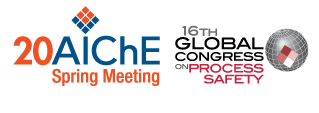
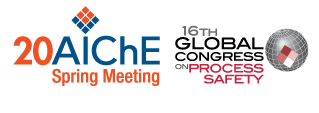
Authors: Vangaever S. 1, Djokic M.R.1, Van Thielen J.2, Olver J.3, Theis G. 4, Van Geem K.M.1,*
1 Laboratory for Chemical Technology, Ghent University, Ghent, Belgium; 2 CRESS B.V., Breskens, The Netherlands; 3 Emisshield Inc., Blacksburg, Virginia, USA; 4 John Zink International Luxembourg, Dudelange, Luxembourg.
Steam cracking furnaces are responsible for more than 75 % of the CO2 emissions of a steam cracking plant. Therefore the energy efficiency and the furnaces technology needs to be drastically changed, preferably in a cost effective way. Several novel technologies including 3D reactor designs, high emissivity coatings and oxy-fuel combustion were tested at various technology readiness levels before implementing the most promising technologies at a commercial scale in the context of the H2020 IMPROOF project.
Oxy-fuel combustion is a promising technology to reduce greenhouse gas emissions when combined with carbon capture and storage. However, a thorough life cycle analysis is necessary to account for the additional emissions required to purify the oxygen. During the IMPROOF project, oxy-fuel combustion experiments have been performed showing how a pilot plant can be retrofitted to run on pure oxygen, natural gas and a diluent for temperature control. NOX emissions were measured showing that the test facility was leak tight, which in turn allowed for further tests where an increasing amount of air was injected into the oxidant stream to check the impact of air leakage on the NOX emissions. When shifting to oxy-fuel combustion, the normalized heat flux profile does not change substantially. This indicates that conventional furnaces can also be retrofitted to run on oxy-fuel. Computational Fluid Dynamics simulations confirm the trends observed when shifting from a conventional air to oxy-fuel. Gas phase absorption-emission models have to be validated for oxy-fuel combustion since most weighted sum of gray gases models are only valid in conventional combustion atmospheres with plenty of non-absorbing nitrogen present.
High emissivity coatings applied on the refractory wall offer a way to increase the firebox efficiency. In addition to higher heat absorption and re-emission, coating the external surface of radiant coils can improve the surface homogeneity and eliminate hot spots on the tube walls. Spectral normal emissivity measurements have been performed for refractory and high temperature alloys, before and after applying a high emissivity coating. These results show that typical spectral normal emissivity values for refractory of 0.4 for the lowest and most important wavelength range can be increased up to 0.95 by applying a high emissivity coating. Several coatings have been exposed to furnace firing conditions to test their stability over time and to better understand any phase changes that occur during sintering. The most promising coating has been applied on the refractory of the UGent steam cracking pilot plant. Fuel consumption and refractory wall temperatures have been measured before and after applying a high emissivity coating.
Especially when applying a high emissivity coating on the refractory wall in combination with a non-conventional furnace atmosphere, e.g. electric furnaces and oxy-fuel combustion, the absorption-emission models are crucial in predicting the expected increase in furnace efficiency.
At present several of the latest technological innovations in the field of energy efficiency and fouling mitigation are being implemented at an industrial scale. IMPROOF will demonstrate the advantage of combining all these technological innovations, with an anticipated reduction of emissions, and increase of the time on stream and thermal efficiency.
Presenter(s)
Language
Pricing
Individuals
AIChE Member Credits | 0.5 |
AIChE Pro Members | $19.00 |
Fuels and Petrochemicals Division Members | Free |
AIChE Graduate Student Members | Free |
AIChE Undergraduate Student Members | Free |
AIChE Explorer Members | $29.00 |
Non-Members | $29.00 |