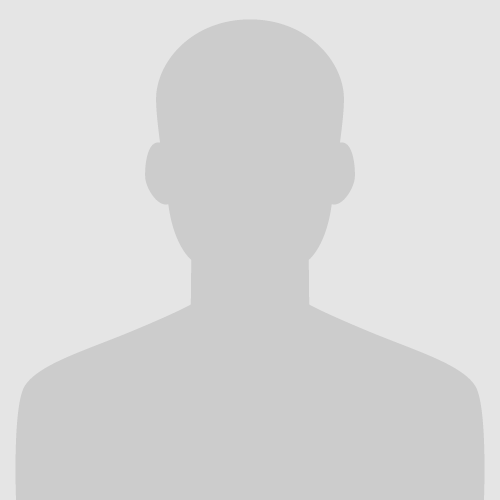
Session Chairs:
- Susanne Wolff, DuPont
- Vinod Kumar Venkatakrishnan, Shell
Session Description:
The poster reception features a mix of poster presentations from both industry and academia. As attendees mingle between posters, hors d'oeuvres and drinks will be served.
This poster session covers diverse topics related to scale-up of process technologies, designing and developing safe processes and maximizing process efficiency.
The objective of this session is to promote sharing of experiences and knowledge on specific topics as well as give participants a great opportunity to network with other process development professionals for developing the next-generation of processes.
*All session and speaker information is subject to change pending finalization
Schedule:
The Poster Session will formally take place from 5:00pm - 6:00pm, followed by open networking. Posters will be available for viewing throughout the full reception.
Abstracts:
Process Considerations to Maximize Catalyst Activity in Solution Polyolefin Polymerizations
Aaron Reed, ExxonMobil Chemical
Production of polyolefins by coordination catalysts in solution reactors is of increasing industrial importance. The development of novel, complex catalyst structures is improving the performance of existing products and expanding the market into new applications. However, as the complexity of these catalyst structures increases so too does the cost. In order to maintain reasonable manufacturing costs, greater attention must be given to maximizing the activity of these catalysts in the polymerization reactor. This paper reviews chemical processing techniques to maximize catalyst activity in solution polyolefin, polymerization reactors.
Overcoming Operational Challenges During Process Development at Intermediate Scale
Omid Ebrahimpour, DuPont
While proof of concept for new chemical processes are commonly performed through batch-based reactors at lab scale, frequently economic analysis identifies that continuous processes should be a route for commercialization of the technology. Therefore, there is commonly a need to demonstrate new technologies at small/intermediate scale prior to full scale or even pilot plant scale. Developing and designing a fully integrated process including feed systems, reactors and purification steps, is very challenging at intermediate scale due to lack of knowledge about the technology and availability of equipment at this scale. In this presentation, a number of challenges, such as handling of solids, at intermediate scale are highlighted. Also, creative strategies that have been developed successfully in the “Kingston Process Development Group” in DuPont Canada to tackle these challenges are described.
Best Practices for Managing Safety in Pilot Plants
Glenn C. Komplin and Vinod Kumar Venkatakrishnan, Shell International Exploration and Production Inc.
This poster covers a range of best practices for managing safety in pilot plants during the design, commissioning and start-up phases. Specifically, the presentation describes the hazards and effects management process that is used at Shell Oil Company including risk assessment matrix, hazard analysis and management of change as applied to a pilot plant case study.
Selecting Solvents for Chemical Products and Processes
Kevin G. Joback, Molecular Knowledge Systems, Inc.
Solvents are essential for many chemical products and processes including paints, cosmetics, adhesives, extractive distillations, crystallizations and liquid extractions. The proper selection of solvents and solvent blends is thus critical to the development of a successful product or process.
In this poster we present an overview of a computational, physical property-based methodology for selecting pure solvents and designing solvent blends. The methodology’s steps include:
1) Property Constraints: we first identify the chemical and physical property constraints that must be satisfied for a viable product or process
2) Substructure Search: chemical constraints are then mapped to molecular substructures that must be included in or excluded from candidate solvents
3) Property Estimation: the physical properties needed to evaluate constraints are extracted from databases or computationally calculated using estimation techniques
4) Screening and Ranking: candidate solvents are then screened and ranked using the constraints developed in previous steps
5) Blend Design: promising candidates are computationally combined to generate thousands of candidate mixtures that are also screened and ranked using constraints
We will demonstrate our methodology by selecting solvents for an extractive distillation process and a nail polish product.
Pilot Plant Testing for Liquid-Liquid Extraction and Distillation
Bredan Cross, Koch Modular Process Systems, LLC
Accurate design for liquid-liquid extraction (LLE) columns and distillation columns often requires pilot plant testing in order to ensure accurate sizing for production columns. Simulations are useful to determine many of the process conditions required for a given separation, but often times these are not sufficient to determine the efficiency and capacity of the column. In many instances, pilot plant testing is required to accurately determine HETP (which sets the column height) and optimal capacity (which sets the column diameter). When testing in a pilot plant, it is imperative to use the minimum size column that is possible, in order to minimize the amount of feed and time required for a test program. This presentation will show the minimum size columns that can be used to effectively generate scale-up data, and will utilize an actual example for both LLE and distillation. LLE testing can be accomplished in a 1” or 3” dimeter column, depending on the column type used. Distillation is performed in 3” – 6” diameter columns with either structured packing or sieve trays. With good experience and an effective test method, the required data can be collected within one calendar week.
Scaling Up Bioenergy Technology
Jason Doggart, Zeton Inc.
Abstract Pending
Scale-up of Select Solid-Liquid Separation Technologies
Monserrat Amezcua, Andritz Separation Technologies Inc.
The range of solid-liquid separation technologies available to choose from when trying to find the best solution can seem daunting. The proper selection and design of technology involves analyzing process integration (e.g. batch or continuous), separation mechanism (mechanical and/or thermal), required performance (solids and liquid quality), capacity, capital and installed cost, reliability, space constraints, required operating personnel, environmental restrictions, etc. The scale-up of equipment for many applications is usually based on laboratory and/or pilot testing with representative sample slurries.
This poster will cover laboratory testing and pilot testing practices used to scale-up for sedimenting centrifuges, filtering centrifuges, filter press, belt press, pressure and vacuum filters, and a selection of dryers including paddle, drum, plate, helix and fluidized bed. Laboratory testing covered consists in first determining physical properties of the slurry, then chemical conditioning requirements and finally performing a simulation of appropriate separation technology based on the results from the previous tests. In some applications, scale-up can be done using results from a simulation with bench scale equipment; in others, a test with pilot equipment is recommended.
Pilot scale catalytic fast pyrolysis of biomass: Leveraging CFD modeling to enable commissioning of an FCC riser unit
David Robichaud, NREL
The scaling of biomass thermo-catalytic conversion technologies faces a variety of interesting engineering, chemistry, and materials challenges. The biomass feedstock can be best described as Velcro coated needles, which of course provides ample challenges in the solids feeding system. Once inside the heated reactor system, one must deal with multiple solids (sand, char, biomass, catalyst), liquid (aerosols), and gas (products, reactive intermediates, co-reactants) phases, heat and mass transport of non-ideal geometries, all while balancing complex chemistries (pyrolysis vs. catalytic upgrading) and residence times. Many of the parameters and correlations needed to evaluate such system are either missing (e.g. catalytic kinetics) or inadequate for the biomass paradigm.
In this poster we will detail the design, construction, and commissioning of an FCC riser unit for biomass catalytic fast pyrolysis (CFP). This riser system is operated in an ex situ arrangement, in which the pyrolysis and char separation occur in a separate, upstream reactor so that the riser unit can focus on the catalytic upgrading (e.g. deoxygenation) of the pyrolysis vapor stream. Specifically, we will focus on the commissioning stage of this system, the challenges that arose, and how computational fluid dynamics (CFD) helped to guide the engineering solutions of those challenges. Finally, we will describe the first application of this system, which was to validate so-called ‘reactor agnostic’ catalyst kinetics for CFP.
Optimization and Intensification of Ethylene Oxide Plant Designs
G.J. (Jimmy) Wells, Shell Catalysts & Technologies
Ethylene oxide (EO) and ethylene glycol (EG) are key products in the chemicals manufacturing chain, and they are used to make a range of industrial consumer products such as polyester films and fibers, detergents, surfactants, engine coolants, and antifreeze. The most common process for making EO/EG starts with direct epoxidation of ethylene with oxygen over silver-based catalysts, and it has been practiced for over 60 years.
The plant design for making EO/EG has been enhanced significantly over time to make it much more efficient. Optimizing the design conditions of a new plant involves consideration of many complex interactions and tradeoffs between costs of energy, raw materials, and capital. A key factor that influences the design is the performance of the EO catalyst over life. Recent families of EO catalyst have dramatically improved the ability to operate at high rates with stable selectivity and activity.
This poster describes sophisticated modeling and optimization tools that have been developed and applied by a team of experts in EO catalyst technology, process design, and process operation. The tools are used to examine a wide range of potential operating conditions, assess tradeoffs, and optimize total cost of EO production. Examples will illustrate use of the tools to generate optimal, intensified designs using modern high-performance catalysts. These new design options significantly reduce costs while maintaining excellent performance stability.
Testing Capabilities of Candle Filters and the Effects on Scalability
Bradley Moakler, DrM Inc.
Proper design of a solid-liquid filter requires a thorough understanding of all the variables within that process. Lack of this understanding can result in a filter that is inaccurately sized, leading to either wasted capital or inadequate throughput, both of which are cost inefficient. The most effective way to investigate these variables is to perform field tests with a filter that can produce scalable results under a wide range of process conditions. This paper demonstrates the benefits of performing field tests using a small-scale FUNDABAC® filter that is easily scalable. A case study is presented that validates the scalability between a lab-size and commercial-size candle filter.
Rigorous Electrolyte Thermodynamics to Enhance the Accuracy of RO Membrane Models for Industrial Water Treatment
Rasika Nimkar, OLI Systems, Inc.
The Mixed Solvent electrolyte model, as developed by OLI Systems, is a recognized leader in process simulation industry for simulating electrolyte chemical systems. OLI technology specializes in the rigorous prediction of multi-phase, multi-component chemical processes. Its temperature and pressure ranges are extreme (-60°C and 4000 bar), and the breadth of chemistry covered include 80+ elements, aqueous and non-aqueous organics, and their behavior in water, vapor, organic, solid, and interfacial environments. The combination of fundamental thermodynamics, property models, numerical algorithms, and databanks enable this unique capability.
This poster will present a novel scientific approach for process engineers to use while simulating and predicting the behavior of reverse osmosis membranes under various conditions. This approach is based on first-principles models to predict membrane permeability using simultaneous electrolyte thermodynamic models, species-transport models, chemical speciation, water coordination and ion hydration (and their respective radii). The poster will consist of three sections.
This poster will illustrate the OLI Mixed Solvent Electrolyte thermodynamic model. Sample chemical systems will be potash, sulfuric acid and lithium double salts. To model the transport mechanism inside the RO membrane, a solution-diffusion approach has been incorporated. In the solution-diffusion model, it is proposed that transfer of ions and water through polymeric membranes occurs via a solution diffusion mechanism because of dissolution of permeates in the membrane materials. In the example case study, the simulation of a desalination plant located in Egypt will be considered with the goal of producing potable water with a TDS (total dissolved solids) less than 100 ppm reduced from a brackish feed water of over 10,000 ppm TDS.