Many chemical engineering courses do not reflect current practices in the chemical process industries (CPI). How should the core curriculum change to better align undergraduate training with industry needs?
The nature of the chemical process industries (CPI) has changed dramatically in the past few decades. Biotechnology has become a dominant area of growth, requiring chemical engineers to understand, not only continuous, but batch and discrete manufacturing processes and control. In addition, process and product designs need to be evaluated, not only for economic feasibility, but also safety, environmental impact, and overall risk.
Despite these changes, many undergraduate chemical engineering courses have remained essentially unchanged. Examples used in coursework and textbooks still typically focus on continuous petrochemical processes that operate at steady state, while analyses of plant designs tend to focus on economics and throughput. As a result, there are gaps between what new chemical engineering graduates know and what they need to know to be successful in their careers.
Chemical engineering program administrators often cite insufficient funds, faculty time, and resources, as well as the belief that there is no room in their curricula for more content, as reasons for maintaining the status quo. In addition, professors may also find it easiest to teach how and what they were taught as undergraduates, but that may leave graduates underprepared to work in a dynamic and multidisciplinary field.
The Accreditation Board for Engineering and Technology (ABET) accredits all chemical engineering programs, verifying that each program meets the needs of its constituents, which in most cases, include industry. To improve and maintain standards, many university chemical engineering departments have appointed industry advisory boards to review programs and suggest changes. Many members of advisory boards have acknowledged the challenge in updating course content. They also note a trend for companies to send new hires to courses — either developed inhouse or by technical societies, associations, or technology vendors — to fill knowledge gaps.
Companies and organizations in the CPI are doing their part to bridge knowledge gaps by participating in university advisory boards and sending employees for additional training, but the question remains: Should universities do more?
This article looks at three chemical engineering core curricula — process design, separations, and process control — to highlight the divide between academia and industry and suggest changes that would help modernize these courses and better prepare graduates for industry. This overview is based on observations and discussions with university faculty and industry practitioners over the past decade. Our goals are similar to those that drove a 2015 study (1) of industry-academic alignment by AIChE and the National Science Foundation (NSF), which were to:
- gather opinions on the level of preparedness of undergraduate and graduate students for CPI jobs
- assess whether graduates need more workplace preparation, and in what areas
- evaluate various subject areas in terms of career importance, the present level of academic preparedness, and the need for more training
- judge the importance of recent hires possessing the skills that directly match their position requirements.
Process design
Current ABET-accredited chemical engineering programs require students to take at least one design course. That course is typically taught in the senior year, and includes a major capstone design project. It demands that students leverage knowledge gleaned from core courses completed during the first three years of the program, while they practice plant design and various analysis techniques.
In most programs, individual students or student teams are presented with either a single plant-design project or a choice of product- or plant-design options. Course lectures cover topics of relevance to product and plant design that were not covered in previous course work, such as safety and environmental regulations, scale-up considerations, simulation software, and systems engineering concepts.
Typically, students are then required to complete an economic analysis of their design, with a focus on capital and operating cost estimations, sales expectations, and expected return on investment. Students then showcase results in an oral presentation and written report.
While an economic evaluation is critical, designs proposed in industry must also be evaluated based on safety, environmental impact, controllability, ease of scaleup, and risk. More organizations are using failure modes and effects analysis (FMEA) to analyze designs and determine potential failure modes and the impacts they could have, which can necessitate plant redesign. FMEA is a simple concept that provides a lot of value, and it is an established industry technique, but it is rarely taught in undergraduate chemical engineering courses.
Some chemical engineering programs are starting to require multiobjective analyses. Chemical engineering students at Purdue Univ., for example, must carry out safety and FMEA analyses, in addition to an economic evaluation.
Senior design courses also have an opportunity to better reflect the quality and quantity of data found in industry. Students are accustomed to having all of the data needed for a project, while the reality in industry is that data are often not available, inaccurate, or have been obtained in a context (e.g., by a research lab) that is not relevant to the current project.
Students should be challenged to collect information using literature, data-estimation techniques, and extrapolation and scaleup. In addition, they should be able to assess whether the data they have are even applicable. Students may also be asked to include a list of pilot plant experiments that they would recommend to obtain information needed to complete or support their full-scale plant design.
Separations
Separations, which is sometimes taught as part of a mass-transfer course, usually focuses on distillation and extraction, because these unit operations are common throughout the CPI. However, several separation unit operations that are relevant to industry, such as filtration and chromatography, are not covered in most separations courses.
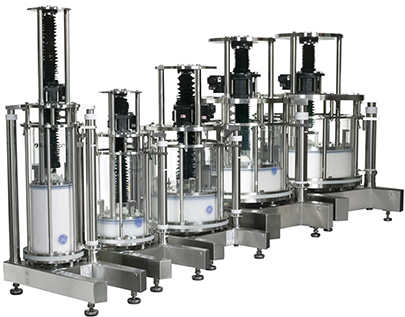
▲Figure 1. Biomolecular production is a growing sector of the chemical process industries (CPI). These chromatography columns are used to separate biomolecules, such as proteins, peptides, and oligonucleotides. Chemical engineers, however, are often not exposed to chromatography during undergraduate courses, and must learn the design and operation of this equipment on the job. Photo courtesy of GE Life Sciences.
Chromatography is used in many biological processes, such as those that begin with a fermentation step, where it is used to isolate and purify components from complex mixtures. It is also used in the production of vaccines and insulin to separate proteins (Figure 1). Because this separation must be carried out at or near ambient temperature to avoid product denaturation, distillation cannot be used. Chromatography is also used in other applications, such as in water purification, food and beverage production (e.g., fructose syrup), and petrochemical production (e.g., xylene).
Several different kinds of chromatography columns may be employed in a process to achieve the desired separations. In many bioprocessing plants, the number of chroma-to-graphy separation columns far exceeds the number of distillation columns.
Although chromatography is widely used, it may not be covered in undergraduate separations courses because the concepts involved in selecting and sizing such a column are quite different from those used in distillation. If the faculty is not suited to covering this topic, engineers or scientists from local industry could serve as guest lecturers. This would at least expose students to unit operations in industry that are not included in a program’s curriculum.
Process control
Process control is part of most undergraduate chemical engineering curricula, but course material is often based on process-control theory and practice from the development of the petrochemical industry over 50 years ago. At that time, targeted processes were continuous, linear, and operated at steady state. Courses still highlight methods specific to these kinds of processes, such as Laplace transforms, Bode plots, and stability analyses based on frequency response.
Many process-control academics and industrial practitioners agree that undergraduate process-control courses need a change, but do not necessarily agree on the details (2). Some experts believe that process control should be taught entirely from the perspective of the time domain, while others prefer to retain the frequency domain paradigm, which requires teaching Laplace transforms.
The CPI are changing and now include more biochemical processes, which are often run as batch processes and include some discrete control. Unlike the textbook examples that most students have been exposed to as undergraduates, these processes are often noncontiguous, nonlinear, and not steady state. Various forms of proportional-integral-derivative (PID) controllers are used for most batch processes, but their activation, configuration, setpoints, and tuning parameters are often time- and process-step dependent.
Practical aspects of process control are typically learned on the job, such as understanding control objectives, how a control strategy fulfills objectives, how to tune control loops, and the dynamic interactions between process variables. Many recent graduates feel shortchanged when they discover how crucial process control is to their job effectiveness, and how little they learned about it in their undergraduate education (3).
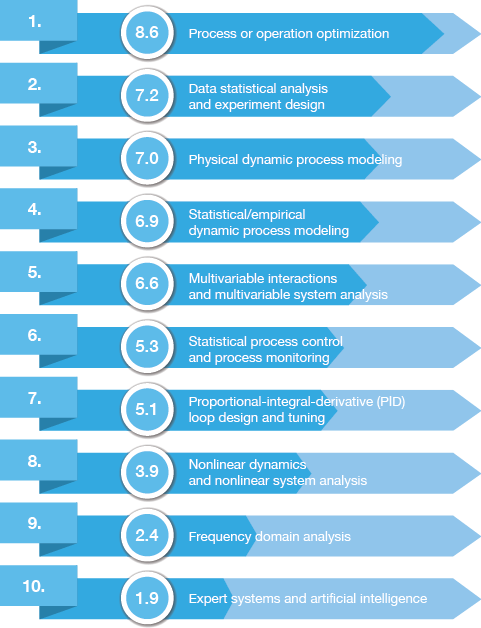
▲Figure 2. Chemical engineers working in systems and control in a variety of CPI sectors ranked ten concepts based on criticality to their jobs. This list indicates the average of the respondents’ ratings of each concept and ranks them from 1 to 10. Source: (3).
A survey of 34 systems-and-control professionals working in various industries, including biotechnology, pharmaceuticals, petroleum and petrochemicals, chemicals, consumer products, and process control, ranked the importance of ten skills and concepts to respondents’ jobs (Figure 2) (3). While process or operation optimization received the highest average ranking, it is not typically covered in process-control courses. Items 2–4 fall under process modeling and identification and received very similar ratings that indicate this topic should be emphasized more in control courses. PID controller design (#7) ranked rather low; respondents from the biotechnology and pharmaceutical industries gave this skill less importance, while engineers from mature industries and consultants rated it highly.
Students should receive hands-on experience practicing process control as it is implemented in industry. Some programs still utilize pneumatic controllers and manual data collection in laboratory exercises. However, computer controls, such as distributed control systems (DCSs) and programmable logic controllers (PLCs), are used for process control in industry, and controller performance monitoring and data collection is done electronically. MATLAB and similar software tools are not uniformly taught to students to help them understand the benefits of advanced control.
In addition to computer control systems, it is surprising that batch processing and batch process control are not a major emphasis in core courses because companies use batch processing to manufacture a broad range of products, including specialty chemicals, metals, electronic materials, ceramics, polymers, food and agricultural materials, biochemicals, pharmaceuticals, multiphase materials and blends, coatings, and composites.
Batch operation practices and control system design differ markedly from continuous operation and control (4). Students should learn about discrete logic in PLCs, which is necessary for control steps and safety interlocks that protect personnel, equipment, and the environment from unsafe conditions. Batch control requires treatment of nonlinear fundamental models because there is no steady state to use for linearization.
Batch-to-batch control is an important concept that is required, for example, when a recipe must be modified between runs, which is common in specialty chemicals and semiconductor manufacturing. In addition, batch scheduling involves optimization with continuous and integer variables.
Discrete process control is another major area of process control that students often are not exposed to during undergraduate programs. Manufacture and inspection of discrete objects, such as in making and inspecting automobile parts and filling and inspecting insulin vials, involves sensors and automated process-control logic. In high-throughput systems, thousands of components per minute may need to be accepted or rejected. The techniques used in discrete process control depart significantly from those taught in most undergraduate process control courses. Undergraduate courses should dedicate at least a few lectures to this type of control, including a case-study analysis.
One of ABET’s requirements for accreditation is that students become familiar with industry standards. However, some important U.S. and international standards are rarely, if ever, mentioned or used in academic process control courses. Students should be exposed to standards of the American National Standards Institute (ANSI) and International Society of Automation (ISA), such as ANSI/ISA-88 on batch process control, ANSI/ISA-95 on the hierarchy of control system function and architecture, and ANSI/ISA-18.2 on alarm system management for the process industries.
Many industrial process engineers would argue that there is no more important chemical engineering course than process control. This course is key to helping chemical plants achieve high yields, optimum plant performance, high-quality products, and safe operation. Yet, some chemical engineering programs provide process control as an elective, not as a required core course. Process control courses could benefit from reducing emphasis on content not often used in industry in favor of batch process control, controller tuning methods (other than Ziegler-Nichols), automation standards, automated control options, and automation systems engineering concepts.
Continuing the dialogue
Chemical engineers in industry and academia must continue this conversation to better align the core curricula in undergraduate programs with the skills that are needed now, as well as to anticipate the skills that will be needed in the future. Each program’s course offerings tend to reflect the specific interests of its chemical engineering faculty, which can make it difficult to get an accurate picture of the current state of alignment across all chemical engineering programs. Our emphasis on process control, for instance, reflects our specific research and teaching interests. We hope that subsequent articles can delve more deeply into other core courses to keep this important conversation going, and better prepare chemical engineering graduates for their careers.
Literature Cited
- Luo, Y., et al., “Chemical Engineering Academia-Industry Alignment: Expectations about New Graduates,” American Institute of Chemical Engineers (AIChE)-National Science Foundation (NSF), www.aiche.org/sites/default/files/docs/conferences/2015che_academicindustryalignmentstudy.compressed.pdf (Nov. 1, 2015).
- Edgar, T. F., “Student to Engineer: Should the Teaching of Process Control be Changed?,” InTech, pp. 30–33 (2006).
- Edgar, T. F., et al., “Renovating the Undergraduate Process Control Course,” Computers and Chemical Engineering,30 (10–12), pp. 1749–1762 (Sept. 2006).
- Seborg, D. A., et al., “Process Dynamics and Control,” 4th Ed., John Wiley & Sons, Hoboken, NJ (2016).
Copyright Permissions
Would you like to reuse content from CEP Magazine? It’s easy to request permission to reuse content. Simply click here to connect instantly to licensing services, where you can choose from a list of options regarding how you would like to reuse the desired content and complete the transaction.