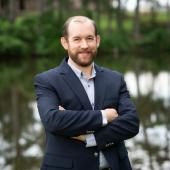
Session Chairs:
- Anastasios Skoulidas, ExxonMobil
- Patrick Heider, The Dow Chemical Company
Session Description:
Process intensification (PI) has attracted increasing attention from many in industry looking for opportunities to reduce costs while maintaining or increasing productivity. PI refers to any chemical engineering development that leads to a substantially smaller, cleaner, safer, and more energy efficient technology. These improvements are achieved by combining multiple unit operations or otherwise simplifying the overall process. Additional reductions in equipment footprint are enabled by enhancing mass and heat transfer. This session will feature talks on the practical implementation of processes incorporating PI and how challenges in scale up were overcome.
*All session and speaker information is subject to change pending finalization
Schedule:
TIME | PRESENTATION | SPEAKER |
10:10am | Efficient Benzene Production by Methane Dehydroaromatization Using Chemical Looping Hydrogen Separation | Brian Goodfellow, The Dow Chemical Company |
10:40am | Process Development and Scale-up of Mixing Sensitive Continuous Flow Reactions in Pharmaceutical Drug Substance Manufacturing | Jon McMullen, Merck & Co., Inc. |
11:10am | Process Intensification of Reactive Systems with Microfibrous Materials | Paul S. Dimick, IntraMicron, Inc. |
Abstracts:
Efficient Benzene Production by Methane Dehydroaromatization Using Chemical Looping Hydrogen Separation
Brian Goodfellow, The Dow Chemical Company
Chemical processes for non-oxidative upgrading of light alkanes are often limited by low conversions arising from thermodynamic equilibrium which are not addressed by catalyst chemistry or reactor engineering. Chemical looping technology, which involves an oxygen carrier comprising a redox-active metal oxide that is circulated through a fluidized reactor and regenerator, has the potential to overcome these limitations while simultaneously providing efficient options for hydrogen separation and energy integration. While significant research, both on process and materials, has advanced applications of chemical looping for combustion and steam reforming of methane, there have been few efforts addressing applications in the production of chemicals. As part of a RAPID project collaboration between the University of Delaware and Dow, chemical looping technology is being developed as a general process intensification strategy for the modular production of commodity chemicals. This talk will focus on the opportunities and challenges associated with integrating a modular chemical looping scheme into such a chemical process through a case study of benzene production by methane dehydroaromatization.
Process Development and Scale-up of Mixing Sensitive Continuous Flow Reactions in Pharmaceutical Drug Substance Manufacturing
Jon McMullen, Merck & Co., Inc.
The manufacturers of active pharmaceutical ingredients and their intermediates have recently rediscovered flow chemistry and continuous processing. This renewed interest in these technologies has arisen from the anticipated benefit in supply chain flexibility and economics and regulatory pressure in addition to the obvious opportunity for improved control over heat and mass transfer, improved process safety, access to high pressure and high temperature conditions, and convenient use of supported catalysts and biocatalysts.
In some parts of the community, there has been an assumption of ease and straightforward scalability for flow chemistry. However, when a flow step is embedded between two batch operations, the flow step would ideally be completed within the same amount of time as a typical batch operation, which in our experience is usually 8 - 24 hours. To achieve this requirement, productivity obtained in a laboratory scale reactor would need to be increased by several orders of magnitude, precluding the simple scale out or numbering-up approaches. In the case of reactions that require optimal mixing for selectivity and yield, the need to preserve the same mixing characteristics at production scale is essential. Achieving this goal would depend on our ability to characterize mixers and define the minimum mixing requirements to maintain the same process performance.
This presentation will discuss various strategies that have been used to scale up flow chemistry applications from the laboratory bench-top to the manufacturing environment. Techniques such as dimensional analysis and mixing characterization via a modified 4th Bourne reaction will be presented as methods to relate mixing to reaction performance. The integration of process analytical technologies with these techniques leads to streamlined analysis and further process understanding. Results from these studies have also inspired 3D-printed stainless-steel static mixer designs for custom applications. In addition, this presentation will discuss on-going efforts aimed at further understanding and modeling of mixing-sensitive reactions.
Process Intensification of Reactive Systems with Microfibrous Materials
Paul S. Dimick, IntraMicron, Inc.
Abstract Pending