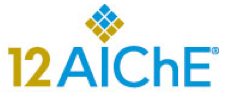
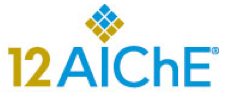
[An earlier edition of this paper was first presented at the “International Conference and Workshop – Process Safety Incidents,” 2000, organized by the Center for Chemical Process Safety (CCPS)]
The need for effective root cause analysis is finally gaining the spotlight in the chemical process industry. But, if we don't find out about an incident, we can't investigate to root causes. We do find out about accidents (harm done) because they are hard to hide. However, learning from accident is too late.
For each accident, there are about 10,000 errors and failures (sometimes called unsafe acts and unsafe conditions) and about 100 near misses. Learning from near misses is much, much cheaper than learning from accidents, yet many companies get fewer than one near miss reported for each accident. The definition of a near miss (a potentially damaging sequence of events and conditions, but without harm) can be vague and varies from site to site. This article describes the reasons why near misses are not reported and shares how companies have increased the reporting ratio to as high as 80:1. It also shares some of the gains from getting near misses reported.