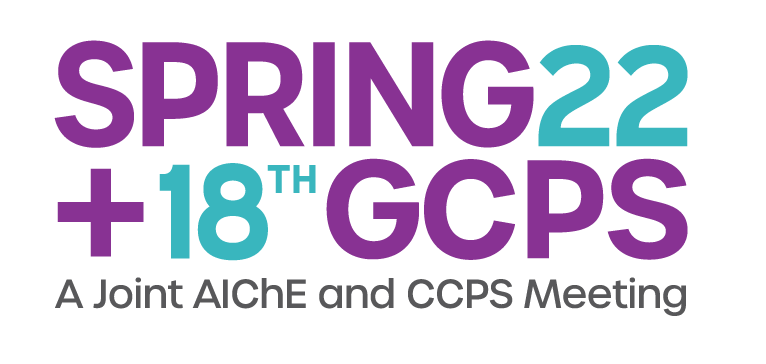
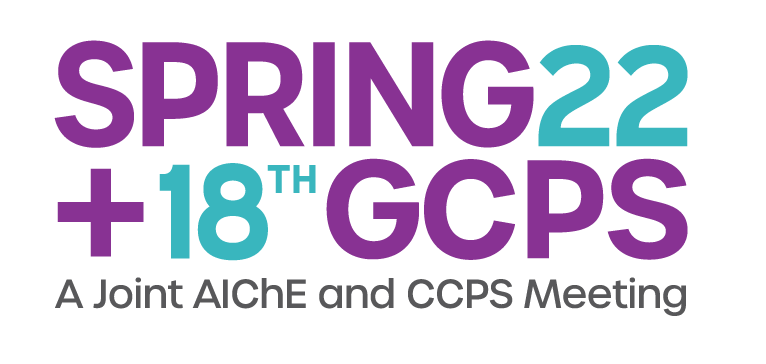
Roberto Tomotaki
Byron Kieser
Engineers are reluctant to place compact designs in even moderate fouling services because of the risk associated with âcleanabilityâ.
It is very common practice to find only straight-tube bundles in fouling services. These bundles are often designed with so-called âcleaning lanesâ, which are arrangements of gaps in the bundle that allow a clear path for hydroblasting jets through the bundle, and wider tube spacing to help prevent the entrainment of fouling within the bundle.
Designing for cleaning in this way reduces an exchangerâs heat transfer surface area and thus its total heat transfer capacity, and increases the needed equipment footprint, network size and complexity.
The advent of cleaning methods, such as ultrasonic cleaning and thermal cleaning can relieve the design concerns by ensuring that even the most compact designs can be cleaned thoroughly on all its flow paths. The elimination of cleaning constraints will afford engineers the opportunity to simply and inexpensively improve heat transfer performance by replacing standard square-pitch bundles with higher performance compact designs. The added heat transfer performance may be used to improve process performance or increase maintenance intervals.
Compact Heat Exchanger Designs
Compact heat exchanger technologies provide an alternative to the typical shell and tube heat exchanger design. When contrasted to traditional straight shell and tube designs, compact exchangers are typically described as having a higher surface area to volume ratio, higher flow turbulence leading to higher heat transfer coefficients, and a higher flow shear stress leading to slower fouling build-up. Many of these types of exchangers can also be designed to having a true-counter flow between the cold and hot fluids producing additional heat transfer efficiencies. These advantages can potentially lead to a lower capital project requirement and higher energy recovery. Common examples of compact heat exchangers are welded plate exchangers, spiral exchangers, and twisted tube bundle exchangers.
A common apprehension of engineers in selecting compact exchanger designs is the concern about the ability to clean such units in cases where they become fouled. Even though fouling build-up is typically slower in compact exchangers, most eventually foul to the extent where a cleaning is required. These exchanger designs have narrow flow lanes where a hydrojet using a traditional hydroblast machine does to have a direct path to impact the foulant deposit. Hence significant foulant deposits may be inaccessible to traditional hydroblast techniques and are left behind after cleaning. These cleaning concerns are often based on a companyâs past negative experience with these exchanger technologies. The difficulty in cleaning has hampered the propagation of compact heat exchanger technology in the industry.
Even for traditional shell and tube exchanger, the question surrounding cleanability impacts design choices, often preventing the use of more compact designs. For example, U Tube bundle designs offer several advantages including: (a) The elimination of a floating head makes the installation simpler and less expensive, (b) Tube side cleaning is possible without bundle removal, (c) The design uses one half of the tube-to-tubesheet joints, reducing the risk of leak failures, (d) the design is generally less prone to thermal stresses, and (e) It is generally possible to have higher surface area within the same volume by eliminating the need for the floating head at one end. Despite the advantages, U-tube designs do suffer from a significant liability related to cleaning. The tube bends, particularly the tighter bends on the innermost tubes, can present a challenge to traditional hydroblast techniques, which can often fail, even damaging tube integrity, when trying to remove fouling from the bends. For this reason, U-tubes are often avoided in favour of traditional straight-tube designs.
Compact tube layouts are another way that higher heat transfer surface areas can be imparted in traditional tube and shell designs. The default design for fouling services is a wide, square pitch layout. This design sacrifices tube count for cleaning effectiveness with hydroblasting, providing open channels through the bundle through which hydrojets may be directed. Even with these âcleaning lanesâ however, hydroblasting is unable to reach 100% of the tube outer surface with sufficient momentum to provide complete cleaning. Typical results from hydroblasting alone result in exchangers returned to service at less than 80% of design performance. This reality impedes any consideration of more dense tube layouts, such as triangular pitch, which offers no cleaning lanes for hydroblasting. Similarly, the adoption of twisted tubes and other modified tube designs to improve heat transfer has been hindered by concerns about foulant removal during cleaning.
Twisted tube designs (e.g. Twisted Tube® from Koch Heat Transfer) provide improved heat transfer through increased surface area and improved flow characteristics. Performance improvements over standard straight tube exchangers can exceed 40% in the same volume. These bundles however can present a challenge for traditional hydrojet cleaning when fouled.
Novel heat exchangers designs, such as welded plate exchangers provide very high performance in a small volume. These designs however are often not selected in fouling services because of concerns around cleaning effectiveness.
Better Cleaning Technologies
Fortunately, there are two well established technologies which have the potential to alleviate these concerns, providing the possibility to address the cleaning difficulties experienced with these compact designs. Ultrasonic and thermal cleaning technology are now industrially available and have shown promising results with many of these more efficient heat exchangers.
Clean As New provides ultrasonic cleaning and has successfully cleaned many types of compact heat exchangers in severe fouling services, including U-tube, welded plate, spiral, and twisted tube exchangers. Clean As New uses Tech Sonicâs Ultrasonic technology, which works by allowing ultrasonic energy, in a large bath filled with suitable cleaning chemistry, to penetrate throughout the entire volume of a heat exchanger, loosening the fouling on both the OD and ID, which may then be effective rinsed away by hydroblasting. Normal hydroblasting techniques may be used on the ID to ensure perfect cleaning on the ID of any tube type or configuration. Because of the action of the ultrasonic bath to loosen the fouling, normal bundle blasting on the shell side is able to completely remove all fouling, including entrained fouling.
Figure 1. A heat exchanger being lowered into an ultrasonic bath (courtesy Clean As New)
Heavily fouled welded plate heat exchangers are routinely cleaned to like-new performance in the companyâs Baytown Texas facility. The example pictures in Figure 2 show a welded plate exchanger from a âcrude/residâ service which is restored to near 100% of clean design performance using a combination of ultrasonic cleaning and high-pressure rinsing.
Figure 2. A badly fouled welded plate exchanger, cleaned using ultrasonics.
Another example, Figure 3, shows an example of a badly fouled twisted tube bundle used in a naphtha cracker cleaned using the ultrasonic method. In total, 12 units were cleaned in four days, each unit being returned to like-new performance levels.
Figure 3. Twisted Tube® bundles cleaned using ultrasonic technology (courtesy TechSonic)
Thermal cleaning offers an approach to cleaning compact heat exchangers fouled with materials that are not suitable for ultrasonic cleaning. Thermo-Clean, a Belgium-based company, has developed an advanced thermal cleaning system that is able to address difficult-to-clean hydrocarbon fouling, such as polymers, completely on even the most compact heat exchanger designs. Figure 4 shows a spiral heat exchanger, fouled with polyethylene. This exchanger can be completely cleaned of the polymer fouling by this technique, which under tightly controlled thermal and atmospheric conditions, will reduce any hydrocarbon fouling to ash, which is then rinsed away.
Figure 4. A spiral tube exchanger cleaned using controlled pyrolysis (courtesy Therm-Clean)
A combination of ultrasonic and thermal techniques may be used when the fouling includes both polymer and inorganic material, such as scale on either the tube- or shell side. Thermal cleaning is not a suitable technique for inorganic fouling whereas most inorganic fouling may be removed quickly and completely using the ultrasonic method. In these cases, removal first of the inorganic scale by ultrasound followed by polymer removal by pyrolysis can restore even the most compact heat exchangers to 100% of design performance.
By demonstrating to the industry that these new approaches have the ability to clean compact exchanger designs in even challenging fouling services, and with a growing body of data to prove it, companies like Clean As New and Thermo Clean are easing the industryâs concerns with using compact exchanger technologies in fouling services and offering new opportunities to improve performance.
About the authors:
Roberto Tomotaki is a veteran of the oil and gas industry with over 25 yearsâ experience in heat exchanger design, monitoring, innovation, and troubleshooting. He currently provides consulting services to Becht Engineering and Clean As New.
Byron Kieser has a 30 plus year career in academic research, teaching, chemical instrumentation business development, marketing, and ultrasonic technology development. He is the Director of R&D for Tech Sonic.