Superabsorbent hydrogels — capable of absorbing liquids and swelling up to several hundred times their initial mass — can be used within topical personal care products, in the cores of absorbent hygiene products such as disposable diapers, and in soils and growing media to improve water retention for agriculture applications.
Superabsorbent materials are traditionally made of synthetic copolymer hydrogels, which have limited biodegradability. Their environmental impact is substantial: For example, in the U.S. alone, around 28 billion disposable diapers are sent to landfills every year. Global environmental regulations and mandates and growing consumer interest in natural and eco-friendly products are driving strong demand for biobased and biodegradable alternatives to synthetic materials.
One biodegradable alternative to synthetic superabsorbents is based on polysaccharide chemistries (e.g., starch or cellulose). However, polysaccharide-based absorbents have a lower absorbency under load (AUL) than traditional superabsorbents. AUL, the amount of fluid that can be absorbed under a static pressure, is a key performance metric for hygiene applications.
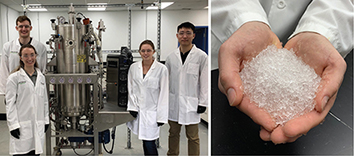
▲ Ecovia has developed a process to produce biodegradable polyamino acid products that mimic the structure and absorbency properties of conventional synthetic superabsorbent materials. They are constructing an in-house pilot plant capable of producing kg-scale batches.
Through funding from the National Science Foundation (NSF), Ecovia Renewables, Inc. (a spinout company from the Univ. of Michigan), has developed a novel, cost-effective fermentation-based bioprocess for producing biodegradable superabsorbents. The bioprocess generates crosslinked polyamino acids from low-cost raw materials such as glycerol or glucose. The process has a stoichiometric theoretical yield of 0.7–0.72 g product per g substrate, depending on feedstock selection.
Ecovia’s bioprocess involves a fermentation step that polymerizes amino acids in situ via a non-ribosomal enzymatic reaction, followed by purification to yield high-molecular-weight polyamino acids, which are subsequently crosslinked without the use of costly activating reagents. The polyamino acids have carboxylate side groups, which mimic the structure and absorbency properties of conventional synthetic materials.
The bioprocess can be tuned to tailor the polyamino acid to a specific application. Furthermore, the polyamino acid product has a higher AUL and centrifuge retention capacity (i.e., ability to retain liquid after being saturated and subjected to centrifugation) than polysaccharide superabsorbents.
Although conventional fermentation routes exist for producing polyamino acid products, they are costly. Current processes require expensive raw materials for the fermentation step, have complex purification and crosslinking processes, and generate products with unfavorable properties for superabsorbent polymer applications. Developing a lower-cost bioprocess while simultaneously increasing product performance was a key challenge for Ecovia. By leveraging innovations in fermentation, purification, and crosslinking, Ecovia has developed the bioprocess to a point sufficient for commercialization in medium-value applications. Ecovia expects to be cost-competitive with commodity synthetic superabsorbent materials after further research and development and scale-up work.
“Demonstrating Ecovia’s bioprocess platform at pilot scale this year will be an important and exciting milestone for our technology, representing a key step in de-risking and preparing for commercial production,” explains Jeremy Minty, President and CEO of Ecovia Renewables, Inc.
In 2018, the Ecovia team signed a joint-development agreement with Seppic, Inc., a subsidiary of Air Liquide, to develop ingredients for topical cosmetic and dermal pharmaceutical formulations inspired by Ecovia’s biopolymer products. “There are strong expectations from consumers for natural and sustainable cosmetic products, and biobased and biodegradable functional ingredients are key in today’s cosmetic formulas,” says Sébastien Duprat de Paule, Innovation Director for Seppic. Ecovia is progressing on the construction of an in-house pilot plant capable of kg-scale batches. Moving forward, the company is also preparing to scale up the process to produce commercial quantities of the superabsorbent polymers.
This research and technology was funded through the NSF Small Business Innovation Research Program (SBIR).
This article was prepared by the National Science Foundation in partnership with CEP.
Copyright Permissions
Would you like to reuse content from CEP Magazine? It’s easy to request permission to reuse content. Simply click here to connect instantly to licensing services, where you can choose from a list of options regarding how you would like to reuse the desired content and complete the transaction.