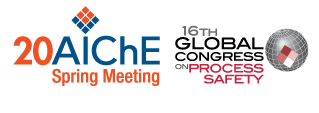
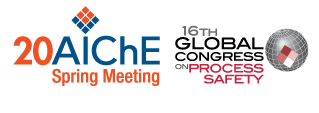
Presenter Information |
Contact Information |
|||||||||||||||
Presenter Name: Bejoy Bharatiya |
Contact Name: Bejoy Bharatiya |
|||||||||||||||
Telephone No.: +61 8 9440 0440 M: +966 553 543 149 |
||||||||||||||||
Presenter Biography: (50 words Maximum) Bejoy Bharatiya a Chartered Professional Engineer (CPEng), is Senior Process Safety Engineer at Saudi Aramco Shell Refinery (SASREF), and has over 30 yearsâ of professional experience in the upstream oil & gas, refining, petrochemical, and mineral processing industry. Prior to joining SASREF, he was the Process Safety Consultant at SANTOS (South Australian Oil Search) Pty Ltd. Australia, Senior Operations Engineer with Saudi Aramco, and the Principal Process Engineer of Brown & Root Energy Services (currently, Kellogg, Brown & Root), Australia. |
Fax No.: +61 413 098 008
|
|||||||||||||||
E-mail Address (Required): |
||||||||||||||||
Paper/Presentation Title: Flare System Assessment-A Basic Approach |
||||||||||||||||
Abstract: (1500 words Maximum): Methodology for Conducting Flare System Assessment in Petroleum Refinery Bejoy K. Bharatiya Saudi Aramco Shell Refinery The petroleum industry has long since recognized certain risks are involved in the flare and relief system of a hydrocarbon processing facility. Over the years, the oil and gas industry has learned lessons from a number of process safety events and various hazards to flare systems such as loss of control and loss of containment top events that could result in: fires, vapour cloud explosions (VCE), toxic and asphyxiant exposure, which occurred in various parts of the world and are not limited to the country of origin. The design and operation of flare system s have been the subject of concern to the oil industry. It has been the continuous effort of the industry to update the design and operating philosophies to improve the inherent safety of the flare and relief systems. The flare system is the last line of defense for various emergency scenarios. The present paper is concerned with defining the major safety considerations of international oil companies including Saudi Aramco and Shell, and International Industry Standards in designing and operating the flare systems. The flare system scope is defined in this paper as the piping and equipment downstream of the relief devices, control valves and equipment vents tied into the flare system all the way to the flare tip including knock out vessels and seal vessels. These design considerations include basic design philosophies, and safety instrumentations in relief valve back pressure limitations and sizing of the discharge piping. Major design considerations and hazard assessment for flare system to be discussed in this paper are described below. Some oil companies use required relief valve capacity for sizing the closed discharge systems, rather than rated capacity which is mentioned in API 520 Part II. The following relief load reduction credits are used for designing the flare system: 1. Flare system design philosophies - Generally, there are three permitted methods typically adopted by some of the leading oil companies for flare load mitigation: Use of 100-50-50 method; Flare IPF (Instrumented Protective Functions) method; and Flare Bundle method. a) Use of 100-50-50 methodology · The impact of the common discharge system design produced by relief flows from the connected process units as a result of global utility failure is calculated by taking 100% of the quantities established for the relief and de-pressuring load from each unit in turn, together with 50% thereof for the other units. · If it is determined that multiple trains will discharge simultaneously, the relief loads from those trains shall be taken at 100% (e.g. parallel trains that would simultaneously relieve or de-pressure during a utility failure). · The individual relief valve backpressure shall be taken as the highest value from any of the cases mentioned above. · 100-50-50 method shall not be combined with the other methods described below. This methodology considers beneficial effects of dynamics, operator intervention, control and safeguarding systems without the need to specify these. The resulting design is ALARP based on the long operational experience demonstrated by the company.
b) Flare IPF method - This considers beneficial effects of all safeguarding systems on the flare loads. Additional inputs required are: mitigated relief loads (relief loads when the safeguarding is effective) and the SIL classification of the safeguarding systems. ⢠The flare IPF method shall not be combined with the 100-50-50 methodology to analyze the same common mode scenario. ⢠The system shall meet the tolerability requirements with any single IPF failing (not working as designed). ⢠The combination of up to three concurrent individual or partial IPF failures resulting in total flare loads exceeding the acceptance criteria be designed to the appropriate SIL level to meet the acceptance criteria. ⢠It results in an enumerated probability of exceeding design requirements such as backpressure, flare radiation etc. The resulting design is ALARP based on the application of SIL classification to manage the risk. c) Flare Bundle method - This considers beneficial effects of safeguarding systems as well as basic process control and operator intervention. Required inputs are following parameters: I. common mode relief loads for all utility failures II. as I above. but mitigated relief loads (relief loads when the basic process control or operator is response is effective) III. the probability of the mitigation of effective operator response (to be established and documented in a team review) It results in a design with probability of exceeding design requirements being managed both by systems and by operator competencies. The resulting design is ALARP. This method requires a commitment to establish systems capable to maintain each of the flare load management instrumentation barriers as completely independent of each other. This method requires lifetime commitment to maintain and assure the ongoing effectiveness of the barriers. The advantage of this approach is that additional instrumentation (basic process control or IPF) barriers can be installed on a system to reclassify loads from the Likely Load, or Somewhat Likely categories, where statistically a fewer number of loads are required for the analysis. The above methods (a, b, c) rely on the hydraulic model for the flare system network based on the accurate input data (relief loads and piping data). Generally, software/applications such as Aspen Flare System Analyzer or, Honeywell UniSim Flare is used for the network analysis. There are also other software available in the market for performing the hydraulic calculations.
I. O2 Ingress into the Flare System II. Loss of Pilots / Flame III. Flare Line Entry / Live Flare Opening IV.Overpressure due to Blocked Flow V.Flare Header Liquid Hold-up / Slug Flow VI.Flare Stack Structural Failure VII.Hydrocarbon / H2S Breakthrough to Sewer / Atmosphere VIII.Backpressure Exceeding Flare System Design leading to Equipment Overpressure IX.Flow induced vibration X.Acoustic Fatigue XI.Low-temperature effects/brittle fracture XII.Radiation Etc. 4. Flare Network Analysis â In the industry, there are many software that are being used to carry out the network analysis, viz. UniSim Flare and Aspen Flare System Analyzer. Overview of our network analysis as an example will be presented to describe the effect of global power failure case (100%) and the results of high backpressure and/or high noise from certain relief valves in the process unit.
This paper discusses industry experience and summarizes the salient design considerations and risk assessment to improve safety integrity of the flare system. An effort has been made to highlight the major design approaches/ methodologies adopted by oil companies using company design standards, and industry standards like API. Emphasis has been made to increase the awareness among the process design engineers to develop safer designs of the flare systems.
|
Preview Presentation
Presenter(s)
Language
Pricing
Individuals
AIChE Member Credits | 0.5 |
AIChE Pro Members | $19.00 |
Employees of CCPS Member Companies | Free |
AIChE Graduate Student Members | Free |
AIChE Undergraduate Student Members | Free |
AIChE Explorer Members | $29.00 |
Non-Members | $29.00 |