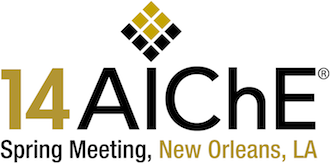
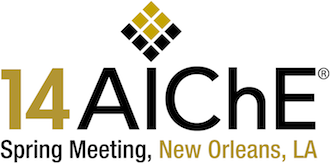
Improving Plant Safety - An Operator Centric View on Process Safety
Dr.-Ing. Gregor Fernholz, Global Business Development Manager OTS, Invensys, Germany
Dr. Ian Willetts, DYNSIM and OTS Product Director, Invensys, US
Dr. Hans-Rolf Lausch, Director CAPE & Automation, Evonik Industries AG, Germany
Abstract
Reviewing thirty years of accidents, Marsh and McLellan (1998, p.2), reported that “operator error” was the primary cause of 22% of the large property damage losses in the hydrocarbon-chemical industries. While “operator error” is one cause of loss, this statistic does not provide a solution to the problem – how can we reduce this particular cause of accidents or losses? At the same time operators are the last line of defense in preventing an accident: If all other measures fail, it’s the operator who can prevent the accident. Thus, the operator is impacting plant safety twice: As a potential cause of the error and as a means to prevent an accident.
If operators can have such an important impact on plant safety, then it is beholden on all operating companies to identify what can be done to ensure that all operators always operate the plant safely and to maximize the operator’s readiness to be able to identify critical conditions in the plant and to take the right actions to prevent an accident.
Understanding the factors governing success or failure of an operator in plant operation and in critical situations is one important consideration when designing a successful program to improve plant safety. We intuitively know that it is preferable to have highly skilled and experienced operators. However, we need to understand what skills are needed and what we can do to help operators gain that experience. This paper discusses different elements that should be included within a training program to help drive the skills and experience of operators and to enhance the safety concept.
Once these elements are understood, the paper then discusses in more detail how operator training simulators can be a critical enabling tool in the training arsenal and the testing and validation of safety relevant operational procedures. Operator training simulators provide comprehensive test and training environments for plant operators, very much like flight simulators do for commercial aircraft pilots. However, an operator training simulator doesn’t necessarily improve plant safety unless the training regimen specifically considers emergency preparedness for handling untoward operating conditions and includes the validation of procedures and their impact on the plant safety.
This paper discusses the different ways that operator training simulators can be used to accelerate the time to competence for operators and how training can target plant safety as well as how to execute standard operating procedures and how to ensure that these procedures improve plant safety.
While the first two parts of this paper are plant and company independent, the third part of this paper provides an inside view on process safety and operator training from an operating company’s perspective.
Several years ago Evonik Industries started to employ operator training simulators or “Virtual Plant Simulators” (VPS) which is the term used inside Evonik, as a tool dedicated for the start-up training of new plants. But lately the scope of application for the VPS installations is more and more extending to make better and more efficient use of the high sophisticated but cost intensive models.
In the past, operators had to build expertise for a process by experiencing numerous events. This resulted in a very accurate mental model for predicting what will happen in a certain situation and what actions will be needed to ensure safe operation. Due to the improved operation, a rising level of automation and advanced control concepts in the plants, the complexity is rising while the need for operator actions is reduced. The operators now experience events much less frequently which make it increasingly difficult to develop or maintain expertise. So the VPS is a perfect training tool for permanent upkeep and improvement of operator skills as well as the safe and advanced operation of chemical plants.
Self directed VPS sessions as well as instructor facilitated VPS sessions include all safety relevant scenarios in a plant from safe operation during a reactor start-up of oxidation process up to typical faults and malfunctions which could for instance result in undesired polymerization in distillation columns.
Recently VPS are also used more often used for root cause analyses after incidents or during PHAs to test certain scenarios as well as for the development of standard operating procedures.
The last section of the paper will provide an outlook on trends in the industry impacting plant safety and how this will affect training requirements and how recent technologies can help to address these issues.
References:
“Large Property Damage Losses in the Hydrocarbon-Chemical Industries: A Thirty-Year Review” J & H Marsh & McLennan Inc., 1998, New York