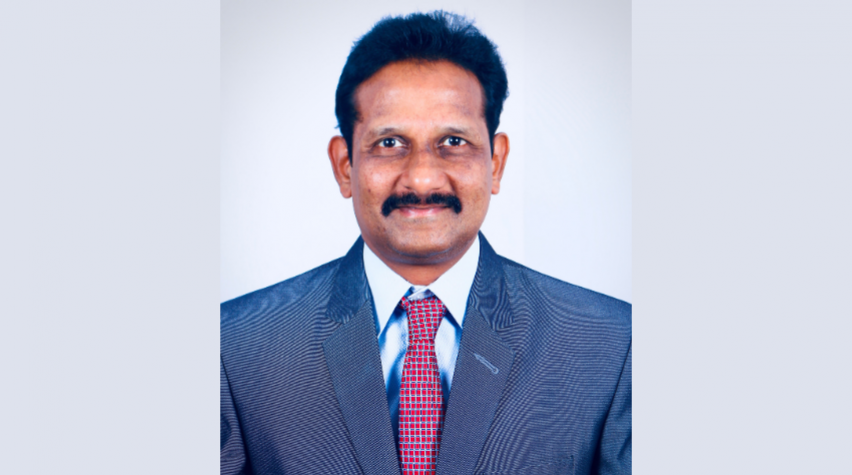
Welcome to the latest in a series of AIChE blog posts profiling process engineers, a diverse group of professionals spanning multiple industries and regions. In this series, we profile process engineers who work in diverse fields, including petrochemicals, pharma, bulk chemicals, food, or any process-intensive industry.
Are you a member and process engineer interested in being profiled? We’d love to hear from you via this volunteer opportunity. Please also check out our online discussion group specifically for process engineers. You can find out about these initiatives and join our efforts by visiting https://www.aiche.org/processengineering.
This month, we introduce you to Kotti Rama Raghava Kumar, who previously worked as Head Plant Operations at IG Petrochemicals Limited (IGPL) in Navi Mumbai, India. He discusses his accomplishments as a process engineer, overcoming challenges and the importance of his work.
Tell us a bit about your work as a process engineer.
I have 30 years of experience in the chemical process industries and I worked as head plant operations at IG Petrochemicals Ltd. (IGPL) for over two years. IGPL has continuous process plants and also batch plants. The main product of IGPL is phthalic anhydride (PA) along with the by-products maleic anhydride (MA) and benzoic acid (BA). They have a total of seven plants (three PA units, three MA units, and one BA plant) with all associated off-sites and utilities.
Before working for IGPL, I worked with Nagarjuna Fertilizers and Chemicals Ltd. (NFCL) for 28 years and worked with production, projects, and also with technical services. Before leaving NFCL, I was general manager of projects and headed projects at the NFCL complex. I have also worked as head of department (Process Plant-1) for Ammonia-1 and Urea-1 plants.
Prior to that, I was section head for urea production and later on for an ammonia plant. I installed and commissioned an S-300 ammonia converter in parallel to an existing ammonia converter. I have experience with full cycle implementation of multiple urea plants, revamping of ammonia and urea plants, and I've written and published over a dozen papers on ammonia, urea, carbon dioxide recovery, and phthalic anhydride plants. I am also a senior member of AIChE.
Why did you become a process engineer?
While performing duties, a process engineer is accountable for protecting nature by conserving resources and reducing emissions. Being socially responsible, process engineers should protect the safety of both people and equipment.
I joined chemical engineering based on my merit in the entrance exam, thanks to my chemical engineering professors at Andhra University who were very knowledgeable and interested in what they taught. Later on, I developed an interest in chemical engineering due to university culture, ambience, batch mates, my brothers, and maternal uncles who are all engineers.
One of my chemical engineer uncles is the reason behind my motivation. The Andhra University Department of Chemical Engineering was started in 1933 and is one of the most reputed chemical engineering and technology institutions in India.
Here, Kotti Rama Raghava Kumar is pictured with colleagues at a discussion on process risks and hazards.
What were some of the biggest challenges you faced in your role as a process engineer?
One of the biggest challenges I faced in my role was attempting to increase the capacities of ammonia and urea process plants by around 25%. Initially process plants bottlenecks were studied carefully and only necessary equipment was replaced or additionally provided.
This was a challenging task as it required strong process experience as well as having to convince people to overcome their resistance. The large fertilizer complex (two ammonia plants, two urea plant units and off-sites) was revamped without consultation. Simultaneously, the 450 MTPD carbon dioxide recovery (CDR) plant was also set up. The project was driven with a minimum cost of around 30 MM USD within a scheduled period of 24 months with internal expertise.
During that time, one ammonia plant feedstock was changed from mixed fuel (naphtha and natural gas) to natural gas alone. By the time natural gas was made available from the supplier, the carbon dioxide plant was ready and a mini-revamping of all process plants was completed. The project was completed in less time than the targeted schedule of 24 months. Finally, the task of increasing complex urea production by around 200,000 MT of urea per annum was achieved successfully.
The director and the chief operating officer gave me a letter of appreciation as well as a cash bonus for this accomplishment. Needless to say, this was an example of what teamwork can accomplish at NFCL from top to bottom, including contractors.
Subsequently, after the revamp, there was one more challenge. While enhancing capacities of ammonia and urea plants, the Urea Plant I LP condenser was replaced with a bigger one, and the removed condenser of Urea Plant I was installed parallel to the LP condenser in Urea Plant II.
Each of the condensers was only coming in one operation at a time. This aspect resulted in higher LP loop pressures with the vent valve in a fully open condition, which became a bottleneck for the plant operation. Finally, the problem was solved successfully after thorough study and coordinating with the technology supplier.
How is your work as a process engineer critical to your particular job assignment or industry?
While performing duties, a process engineer is accountable for protecting nature by conserving resources and reducing emissions. Being socially responsible, process engineers should protect the safety of both people and equipment.
I've listed a few job related critical assignments below:
- At Indo German Petrochemicals Ltd (IGPL) controlling effluents (gaseous from heaters/furnaces, boilers and liquid effluents from process plants mainly), maintaining product quality without compromising on day-to-day production targets.
- Controlling all kinds of incidents (process, reliability, safety, etc.) by addressing the recommendations of root cause investigations.
- Energy-related aspects like control of fuel consumptions per annum were also critical.
What do you think was most important about what you did as a process engineer?
One of many important tasks was identifying the limitations for plant operations of any kind and addressing them. I've dealt with and solved problems for all disciplines in other engineering departments like mechanical, technical services, electrical, civil, and instrumentation. Problems may be related to production, maintenance, energy consumption/reduction, safety of the people, process and equipment, strict effluents control, and safe shutdown/startup of plants.
Few process industries have a combination of continuous as well as batch processes. In such a case, batch time optimization and achieving production targets played an important role. In the case of old plants, probing into life cycle assessment and initiating actions to improve the equipment’s life or planning for replacement was also very important. While implementing management of change (MOC), inspecting all the stages of MOC for missing elements or process safety aspects, and ensuring that a proper HAZOP study is conducted is paramount. It's vital to investigate the root cause for all process related incidents and ensure that recommendations are implemented.
As a process engineer, I've also conducted feasibility studies for grassroots projects, revamped projects, and selected the best technologies after thorough comparison. It's imperative to arrive at the best payback option by leveraging various technologies, project methodologies, scope and utilizing internal manpower. It's important to demarcate the scope between the agencies involved (like technology suppliers, and owners for instance) to arrive at the optimum project cost.
The role of a process engineer is very important when it comes to reviewing and finalizing basic engineering, detailed engineering packages, as well as commissioning and completing a guarantee test run.
Lastly, I have also implemented the following significant projects:
- Two large-capacity (1500 MT per day) urea plant units with 500,000 MT per annum capacity each
- Increased production capacity of two units of ammonia and urea plants, each by around 25%
- Installed new 450 MT per day carbon dioxide recovery plant two months ahead of schedule
- Commissioning and GTR of NFL-Nangal urea plants each by around 30%
- New ammonia converter installation, catalyst loading, commissioning and operation of S-300 with a daily capacity of 1350 MT.
Connect with Kotti Rama Raghava Kumar on AIChE Engage
Join the Community of Process Engineers
The Community of Process Engineers is brought to you by Scott & Karen Love. Their support enables the AIChE Foundation to advance process engineers at every stage of their career allowing them to Do a World of Good.
AIChE Foundation – Doing a World of Good Campaign