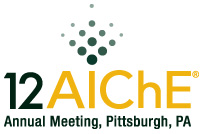
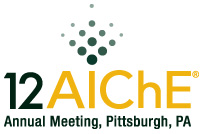
Global warming stemming from the increase in carbon footprints or greenhouse gas (GHG) emissions has become a worldwide concern in recent years. Oil production and processing, especially when involving nonconventional origins such as oil sands and oil shales are considered major contributors to atmospheric CO2 buildup. To reduce the negative impact along this line, and for the consideration of declining fossil resources, biofuels, being a source of renewable energy, are gaining increased industrial and scientific interests. In 2008, biofuels provided 1.8% of the world’s transportation fuels.1 The European Union set targets for biofuel usage of 2% in 2005 and 5.75% in 2010.2 In Canada, regulations also require an average renewable fuel content of five per cent in gasoline starting December 15, 2010.3
Biofuels refer to a wide range of fuels derived from biological sources, especially biomass. In 2010, we reported a study4 in which the oil from Canola, a cultivated variety of rapeseed, was catalytically cracked in the presence or absence of a conventional FCC feed, a heavy gas oil (HGO). In the present study, the focus was on the production of “fungible” transportation fuels from cellulosic biomass considered to be an ideal feedstock since it is abundant, relatively inexpensive, and does not compete with the global food supply. In summary, the objective of this study is to develop and demonstrate a viable economical pathway to produce renewable transportation fuels from cellulosic biomass such as wood chips, forest wastes, and agriculture residues. The ultimate goal is to mitigate the contribution of petroleum fuels to carbon footprints and global warming and to offset the declining fossil resources thereby increasing future national energy security.
2. Experimental
A biomass-derived liquid was obtained from Ensyn’s Rapid Thermal Processing (RTPTM) plant where residual wood was thermally cracked at mild temperature in a short duration (typically less than 5 seconds) with about 80 wt% liquid yield. The homogeneous liquid, for use as a fuel in boilers or in diesel and stationary turbines, is called “Renewable Fuel Oil” (RFO). RFO was blended with a conventional HGO from a US refinery in 5:95 weight ratio. Properties of the two parent feeds and their blend are given in Table 1. It is important to note that the RFO contains approximately half of the energy and carbon content of HGO, and the total energy and carbon content of a blended feedstock is therefore less than that of a pure HGO on an equivalent weight basis. This must be considered when product yields are reported and compared. The HGO (base oil) and the 5wt% RFO blend were cracked in a fluid-bed microactivity test (MAT) unit at 510°C and 10–30 h-1 WHSV, with a constant oil injection time of 30 s using the same equilibrium catalyst in the previous study.4 Details of the experiment have been reported elsewhere.5
Table 1. Feed Properties
Note – MAF: Moisture and ash free basis
3. Results and Discussion
3.1. Conversion
Conversion is defined as the portion of the feed converted to 221°C– products, including gas and coke. Figure 1 shows that conversion increased with catalyst/oil (C/O) ratio. At a given ratio, the 5wt% RFO blend gave 1–3wt% higher conversion than the base oil. The gap between the two curves diminished at high C/O ratios.
Figure 1. Relationship between Conversion and C/O Ratio
3.2. Dry Gas
Dry gas is composed of H2, H2S, CO, CO2, and C1–C2 hydrocarbons. Figure 2 shows that dry gas yield increased exponentially with conversion. At a given conversion, the two feeds gave almost identical dry gas yields. Only CO2 but not CO was detected during cracking of the two feeds with 0.02–0.08wt% CO2 yield higher for the blend at 65–75wt% conversion indicating the decomposition or combustion of the oxygenates in the blend. However, the blend produced less H2 by 0.06wt% throughout the entire conversion in this study possibly due to water formation.
Figure 2. Relationship between Dry Gas Yield and Conversion
3.3. Liquefied Petroleum Gas
Liquefied petroleum gas (LPG) consists of C3 and C4 gaseous hydrocarbons. LPG is considered a valuable product since its components can be used as alkylation and petrochemical feedstocks. Figure 3 shows that, in contrast to the dry gas yield, the blend exhibited lower LPG yield by 0.3-0.8wt% at a given conversion than the HGO feed. This was probably caused by the reduced gasoline yield (to be discussed later) of the former as catalytic cracking is a stepwise process.
Figure 3. Variation of LPG Yield with Conversion
3.4 Gasoline
Gasoline (C5–221°C boiling point) is the major and the most desirable product in FCC operation. Figure 4 demonstrates that at a given conversion, the blend lowered the gasoline yield by less than 1wt% until the conversion was higher than 70wt%. Note that the blend itself contained 1.33 (calculated from RFO analysis) to 1.90wt% (Table 1) H2O which could partially explain the drop in gasoline. Overcracking was observed for the blend at 75–80wt% conversion.
Figure 4. Relationship between Gasoline Yield and Conversion
3.5 Coke
In FCC operation, coke is necessary to supply heat for feed preheating and cracking. However, too much coke can seriously poison the catalyst and overload the air blower during catalyst regeneration, causing excessively high temperatures in the regenerator. Figure 5 shows that, similar to the dry gas, both feeds gave almost identical coke yield at a given conversion although the blend had 0.27wt% higher Conradson Carbon Residue (CCR, Table 1).
Figure 5. Relationship between Coke Yield and Conversion
3.6 Oxygen Balance
Table 2 gives the oxygen distribution in the gaseous and liquid products. It can be seen that, after cracking, most of the oxygen in the blend appeared as H2O (74.6–94.1wt%), with the rest forming CO2(0.7–5.3wt%)., The liquid products were analyzed for oxygen content and found to be below the detection limit (0.25wt%). More study is necessary to clarify the existence of oxygen compounds (oxygenates) in TLP.
Table 2. Oxygen Balance in Cracking 5wt% RFO Blend
4. Conclusions
· Catalytic cracking of the blend containing 5wt% RFO resulted in the formation of water and carbon dioxide, plus the possible retention or conversion of some oxygenates in the TLP, at the expense of gasoline and LPG production.
· At a given severity and compared with the base oil, the blend gave 1–3wt% higher conversion which increased with C/O ratio.
· At a given conversion, the blend gave lower yields of LPG and gasoline than the base oil. Other yields including those of dry gas, light cycle oil (diesel), heavy cycle oil (heavy fuel oil), and coke were almost the same for the two feeds. However, among the dry gas components, higher CO2 but lower H2 yields were observed for the blend.
· After cracking, most of the oxygen in the blend appeared as H2O with the rest in the form of CO2. The liquid products were analyzed for oxygen content and found to be below the detection limit.
· Primary indication from this study suggested a high potential of coprocessing the conventional FCC feed and RFO in an adequate ratio on account of the significant contribution of the organic ingredient in RFO to valuable products upon cracking.
· When yields of an RFO blend and HGO are compared on the basis of equivalent energy input to the MAT system, gasoline and LPG yields from the RFO blend are higher than corresponding yields from 100% HGO
Acknowledgments
The authors wish to thank the analytical laboratory of CanmetENERGY.
References.
(1) “Towards Sustainable Production and Use of Resources: Assessing Biofuels”. United Nations Environment Programme 2009-10-16.
(2) Selçuk, S., Kaygusuz, K., Sari, A., Energ. Sour. 2004, 261119-1129.
(3) The “Renewable Fuels Regulations”, published on September 1, 2010 in the “Canada Gazette, Part II”.
(4) Ng, S.H., Shi, Y., Ding, L., Chen, S., Gieleciak, R., Hager, D. “Catalytic Cracking of a Rapeseed Oil for Production of Transportation Fuels and Chemicals: Yield Structure”, Proceedings of the 2010 AIChE Annual Meeting, Salt Lake City, UT, 2010.
(5) Ng, S.H., Zhu, Y., Humphries, A., Zheng, L., Ding, F., Gentzis, T., Charland, J. P., Yui, S. “FCC Study of Canadian Oil-Sands Derived Vacuum Gas Oils. 1. Feed and Catalyst Effects on Yield Structure”, Energy Fuels 2002, 16, 1196-1208.