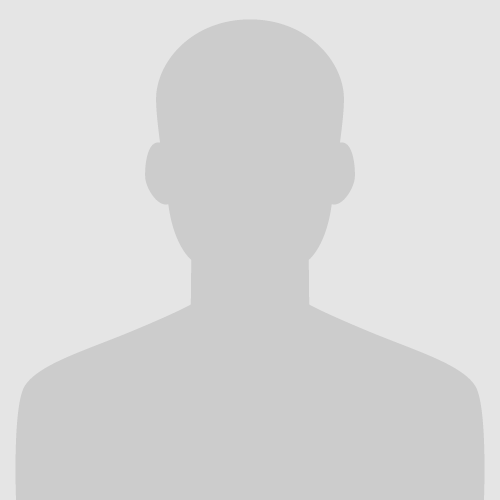
Session Chairs
- Robert Giraud, Chemours
- Tom Xu, DuPont
Session Description
Chemical separations central to processes everywhere require over 40% of the energy required in chemical manufacturing. Overall, this equates to roughly 10% of energy consumption nationally. Recent membrane technology developments allow manufacturers to achieve the same separations for a small fraction of the energy. This is especially true for separation of organic liquid mixtures where membrane separations such as organic solvent nanofiltration (OSN) are being deployed. This session will feature an overview of membrane organic separations technology followed by presentations on application of OSN and related membrane technology across a wide range of industrial segments.
*All session and speaker information is subject to change pending finalization
Schedule:
TIME | PRESENTATION | SPEAKER |
1:35pm | Membrane Organic Separations: An Overview | Ryan Lively, Georgia Tech |
2:05pm | Major Applications of OSN Membrane Technology in Pharmaceuticals and Fine Chemicals | Kumar Abhinava, Evonik |
2:35pm | Exploring Membrane Separations in Hydrocarbon Processing | Ben McCool, ExxonMobil |
Abstracts:
Membrane Organic Separations: An Overview
Ryan Lively, Georgia Tech
The rapid increase in global industrialization necessitates technology shifts in energy production, manufacturing, and carbon management techniques. Large energy costs in refineries, power plants, and manufacturing facilities using traditional separation techniques are currently a major opportunity for innovation. Approximately 10% of global energy use can be attributed to separation processes, with the vast majority of separations being “thermal” in nature (e.g., distillation). Significant energy and cost savings can be realized using advanced separation techniques such as membranes and sorbents. One of the major barriers to acceptance of these techniques remains linking engineering materials to actual processes that are effective in the presence of aggressive industrial feeds (Sholl and Lively, 2016).
We created free-standing carbon molecular sieve membranes that translate the advantages of reverse osmosis for aqueous separations to the separation of organic liquids (Lively and Sholl, 2017). High-performance membranes derived from carbon materials have shown excellent chemical resistance, high molecular selectivity and fast mass transport across the membrane. Carbon molecular sieve (CMS) membranes with tailored ultramicropore and micropore dimensions show both high processability of polymeric membrane and the high selectivity of inorganic membranes. CMS membranes have been proven to be effective in a variety of gas separation processes such as olefin/paraffin separation, natural gas separation and air separations. However, the low fluxes observed in CMS hollow fibers (due to porous substructure collapse during pyrolysis) hinder scale-up of CMS membranes for industrial separation applications. The performance of carbon molecular sieve separation membranes, which exploit the effect of mass transport across a selective diffusion barrier to separate molecules, can be improved by reducing the thickness of the membrane. We discuss methods to create hollow fiber membranes with thin CMS skin layers. We show that these membranes operate in “organic solvent reverse osmosis” (OSRO) separation modalities and purify p-xylene at room temperature without requiring any phase change (Koh et al., 2016).
References
“Seven chemical separations to change the world”, DS Sholl, RP Lively, Nature 2016, 532, 435-437.
“From water to organics: revolutionizing membrane separations”, RP Lively, DS Sholl, Nature Mater. 2017, 16, 276-279.
“Reverse osmosis molecular differentiation of organic liquids using carbon molecular sieve membranes,” DY Koh, BA McCool, HW Deckman, RP Lively, Science 2016, 353(6301), 804-807.
Major Applications of OSN Membrane Technology in Pharmaceuticals and Fine Chemicals
Kumar Abhinava, Evonik
For more than half a century, membranes have been used for molecular scale separations in aqueous solutions with applications in reverse osmosis and nanofiltration – e.g. waste water treatment, water desalination, dairy industry - but the new frontier in liquid filtrations is molecular separation in organic solvents [1]. Organic solvent nanofiltration (OSN) is an emerging technique used for product purification in a wide range of process chemical industries (e.g. Pharmaceuticals, Specialty, Chemicals, Petrochemicals, Natural Oils etc.) where molecules in the 150 to 1,500 Da range need to be separated or concentrated in presence of an organic solvent. The recent breakthrough in OSN technology with the commercialization of the DuraMem® and PuraMem® range of membranes has opened up possibilities for these OSN applications in a variety of organic solvents ranging from non-polar through polar to polar aprotic.
In majority of process chemistries, up to 90% of the capital investment involves separation processes [2]. OSN can be applied as a unit operation on its own or in combination with other unit operation(s) to achieve various separation tasks. In the Pharmaceutical industry alone, examples include purification of raw materials, concentration of temperature sensitive products, solvent swap of temperature sensitive products, product recovery from mother-liquors, color impurity removal, homogeneous catalyst removal, recovery and reuse, concentration of chromatography streams etc.
The relevance and importance of these applications will be demonstrated through several major case studies on applying OSN. Benefits such as mass efficiency via increase of product yields, reduction of process time, and reduced use of high-energy consuming technologies will be presented.
References:
[1] Vandezande, P., Gevers, L.E.M., Vankelecom, I.F.J., “Solvent resistant nanofiltration: Separating on a molecular level”, Chemical Society Reviews, 37 (2), 365-405 (2008).
[2] Cuperus P., Ebert K., “Non-aqueous application of NF”, in Nanofiltration - principles and applications, Elsevier, 521-536, 2002.
Exploring Membrane Separations in Hydrocarbon Processing
Ben McCool, ExxonMobil
ExxonMobil has been interested in the use membranes for both gas and liquid separations for at least the last 25 years. In that time we have investigated numerous applications with and worked with inorganic membranes of all types. That work resulted in over 100 granted US patents and over 30 publications in the peer reviewed literature. This presentation will provide an overview of the work from the past 25 years – including key findings in our continued progression toward understanding molecular transport and materials engineering aspects of inorganic membrane separations. Specific examples will be presented on zeolite membranes for the separations of CO2/CH4 and xylenes as well as hybrid systems for aromatics/non-aromatics pervaporation. The second half of the presentation will focus on our on-going work in the separation of complex hydrocarbon mixtures using polymeric and inorganic membranes. We will cover our efforts in novel materials development, compositional modeling for separation products in complex mixtures, and process concept development for nano-filtration and hydrocarbon reverse osmosis applications.