waste generator to understand and communicate the hazards of its own waste streams” (7). Both the NTSB and Exponent articles are excellent summaries of this incident.
Understanding the reactivity of TDI residue. Following the Essroc incident, bench work was done in the research center at Lake Charles that theorized a new chemical pathway explaining phosgene liberation and pressurization of containers that contained TDI residue over time during heating. Both TDA and TDI are difunctional molecules, and it is possible to react both functional groups to produce di- and tri-carbodiimides. Once formed, the carbodiimides react with phosgene, HCl, and isocyanate to form adducts. The adduct formation occurred early in the process in the reactor and HCl separation sections where the highest concentrations of phosgene and HCl are found at conditions favoring the reaction. The carbodiimide can then cleave phosgene given heat, time, and the correct pressure found in the residue concentration section of the plant. Figure 3 illustrates a phosgene carbodiimide adduct formed from a TDI residue reaction.
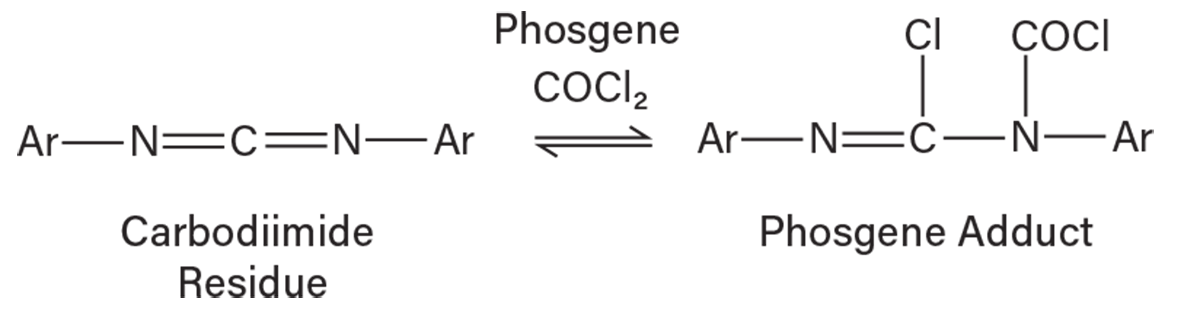
▲Figure 3. Carbodiimide residue can react with carbon dichloride oxide (phosgene) to form a phosgene adduct.
After 30 years of making TDI and recognizing the reactivity of its residues, which led to a young engineer’s ER visit and a railcar explosion, the site had a working model that explained how phosgene could be associated with residue and generate excess vapors when heated.
Process safety management system failures
Process safety culture. The site’s leadership had a stated goal to make the lowest-cost TDI in the world from 1985 to 1996. This goal created an atmosphere that placed the importance of production over process safety. This was repeatedly demonstrated by the failure to dedicate resources to improve reliability, by accounting for stored hazardous waste as TDI production, and by accumulating 128 railcars of material.
A single focus on cost per pound of product has been shown to be shortsighted and counterproductive. The Center for Chemical Process Safety (CCPS) published “The Business Case for Process Safety” in 2003, based on a study conducted between 1999 and 2002. This study was revised as recently as 2018 and continues to show the business benefits of process safety (8). Storing TDI residue led to an apparent accounting loss since the non-recoverable product and solvent had to be written off. Large accumulations of material that were accounted for as product increased working capital. The greatest deduction from profit stemmed from the opportunity cost incurred by lost production due to poor incinerator reliability. If the business had a better understanding of residue reactivity and solved incinerator reliability problems at the time of EPA’s implementation of HSWA, the capital, storage, disposal, and engineering costs would have been avoided. Increased reliability would have resulted in more production and lower cost per pound for TDI. Perhaps the most significant cultural process safety oversight is the lack of recognition that fatalities or community incidents caused by the reactivity of stored TDI residue might have significantly damaged the company’s reputation and financial bottom line.
Process safety information. Although TDI residue was an RCRA-listed hazardous waste by reactivity and toxicity, little was known about the nature of the reactivity. TDI was produced for 30 years before the research group theorized a plausible chemical route to residue that explained the presence of phosgene and behavior of the material with time and temperature. Had this PSI been known years before, each incident related to stored residue could have been prevented.
The U.S. Chemical Safety and Hazard Investigation Board (CSB) has published several documents and reports, including the “Improving Reactive Hazard Management” and “T2 Laboratories Inc. Reactive Chemical Explosion” reports, illustrating that lack of chemical reactive hazard recognition is a repetitive cause of process safety events (9, 10).
Hazard identification and risk analysis (HIRA). Despite the company having a robust hazard review system prior to 1992, one was not performed on the new process of residue storage. Even after the promulgation of the Process Safety Management (PSM) standard in the U.S. in 1992, residue railcars were not in PHA scope as they were not considered part of the process. Although residue storage vessels were in HIRA scope, the reactive hazards were not considered due to the lack of reactivity hazards PSI. Changes to the residue storage practices were not adequately evaluated by MOC after 1992. Failure to complete a HIRA left unanswered questions of what could go wrong in the process, how bad it could be, and how frequently it might occur.
Failure to understand the risk of residue storage also led to other process oversights, such as an incomplete understanding of shelf life, no storage or handling guide, and no unloading procedures. Ogle et al. (Exponent) point out that the material safety data sheet (MSDS) used for the material was based on assumed chemical composition (7).
Incident investigation. Had an incident investigation been completed after my Friday night in the ER, it is possible that the cause of phosgene associated with TDI residue and the true reactive nature of TDI residue would have been identified, allowing leaders to make different decisions on railcar storage.
Additional incidents listed as warning signs, such as explosions in residue pumps, phosgene in product TDI, and changing compositions in storage, should have led to investigations that might have evaluated reactive hazards sooner. Had any rigorous investigations been completed, the Essroc explosion may have been prevented.
Key lessons for process safety engineers
That Friday night in the ER, along with other process safety incidents from my career, reinforce a few key takeaways for process safety engineers:
- Assign personnel with relevant experience to tasks involving significant hazards and risks. This includes incident investigation, HIRA, MOC, and other risk-based process safety activities.
- Investigate all incidents and near misses. Identify the true causes and provide corrective action to eliminate them.
- Conduct meaningful HIRA and MOC for all changes to equipment and technology, including tests, pilots, and capital. Identify and mitigate risk to a manageable level.
Perhaps the most important lesson is to find a compatible process safety culture. Leaders who say “safety first” but act on production over process safety do not create an environment that is committed to process safety. Investigations that do not identify real causes and suggest ineffective corrective actions should raise a flag. If the process safety culture doesn’t feel right, find a new place to work.
In closing
My Friday night in the ER was the first of many process safety incidents in my career. Shortly after the incident, OSHA’s PSM and EPA’s Risk Management Program regulations were promulgated. I was fortunate to have participated in early compliance efforts as the field of process safety was developing. By 1988, I was part of a grassroots aliphatic diisocyanate project, and in 1992, I worked in manufacturing hydrazine propellants for NASA. Working in isocyanates and propellants made me an ideal candidate for technical manager charged with process safety compliance.
A very significant event occurred in 1994, resulting in a fatality at the plant. This event, and the many others leading to the 1994 incident, solidified my path toward process safety. The Lake Charles plant shut down in 2005 after being destroyed by Hurricane Rita. I moved on to corporate roles in my company where I held positions as Operational Excellence Manager, refinery Process Safety Manager, Global HSE Manager of Engineering and Support, and Global Process Safety Manager. I retired as a Senior Director of Global Process Safety and am now a process safety improvement consultant. I have the pleasure of teaching process safety in chemical engineering at Louisiana State Univ. with the hope of inspiring the next generation of chemical engineers to learn from the past, save lives, protect the environment, and preserve jobs by preventing process safety events.
Since I dedicated my career to process safety, I feel like I haven’t worked a day. It all began with my Friday night in the ER.
Literature Cited
- Cameo Chemicals, “Phosgene Chemical Data Sheet,” https://cameochemicals.noaa.gov/chemical/4228 (accessed Jan. 4, 2024).
- U.S. Environmental Protection Agency, “Hazardous Waste Listings,” www.epa.gov/sites/default/files/2016-01/documents/hw_listref_sep2012.pdf (Sept. 2012).
- WebMD, “Pulmonary Edema,” www.webmd.com/lung/the-facts-about-pulmonary-edema (accessed Jan. 4, 2024).
- Cameo Chemicals, “Toluene Diisocyanate Chemical Data Sheet,” https://cameochemicals.noaa.gov/chemical/17847 (accessed May 13, 2024).
- U.S. Environmental Protection Agency, “Summary of the Resource Conservation and Recovery Act,” www.epa.gov/laws-regulations/summary-resource-conservation-and-recovery-act#:~:text=HSWA%20%2D%20the%20Federal%20Hazardous%20and,as%20corrective%20action%20for%20releases (accessed Jan. 4, 2024).
- National Transportation Safety Board, “Rupture of a Railroad Tank Car Containing Hazardous Waste Near Clymers, Indiana, February 18, 1999,” Hazardous Materials Accident Report NTSB/HZM-01/01 (Mar. 2001).
- Ogle, R. A., et al., “Explosion of a Railcar Containing Toluene Diisocyanate Waste,” Process Safety Progress, 23 (4), pp. 316–320 (Dec. 2004).
- Center for Chemical Process Safety, “The Business Case for Process Safety,” www.aiche.org/ccps/about/business-case-process-safety (accessed Feb. 21, 2024).
- U.S. Chemical Safety and Hazard Investigation Board, “Improving Reactive Hazard Management,” Report No. 2001-01-H (Oct. 2002).
- U.S. Chemical Safety and Hazard Investigation Board, “T2 Laboratories Inc. Runaway Reaction,” Report No. 2008-3-I-FL (Sept. 2009).
Copyright Permissions
Would you like to reuse content from CEP Magazine? It’s easy to request permission to reuse content. Simply click here to connect instantly to licensing services, where you can choose from a list of options regarding how you would like to reuse the desired content and complete the transaction.