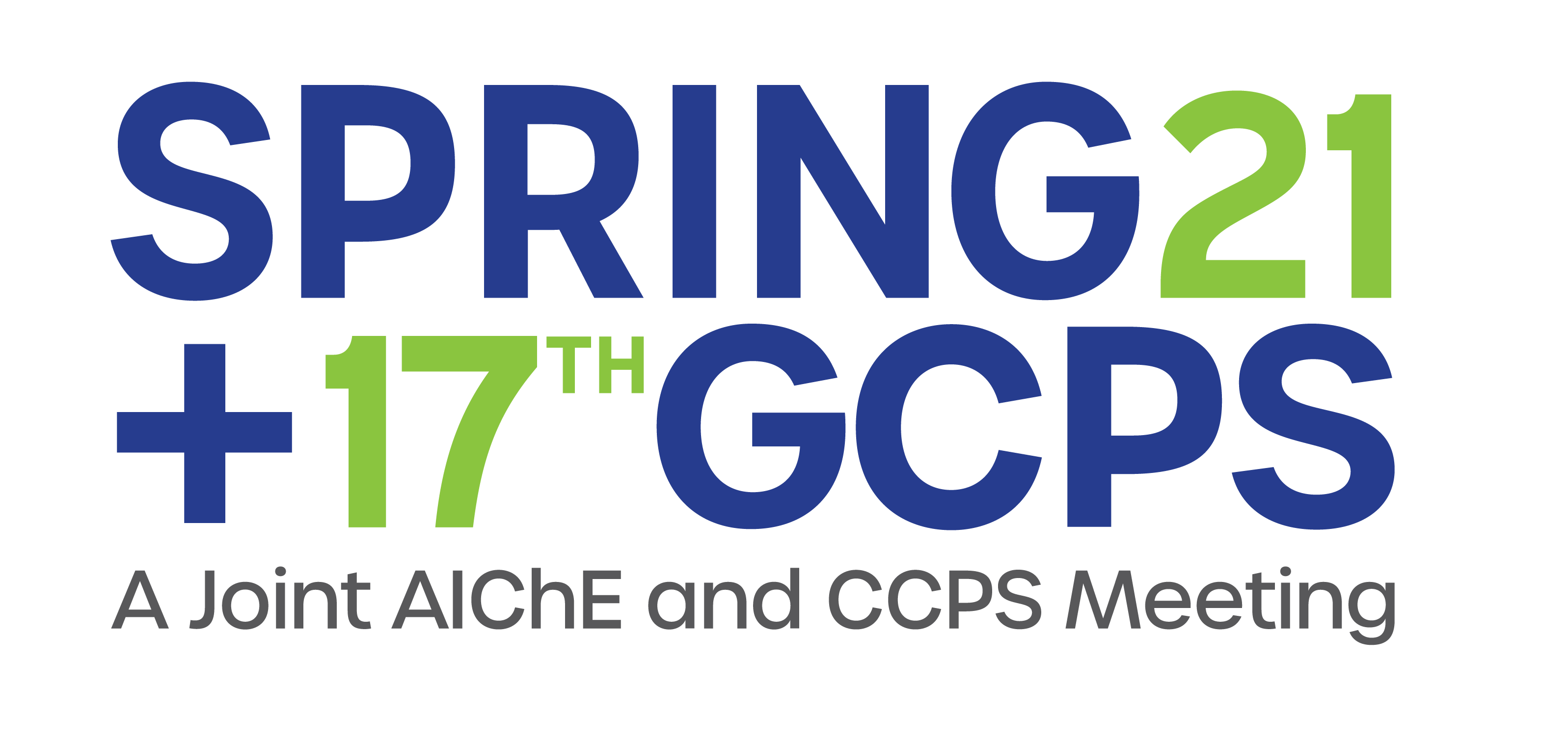
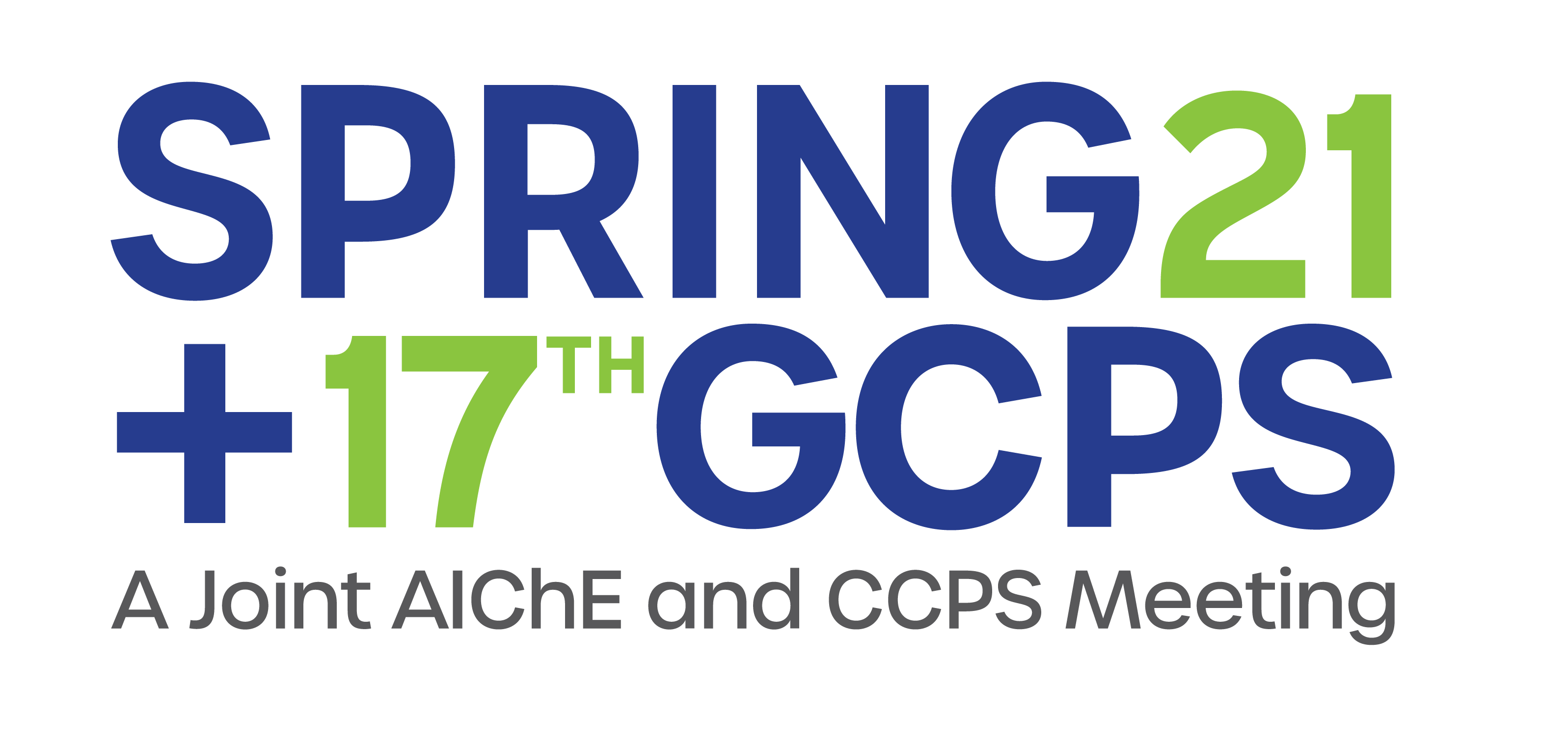
Computational fluid dynamics (CFD) modeling has enabled a deeper understanding of complex mixing of high viscosity materials that enables more predictable decisions when designing process equipment. In industry, this translates to more effective investments that target improved efficiency and productivity as a result of more informed design decisions. In silicone rubber, heating and cooling of the rubber is a mostly non-value added step within the production process that has a significant impact on cycle time and overall production capacity. In this instance, CFD modeling was used to model the heating and cooling of high viscosity uncured silicone rubber at different scales in sigma blade-style high viscosity mixers. This modeling was able to determine not only optimum heating and cooling conditions, but also enabled decision making on what mixer sizing would prove optimal for processing of similar material.
Presenter(s)
Once the content has been viewed and you have attested to it, you will be able to download and print a certificate for PDH credits.
If you have already viewed this content,
please click here
to login.