Job hazard analyses require employees and employers to think critically about the dangers of a work environment and prepare operators for the unexpected.

Sweeping up dust accumulations. Replacing a light above a process vessel. Inspecting a valve. These tasks are frequently performed in chemical process industry (CPI) facilities, yet can expose workers to hazards such as flash fire, falls from height, and thermal burns from hot surfaces, among many others. A properly conducted job hazard analysis (JHA) validates the safeguards in place to protect workers from the litany of exposures they could face. In many cases, a JHA determines which personal protective equipment (PPE) is an appropriate defense against the hazards associated with a task.
U.S. Occupational Safety and Health Administration (OSHA) regulations (29 CFR Part 1910) (1) require a JHA for work environments in which PPE is deemed necessary, when work is performed in confined spaces, and for documenting lockout/tagout procedures. This requirement is a double-edged sword: its enforceability often justifies its use; however, supervisors and enforcers must be cautious that a JHA is not reduced to a mere paper-pushing exercise or conducted only when authorities request the documentation. Critics of JHAs argue that it is a waste of time and enables supervisors to micro-manage. However, by taking a more targeted approach and treating the JHA as a living document that addresses all stakeholder objectives, you can boost the effectiveness of a job or task hazard analysis.
This article reviews what is required to begin a JHA, how to properly maintain the document, and how to address its findings. Because JHA findings can include engineering and administrative controls that are beyond the scope of this article, the discussion here is limited to PPE-related findings. Notwithstanding extreme events, carefully chosen PPE is often the last layer of mitigation for an incident and perhaps the best line of defense when there is no time to react.
When is a JHA required?
Every organization should have an internal understanding and a written policy establishing when a JHA is required. Preferably, a JHA should be executed for any job that has a high injury or illness rate, has the potential to cause severe illness or injury, or is prone to human error, as well as any time that changes are made in such operations.
To avoid reducing the analysis to a box-checking exercise, the organization should be sensitive to excessive requirements. Thus, some facilities do not require JHAs for low-risk/routine tasks, while others may have internal policies that explicitly state which tasks require JHAs. A written policy might indicate JHA triggers, and might mandate an analysis for any job requiring a crane, a task involving a highly toxic chemical, a complex task requiring written instructions, or other high-hazard circumstances.
The policy must be in harmony with the facility’s operations, workflow, and staff experience level. With this in mind, it is generally effective to integrate the JHA findings and requirements into the facility’s standard operating procedures (SOP) so they can be easily referenced during operations.
Employers should already be aware of the obvious hazards — particularly hazardous substances, extreme process conditions, and high-hazard settings such as elevated temperatures and pressures. Usually, protective controls for such situations are incorporated in the process prior to operation. Such planning, however, does not replace the JHA.
The objective of the JHA is to put the hazards of the materials in the context of the process and reveal the interaction between material and process hazards and personnel performing the job. For that reason, the thoroughness of the JHA depends on how the task is broken down for the analysis. A broad analysis examining only key steps can overlook some hazards. A better approach, especially for complex and new processes, is to begin with a general outline, which can be further refined by informed experience. With careful thought and proper breakdown of the procedural steps, hidden interactions can be revealed.
Starting a JHA
To begin the JHA, a team should be assembled that includes all employees involved in conducting the job, their supervisor, and preferably a staff member responsible for facility safety. Having front-line staff involved in the JHA process demonstrates management’s commitment to safety, encourages total buy-in, and allows the most qualified and experienced individuals to provide their perspectives. The size of the team depends on the complexity of the job, but no fewer than two or three people should be involved to reduce the risk of oversights. A diverse team helps identify critical administrative controls and internal policies.
Follow these steps (as applicable) to capture the most critical components of a JHA:
Step 1. List the elements of the task. Compile a complete list of the materials, equipment, process steps, and parameters of the procedure, and then review any accident and near-miss history involving this task. When the list of materials and equipment is complete, and before continuing, reflect on whether the existing hazard controls and protections are adequate. Specific materials, procedures, or controls may need to be modified before the team delves into the JHA if this preliminary assessment shows that certain hazards cannot be mitigated.
Step 2. Break down the process. Break down the job into a series of meaningful steps that are specific enough to enable the identification of hazards. This step is comparable to defining nodes in a hazard and operability (HAZOP) study. Analyze the impact of each step on the subsequent step and brainstorm hazards that might arise when the elements come together. If a process is controlled by software, especially programs that are frequently modified, place extra emphasis on human error in Step 5.
It is important to note that in certain situations where a step may have various outcomes, such as in high-hazard research and development (R&D) facilities, the JHA should consider this uncertainty. Generally, higher levels of uncertainty require greater margins of safety.

▲Figure 1. Examining the bidirectional effects of all elements of a job can help to avoid overlooking negative interactions. Numerous accidents can be traced to a missed connection.
Step 3. Identify interactions. Thoroughly examine the effects of all elements of the task, including materials, equipment, process steps, and personnel, on one another (Figure 1). For example, assess the effects of chemicals on personnel (e.g., toxic exposure) and personnel on chemicals (e.g., spills). In doing so, it is critical to identify all exposed employees, including those who may be near but not involved in the job or with the equipment.
Contractors performing work at multiple locations should integrate the relevant site-specific conditions into their JHA.
Step 4. Identify engineering controls. Once procedures and interactions are analyzed, determine the engineering controls necessary under normal operation if the hazard cannot be eliminated. Many of these controls may already be incorporated into the JHA for existing processes.
Step 5. Identify hazards under upset conditions. Consider abnormal operating conditions — the failure modes of equipment, procedures, and protective controls, and the potential for human error.
Addressing the identified hazards
It is unlikely that all team members will identify the same hazards. An operational team member may recognize ergonomic hazards, whereas a safety engineer may highlight electrical area hazards. Consequently, solutions might conflict, and together the team must decide where to compromise.
For example, equipment location substantially impacts the hazards in a laboratory or production environment. Consider, for instance, a task requiring the use of electrical equipment near flammable liquids that could vaporize. A JHA may need to weigh the capital cost of electrical equipment classified for hazardous locations against the increased hazard of manually transporting flammable liquid containers a longer distance. A JHA also needs to consider the effect of shared space or equipment. Personnel who share equipment, tools, and work areas need to understand adjacent hazards that may affect them, even those unrelated to their own task.
Preventive measures can be general, such as limiting high-risk jobs to experienced employees, or more targeted, such as prohibiting individuals with pacemakers from performing industrial welding because of the specific health implications of that activity.
Whenever possible, engineering controls should be implemented to eliminate or minimize the hazardous conditions identified by the JHA. However, not all hazards can be engineered out. Some hazards materialize so quickly that the employee does not have time to respond effectively to prevent the hazard. Mechanical hazards usually fall into this category and comprise 88% of hazards involving equipment (2). In these situations, PPE may be the last line of defense.
Personal protective equipment

▲Figure 2. In a study of 920 PPE-related accidents, the root cause for nearly half of the incidents was failure to consider PPE (21%) or failure to use the PPE provided (23%) (3).
If analysis determines that engineering controls cannot eliminate an exposure, the first step in selecting PPE is to minimize the portions of the body requiring protection (eyes, face, toes, full body, etc.). PPE selection depends on the area of coverage and the exposure severity and type. Higher-risk exposures require more careful selection and rigorous certification. Up to 20% of PPE-related accidents are caused by failure to specify (11%), use (6%), and maintain (2%) PPE (Figure 2) (3). These failures may stem from overlooking multiple exposure hazards for the same area (e.g., using a lab coat that protects only against biological agents even though personnel may be exposed to both biological and fire hazards).
Companies should select garments certified to comply with widely accepted standards to ensure that the PPE is sufficient for the intended use. Table 1(4–11) lists standards and best practices for various hazards and their applicability. It is important to understand the limits of each garment as well as the employee’s potential exposure. Exposure routes need to consider both the source of the hazard and the target receptor. Common hazard sources include fire/heat, electrical, and chemical hazards, as well as environmental hazards such as cold air and surfaces, heat stress, and smoke. Target receptors can include skin and eyes (dermal route) and lungs (inhalation route).
Table 1. Published safety standards can help in selecting appropriate PPE (4–11). | |||
Regulation | Target Area | Hazard | Intended Audience |
NFPA 70E — Standard for Electrical Safety in the Workplace | Full Body | Electrical | All |
NFPA 1852 — Standard on Selection, Care, and Maintenance of Open-Circuit Self-Contained Breathing Apparatus (SCBA) | Inhalation | Chemical, Biological, Radiological, and/or Nuclear (CBRN) | All |
NFPA 1891 — Standard on Selection, Care, and Maintenance of Hazardous Materials Clothing and Equipment | Dermal | Physical and Health | All |
NFPA 1986 — Standard on Respiratory Protection Equipment for Tactical and Technical Operations | Inhalation | Health | First Responders |
NFPA 1992 — Standard on Liquid Splash-Protective Ensembles and Clothing for Hazardous Materials Emergencies | Dermal | Liquid Chemical | First Responders and Trained Personnel |
NFPA 2112 — Standard on Flame-Resistant Clothing for Protection of Industrial Personnel Against Short-Duration Thermal Exposures from Fire | Dermal | Fire | Industrial Personnel |
NFPA 2113 — Standard on Selection, Care, Use, and Maintenance of Flame-Resistant Garments for Protection of Industrial Personnel Against Short-Duration Thermal Exposures from Fire | Dermal | Fire | Industrial Personnel |
ISO 11612 — Protective Clothing — Clothing to Protect Against Heat and Flame — Minimum Performance Requirements | Dermal | Fire | All |
Chemical exposures. Safety data sheets (SDS) generally recommend PPE for use with a chemical under standard temperature and pressure (STP) and typically do not consider the chemical’s full potential. Therefore, the SDS should be used only as a starting point for the PPE assessment.
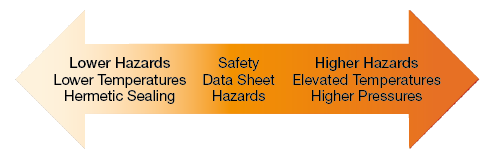
▲Figure 3. The safety data sheet presents only the baseline hazards of a chemical. The hazard of a chemical can be viewed as a spectrum; the specifics of a task will determine where it falls on that spectrum.
The hazard potential of a chemical can be viewed as a spectrum, and the process conditions determine where on that spectrum the hazard falls (Figure 3). Certain process parameters (e.g., high pressures) may elevate the hazard of the chemical while others (low temperatures) may reduce it. Certain protective measures, such as hermetic sealing of containers, can also reduce the hazard potential of a chemical.
The PPE assessment should also consider any potential byproducts. It is possible for the reaction of two relatively benign chemicals to form a particularly hazardous chemical. For instance, a dilute nitric acid solution contacting elemental copper will form nitric oxide, a highly toxic gas.
Heat exposures. Most industry-specific guidance focuses on PPE guarding against flame and heat. NFPA 2113 (10) recommends a workplace hazard analysis to determine where and when flame-resistant garments are required. Section A.5.2 of the standard lists specific materials and tasks for which flame-resistant garments are recommended. Keep in mind, however, that this list does not replace a facility-specific JHA.
Although NFPA 2113 (10) focuses on the selection of flame-resistant garments, its selection methodology and concepts are transferable to other types of PPE. Selection criteria include determining whether engineering controls designed into the process can take the place of PPE, establishing whether wearing PPE imposes ergonomic constraints, and understanding the hazards created by PPE use.
Electrical exposures. PPE requirements for electrical hazards are well-specified in NFPA 70E, Electrical Safety in the Workplace, which covers a broad spectrum of electrical activities (4). The 2018 edition of NFPA 70E has added a comprehensive list of PPE for electrical hazards and non-electrical hazards, such as fall protection, head protection, foot protection, and more. Annex H of NFPA 70E also provides guidance on selection of PPE. NFPA 70E continues to make an effort to align itself with the OSHA definitions and focus more on the analysis of risk factors and human error.
Inhalation risks. Protection against inhalation hazards can be one of the more arduous tasks of PPE selection. The National Institute of Occupational Safety and Health (NIOSH) offers an online tool, the Certified Equipment List (12), that provides information on how respirators and breathing apparatus protect against chemical, biological, radiological, and/or nuclear (CBRN) hazards. It allows users to search for NIOSH-certified equipment to meet their needs.
When identifying PPE for toxic inhalants, it is important to understand the type of toxicity, the effect of chronic versus acute exposure, and other characteristics of toxicity.
Consult an industrial hygiene professional to quantify exposure and properly fit personnel requiring respiratory protection. If PPE is required for long-term activities, consider the long-term effect of the PPE on employee comfort and health, as not all individuals are suited for long-term respirator use.
Eye risks. Eye protection is extremely critical and should almost always be worn any time other types of PPE are deemed necessary (and many times when other PPE is not required). The ANSI Z87.1 standard for safety glasses at work outlines eye protection requirements for a variety of hazards such as impact, splash, dust, and fine dust (13). When selecting eye protection, consider the comfort level of personnel as well as some employees’ need for prescription eyewear. Also account for interactions between certain chemicals and contact lenses.
Additional PPE considerations for first responders. Some of the resources in Table 1 contain PPE recommendations for first responders and personnel who deal with hazardous materials. However, fire department and hazmat emergency responders are not the only parties that need to consider these standards.
If a facility has the potential for a significant hazardous release, managers need to decide whether response to such releases will be handled internally. If so, the hazardous waste operations and emergency response (HAZWOPER) provisions of Title 29 CFR 1910 (1) require the employer to provide personnel designated to handle hazardous-material releases with appropriate PPE and training. If your facility has an internal hazardous-material response team, refer to these standards to ensure proper PPE selection.
Closing thoughts
A JHA, like other written policies, should be viewed as a living document — not simply an administrative activity to satisfy regulatory requirements. There are several creative approaches to accomplish this goal. An integrative approach in which an SOP incorporates the JHA may be one solution. Another valuable exercise is to review accidents and near-misses at the facility or similar plants and retrospectively determine what protective measures could prevent a future occurrence. Ultimately, the most effective way to conduct a JHA will depend on the work environment. In all cases, it needs to be powerful enough to instill safety awareness.
The JHA process should condition employees to think critically, brainstorm mishaps, and raise awareness of risk factors that may not be explicitly documented in other facility procedures. A JHA carried out with integrity and diligence, and treated with the appropriate level of importance by supervisors and management, will increase hazard awareness among employees and improve the safety culture of the company. Supervisors need to create a climate of safety awareness, communicate it personally, and reinforce it through appointed safety officers and human resources.
Literature Cited
- U.S. Occupational Safety and Health Administration (OSHA), “Title 29, Code of Federal Regulations (CFR), Part 1910 — Occupational Safety and Health Standards,” Washington, DC (accessed 2018).
- U.S. Dept. of Labor, Bureau of Labor Statistics, “Survey of Occupational Injuries and Illnesses (SOII) and the Census of Fatal Occupational Injuries,” Washington, DC (2016).
- U.K. Health and Safety Executive, “Evidence Base for Identifying Potential Failures in the Specification, Use, and Maintenance of PPE at Work,” Research Report 419, Bootle, U.K. (2006).
- National Fire Protection Association, “Standard for Electrical Safety in the Workplace,” NFPA 70E, NFPA, Quincy, MA (2018).
- National Fire Protection Association, “Standard on Selection, Care, and Maintenance of Open-Circuit Self-Contained Breathing Apparatus (SCBA),” NFPA 1852, NFPA, Quincy, MA (2019).
- National Fire Protection Association, “Standard on Selection, Care, and Maintenance of Hazardous Materials Clothing and Equipment,” NFPA 1891, NFPA, Quincy, MA (2006).
- National Fire Protection Association, “Standard on Respiratory Protection Equipment for Tactical and Technical Operations,” NFPA 1986, NFPA, Quincy, MA (2017).
- National Fire Protection Association, “Standard on Liquid Splash-Protective Ensembles and Clothing for Hazardous Materials Emergencies,” NFPA 1992, NFPA, Quincy, MA (2018).
- National Fire Protection Association, “Standard on Flame-Resistant Clothing for Protection of Industrial Personnel Against Short-Duration Thermal Exposures from Fire,” NFPA 2112, Quincy, MA (2018).
- National Fire Protection Association, “Standard on Selection, Care, Use, and Maintenance of Flame-Resistant Garments for Protection of Industrial Personnel Against Short-Duration Thermal Exposures from Fire,” NFPA 2113, NFPA, Quincy, MA (2015).
- International Organization for Standardization, “Protective Clothing — Clothing to Protect Against Heat and Flame — Minimum Performance Requirements,” Publication 11612, ISO, Geneva, Switzerland (2015).
- National Institute of Occupational Safety and Health (NIOSH), “Certified Equipment List,” Atlanta, GA, www.cdc.gov/niosh-cel. (2016)
- American National Standards Institute, “American National Standard for Occupational and Educational Personal Eye and Face Protection Devices,” Publication Z87.1, Washington, DC (2015).
Additional Resources
- Johnson, E. W., “10 Steps to Protect Workers against Airborne Hazards,” Chemical Engineering Progress,113 (10), pp. 78–83 (Oct. 2017).
- Ziskin, M., “Select Appropriate Chemical Protective Clothing,” Chemical Engineering Progress,109 (9), pp. 26–33 (Sept. 2013).
- Elston, H., “Determine the Right Eye Protection,” Chemical Engineering Progress,107 (9), pp. 45–48 (Sept. 2011).
- Spitzenberger, C., et. al, “Strike the Right Balance between Active and Passive Fire Protection,” Chemical Engineering Progress,112 (6), pp. 61–68 (June 2016).
- Copeland, J., “Choose the Right Chemical-Resistant Glove,” Chemical Engineering Progress,101 (1), pp. 44–46 (Jan. 2005).
- Randall, L., “Remember Hand Protection,” Chemical Engineering Progress,101 (1), pp. 41–43 (Jan. 2005).
Copyright Permissions
Would you like to reuse content from CEP Magazine? It’s easy to request permission to reuse content. Simply click here to connect instantly to licensing services, where you can choose from a list of options regarding how you would like to reuse the desired content and complete the transaction.