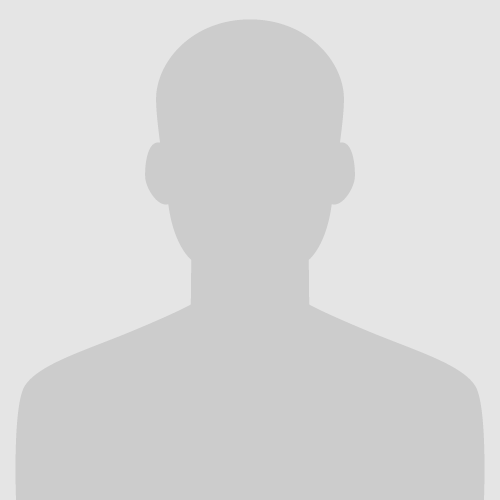
Session Co-Chairs
- Jean Tom, Bristol-Myers Squibb
- Dan Pintar, UOP LLC
Schedule
Presentation | Speaker |
---|---|
Investigation of the Impact of Mode of Operation (Batch vs Flow) on Design Space Map | Shankar Vaidyaraman |
Management for New Process Technology Implementation – Some Key Components | Michael Schaller |
Biopharmaceutical Purification Process Development: Identifying Risks and Dealing with Uncertainty | Steven Weisser |
Investigation of the Impact of Mode of Operation (Batch vs Flow) on Design Space Map
Shankar Vaidyaraman, Eli Lilly and Company
This talk will discuss how the mode of operation (batch vs flow) impacts the design space map for impurities thus impacting the robustness of the process. A specific case study involving a reaction model will be used for this investigation that builds upon previous work on failure mode analysis in continuous processes (Wong etal 2011). There are three impurities of interest formed in this reaction. A reaction kinetic model developed from batch experiments is used to design for both batch and flow processes. The key questions that this investigation addresses are:
- How much does the mode of operation impact the size of the design space?
- Is the link between the uncertainties due to routine variability and model uncertainty and the output impurity levels same or different depending on the mode of operations?
- Can certain generalizations be drawn based on the results of this case study?
Management for New Process Technology Implementation – Some Key Components
Michael Schaller, The Dow Chemical Co
As The Dow Chemical Company continues to increase our emphasis on innovation to meet customer needs, more and more of our capital projects incorporate new process technology, new product technology, or both. Although all capital projects include some degree of risk, we’ve determined that projects involving new process technology face more significant risks. For example, building a new polyethylene manufacturing facility using previously-demonstrated technology may face risks related to material and labor costs, scheduling and/or Environmental, Health and Safety (EH&S) issues. But building a facility to make a new pesticide, the process for which has not been fully demonstrated at the lab scale, and doing it in time to meet the seasonally-driven launch date, poses the same potential cost, schedule and EH&S risks, but also includes operability risks, risks associated with the overlap of process development and process design, a compressed project schedule, limited understanding of the relationship between process variables and product performance, etc.
Because our capital project work processes, and, to some extent, our culture, were developed around building commodity chemical manufacturing facilities, we treat projects involving new process technology (NPT) differently than we do those implementing demonstrated technology. One area that we focus on is risk assessment and risk management. Some of the key aspects of dealing effectively with new process technology implementation that we will share are the following:
- Incorporate inherently low-risk approaches
- Fill and support the Risk Manager role
- Develop and implement a formal Risk Management Plan
- Develop and maintain a detailed plan for Technology Development
- Practice quantitative risk assessment
- Prepare for problems
Biopharmaceutical Purification Process Development: Identifying Risks and Dealing with Uncertainty
Steven Weisser, GlaxoSmithKline
Process and product knowledge is gained throughout the lifecycle of a biopharmaceutical product. Process development teams need to use purification strategies that allow them to respond to new information and accommodate uncertainty. Development of biopharmaceutical purification processes will be discussed with an emphasis on how project teams deal with uncertainty.
Strategies focusing on identification of risks and knowledge gaps, and designing and implementing mitigation plans to deal with them will be discussed. Application of these approaches to problems such as dealing with feed stream variability, risks to key raw materials, and issues observed after scale-up will be presented.