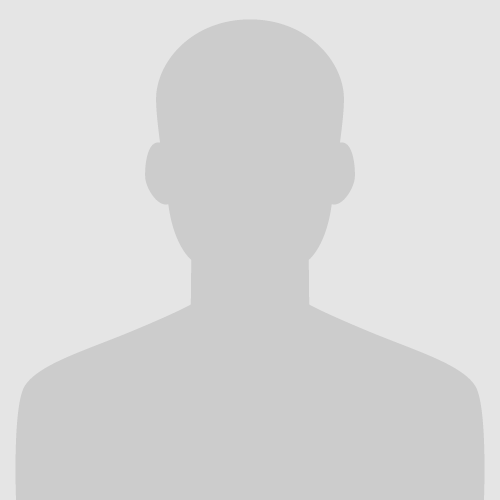
Accelerated development of novel processes and their scale-up and commercial deployment, involves reduced number or right-sizing of experiments and possibly step-skipping. A combination of scale-down from feasible commercial embodiments and risk managed scale-up can maximize the success of process development. In this session we explore examples and methodologies for accelerated process scale-up.
Session Chairs:
- Anastasios Skoulidas, ExxonMobil
- Omid Ebrahimpour, DuPont
Schedule:
TIME (EDT) | PRESENTATION | SPEAKER |
---|---|---|
11:00 AM | Scale-Up of Particulate Processes - Lessons from Industry | Timothy A. Bell, DuPont (retired) |
11:30 AM | Immiscible Liquid-Liquid droplet dynamics – A CFD model for robust scale-up and risk mitigation | Johannes Wutz, M-Star |
12:00 PM | Features of ProSim’s BatchReactor software for Scale-up & Scale-down | Benjamin Wincure, ProSim |
12:15 PM | Accelerated Development of Processes: Case study of silicon-to-operations scale-up and risk management | Anastasios Skoulidas, ExxonMobil |
Abstracts:
Scale-Up of Particulate Processes - Lessons from Industry
Timothy A. Bell, DuPont (retired)
In 1985 Merrow quantified the challenges of starting up new processes that included particles as feedstocks or intermediates. A later publication by McNulty reaffirmed the critical need to pilot new processes that include particles. This presentation will attempt to describe why particle processes are difficult, and provide some suggestions on how best to pilot them. Several case histories of piloting/testing challenges are included.
Immiscible Liquid-Liquid droplet dynamics – A CFD model for robust scale-up and risk mitigation
John A Thomas, M-Star Simulations, USA; Brian Devincentis, M-Star Simulations, USA; Johannes Wutz, M-Star Simulations, Germany; Francesco Ricci, Boehringer-Ingelheim Pharma, USA
Liquid-liquid systems have a wide range of applications in many fields of the industry. In chemical manufacturing, such liquid immiscibility is most commonly utilized for the purpose of chemical separations by liquid-liquid extraction. Such interphase phenomena depend highly on the droplet size distribution.
Figure 1. High resolution turbulent dissipation rate of a lab-scale system.
We begin by performing high resolution direct simulation of two immiscible fluids blending in a lab-scale agitated vessel (Figure 1). We compare droplet size predictions from this model to first-principles turbulence theory, as well as experimentally measured droplet data. We then use this direct model to simulate the break-up of individual droplets moving through the impeller trailing vortex. From these predictions, we develop a predictive relationship between energy dissipation rates and break-up volume fraction.
Figure 2. Dispersed phase from direct simulation shown as spheres for the complete simulation time.
We can extract the breakup characteristics of these two-phase immiscible direct simulations and use this knowledge for the design of a model that can be used for larger volumes. The direct simulation provides data on the size and position of the droplets and by detecting step changes in the droplet volume, we can isolate break-up events (Figure 2). Then, we use a Large Eddy turbulence model (LES) in combination with Lagrangian particles as the dispersed phase to reproduce the droplet size distribution from the direct method with this much faster setup. We are using a hard core-soft shell approach for the particles in this Eulerian/Lagrangian/DEM hybrid model (Figure 3).
This approach allows us to accurately predict droplet size distributions in larger scales in an efficient and fast CFD environment. In order to address full scale production vessels, we use a parcel approach based on the Eulerian/Lagrangian/DEM hybrid model. All three models predict similar droplet size distribution while each abstraction speeds up the simulation time significantly.
Figure 3. Time evolution of the droplet positions for the Eulerian/Lagrangian/DEM hybrid approach.
Features of ProSim’s BatchReactor software for Scale-up & Scale-down
Benjamin Wincure, ProSim
ProSim’s BatchReactor® software [1] is dedicated to the simulation of batch chemical reactors, which provides the user with a detailed modeling of the reactor (heating/cooling system, condenser, mixing device… ), a reliable description of the production recipe, and an analysis of scale-up or scale-down based on the volume or diameter of the reactor, for a reactor with uniform mixing (perfectly mixed). BatchReactor® allows modeling of complex systems by taking advantage of the power of Simulis® Thermodynamics (thermodynamic properties server) which offers an extensive set of thermodynamic models and a pure components database of more than 2,300 pure components (AIChE’s DIPPR® database [2]). Moreover, thanks to the user “interpreted” kinetic rate model available through Simulis® Reaction (chemical reaction server), any kind of specific reaction models can be used in BatchReactor®, including classical models (equilibrium, kinetic, instantaneous) and bio models (Monod, Hill, Comtois, Competitive inhibition, Uncompetitive inhibition, Non-competitive Inhibition, etc). This is essential to represent kinetic bio-reactions with often non-classical laws [3]. So, in BatchReactor®, a stoichio-kinetic model can be coupled with thermodynamic and heat transfer models already available in the software to simulate the bio-reactor.
The strengths of the BatchReactor simulation are accurate thermodynamic and transfer phenomena representation, classical and bio reactions, recipe description, and a user-friendly interface.
Accelerated Development of Processes: Case study of silicon-to-operations scale-up and risk management
Anastasios Skoulidas, ExxonMobil
Acceleration of process development requires all the pieces of an organization to be working in unison. Management and business lines have to be open to innovation, aligned and willing to accept business risks. Teams must be empowered and agile, and many different parts of the development have to be progressing in parallel. A rapid pace of development requires the cooperation of multiple disciplines and frequent and open communication. In this presentation, we detail the development of a mechanical solution to improve the flow distribution and performance of fluidized bed reactors. This new type of hardware was discovered with the help of computer simulations, was scaled-up, approved for field application, installed and started up in less than 8 months. We describe the risk management approach and how we ensured the alignment and buy-in of key stakeholders that made the field application possible.