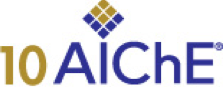
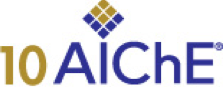
Mercury emissions from coal-fired power plants are a concern to both the state and federal governments in the U.S. US EPA had proposed to regulate mercury emissions from coal-fired power plants using the Clean Air Mercury Rule (CAMR). This two-phase program allowed trading of mercury emissions, similar to the SO2 trading program already in place. As of now, all aspects of CAMR have been vacated by a court ruling, and the EPA has committed to proposing draft mercury emissions regulations for coal-fired power plants by March, 2011. As of October 2009, nineteen states had passed their own mercury emissions regulations.
Mercury exists as the elemental form (Hg0) in the high-temperature regions of coal-fired boilers. As the flue gas is cooled, a series of complex reactions begin to convert the Hg0 to gaseous oxidized forms (Hg2+) and particulate-bound mercury (Hgp). The extent of conversion of Hg0 to Hg2+ and Hgp depends on the flue gas composition, the amount and properties of fly ash and the flue gas temperature and quench rate. The speciation of mercury in coal combustion flue gas affects the performance of activated carbon (a dedicated mercury control technology) and the removal of mercury by wet FGD scrubbers (a “co-benefit” approach to mercury control).
In order to prepare for the existing and impending mercury emission regulations, utilities must have useful tools for compliance planning. REI's MerSimTM mercury simulation tool includes homogeneous and heterogeneous oxidation kinetics, adsorption on fly ash, oxidation across SCRs, and removal and re-emission across wet FGD scrubbers. This model can be used by utilities, given inputs that are generally available to them. On the surface, this requirement might seem obvious and inconsequential; however, matching models for the complex chemistry of mercury in practical combustion systems with the information that is generally available to plant engineers is a difficult undertaking.
We have endeavored to create fundamentally based submodels for mercury behavior, but these models must be based on input data that a plant engineer can reasonably supply. An integrated model requiring inputs that are not available or difficult to obtain will not be a useful compliance tool. Therefore, a balance must be struck between the complexity of the submodels and the complexity of the input parameters, in order to provide utilities with a useful and accurate tool.
Detailed homogeneous and heterogeneous kinetic pathways for mercury oxidation are included in the MerSim integrated power plant model. Overall results of the model have been previously reported.1 However, details of some of the key submodels have not always been reported in detail. Innovation and improvement continue in the integrated model. Recently, a more detailed submodel has been implemented to predict both mercury oxidation and adsorption across regenerative air preheaters.
Using full-scale mercury speciation data assembled from previous DOE- and EPRI-funded programs,1 one can see that regenerative air preheaters promote formation of oxidized and, to a lesser extent, particulate-bound mercury. Figure 1 illustrates these points with observed values of oxidized and particulate-bound mercury at air preheater outlets.