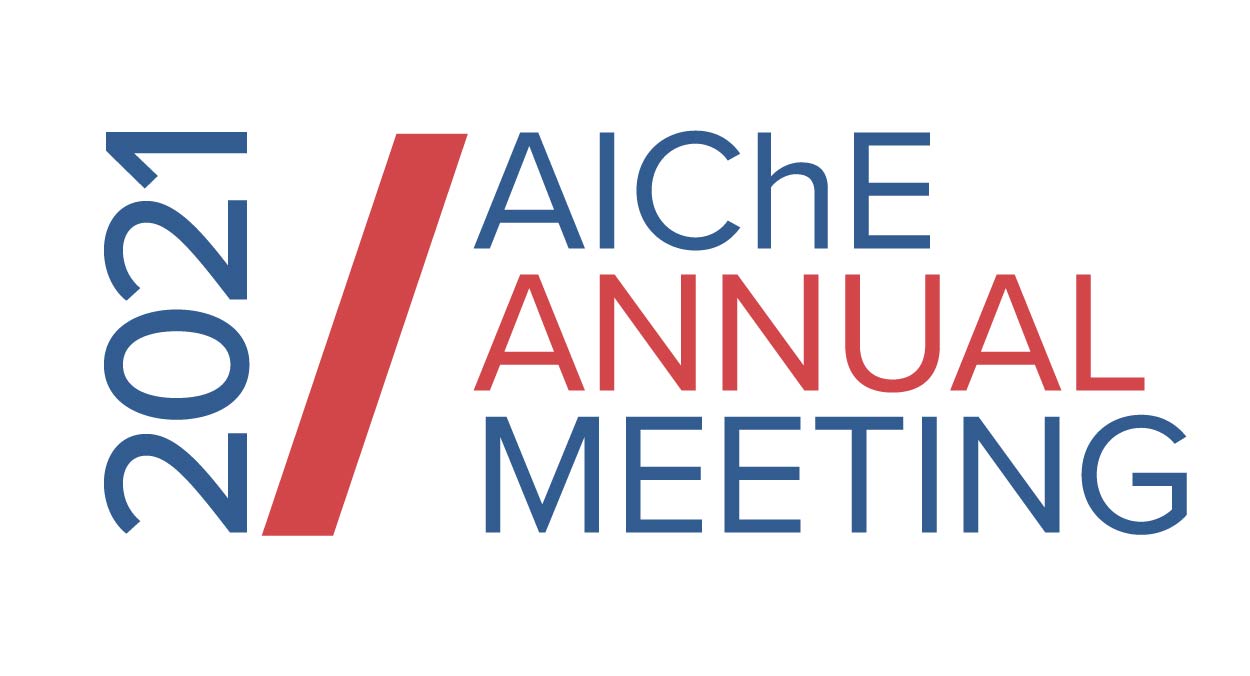
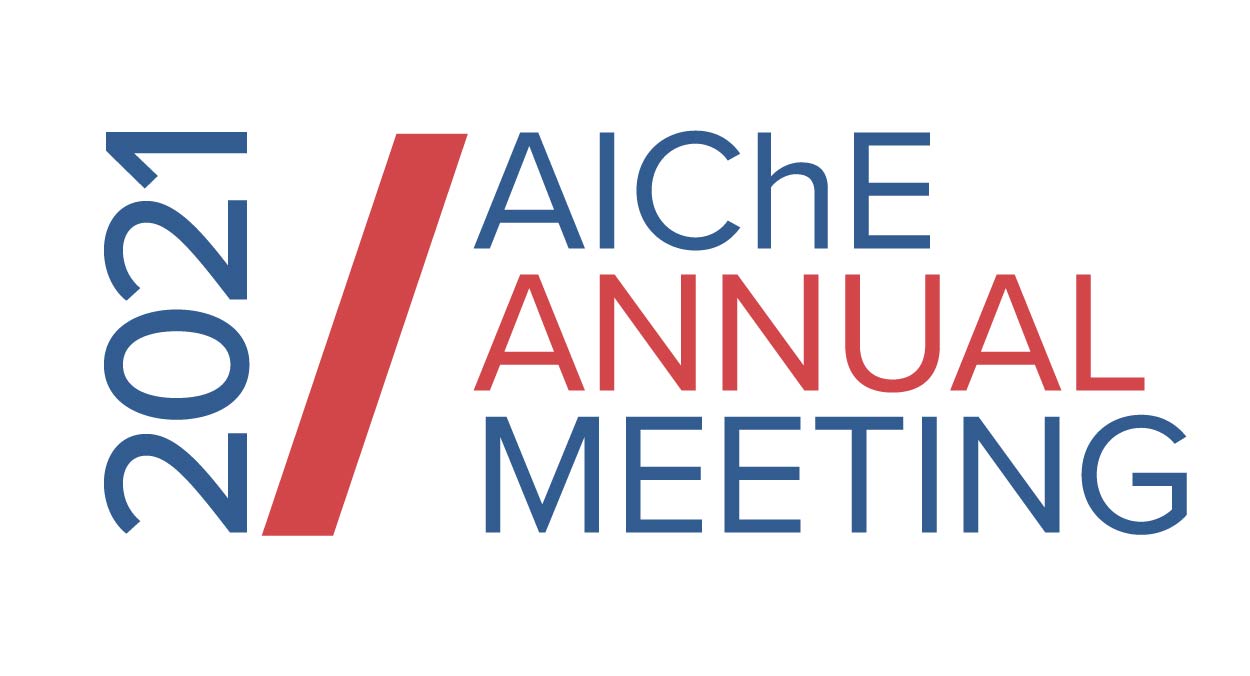
Light olefins such as ethylene, propylene and butadiene are the key building blocks for all kinds of plastics and high-value chemicals, the production of which is driven by population growth and prosperity. Today, steam cracking of hydrocarbon feedstocks is the leading technology to produce these building blocks. As very high temperatures of up to 1130 K are needed for the reactions to occur, steam cracking takes place in tubular reactors suspended within large-scale fireboxes, i.e., furnaces fired by numerous floor and sidewall burners.
In industrial practice, it is often assumed that the temperature in a steam cracking firebox is completely uniform or at best changing according to the height of the furnace, hence disregarding the complex 3D heat transfer phenomena that take place. Adjustments to the firebox conditions are generally avoided during operation because of the difficulty to measure their impact. Only secondary measures like stack oxygen and NOx concentrations, bridgewall temperatures and coil outlet temperatures are monitored. Because steam cracking fireboxes are in fact far from uniform, it is impossible to pinpoint problem areas using only such discrete measurements that are typically located at the boundaries of the firebox. Bad burner management can cause excessive CO, NOx or soot formation due to suboptimal combustion conditions1. Additionally, flame rollover and impingement can occur2, resulting in a non-uniform heat flux to the reactor coils and even hot spots3. The main possible handles to alter the performance of steam cracking furnaces are the air flowrates to the burners. Typically each burner has one or more air ducts to be able to adjust each burner separately or even adjust different air flowrates to a single burner. As more than 100 burners can be present in an industrial steam cracking furnace, this results in a huge amount of degrees of freedom during the operation of the furnace. Because of the high temperatures obtained when combusting fuel gas with air, thermal NOx formation is another significant issue in steam cracking furnaces. Furthermore, there is only a narrow window of combustion temperatures in which nearly full combustion is achieved while NOx formation remains low. This balance needs to be achieved in industrial burners, especially in high-temperature applications such as steam cracking furnaces.
Given the importance of the above considerations, in this contribution, 3D CFD simulations are used to evaluate the effect of altering the air distribution to the furnace. In particular the ratio of primary to secondary air towards the floor burners and the sidewall burners is investigated to evaluate what the optimum is to minimize NOx formation and maximize run length.
Methodology
The 3D firebox simulations are performed using the commercial CFD software Ansys FLUENT 19.0. Conservation equations for mass, momentum, species and energy are solved for a compressible fluid. Turbulence is modeled using the RNG k-ε turbulence model. The detailed GRI 3.0 chemical kinetic network with 325 reactions and 53 species is used to model the non-premixed combustion in the steam cracking firebox. To achieve reasonable computational effort, it is impossible to model every ordinary differential equation for all components in every cell at each iteration, so this mechanism is implemented in a tabulated way using non-adiabatic steady diffusion flamelet modeling.4 Thermal NOx formation is modeled using the Zeldovich mechanism5, using separate conservation equations calculated as a post-processing step, as implemented within FLUENT. The discrete ordinates model is used to solve radiative heat transfer.6
The geometry of the reactor coil is that of a multi-pass coil with 2 inlet tubes per outlet tube. A total of 16 floor burners and 32 sidewall burners provide the heat to the reactor.
Results and discussion
Effects of air distribution to floor burners
Simulations using different primary/secondary air ratios on the floor burners are performed to check their effect on furnace performance. The impact on flame shape, tube metal temperatures, run length and NOx formation is examined. To compare, two primary/secondary air ratios will be used: 25/75 and 75/25. The primary/secondary air ratio of the sidewall burners is kept at 50/50.
An evaluation of the streamlines in the furnace indicates that a large recirculation zone appears in the middle of the furnace when using more secondary air (see Figure 1). This affects the interaction between the floor and sidewall burners, and consequently the incident radiative heat flux (IRHF) to the coils. The simulations indicate that the outlet passes in the 25/75 case have a more uniform IRHF over the furnace height, with the top and bottom of the furnace having a higher IRHF compared to the 75/25 case. This results in a lower maximum TMT in the 25/75 case, which in turn results in significantly reduced coke formation and hence a 66% increase in run length compared to the 75/25 case.
When looking at the simulated NOx concentrations at the exit of the firebox, a significant decrease is found when decreasing the amount of primary air. The 75/25 primary/secondary air ratio results in a calculated NOx amount of 314ppm, compared to 205ppm for the 25/75 primary/secondary air ratio, which is a 53% increase by adjusting the air registers to the burners.
Effects of air distribution to sidewall burners
To check the effect of air distribution towards the sidewall burners, two different primary/secondary air flowrate ratios have been tested: 100/0 and 50/50. For the floor burners a primary/secondary air ratio of 25/75 is used because this was the best case according to the above explanation.
The 100/0 case results in spread-out flames, covering the whole sidewall area due to the high velocity of the premixed fuel/air mixture exiting the burner head. In the 50/50 case on the other hand more compact flames are observed. The simulations also show a significant impact of the floor burner flow pattern and the corresponding recirculation zone in the middle of the furnace. The corresponding different IRHF profile obtained by altering the air flowrates to the sidewall burners again results in a different coking rate over the reactor and therefore a different run length. The effect is however smaller than the effect of the floor burner air distribution: a 13% longer run length is observed for the 100/0 case compared to the 50/50 case.
There is a decrease in NOx formation with increasing primary air, i.e. 205ppm for the 50/50 case and 143ppm for the 100/0 case. This is caused by the increased velocity of the fuel-air mixture exiting the sidewall burner head. An increased velocity results in a more spread-out flame. Although the peak temperature is higher in the 100/0 case, the residence time in this high temperature region is so low that a lower amount of NOx is formed. Therefore the shift to more primary air results in a NOx reduction for the sidewall burners.
Conclusions
In this contribution, highly detailed 3D CFD simulations are performed of an industrial steam cracking furnace. The effect of the air distribution is investigated by manipulation of the primary to secondary air ratio to the floor burners and sidewall burners separately. It was shown that this manipulation results in a significant impact on the performance of the firebox. This is not only applicable to steam cracking, but can be extended to steam reformers, EDC cracking furnaces, fired heaters in refineries etc.
References
- Baukal, C. E. J., The John Zink Hamworthy Combustion Handbook. CRC press: 2012.
- Sullivan, B. K., Ethylene Cracking Heater Troubleshooting. In AIChE Spring National Meeting 2015, Austin, Texas, 2015.
- Vinayagam, K., Minimizing Flame Impingements In Fired Heaters. Chemical Engineering 2007, 114 (5), 70-73
- Pitsch, H.; Barths, H.; Peters, N. Three-dimensional modeling of NO x and soot formation in DI-diesel engines using detailed chemistry based on the interactive flamelet approach. SAE transactions 1996, 2010.
- Zeldvich, Y. B., The oxidation of nitrogen in combustion and explosions. J. Acta Physicochimica 1946, 21, 577.
- Carlson, B. G.; Lathrop, K. D. Transport theory: the method of discrete ordinates; Los Alamos Scientific Laboratory of the University of California, 1965.