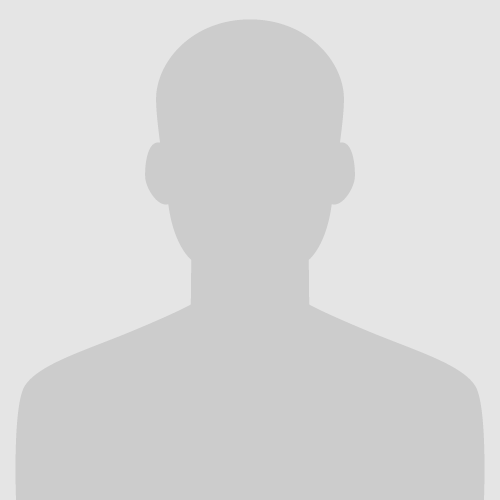
Session Chair & Co-Chair:
- Joe Kurian, W.L. Gore & Associates
- Sujata Bhatia, Harvard University
Session Description:
Consciousness of environmental issues, as well as compliance with environmental standards, are critical to a sustainable chemical enterprise. The session will cover environmentally conscious design of chemical processes; compliance with Globally Harmonized Standards; and cost savings achieved through waste reduction.
Schedule:
PRESENTATION | SPEAKER |
---|---|
Optimizing Moving Bed Biofilm Reactor (MBBR) Design for Chemical Industry Applications | Li An, Veolia Water Solutions & Technologies |
Guiding Operations Toward GHS Compliance | Andy Scherz, Epson America, Inc. |
Achieving Cost Savings Through Waste Reduction | Ross Topliff, Tops Engineering |
Optimizing Moving Bed Biofilm Reactor (MBBR) Design for Chemical Industry Applications
Li An, Veolia Water Solutions & Technologies
Moving Bed Biofilm Reactor (MBBR) is a well-known technology for biological treatment of wastewater. The technology originated through scientific work at the Universities of Lund, Sweden, and Trondheim, Norway, during the 1980s and was first brought to market by AnoxKaldnes. Since the development of this technology, AnoxKaldnes has installed over 600 MBBR systems in the municipal and industrial markets. In addition, the company has performed hundreds of laboratory, bench-scale, and pilot tests performed to evaluate specific design parameters associated with MBBR research, development, and implementation in a variety of industries.
Over the past twenty years, the MBBR technology has evolved and many lessons have been learned about the application of this technology in chemical and other industries. Among the various suppliers of MBBR systems today, there is a tendency to under-design MBBR systems for wastewater treatment needs because of the unique characteristics of the influent wastewater from chemical plants. The presentation will highlight the lessons learned based on data from case studies of the MBBR technology applied in chemical and related industries. In particular, the presentation will address the following design parameters to educate the chemical industry on this technology and provide key questions that should be asked to ensure an adequate design prior to investment for implementation.
- Media – Optimization of surface area, configuration, and material of construction of the appropriate media is important.
- Kinetic Rate is another key parameter for successful, trouble-free operation.
- Oxygen Transfer – Depending on the wastewater characteristics, different applications require variations in the amount of oxygen needed to drive the biological reaction.
- Basin and Screening Velocities - Retrofits of conventional biological treatment using MBBR technology require detailed knowledge of the existing system and how modifications must be applied for optimum MBBR operations. If the design is based on headloss rather than screen velocity, your system may be undersized.
- Mixing Air Requirements – Inadequate air supply or improper delivery can lead to operational problems and ineffective results.
- Start-up Requirements - Defoamer addition may be necessary in some applications.
- Level Monitoring – This simple step can have a big impact.
- Temperature Effects - Extreme cold conditions, hot climates, and on high temperature process streams impact the MBBR treatment efficiency.
- Monthly Average and Daily Maximums – Use of EPA’s guidelines on log normal distribution is necessary to ensure compliance with applicable permit limits.
- Fine, Coarse, and Medium Bubble Aeration – The air delivery method can make a significant difference in performance.
The lessons learned as described in this abstract are only a few examples of the experience that AnoxKaldnes has obtained since its introduction of the technology to the marketplace. Applying this knowledge is key in ensuring that a system will perform as needed while minimizing potential operation and maintenance issues. If properly applied, MBBR can be a very cost-effective option for management of wastewater from chemical operations.
Guiding Operations Toward GHS Compliance
Andy Scherz, Epson America Inc.
Chemical, environmental, bioprocessing, industrial and manufacturing companies involved in the handling, production and distribution of chemical and hazardous goods must take steps now to ensure they are in compliance with Globally Harmonized System (GHS) standards. With the standards becoming mandatory in the U.S. in June 2015 and already implemented in many other countries, there’s no time to waste. This presentation will help attendees understand the new requirements and learn how to adopt GHS compliant color labeling.
Key Takeaways:
- GHS compliance will have a major global impact on chemical processing, food/beverage processors and pharmaceutical companies
- 43 million employees in the U.S.
- 90,000 workplaces that process hazardous chemicals
- Cost for industry compliance is estimated at $201 million annually (according to the OSHA)
- The benefits for companies adopting this standard include:
- Increased employee safety and health
- Higher productivity and reduced trade barriers
- Reduced costs (pre-printed color labels, inventory management costs, shipping error/delays and waste)
- Key deadlines and new label requirements
- Key dates (Dec-2013, June-2015 and June-2016)
- Revised label elements and color requirements
- Best Practices and Questions
- Electronic label management
- Compliance checklists
- Reduce costs with color on demand label printing (pre-printed color labels, inventory managements costs, shipping error/delays and waste)
Achieving Cost Savings Through Waste Reduction
Ross Topliff, Tops Engineering
Essentially every manufacturing process produces some type of waste. While many have an ultimate goal of zero waste production or 100% reuse/recycle, that is seldom economically feasible. At the same time, waste collection, handling, and disposal can add over 5% to the total manufacturing cost. Any reduction in this cost will drop straight to the bottom line, improving the profitability of that process.
Attendees will learn how to prepare and conduct a unique type of waste audit. Rather than looking at waste after it comes out of the process, this audit utilizes material and energy balances across the entire facility and at each manufacturing step to uncover waste at its source.
Once various waste sources are uncovered, we will show you how determine which ones to go after in order to achieve the maximum return on your investment of time, personnel, and money. Using several factors, you can assign costs to each waste stream and means of reducing the waste. From there, it is relatively simple to develop an action plan that has the support of top management.
We will show the Topliff Material & Process Audit (MPA ™) in action through case studies in pharmaceutical and food manufacturing facilities.
Specifically, this presentation will review:
1) The importance of gaining upper management support for this effort,
2) How to form an effective audit team
3) How to calculate the amount of known and unknown waste generated by each process step,
4) Ways to assign a value to that waste, even when it is later combined with others prior to treatment,
5) Factors useful in prioritizing the streams to address, and
6) Considerations in developing an action plan to achieve the desired savings and profitability increase.