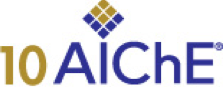
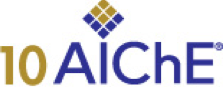
In recent years, the global tightening of emissions standards has created numerous challenges for the owners and operators of ethylene cracking furnaces. Achieving ultra-low NOx emission levels in ethylene cracking furnaces, where the operating temperatures routinely range between 2000°F to 2200°F can prove a difficult task. In addition, the harsh environment in these furnaces, such as high temperatures, poor fuel quality, difficult-to-predict furnace currents, and so on, often create other problems, such as burner tip plugging and poor flame patterns.
This paper outlines the process Zeeco used to achieve Ultra Low NOx emissions in an ethylene cracking furnace. The burner used was the ZEECO® Ultra-Low NOx Free-Jet Burner. Maintenance costs on the burners were also reduced because of the design characteristics of the burner, which is discussed in more detail.
NOX emissions from this particular furnace have been reported at a sustainable 0.04 lb/MMBtu to 0.05 lb/MMBtu (31 ppmv to 39 ppmv corrected to 3 percent O2 dry). This is impressive given this application has high temperatures near the furnace floor, which were measured at approximately 2100°F. To achieve low emissions, the ZEECO Ultra-Low NOx Free-Jet Burner technology entrains, recirculates and mixes inert furnace gases into the combustion zone, without using external flue gas recirculation. To reduce NOX production, this free-jet technology also delays combustion and lowers the flame temperatures.
In ethylene cracking furnaces, the harsh environment and high temperatures often create problems with the burner tips plugging. These incorrectly-designed burner tips are exposed to intense radiant heat, and the internal temperature of the tips may reach high enough levels that thermal cracking of the fuel's heavier components occurs. In addition, fuel-carried liquid droplets may reach a fuel tip that is exposed to elevated temperatures. Once thermal cracking, &'coking,&' of the fuel initiates in the tip, deposition of coke inside the tip accelerates, eventually plugging the tip. To avoid these coking problems, the ZEECO Free-Jet design limits the tip's exposed surface area to radiant heat. Compared with other burner technologies, the ZEECO Free-Jet Burner tips have less area and are positioned to protrude less than an inch into the furnace. In addition, the free-jet burner design does not incorporate ignition ports, as other burner technologies require. By eliminating the need for smaller ports on the tips, the burner is less susceptible to plugging by debris, such as scale or other material that can be carried by the fuel to the burner.
The results of installing a free-jet burner are low emissions, lower maintenance costs and a good flame pattern. This paper discusses the free-jet design and how it achieves low emissions, as well as, presents pictures and data from the installation.