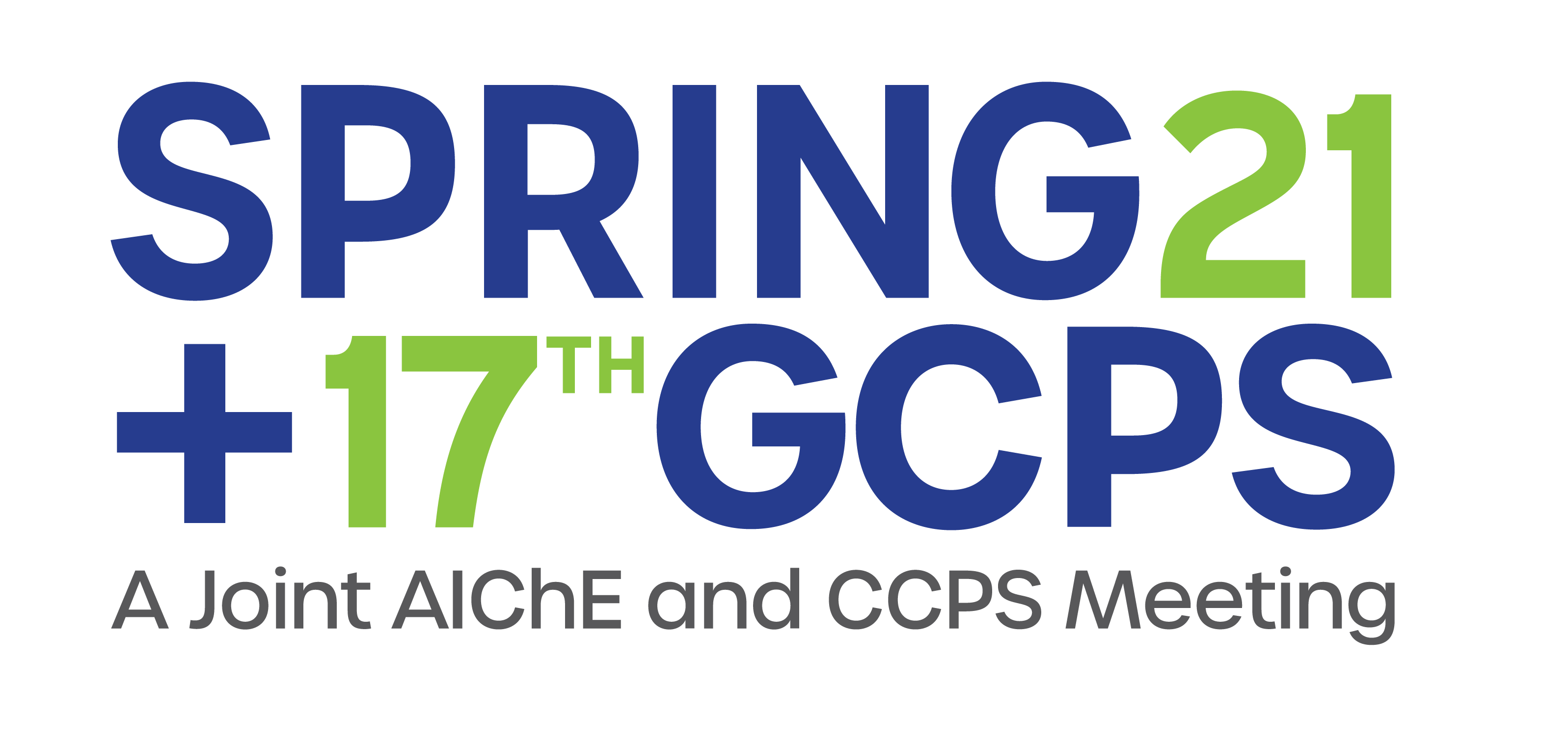
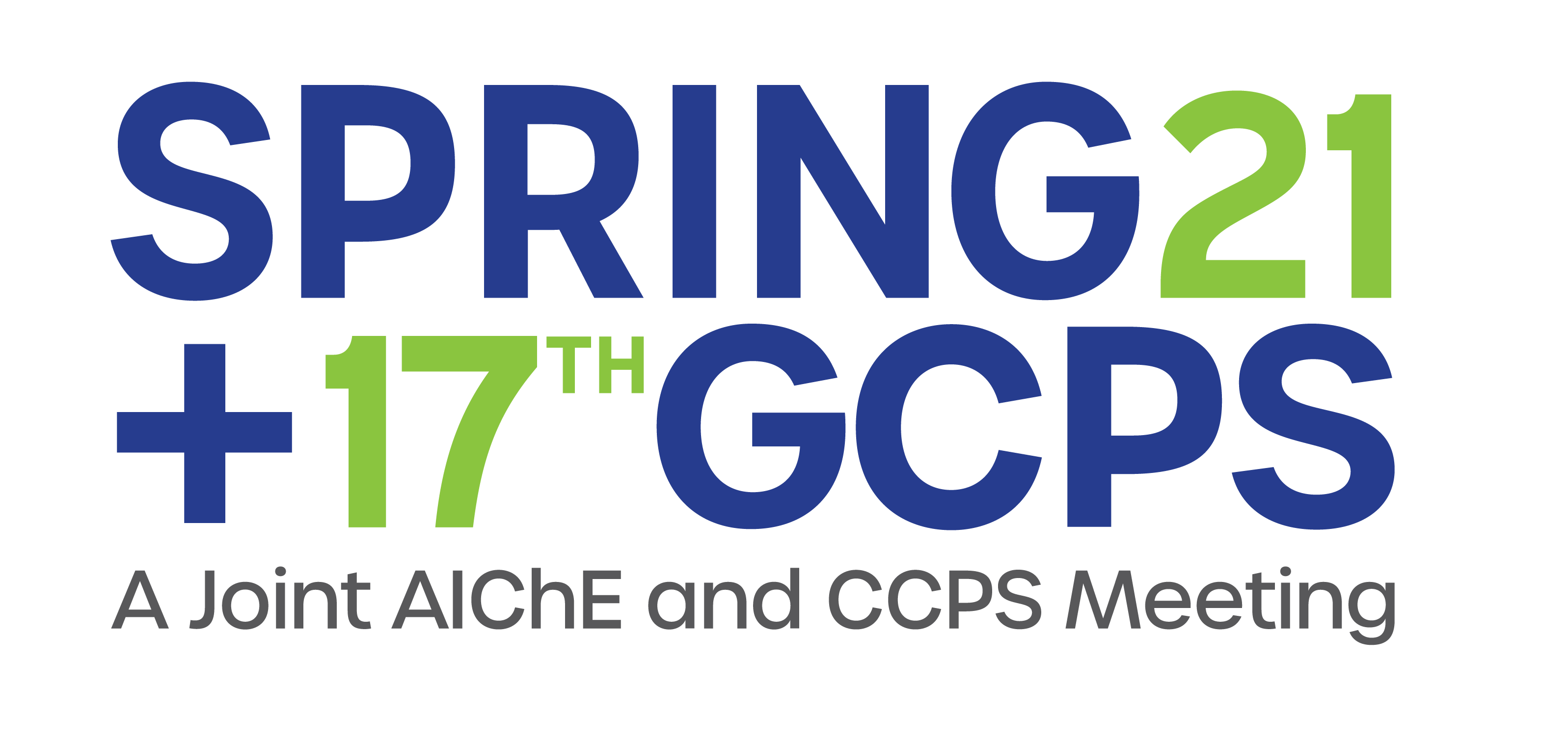
Contact Information |
|
Presenter Name: Bejoy K. Bharatiya |
Contact Name: Bejoy Bharatiya |
Telephone No.: +61 413 098 008 |
|
Presenter Biography: Bejoy Bharatiya is Project Lead-Process & Process Safety at DNV GL Offshore and Industrial Services (B) Sdn. Bhd. He has over 30 years of professional experience in the upstream oil & gas, refining, petrochemical, and mineral processing industry. Prior to joining DNV GL, he held various positions, Process Safety Group Lead at Saudi Aramco Shell Refinery Company (SASEF), Senior Process Safety Engineer at SANTOS (South Australian Oil Search) Pty Ltd. Australia, Senior Operations Engineer with Saudi Aramco Gas Operations, and the Principal Process Engineer of Kellogg, Brown & Root (KBR), Australia. |
Fax No.: |
E-mail Address (Required): |
|
Your Company/Department: DNV Germanischer Lloyd Offshore & Industrial Services (B) Sdn. Bhd. |
|
Abstract (max of 1500 words) Project Assurance Framework for Capital Project of a Petroleum Refinery - A Process Safety Approach Bejoy K. Bharatiya DNV Germanischer Lloyd The petroleum industry has long since recognized that certain risks are involved in the major hazard industries. It becomes a major challenge to minimize risk by comprehensive project assurance/audit framework in the project execution of a major process facility in the hydrocarbon industry. Over the years, the oil and gas industry has learned lessons from a number of process safety events and various hazards such as loss of control and loss of containment top events that could result in: fires, vapour cloud explosions, toxic and asphyxiant exposure, which occurred in various parts of the world and are not limited to the country of origin. The design and operation of process facility for the refinery and petrochemical complex have been the subject of major hazard to the oil industry. It has been the continuous effort of the industry to update the design and operating philosophies to improve the inherent safety of the processing units. The present paper is concerned with defining the major safety considerations of international oil companies, and Industry Standards in designing and operating the refinery and petrochemical process facilities. Inherently safe design and structured project assurance and audit program are mandatory to guide and drive the design intent of HSE critical systems. The main safety philosophies include: ESD and blowdown, fire and gas detection, toxic gas (H2S) detection, active and passive fire protection (including guidelines for firefighting systems and fire protection), layout HSE philosophy, process safety and containment etc. This paper provides the assurance/audit framework for a major project but does not attempt to cover in detail every aspect of safety design. Reference should be made, therefore, to specific discipline philosophies and specifications as appropriate. (Refer to Figure 1). Project audit or assurance program shall be applied throughout all the project development phases, engineering, construction, start-up, and operation via dedicated and well-structured efforts. The safety philosophy, and resulting protection of persons and assets, is combining all provisions undertaking during all project phases. (Refer to gated process, 1-6 Steps explained below). During the detailed engineering, and subsequent construction and commissioning, particular care will be taken by achieving: · Good engineering practice · Application of an all-encompassing QA system · Development and implementation of a safety management system · Design reviews at 30%, 60% and 90%, layout review, HAZID, Design Safety Review (DSR), accessibility reviews and other reviews. · Qualitative and quantitative risk assessments and IPF review · Design of installation for extreme weather conditions · Execution of an extensive pre-start up review of the plant before introduction of feed (Hydrocarbon, gas) covering both hardware and, control systems and procedures. · Conformity check with local regulations, project standards and other applicable industry standards and directives. Figure-1 Gated Process for Project Assurance/Audit Framework for Project Execution Project Assurance Review/Audit is required at all stages of project execution. 1. Pre-Financial Investment Decision (FID) stage: 1) Management: review critical contractors capability, business license, & project experiences, PEP, schedule. 2) QA/QC: review critical contractors ISO 9000 certificate, QA/QC plan, standards/policies/procedures (SPP), sample check of work records/reports etc. (see Table-1 International Codes and Standard) 3) HSE: review critical contractors ISO 18000 certificate, project HSE plan, SPP, sample check of work records/reports etc. 4) Technical: review Feasibility Study, Environmental Impact Assessment (EIA) reports., compare critical design area engineering standards against international standards as well as best industry practices, etc. Deliverable: review comments or audit findings 2. Front-end Engineering Design (FEED) Stage: 1) Management: review critical contractors capability, business license, & project experiences, PEP, schedule 2) QA/QC: review critical contractors ISO 9000 certificate, QA/QC plan, SPP, sample check of work records/reports etc. 3) HSE: review critical contractors ISO 18000 certificate, HSE plan, SPP, sample check of work records/reports, including PHAs/HAZOP/QRA etc. 4) Technical: review FEED engineering design, & risk assessment e.g. HAZID, HAZOP, QRA, etc. Deliverable: audit findings on Statement of Review for FEED, Statement of Review for FEED Safety Study. 3. Detail Design Stage: 1) Management: review critical contractors capability, business license, & project experiences, PEP, schedule 2) QA/QC: review critical contractors ISO 9000 certificate, QA/QC plan, procedures, standards/policies/procedures (SPP), sample check of work records/reports etc. 3) HSE: review critical contractors ISO 45001 certificate, HSE plan, standards/policies/procedures (SPP), sample check of work records/reports etc. 4) Technical: review Detail Design engineering design, design variation, & risk assessment e.g. closeout of HAZOP recommendations, etc. Deliverable: review comments or audit report on Statement of Review for Detail Design, Statement of Review for Detail Design Safety Studies. 4. Procurement Stage: 1) Management: review critical contractors capability, business license, & project experiences. 2) Technical: review specifications of safety critical equipment and QA/QC process. 3) Engineering requirement e.g. specification, database, drawings etc. (1). Manufacturing documents e.g. drawings, inspection & test plan, witness Factory Acceptance Test (FAT), review FAT report & Manufacturing Databook/Spare parts, etc. (2). Inspection & Test Organization documents e.g. Inspection Report, 3rd party certificate etc. Deliverable: review comments or audit findings. 5. Construction Stage: 1) Management: review critical contractors capability, business license, & project experiences, PEP, schedule, etc. 2) QA/QC: review critical contractors ISO 9000 certificate, QA/QC plan, standards/policies/procedures (SPP), sample check of work records/reports etc. 3) HSE: review critical contractors ISO 45001 certificate, HSE management system, plan, procedures, standards/policies/procedures (SPP), sample check of work records/reports etc., construction environmental monitoring, waste treatment plan, emergency response plan 4) Technical: compare critical design area project engineering standards against international standards, review construction methodologies, check list, punch list, site construction/safety/environmental/QA/QC activities, design variation, mechanical completion, handover report etc. (see Mechanical Completion Certificate Checklists for conducting site audits Deliverable: review comments or audit report, Statement of Review for Construction 6. Pre-Commissioning & Commissioning Stage: 1) Management: review pre-commissioning & commissioning plan schedule, integration plan etc. 2) Technical: review pre-commissioning & commissioning plan, isolation list, punch list, Site Acceptance Test (SAT), red-line markup drawings, design variation, witness pre-commissioning & commissioning activities, Prestart-up Safety Review (PSSR), ready for startup inspection etc. Table 1 International Codes and Standards IEC 79 Electrical Apparatus for Explosive Gas Atmospheres API RP 520 Recommended Practice for the Sizing, Selection and Installation of Pressure Relieving Devices (Part 1 and 2) API RP 521 Recommended Practice for Pressure Relieving and Depressurizing Systems NFPA 10 Portable Fire Extinguishers NFPA 11 Low Expansion Foam NFPA 13 Installation of Sprinkler Systems NFPA 15 Water spray Fixed systems for Fire Protection NFPA 16 Deluge Foam Water Sprinkler and Foam Water spray systems NFPA 17 Dry Chemical Extinguishing systems NFPA 24 Installation of private fire service mains and their appurtenances NFPA 30 Flammable and Combustible Liquids Code NFPA 72 National Fire Alarm Code NFPA 101 Life Safety Code NFPA 2001 Clean Agent Extinguishing System NFPA Fire Protection Guide to Hazardous Materials IP Model Code of Safe Practice Part 3 Refinery Safety Code IP Model Code of Safe Practice Part 19 Fire Protection at Petroleum Refineries and Bulk Storage Installations BS 5839 BS 5839 Part 1988 for Fire Detection and Alarm Systems for buildings IEC 61511 Functional Safety, Safety Instrumented Systems for the Process Industry ISO 14692 Petroleum and Natural Gas Industries Glass Reinforced Plastics (GRP) piping
This paper discusses industry experience and summarizes the salient design considerations and risk assessment to improve safety integrity in the execution of capital projects for refinery and petrochemical complex. An effort has been made to highlight the project assurance/audit framework with HSE methodologies adopted by major oil companies using project standards, and industry best practices and standards like API, ASME, NFPA, IEC, ISO etc. Emphasis has been made to increase the awareness among the discipline design engineers and process safety engineers to develop safer designs of the refinery and petrochemical facilities
|