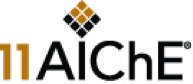
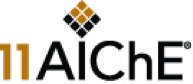
Over a period of more than 10 years of deploying industrial projects related to energy systems real time
optimization and cost reduction in processing industries around the world, the following issues have been found
time and time again:
• Many applications of energy cost reduction technologies are successful when used offline by Engineers, in
their offices, but only a few of them succeed when transferred to the Operators to be routinely used in real
time, tied to online field data and running under unsupervised automatic execution.
• Certain systems, deployed under well engineered, successful real time projects, received enthusiastically by
Engineers and Operators are not used more than for just a few months after the project completion.
• Real time systems with acceptable initial up-time figures degrade and finally are unused when the Engineer in
charge of them is promoted to a new position as a consequence of being so successful with them.
• Very well proven, sound technologies, fail when applied at a given Site while they succeed in a different
location owned by the same Company.
• After a failure with one of those advanced technology, the Site or the Company becomes “immunized” against
similar technologies and only after several years, with the renewal of the Engineering staff and young blood
that has not been exposed to the past failure, does the technology have a chance to be considered again.
This paper address some of the root causes for the above mentioned issues and discuss about the best practices that
will help to avoid project failures.
It also presents real industrial examples in which the whole utilities system of a production Site (i.e., steam, fuels,
boiler feed water and electricity) is optimized with a real time online, industrially well established software. The
examples and results correspond to projects implemented in processing units worldwide, such as refineries,
petrochemicals, chemical plants and ethanol units.
Main project steps are explained and critical details to be taken into account to assure successful use and proper
technology transfer are presented.
The optimization objective is the overall utilities system cost reduction and takes into account the constraints
associated with the existing equipment, fuels and electricity pricing and contracts, including emissions limits,
quotas and rights. The energy management system models are executed and optimized at a scheduled frequency,
fed with online, real time data, flowing into and out the program using the standard OPC protocol.
Besides the optimization, Key Performance Indicators (KPIs) are also calculated and sent back to the Site Plant
Information System or DCSs for Operations and Management use.
The paper’s objective is to help achieve a successful technology deployment, avoiding project pitfalls and ensuring
the continuous use of the real time energy systems optimization based on the proper technology implementation,
knowledge transfer and deployed system maintenance.
Presenter(s)
Once the content has been viewed and you have attested to it, you will be able to download and print a certificate for PDH credits.
If you have already viewed this content,
please click here
to login.
Language
Pricing
Individuals
AIChE Member Credits | 0.5 |
AIChE Pro Members | $15.00 |
Fuels and Petrochemicals Division Members | Free |
AIChE Graduate Student Members | Free |
AIChE Undergraduate Student Members | Free |
AIChE Explorer Members | $25.00 |
Non-Members | $25.00 |