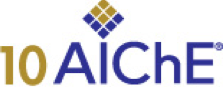
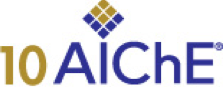
Chemical and energy conversion systems based on microchannel process technology (MPT) demonstrate high performance in applications in which rates are controlled by diffusive heat and mass transfer flux. MPT-based heat exchangers, absorbers/desorbers and chemical reactors all benefit from process intensification and have been used in a variety of mobile energy conversion systems including fuel reformers/converters, heat pumps and waste heat scavenging technologies. The service environments typical of MPTs often require the devices to be fabricated from metals such as aluminum, titanium, stainless steel or high temperature super alloys. Flow channels and associated critical dimensions in these devices can be as small as 50 um, but generally range from 100 to 1000 um in width and height with characteristic flow channel lengths normally in the mm to cm range. High surface area architectures (e.g. wicks or textured surfaces) are often included in the flow channels as well for enhanced mass transfer and/or catalytic functionality. Fabrication of MPT devices has historically been performed using a stacked-shim approach in which individual metal sheets are first patterned with micro- and meso-scale flow features and subsequently bonded in a stack to create an array of miniaturized, parallel flow paths. Typical proof-of-concept fabrication efforts have utilized photo chemical machining (PCM) for shim patterning and diffusion bonding or diffusion brazing for joining of shim stacks. While flexible and capable of supporting technology demonstrations, these techniques can be expensive at prototyping volumes. The high costs associated with these fabrication processes has contributed to a perception that MPT technology is expensive and will be relegated to a small application space. Recent work at the Microproducts Breakthrough Institute (MBI) has focused on exploring the cost structure of high volume manufacturing approaches for MPT devices in an effort to identify new paths to lower cost fabrication. Through systematic exploration of fabrication process capabilities and associated cost structures, the MBI is developing volume-sensitive cost estimation models for predicting manufacturing costs of MPT devices fabricated using different processing technologies. The process-based cost models are used to develop an understanding of the economic trade-offs between candidate processes and are utilized in a design for manufacturing approach to MPT device development. In this paper we present results and analysis of the cost modeling effort to date and apply the methodology in a case study of a stainless steel MPT device designed, built and tested by Pacific Northwest National Laboratory. Extensions of the model to adjacent material sets and the interaction of device designs with fabrication processes will be discussed.