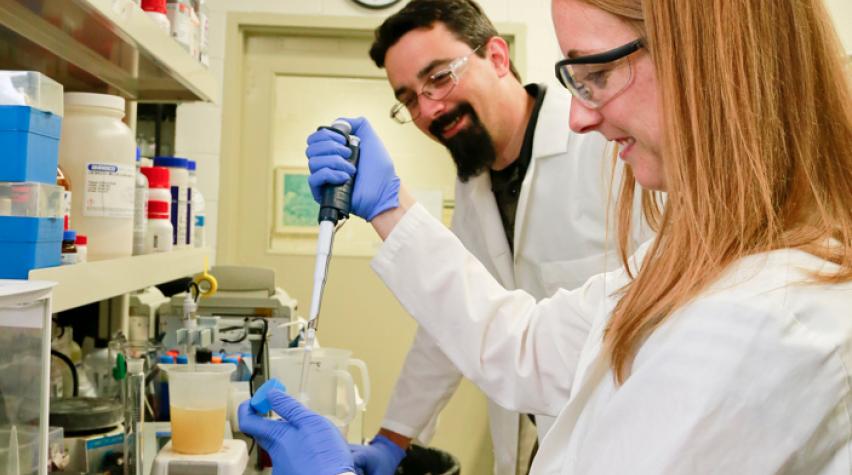
Another technological barrier to gas-tank-ready biofuels has fallen. And not a moment too soon.
That's because the lowest oil prices in six years have pretty much derailed (in the short term) any rationale for blending corn ethanol. As the price of crude oil fell 57 percent in the past year to $40.80 a barrel — gasoline plunged 42 percent — the ethanol additive, originally introduced to stretch limited gasoline resources, became unnecessary and much less attractive.
Regulatory support has also softened. In May, the EPA proposed reducing the amount of ethanol required to be mixed with gasoline from statutory levels set in 2007, citing reduced driving and improving fuel efficiency since then.
A long-term goner
Ethanol might eventually be a goner — for many reasons — and isobutanol, a newcomer with a more a gas-friendly chemistry, could take its place if it gets the right breaks. Fortunately researchers at the Department of Energy’s BioEnergy Science Center (BESC) just reported in the journal Metabolic Engineering that they've tweaked a new microbe to improve isobutanol yields directly from cellulose by a factor of 10 over an earlier version.
While BESC's early work represented a significant gain, “Four years ago, we were using Clostridium celluloyticium, a much less complex organism,” said James Liao of UCLA’s Henry Samueli School of Engineering and Applied Science. “Now we've engineered similar traits in the much higher yielding Clostridium thermocellum, and that's taken us to new levels of consolidated bioprocessing efficiency.”
Ethanol, nobody's idea of the perfect fuel
Ethanol was never anyone's idea of a perfect fuel, and isobutanol improves on most of it flaws. First of all, no one liked ethanol's high volatility. The nation’s gasoline supply changed with the introduction of ethanol oxygenate. Inexpensive light ends were removed to produce the costlier Reformulated Blendstock for Oxygenate Blending (RBOB), to compensate for ethanol’s high volatility. Isobutanol, on the other hand, has very low volatility, allowing blending without the need for RBOB, freeing the refiner to get higher margins for heavier cuts.
In addition, isobutanol's four carbon molecule has nearly 20 percent more energy punch than puny, two carbon ethanol. In fact, it's close enough to gasoline that it can be used at any blend ratio, even at 100 percent. According to Biofuels Digest, physicist David Ramey drove from Ohio to San Diego, California, using 100 percent butanol in an unmodified 1992 Buick Park Avenue without incident and achieved a 14 percent increase in fuel mileage compared to 87 octane gasoline.
Ethanol is also extremely corrosive. So for that reason, it can't be pipelined and must be transported by truck or rail instead. Butanol’s much lower affinity for water make pipe-to-refinery blending viable. Further, isobutanol has already been approved for blending into marine gasoline, where ethanol is banned.
But beyond being a direct replacement for gasoline, isobutanol is also a chemical feedstock for many products. One important example: isobutanol can be upgraded into jet fuel.
Gevo and Butamax
Currently, two US companies are leading the push for traditional biobutanol, Gevo of Englewood, Colo., and Butamax Advanced Biofuels, a joint venture of BP and DuPont based in Wilmington, Delaware. Both make butanol the same way ethanol is made, through yeast-based fermentation followed by distillation. Gevo licensed James Liao's much earlier research, which uses yeast cells with tweaked metabolic pathways to divert isobutanol production from amino acids.
Gevo and Butamax don't want to compete with ethanol-producers. Rather, they're trying to convince them to license their bolt-on systems to convert some ethanol production to isobutanol and add more revenue streams. While these upgrades haven't won many converts, Gevo says that a US gas station is selling gasoline blended with its isobutanol for the first time.
Express Lube of Fredericksburg, Texas, is the "first of many retail locations to offer Gevo's product as the company rolls out its isobutanol to the marina, outdoor equipment, and off-road gasoline markets."
Low-cost breakthrough
BESC's new consolidated bioprocessing bundles several separate processes into a single microbe to extract sugar from a plant’s cellulose and convert it into a biofuel. This approach combines several steps — pretreatment, enzyme treatment and fermentation — to produce biofuel at a lower cost. The process also helps overcome recalcitrance, or a plant’s natural defenses to being chemically dismantled. Recalcitrance has been one of the barriers to using lignocellulosic biomass such as corn stover and switchgrass as a feedstock for biofuels.
While Liao's first genetically engineered mulit-process microbe achieved conversion results of 0.6 gram of isobutanol per liter, Clostridium thermocellum has produced 5 to 6 grams per liter. Researchers accomplished this by inserting five genes into one microbe, enabling it to internally synthesize isobutanol. Scientists consider this as a clear next-generation advance over strategies that use yeast, such as those used by GEVO and Butamax, to create biofuels from cellulose.
“In addition to this development, which moves the BESC team closer to the production goal of more than 20 grams per liter, the prospects of commercial realization of this approach are greatly enabled by the fact that the microbe works at temperatures high enough to keep competing bugs from contaminating the microbial fermentation tanks and interfering with the conversion process,” said Paul Gilna, director of BESC.
How quickly can this be mainstreamed?
Image: researchers, BESC