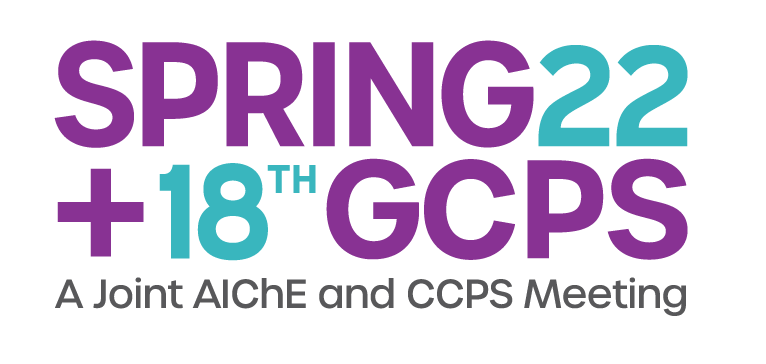
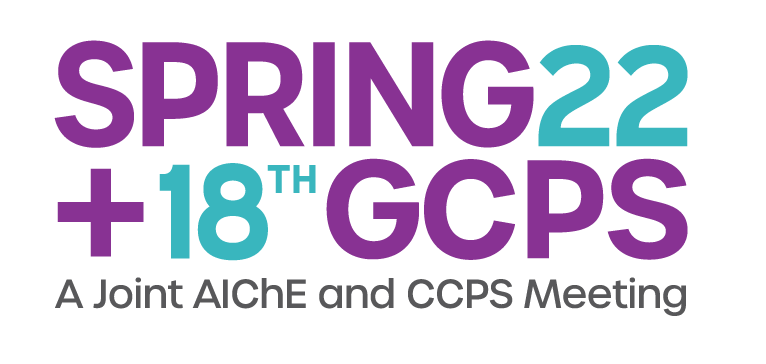
While similar comments can be found in other expert articles supporting the intensive, industrial complexes surrounding the US Gulf Coast, it doesnât mean that oil refineries and chemical plants can continue to operate as theyâve done in the past.
In order to remain competitive, US Gulf Coast processors will need to adopt new technologies and methods, in their pursuit of both profit margins and favorable public opinion. To remain relevant, and be seen as part of the clean energy future, these processors need to demonstrate a mindset for employing new technologies that reduce the energy these plants consume and the emissions they create.
One of the leading culprits for energy consumption in these Coastal plants, are the thousands of âheat exchangersâ required by these processors for the refining of the raw materials. The key challenge with the various forms of heat exchange equipment such as: boilers; chillers; evaporators; condensers and heatersâis simply, that they become dirty or fouled.
The annual loss attributable to heat exchanger fouling in the US and UK together is $16.5 bilÂlion. Heat exchanger fouling has a direct impact on plant profitability and is one of the costliest problems facing the refining and chemical industries today.
Heat exchanger fouling can cause a wide range of problems to occur if action is not taken to periodically remove deposits or pre-emptively, prevent deposit-formation in the first place. For the purposes of this paper, we focus our presentation on two of the more notable problems:
- Fouled heat exchangers require far more energy to operate, Vs., when they are clean,
- CO2 emissions increase exponentially in fouled heat exchangers if left unresolved.
In most industrial situations, the inefficiency of heat transfer resulting from fouling has a direct link to excess fuel consumption in the process. In addition to the appropriate selection of operating conditions and exchanger geometry, there are numerous chemical and mechanical methods to mitigate fouling and to remove deposits from the heat transfer surfaces.
However, all methods to reduce fouling require some understanding of the mechanisms of the deposition process, the structure of the deposits and the factors which govern adhesion to the heat transfer surfaces. Even with optimal design and operation, cleaning of the heat exchanger surfaces eventually becomes necessary.
Having to clean is by no means a new phenomenon. In fact, this dirty equipment continues to foster a multi-billion dollar collective of industrial-services companies, dedicated to this annual expenditure by US Gulf Coast refiners & processors.
What if there was a technology that significantly reduced heat exchanger fouling and in some cases eliminated the cleaning cycle for years?
This paper will reveal the results from a study conducted by one of the major, US Gulf Coast refiners as they adopted a specific fouling mitigation technology in Europe, to reduce energy consumption within one of their processing units.
Empirical data shared from the 16 month trial, demonstrates that specific goals of overall fouling reduction and increased ârun-lengthâ, were achieved for this particular refiner. However, it was the energy recovery portion and reduction in process emissions, that topped the operational benefits. The annual energy recovery was documented at US $1.4million for this one processing unit.
Donât mistake this paper for just another technology vendor hawking their wares. We chose to draw your attention to heat exchanger fouling, because itâs a big beast. Are there other waste culprits? Sure. But consider this: One of, if not the largest, petrochemical refiners in the Gulf Coast has processing facilities in both Beaumont and Baytown (TX). Collectively, they will clean over 2500 heat exchangers annually, due to fouling. How much energy could be recovered, if they didnât have to clean?
Achieving cleaner energy is indeed possible. Exploring this future through cleaner processing equipment, via new technologies, is just one of the ways Gulf Coast processors can ensure themselves of being part of the sustainable, profitable and forward thinking industries in the region.