With a history that dates back to the 1970s, process intensification (PI) is not a new concept. Several developments have moved PI forward, but realizing PI’s full potential will require the concerted efforts of industry, academia, and government.
Process intensification aims to dramatically improve manufacturing processes through the application of novel process schemes and equipment. These novel approaches can be used to overcome bottlenecks, such as those imposed by thermodynamics, or to combine processing phenomena into fewer processing units with a concurrent reduction in capital cost and/or energy intensity. PI goes beyond the incremental improvements achieved through optimizing existing equipment and process schemes and achieves step changes in energy efficiency, capital cost reductions, and environmental impact.
PI is not a new concept and has been the topic of many review articles, including an article published in CEP in January 2000 (1). That article introduced and defined PI, provided examples of PI equipment and process design, and offered predictions about the future of the chemical process industries (CPI). Even though it has been nearly two decades since the publication of that article, PI has yet to transform the CPI, for reasons such as (1):
- capital costs and reliability, availability, and maintainability risks associated with implementing new processes
- the complexity of intensified, modular systems combined with the lack of standard equipment and techniques
- insufficient software, design tools, and data to develop intensified processes
- challenges related to the technical, economic, and intellectual property of developing standardized design and manufacturing protocols for a complex new technology space at an early point in its technical and commercial development
- limited understanding of design and operation of PI technologies across a broad range of key industry sectors.
This is not to say that PI has not found any application in commercial chemical manufacturing today (examples are discussed in this article). However, PI is still the exception instead of the rule.
Recent developments could change that, including AIChE’s formation of the Rapid Advancement in Process Intensification Deployment (RAPID) Manufacturing Institute. With $70 million in funding from the U.S. Dept. of Energy (DOE) and a slate of high-profile members, RAPID is headed down a path to address these barriers and bring PI to its rightful position in the CPI. RAPID is charged with enabling the development of breakthrough technologies to boost energy productivity and efficiency, cut operating costs, and reduce waste of manufacturing processes in industries such as oil and gas, pulp and paper, and chemical manufacturing.
This article provides a brief introduction to PI and highlights a few examples of progress in the application of process intensification. To show how PI will likely unfold over the next few years, the article discusses the RAPID Manufacturing Institute and provides an overview of the Institute’s roadmap. Finally, the article outlines challenges and potential future developments.
What is process intensification?
As with many multidimensional concepts, PI is not easily defined. Although PI may be best explained through examples, here are a few potential definitions to consider when thinking about process intensification.
Well-known experts in PI Stankiewicz and Moulijn, both at Delft Univ. of Technology, define PI as the development of innovative apparatuses and technologies that bring dramatic improvements in chemical manufacturing and processing, substantially reducing equipment volume, energy consumption, or waste formulation, and ultimately leading to cheaper, safer, sustainable technologies (1).
Stankiewicz and van Gerven add four guiding principles to that definition (2):
- maximize the effectiveness of intramolecular and intermolecular events
- provide all molecules the same process experience
- optimize driving forces at all scales and maximize the specific surface areas to which they apply
- maximize synergistic effects from partial processes.
The European Roadmap on Process Intensification describes PI as providing “radically innovative principles (paradigm shift) in process and equipment design, which can benefit (often with more than a factor of two) process and chain efficiency, capital and operating expenses, quality, wastes, process safety and more” (2).
Reay et al. describe PI as “a chemical and process design approach that leads to substantially smaller, cleaner, safer, and more energy-efficient process technology” (3).
The common thread among these definitions is a focus on new schemes and equipment that create improved processes by combining, controlling, and/or enhancing the chemistry and transport phenomena in a chemical process.
A classic example of PI equipment is the static mixer. Although there are many different designs for static mixers, the basic concept is the same: Stationary mixing elements placed in the path of fluid flow create locally highly mixed channels for the fluid to move through. Homogeneous mixing occurs quickly, with no external energy input other than that associated with the small pressure drop, at typically low capital costs. (The third article in this special section, pp. 55–62, discusses static mixers in detail.)
Static mixers can be incorporated into other unit operations (e.g., reactors) to enable the combination of processes and can be tailored to match mixing scales and times to optimize overall process efficiency. For example, static mixers can be placed in a tubular reactor for a two-phase reaction system — creating a high level of mixing while maintaining a largely plug-flow profile (typically found at a much smaller scale) at the larger reactor scale. Such an approach could offer many advantages over the alternative of operating a large continuous stirred-tank reactor to maintain high levels of mixing.
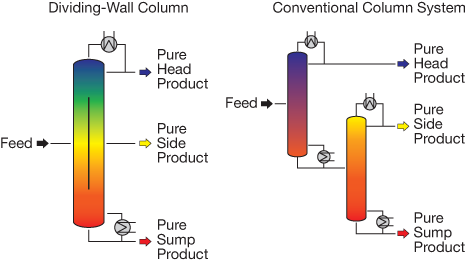
▲Figure 1. The dividing-wall column is one form of process intensification that enables the separation of a three-phase system in a single distillation tower. The internal wall splits the column into two halves. The three-phase system is pumped into one side of the column and is reflected by the wall. The lightest component flows upward and exits at the top of the column, while the heaviest component drops to the bottom and is withdrawn. The intermediate component is initially entrained in both streams; the intermediate component that flows upward subsequently separates and falls down on the opposite side of the wall, while the component that is entrained in the heavy component separates and flows up the back side of the column, where the entire intermediate stream is recovered through a side port.
There are many other examples of PI equipment, including microchannel reactors, spinning-disk reactors, centrifugal contactors, and dividing-wall columns (Figure 1) to name a few. Each of these relies on a novel driving force (e.g., rotation) or nonstandard configuration (e.g., microchannels) to enable increased control over mixing, reaction, and heat, mass, and momentum transfer to bring about step changes in the reduction of energy consumption and capital costs.
Advancements in PI
While process intensification is still a rapidly developing field that has yet to reach its full potential, many industrial applications of PI have been realized. It is beyond the scope of this article to give a complete review of past successes. Instead, here are a few illustrative examples.
Applied fields. Many early applications of PI involved the use of applied fields to enhance a process. A very early example is the centrifugal separation device patented by Podbielniak more than 70 years ago. The device, which has been applied industrially for over 60 years and is still marketed by B&P Littleford, consists of a horizontal-axis centrifuge that continuously processes liquids for accelerated counter-current solvent extraction and/or liquid-liquid separation (4). The use of rotation to augment the normal gravity-driven separation of liquid-liquid systems allows for more-compact footprints and improved performance.
Another example of applied-field-enhanced PI is ICI’s development in the early 1980s of the HiGee rotating packed-bed technology, in which a donut-shaped packing rotates to generate a centrifugal force. Liquid at the center of the bed sprays outward, and in the presence of high gravity it disintegrates into tiny droplets. The total surface area of the tiny droplets is very high, which significantly improves mass transfer. Gas-liquid HiGee technology has been commercially deployed as an improvement over conventional stripping and distillation. In these systems, the gas-liquid flow is driven by rotation (100–1,000 G) and flows horizontally, so the capacity is set by the height of the rotating bed and the efficiency is set by the bed diameter — the opposite of the relationships in traditional, gravity-driven gas-liquid contacting devices (5).
Coupled driving forces. PI has also involved coupling conventional driving forces to reduce the number of process steps required. One such application, dating back to the 1940s, is the dividing-wall column (6–8). This device separates a three-phase system in a single distillation tower that incorporates an internal wall into the vessel (Figure 1). The wall allows for thermal transfer in the radial direction but restricts mass transfer. While dividing-wall columns are not a fit for all separation challenges, in an appropriate process the capital and energy savings can be significant. Many companies, including BASF, Dow Chemical, and ExxonMobil, have reported successful operation of dividing-wall columns.
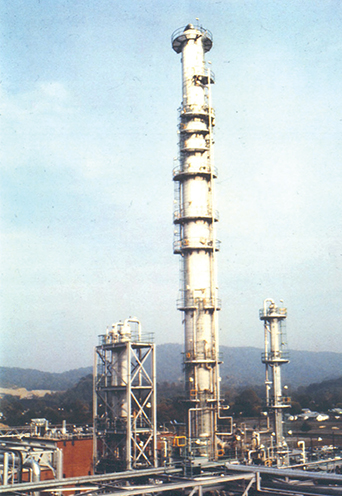
▲Figure 2. Eastman’s methyl acetate process combines multiple steps into one column by applying process intensification. The reactive distillation column is located at Eastman’s chemicals-from-coal complex in Kingsport, TN. Image courtesy of Eastman, all rights reserved.
Another example that involves coupling conventional functions in unique processing schemes is reactive distillation, which combines separation and reaction in a single unit operation with the general purpose of removing equilibrium limitations (9). The most-cited application of reactive distillation (considered by many to be the architype of PI in general) is the methyl acetate process developed by Eastman Chemical (Figure 2). In this scheme, five process functions are combined in a single vessel. Reference 10 provides details on the development, demonstration, and commercial startup of this technology. On an industrial scale, reactive distillation is currently in operation in a variety of processes, including the synthesis of acetates (ethyl, butyl, and methyl), the hydrolysis of methyl acetate, the removal of methanol from formaldehyde, and the formation of fatty acid esters.
Temperature control. Recent activity has focused on modular and micro-channel systems that employ PI concepts. There have been several commercial attempts to employ microchannel reactors — which allow much higher heat input and removal rates than conventional systems — to carry out highly endothermic (steam methane reforming) or highly exothermic (Fischer-Tropsch synthesis) reactions at a small scale (11). While applications are still limited at this point, activity has shifted from lab-scale equipment to the initial stages of commercial deployment.
New, commercial concepts for reactive separation have also emerged. Modular, reactive separation technologies may be a good fit for light-gas conversion, where widely distributed feedstocks and inherent equilibrium limitations on conversion make conventional processing less attractive. For example, CoorsTek Membrane Sciences in Norway has developed a reactive separation process to non-oxidatively convert natural gas into hydrocarbon liquids. A ceramic membrane incorporated into the reactor simultaneously removes hydrogen and injects oxygen, which enables gas-to-liquids conversion in one vessel (12).
A roadmap to PI success
Making real strides in PI will require the collaborative efforts of diverse stakeholders to address complex and crosscutting gaps. The RAPID Manufacturing Institute has worked with over 100 subject-matter experts from across its member base to develop a roadmap that identifies high-priority gaps that, if addressed, would significantly impact the success of PI in manufacturing.
Modeling tools. The lack of readily available modeling tools is a major barrier to widespread development and deployment of PI. As new technologies and design schemes are developed, engineers will need a way to evaluate and screen these ideas. Models and simulation tools similar to those available for conventional technologies are needed to evaluate PI processes, including integrated processes (such as reaction and separation) and cyclic processes (such as pressure-swing adsorption and temperature-swing adsorption). These models should be able to calculate heat and material balances for PI as well as conventional process technologies so engineers can analyze and compare hybrid process schemes. While specialized modeling tools already exist for a few PI applications, the development of tools that address a larger set of technology options and that are accessible by a broader community of users would be a major step forward.
Data needs. Along with modeling and simulation tools, data for PI systems is also lacking and will be needed for the development and evaluation of new technologies. Unlike traditional processes, for which data on the thermodynamic properties of bulk species is sufficient, intensified processes will require data describing the interactions between the chemicals of interest and other complex materials, such as novel solvents or mass-separating agents. The lack of physical property data for these complex systems is a critical gap that must be filled.
Standard PI designs. One way of applying PI to energy-intensive manufacturing sectors is to use modular sub-systems and intensified components that are preassembled then transported to and installed at a manufacturing site. Such modules would enable decentralized manufacturing and a numbering-up strategy. Although the potential benefits of modular manufacturing are well-established, several barriers have prevented wide-scale deployment. Perhaps the most significant of these has been the custom nature of modules, which makes them difficult and costly to design and install. Defining uniform design approaches and standardized pieces of equipment could enable modular manufacturing to realize the “scale-out/number-out” economics required to make this approach viable.
Novel process schemes. Integrating multiple unit operations into a single device is a classic illustration of process intensification. In particular, many see the combination of reaction and separation as a PI technology that could have a large impact. Membrane-enhanced and sorption-enhanced reactors are examples of this approach. Developing such integrated reactive separation technologies along with the requisite advanced materials (e.g., membranes that can operate at high temperatures) could transform the production of many commodity chemicals.
RAPID jumpstart projects
Several jumpstart projects that RAPID began funding in 2017 illustrate how PI can be applied to manufacturing.
Modular manufacturing. A key step in commercializing new hardware in the PI space is to establish a commercial route for manufacturing such hardware that spans the initial stages (low volumes of 10–100 units) to full commercial deployment (with orders of magnitude increases in production volumes). Oregon State Univ., Pacific Northwest National Laboratory (PNNL), and the STARS Technology Corp. are seeking to do this for a novel technology that converts natural gas into hydrogen.
The PI technology employs a mirrored parabolic dish to concentrate sunlight onto an array of meso-/micro-channel tubes for reaction and heat exchange. The concentrated sunlight heats natural gas as it flows through the catalyst-packed reactor channels and reacts with steam to produce synthesis gas (hydrogen and CO). The use of micro-/meso-sized tubes drastically improves heat and mass transfer, reduces thermal losses, and increases efficiency. STARS has set a world record of 69% conversion of solar energy to chemical energy.
The current RAPID project will define the most cost-effective manufacturing supply chain and approach for this technology for solar thermal methane reforming. This includes redesigning process equipment and materials of construction to reduce cost and to be amenable to lower-volume fabrication routes such as additive manufacturing. Although the project focuses on developing a manufacturing supply chain for a specific technology, the general approach and many of the capabilities that are being developed should be applicable more broadly to modular manufacturing in general.
Natural gas upgrading. While some embodiments of process intensification require the invention of entirely new hardware and processing approaches, others rely on more traditional technologies that are enabled by advances in controls, manufacturing, or materials. A RAPID jumpstart project by Praxair and the Georgia Institute of Technology is an example of this type of PI. This project aims to develop a modular pressure-swing adsorption (PSA) system for applications in unconventional gas production using a material that has shown great potential for the separation of nitrogen from methane.
Two types of fracturing fluids are used in North America to stimulate flow and production of shale and tight sandstone reservoirs: water with friction-reducing agents and thickening polymers, and solutions energized with compressed gases (e.g., N2, CO2). The latter approach often requires producers to divert initial gas production to a flare to reduce the concentration of N2 and CO2 gas in the flowback fluid so it can be fed into the natural gas pipeline network. In the Grande Prairie region, producers have developed very large, multistage N2 fracture operations that consume in excess of 1,000,000 m3 N2 per well. The flowback process at these wells can last 5–20 days and flare 10,000–40,000 GJ of hydrocarbon energy; in addition, about 500–2,000 m.t. of CO2 is emitted per well. Currently, no economic wellhead technology exists to reject sufficient amounts of nitrogen from produced gas to allow these wasted hydrocarbons to be captured.
Praxair recently developed a proprietary nitrogen-selective adsorbent and PSA system suitable for removing N2 and CO2 from wellhead natural gas. By rejecting the N2, hydrocarbon can be recovered from the stream that would otherwise be flared and sold to customers. Based on laboratory tests, Praxair estimates that 50–80% of the hydrocarbon can be recovered during the flowback operation, depending on its duration (50% in the case of a 5-day flowback). To quantify the benefit of this N2-separation process, consider a well that flows back the nitrogen put into the shale for 10 days; without the separation process, flowback fluid containing 14,400 GJ of saleable hydrocarbons and 840 m.t. of CO2 emissions would be flared. The team for this project is developing technology to reduce both the lost energy and CO2 emissions by 70%. To date, pilot plant testing has supported initial predictions of separation performance, and initial studies of the commercial-scale production of the adsorbent material appear promising. The project will seek field-testing opportunities in 2018 to further validate system performance.
Biorenewable products. Another RAPID jumpstart project addresses challenges related to the deconstruction of lignocellulosic biomass into fermentable sugars. The project team from Iowa State Univ. and Easy Energy Systems has proposed a thermal biomass-conversion system (as an alternative to enzyme-based conversion). So far, they have demonstrated that biomass can be converted via pyrolysis to sugars at a volumetric yield (sugars produced per unit reactor volume) that is at least 100 times greater than traditional approaches. This process could enable the use of modular equipment that could be broadly deployed for the conversion of biomass to sugars.
One key bottleneck in the pyrolytic conversion of biomass to sugars is driving sufficient heat into the reacting system. The heat required to carry out conversion in the reactor scales with the amount of reactant (i.e., the reactor volume), while the ability to get heat into a system scales with reactor surface area. This can lead to large thermal gradients in the system and/or conversion that is limited by heat transfer rather than intrinsic kinetics.
The project team has overcome these issues with an autothermal pyrolytic process that couples heat transfer and generation into the reactor itself. Specifically, air is co-fed into the reactor with the biomass. By controlling the process conditions in the system, the incoming air selectively burns biomass components to generate heat without oxidizing the desired sugar products. Since the desired product from pyrolysis is a liquid, air (rather than purified oxygen, as is needed in autothermal reforming of natural gas) can be used as the oxidizing agent without adding significant costs to the downstream separation. This use of an intensified process that combines reaction and heat transfer into a single vessel along with the approach of utilizing thermal energy to generate sugars from biomass creates the potential for a truly disruptive modular technology.
As part of the work being carried out with RAPID, the team will use the modular energy production systems (MEPS) developed by Easy Energy. In MEPS, unit operations are configured as modules sized to fit in standard shipping containers; these modules are mass-produced and integrated in the field to form fully operational biorefineries at a smaller scale and on demand. Work is already underway on the design and demonstration of a 50 m.t./day modular system that, if successful, would pave the way for commercial systems on the order of 250 m.t./day.
Path forward
The advantages of PI over conventional process optimization strategies are undeniable. While progress has been made in advancing several aspects and design schemes of PI, there is much more potential to be exploited.
In the coming months, the RAPID Manufacturing Institute will start 21 new projects that address many of the issues highlighted in this article and will also open its second call for projects. The institute is also advancing a suite of educational offerings to help researchers and practicing engineers learn process intensification and modular processing concepts that they can apply to issues occurring within the chemical and commodity manufacturing space. For more information about RAPID and how to get involved, go to www.aiche.org/rapid.
Literature Cited
- Stankiewicz, A. I., and J. A. Moulijn, “Process Intensification: Transforming Chemical Engineering,” Chemical Engineering Progress, 96 (1), pp. 22–34 (Jan. 2000).
- European Federation of Chemical Engineering, “European Roadmap on Process Intensification,” http://efce.info/efce_media/-p-531-EGOTEC-l7i4ctj2tq0utamp580m4p0qu7.pdf?rewrite_engine=id (Feb. 2015).
- Reay, D., et al., “Process Intensification: Engineering for Efficiency, Sustainability and Flexibility,” Butterworth-Heinemann, Oxford, U.K. (Aug. 2008).
- B&P Littlefield, “Liquid-Liquid Extraction Process Centrifugal Separator,” www.bplittleford.com/pod-centrifuge.html (accessed Jan. 2018).
- Kiss, A. A., “Process Intensification: Industrial Applications,” Chapter 4 in Segovia-Hernández, J., and A. Bonilla-Petriciolet, eds., “Process Intensification in Chemical Engineering,” Springer International Publishing, Cham, Switzerland, pp. 221–260 (2016).
- Schultz, M. A., et al., “Reduce Costs with Dividing-Wall Columns,” Chemical Engineering Progress,98 (5), pp. 64–71 (May 2002).
- Parkinson, G., “Dividing-Wall Columns Find Greater Appeal,” Chemical Engineering Progress,103 (5), pp. 8–11 (May 2007).
- Slade, B., et al., “Dividing Wall Column Revamp Optimizes Mixed Xylenes Production,” IChemE Symposium Series, No. 152, Institution of Chemical Engineers, Rugby, U.K. (2006).
- Harmsen, G. J., “Reactive Distillation: The Front-Runner of Industrial Process Intensification — A Full Review of Commercial Applications, Research, Scale-Up, Design and Operation,” Chemical Engineering and Processing, 46 (2007), pp. 774–780 (June 2007).
- Agreda, V. H., et al., “High-Purity Methyl Acetate via Reactive Distillation,” Chemical Engineering Progress, 86 (2), pp. 40–46 (Feb. 1990).
- LeViness, S., et al., “Velocys Fischer-Tropsch Synthesis Technology — New Advances on State-of-the-Art,” Topics in Catalysis, 57 (6–9), pp. 518–525 (Apr. 2014).
- Morejudo, S. H., et al., “Direct Conversion of Methane to Aromatics in a Catalytic Co-Ionic Membrane Reactor,” Science, 353 (6299), pp. 563–566 (Aug. 5, 2016).
Copyright Permissions
Would you like to reuse content from CEP Magazine? It’s easy to request permission to reuse content. Simply click here to connect instantly to licensing services, where you can choose from a list of options regarding how you would like to reuse the desired content and complete the transaction.