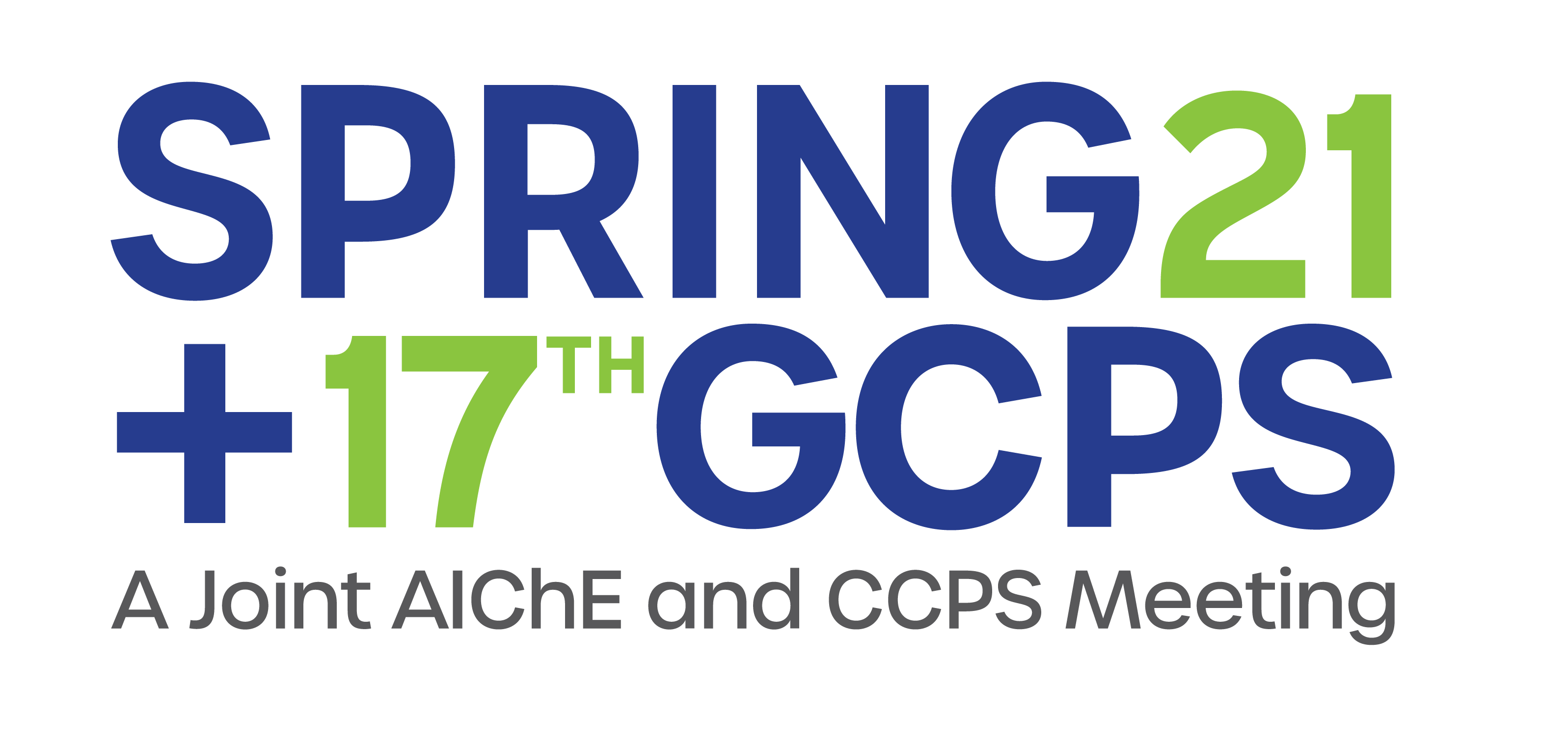
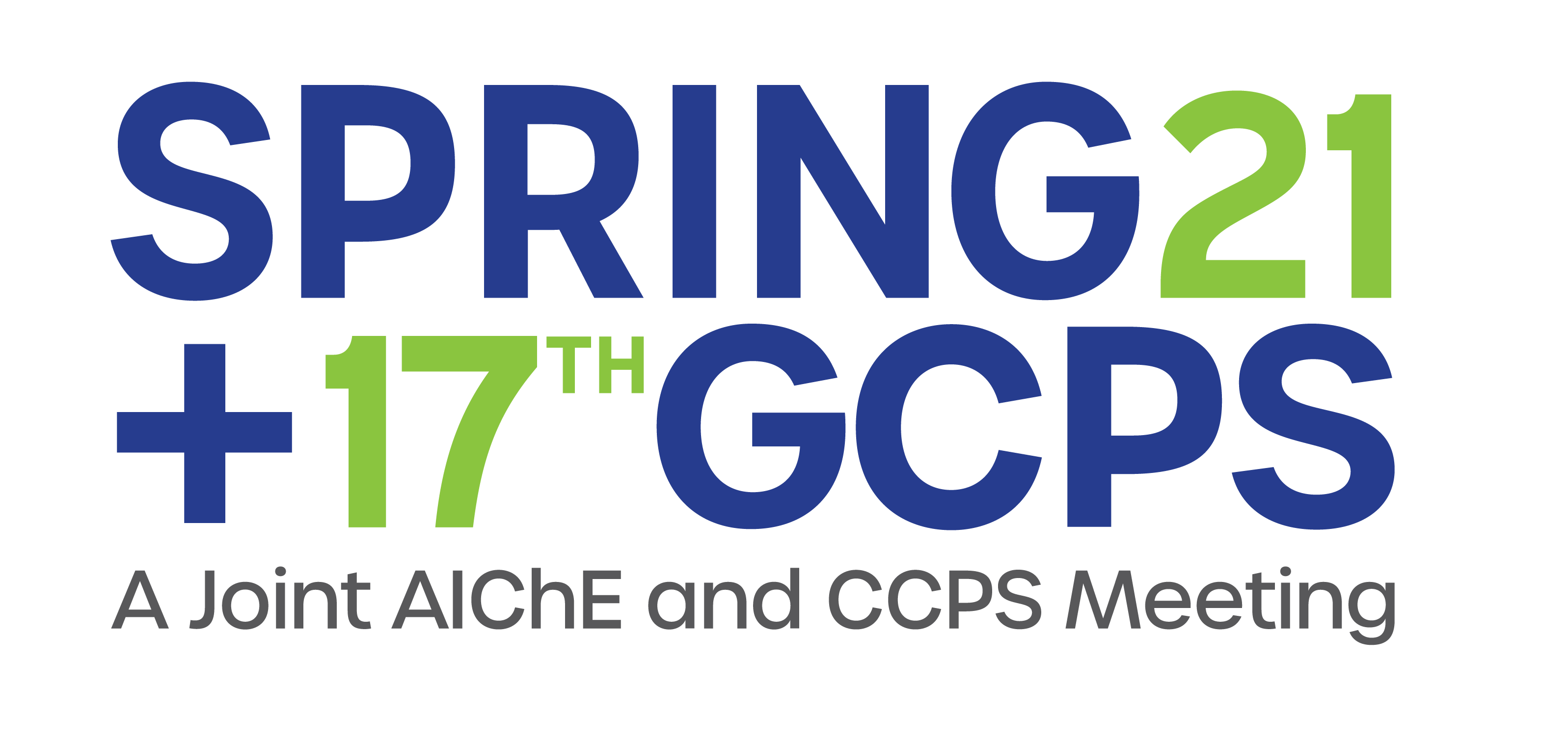
An understanding of human errors and mistakes makes it possible to identify how to reduce the possibility that they occur. Human Factors is more than common sense. There are many reasons why people may make mistakes. There are many factors that influence how people perform. A Human Factors view states that it is vital to ask why and how errors and mistakes might occur. This includes asking, for example:
- How an individualâs performance is influenced by the conditions they work in;
- Whether the information and equipment they have been given are suitable and sufficient;
- Whether the training they have been given is sufficient; and
- How an individualâs performance is influenced by the prevailing culture.
Understanding human performance is also critical to support people to successfully complete tasks. Human Factors helps to achieve high performing teams. It helps to achieve reliable teams who can be trusted to perform safety critical tasks, to be diligent, to learn, and to improve.
Process operations can be complex and involve many difficult tasks. In a process environment, with many complex tasks and safety critical operations, Human Factors methods need to be implemented systematically. The highest standard of human performance is necessary.
The Centre for Chemical Process Safety and the Energy Institute have produced (written by a Human Factors consultancy, Greenstreet Berman Ltd) a comprehensive but simple to understand handbook for people responsible for the âsharp-endâ of process plant operations and maintenance. The handbook provides practical advice, examples of good practice as well as principles, and tools. It covers how to support human performance through procedures and job aids, training and learning, effective task planning, high reliability communications, fatigue risk management, development of error management skills, and preparing people to perform emergency response tasks.
The handbook is intended for people who understand process operations, but have limited or no Human Factors knowledge. This includes Frontline supervisors, operations and maintenance managers, plant superintendents, process engineers and process safety and health and safety personnel.
The handbook expressed the view that errors and mistakes happen because of a combination of problems in the working environment and due to the support, or lack of it, offered by the organization. Directors, managers and supervisors should create the right environment for successful task performance. This is sometimes called the âsystemsâ approach to Human Factors. This means that its vital to ensure that, for example, the system of training, the system of supervision, the rota system, the system of communication and so on, are all designed to positively support successful task performance.
In order to support human performance and reduce the potential for error and mistakes, it is important to understand the nature of the tasks, the type of human performance required, and the causes of possible error and mistakes. Also, people have a range of capabilities. A general understanding of human performance can be used when designing training programme, setting staffing levels, selecting a type of job aid and many other Human Factors matters. By understanding peopleâs capabilities, ways of thinking and limitations, it is possible to design work to maximize human performance and minimize the potential for errors and mistakes. It may also be possible to train people to be more aware of how mistakes might be made. This would help people to recognize the risks or early warning signs of a mistake and give people the time and ability to prevent these mistakes from happening.
This paper will summarize how the handbook draws together latest good practice on key Human Factors topics. Each chapter can be read by itself. Altogether they provide a comprehensive aid to optimising the human factor of chemical process operations.
After providing overarching Human Factors concepts and knowledge, the first chapters cover core topics of job aids, equipment design, competence, fatigue management, staffing levels and task support.
It then moves onto error management in task planning, preparation, and control; capturing, challenging, and correcting error, communicating information and instructions. For example, it includes the role that âerror assessmentâ can play in foreseeing and preventing human error, by engaging in effective task planning and preparation. Many tasks are complex, with many task steps, creating the potential for errors and mistakes. Motivated staff can be very âtask focusedâ and intent on completing the task and solving the problems. This can create a risk of losing awareness of the situation, improvising unsafe ways of completing a task, and overlooking unexpected events or conditions that require a change in their actions. When people are task focused, they can miss âweak signalsâ around them that the situation is unsafe or is changing.
Recognising Error-likely situations can help to spot, capture and correct errors before and during operations. The handbook notes tactics for minimizing distraction and interruptions, such as âheads downâ announcements and cordoning off activities. An open team culture that invites, values, and accepts challenge is also vital. When challenges are made, they should be explored and understood. People need to be able to trust that their challenges will be welcomed by their colleagues.
It then moves onto other essential non-technical skills, including situational awareness and agile thinking. Human perception and memory possess limitations. A strong focus on one part of the situation, or element of the environment, can lead to other sources of information being neglected or missed. High workload, stress, and extensive task and time focus can impair their cognition. For any team to work effectively they must have âshared situational awarenessâ â that is, a common understanding of the event.
Non-technical skills training can increase awareness and knowledge of situational awareness and agile thinking, and allow people to practice using these skills. This is sometimes known as Crew Resource Management. For example, how to gather and interpret information, how to foresee future implications of current events, and how to recognize a mismatch between personal situational awareness and situational awareness of others, and act accordingly. Tools and job aids such as Dynamic Risk Assessment and Stop-Think-Act-Review (STAR) assessment can help people to pause and maintain awareness of the situation.
The next chapters cover the human factors of emergency response. This again focuses on non-technical skills, such as stress management, psychological resilience and challenge behaviours, as well as ensuring people have the technical knowledge and job aids such as decision trees to understand what is happening in an emergency situation and to devise appropriate actions.
Cutting across all of these, the handbook concludes with the use indicators to recognize human performance issues, and how to learn from error and performance. Every chapter of this handbook applies equally to contractors and subcontractors. Finally, a chapter covers the Human Factors of operational level change, whether this is new plant, changed procedures or organisational change. It advises on how to recognise the impact on people, assess and manage these impacts.
The scope of the handbook and the guidance, examples and tools has been specified by representatives of chemical process companies, ensuring that it is directly applicable and practical. It focuses on existing process operations. The handbook is in press and is expected to be published in late 2021.
Presenter(s)
Language
Pricing
Individuals
AIChE Member Credits | 0.5 |
AIChE Pro Members | $19.00 |
AIChE Graduate Student Members | Free |
Safety and Health Division Members | Free |
AIChE Undergraduate Student Members | Free |
AIChE Explorer Members | $29.00 |
Non-Members | $29.00 |