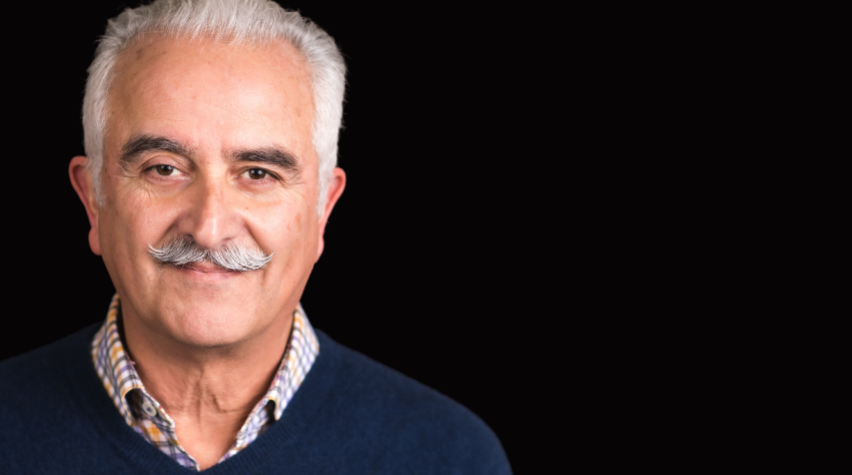
Welcome to the latest in a series of AIChE blog posts profiling process engineers, a diverse group of professionals spanning multiple industries and regions. In this series, we profile process engineers who work in a wide range of fields, including petrochemicals, pharma, bulk chemicals, food, or any process-intensive industry.
Are you a member and process engineer interested in being profiled? We’d love to hear from you via this volunteer opportunity. Please also check out our online discussion group specifically for process engineers. You can find out about these initiatives and join our efforts by visiting https://www.aiche.org/processengineering.
This month, we introduce you to Ken Ravon, the CEO and President of Solutions Recovery International. He discusses the path that led to his career in process engineering, overcoming challenges, and the importance of his work.
Tell us a bit about your work as a process engineer
I am a seasoned senior executive with a record of 40 years of building market share and achieving revenue, profit, and business objectives within startups and multi-million dollar companies worldwide.
I consider myself a strong sustainable strategist and tactical executor with superb leadership skills in the energy, environmental, and engineering/construction industries.
I am also highly successful in building relationships with decision-makers through knowledge of international and multi-cultural environments.
I manage P&L from $10M to $200M revenue. My specialties include process design, corporate sustainability, financial modeling, marketing, business development, business evaluation, and reporting.
Why did you become a process engineer?
After receiving my mechanical engineering degree, I immediately started working in a manufacturing company building industrial wastewater treatment systems. With my strong background in chemistry, I learned the different treatment processes from various sources of wastewater. Later on, I went into the municipal market and designed sequential batch reactor (SBR) systems, which we installed at more than 30 plants in Taiwan alone. I enjoyed the process design for all of these treatment processes. Nowadays, I design other processes for top Fortune 500 companies.
Process design is at the heart of every project. Other disciplines are built upon the process design.
What are some of the biggest challenges you face in your role as a process engineer?
Every project has its own challenges, but four common challenges come to mind. One is quality assurance. Most FABs require high-purity chemicals with very tight specifications. Balancing between the design, safety, and budget presents a unique challenge. For instance, for a process design for high-purity chemical distribution systems, we need chemical bulk storage tanks, pump stations, branching boxes, isolation valves, and on-demand solenoid valve systems. Semiconductor facilities require the same quality of chemicals produced by the chemical manufacturers at their point of use. This requires a careful selection of materials, which normally need PFA tubing, pumps, and valve systems.
On the other hand, a good process design includes process safety from double-containing tanks, pump stations, branching boxes, and valve systems. Once a component is double-contained, leak detection is required to notify the operator of any possible leaks. Then the process design would also require alarm systems not only for high and low levels, pressure, etc., but also to cover areas such as unauthorized access to the program, pump stations, and branching boxes to prevent any sabotage. All of these tend to increase the overall cost of the project.
The second challenge is the permitting process itself. Obtaining a permit for a chemical bulk storage and distribution system depends on the workload of the city’s building department that has jurisdiction over the project. Normally in Silicon Valley, the permitting process takes six to eight weeks. Therefore, a process engineer needs to describe all code-related concerns on the drawing package to assure the city that the design meets all codes. Getting this right upfront shortens the approval process.
That raises a third challenge: keeping projects on a strict schedule. Corporations have annual budgets, requiring a project to be completed and invoiced in a fiscal year calendar. Therefore, a good process engineer must manage the design phase efficiently and even order long-lead items ahead of time to ensure that the fabrication can start immediately and upon obtaining the permit, and that the construction can also start.
And the fourth challenge that comes to mind is the payback period. Bulk storage chemical and distribution systems normally pay for themselves in 1.5 years (Analog Devices, October 2018). However, some clients require a payback period of less than one year. With high-cost materials, components, and safety needed for a good process design, this presents a challenge. A good process engineer needs to convince the corporate management that a 1.5 year payback period is a good ROI while protecting the product quality, yields, environment, and workers.
How is your work as a process engineer critical to your particular job assignment or industry?
I am the CEO/President of my company, and besides the project management, I also do the process and mechanical design of every project. Process design is at the heart of every project. Other disciplines are built upon the process design. I start with the process flow diagram (PFD) to identify the unit process. Then, I develop the process and instrumentation diagram (P&ID), where I size every unit process.
Based on the P&ID, I create the layout drawing to ensure the process design will fit into the space specified by the client. Space is limited most of the time, and we have to change the PFD and P&ID to meet the space allotment. We conduct failure method and effects analysis (FMEA) for every project to avoid downtime.
Upon finalizing the PFD, P&ID, and layout, instrumentation and control ensures the process parameters are followed. We use a programmable logic controller (PLC) to program every step of the process with a human/machine interface (HMI) to allow the operator to change setpoints based on the site conditions.
What do you think is most important about what you do as a process engineer?
Of course, safety is the most important aspect of a process design. Equally, FMEA is also important, as a one-hour shutdown could cost the company $1MM. Part of FMEA is selecting the right components or doubling them to avoid process shutdown. Also, don’t forget about the budget and schedule. As you can see, all of these factors play important parts in a successful design.
Connect with Ken on AIChE Engage
Join the Community of Process Engineers
Process Engineer Perspective Talks (PEP Talks)
AIChE is launching a new series of virtual presentations called Process Engineer Perspective (PEP) Talks, which will feature perspectives of process engineers on topics relevant to other process engineers. Join us every second Thursday of the month to get to know your fellow process engineers. Attendance is free.
The Community of Process Engineers is brought to you by Scott & Karen Love. Their support enables the AIChE Foundation to advance process engineers at every stage of their career allowing them to Do a World of Good.
AIChE Foundation – Doing a World of Good Campaign