Propylene oxide (PO) is a major commodity chemical used to produce intermediate chemicals, such as propylene glycol, polyether polyols, and polyurethanes, that go into a variety of end products, including coatings, adhesives, furniture foams, and automobiles. A California-based startup has developed a new, drop-in replacement catalyst for PO production. This catalyst improves profitability and sustainability because it has higher catalyst selectivity than current catalysts and it eliminates the deactivation problems that plague catalysts on the market today.
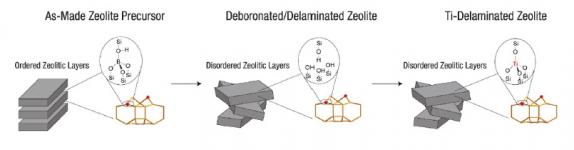
▲ Zeolites are robust, but are limited by a lack of accessibility. The BMS synthesis process unlocks the potential of zeolites as superior catalysts for epoxidation by breaking the zeolite’s solid rock-like structure into tiny sheets, thereby exposing surface sites that would otherwise be buried and inaccessible. The approach delaminates a layered zeolite precursor (left) and grafts Ti to the delaminated intermediate material (middle) to position active Ti sites in the preferred framework environments (right).
Nearly half of the world’s total PO production uses organic hydroperoxides as an oxidant. Organic hydroperoxide is chemically unstable, and its presence in the separation train is minimized to avoid undesired side reactions. Thus, PO production typically requires over 99.9% consumption of the organic hydroperoxide in the PO synthesis reactor. This high organic hydroperoxide conversion requires high temperatures in the tail-end section of the PO synthesis reactor, where the last 20% of the conversion occurs. These conditions cause a substantial loss of selectivity. In a highly competitive commodity-chemical market, even a fractional improvement in the selectivity of organic hydroperoxide toward PO represents a significant manufacturing efficiency improvement for PO producers.
Although many industrial efforts focus on increasing catalyst selectivity for PO synthesis, conventional industrial catalysts (such as those based on titanium grafted onto an amorphous-silica support) deactivate with increasing onstream time. The extent of catalyst deactivation is particularly high under the harsh conditions required in the tail end of the PO synthesis reactor. This deactivation impacts plant productivity and requires reactor shutdown and catalyst replacement on a periodic basis.
Start-up company Berkeley Materials Solutions (BMS) has developed a promising selective epoxidation catalyst that overcomes catalyst deactivation and can be a drop-in replacement for catalysts in the tail end of existing PO-synthesis reactors. This catalyst is based on novel delaminated-zeolite technology developed by a Univ. of California, Berkeley (UC-Berkeley) research group with funding from the National Science Foundation. UC-Berkeley’s Alexander Katz and his colleagues replaced the amorphous silica support of traditional catalysts with a crystalline zeolite-sheet-based support, which dramatically increases catalyst’s stability, selectivity, and activity.
The key to this patented catalyst technology is creating the right environment around each Ti site, which is enforced by the crystalline zeolite framework. A crucial advance is the delamination of layered zeolite precursors under mild conditions (pH below 10 and organic-solvent media), which preserves the crystalline zeolite structure while increasing the external surface area that is accessible and available for catalysis. This delamination technology unlocks the potential to use zeolitic catalysts for transformations involving large molecules, such as organic hydroperoxides, which previously could not access the majority of zeolite sites. The resulting crystalline catalyst has a higher selectivity and steady-state stability and a longer useful life than its amorphous counterpart.
The UC-Berkeley engineers demonstrated that the BMS catalyst has a steady-state selectivity that is 14% higher than that of a conventional catalyst in model-reaction studies consisting of 1-octene epoxidation with ethylbenzene hydroperoxide in a flow reactor under tail-end conditions. Such a performance increase could translate into a meaningful multiple-percentage-point selectivity improvement in the tail end of the PO synthesis reactor.
BMS and the Katz group are currently testing their prototype with industrial partners (PO manufacturers), and they are synthesizing new scalable prototypes. According to customers, the improved catalyst robustness and performance activity, particularly for the tail end of the propylene epoxidation reactor, address specific needs and will thus provide new opportunities for commercial implementation.
This technology was funded through the NSF Partnerships For Innovation (PFI) Program.
This article was prepared by the National Science Foundation in partnership with CEP.
Copyright Permissions
Would you like to reuse content from CEP Magazine? It’s easy to request permission to reuse content. Simply click here to connect instantly to licensing services, where you can choose from a list of options regarding how you would like to reuse the desired content and complete the transaction.