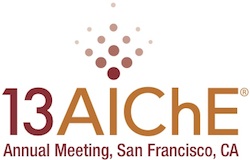
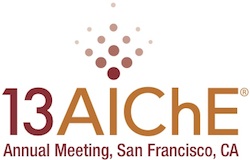
Model based development and validation of a preparative Size Exclusion Chromatography step Ernst B. Hansen , Thomas B. Hansen and Lars Sejergaard Novo Nordisk A/S , Hagedornsvej 1 , DK-2820 Gentofte , Denmark The application of mechanistic models for process development and optimization has been a topic of discussion in the Pharmaceutical industry for many years. Mechanistic models are considered as an alternative to a standard DoE type empiric approach. Most often the DoE approach is preferred based on a cost-benefit evaluation where the time consumption and the complexity are found to extensive when using mechanistic modelling. In our company we use mechanistic models for the development of selected downstream process steps. A Model based approach is preferred when a suitable model has been established , in the literature or in-house , and the process step is considered a key step regarding economy and/or product quality. The presented case deals with Size Exclusion Chromatography (SEC) as the final purification step for a therapeutic protein. The model was developed with the purpose of using simulation for the process evaluation which is done in preparation to the production scale Process Performance Qualification (PPQ). The main function of the SEC step is to reduce the content of larger proteins (HMWP and dimer). The model is based on differential mass balances for each component and includes axial dispersion and mass transfer as dispersion effects. The model was calibrated using four lab runs with variation in load , flow and bed height. The fitted model parameters for each component were the exclusion coefficient (0<Kd<1) which determines the retention in the column and the mass transfer coefficient related to dispersion (peak width). Before doing the actual process evaluation we had to deal with a challenge concerning the concentration in the product pool from the SEC step. The feed concentration to the SEC step varied quite a bit and since the SEC step can only dilute the product (no adsorption takes place) the variation in the feed concentration results in a variation in the pool concentration. As this is the final step before formulation there is a lower limit to the concentration which must be met. Using simulation we were able to create enough data to visualise the problem and come up with a new strategy for loading the column which can compensate for the variation in the feed concentration. The process evaluation is a systematic check of the performance of the step when varying the important process parameters within their operating range. Due to the experimental constraints (time , availability of product) this is often done as a reduced design (DoE). Since we were using simulation there was no need to set up a reduced design. The evaluation was thus based on 216 simulations covering the operating range of the important process parameters (e.g. load , flow , bed height , OD cut). A perhaps overlooked advantage of using simulation is that both the concentration and the content (impurity levels) of the feed solution can be varied as part of the study without any extra effort such as dilution , concentration , or spiking with impurities. Our experience of using modelling is very positive. The initial extra energy put into understanding and developing the models and the methods for calibration is worthwhile. But , contrary to the general discussion of which approach is better , it is not a reduction in resources or time consumption that drives us. It is the level of process understanding that we gain from using a model based approach compared to an empiric approach. Knowing what is going on we raise the bar for what is expected and what is unexpected. When the model describes the data well we are confident that the process is running as would be expected. This can include non-linear and counter intuitive behaviour. On the other hand when there is a systematic descrepancy between the model and the data we acknowledge that something unusual is going on and start looking for the unexpected phenomena.