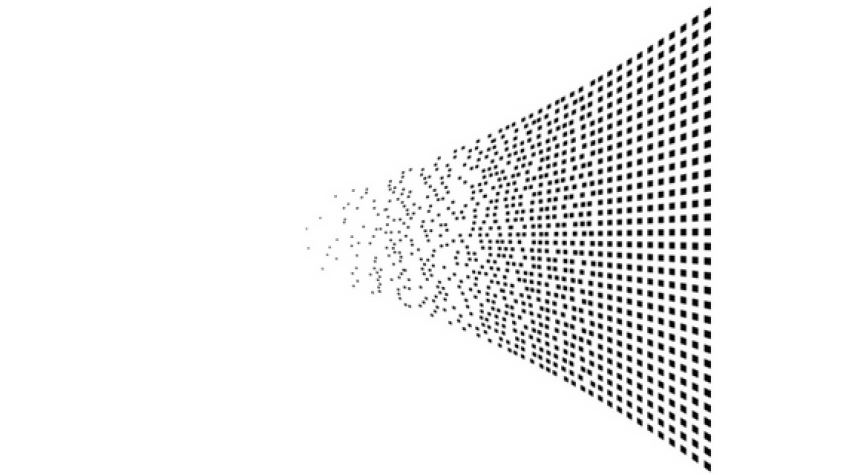
In a recent National Defense Industry Association (NDIA) meeting on advanced manufacturing, data was characterized as “the new ‘oil,’ we need to figure out how to refine it.” On the future of advanced manufacturing at a recent Manufacturing Leadership Council meeting, fellow panelists and I were consistent, “the bottom line is a data-driven environment for manufacturing,” “from experienced-based manufacturing to evidenced-based manufacturing,” “data is fueling everything, we need to learn how to handle it,” and “make data a key manufacturing asset.”
So how are data at the economic center of next-generation advanced manufacturing when manufacturing has been digitizing operations for 30 years? Highly compartmentalized manufacturing line operation and supply chain enterprises are being restructured for operational data interconnectivity and significantly greater overall productivity. For example, dynamic recipe management is enhanced with right-time property data from upstream suppliers. Local product precision is being improved significantly with real-time, in situ qualification.
The production of specialized materials and products with increased value-add customizations are being accelerated, often in smaller lots, with extended upstream and downstream interoperability and global orchestration. For example, sensing/modeling upstream product tolerances and managing equipment maintenance makes it possible to manage downstream tooling with machine configuration management. Zero incident, zero defect manufacturing using far less energy and material offers reinvestment potential. The Clean Energy Smart Manufacturing Innovation Institute (CESMII) has estimated economic savings in U.S. manufacturing at $200 billion over 10 years for a mere 5-10% uptake in Smart Manufacturing practices. Virtual enterprise businesses that can more rapidly form and maximize physical facilities for market opportunity are spurred by business agreements that define selective interoperable data.
While advanced manufacturing needs data in the right form at the right time, industry is presently managing interconnected data to greatest complexity. There is a long list of important methodologies under ‘brand’ labels – big-data analytics, data lakes, data-based modeling, AI, machine learning, etc., that won’t scale or be usable unless “good, understandable” data (i.e. contextualized data) are readily available. Data won’t be available unless business agreements, IP and information security are managed differently. Over 90% of the effort and cost of a data project is just ‘getting’ good data into a useful format. Smart Manufacturing has examples of ‘not smart’ efforts in which over 200 hours are needed to securely integrate just two vendor software products and set up the selection and security of the data to be exchanged (i.e. data interoperability).
One-off networked data interfaces between pairs of systems are already many, complex, and unscalable. As software solutions, IoT devices, and vendor cloud platforms proliferate, control and execution systems using digitized data (OT) and information technology and data systems (IT) are on a trajectory to become larger barriers. Costly reconciliation, synchronization and maintenance of data networks and models go up exponentially as the pairs of interconnections increase. Updating with new technology is difficult at best and the data management structures for making ‘contextualized’ data available for more than one application (i.e. data reusability) are for the most part non-existent. The technology is pretty much out of reach to small and medium companies.
Reaching advanced manufacturing opportunities requires treating data as key assets and new ways to integrate OT and IT in support. Integrated OT/IT properties need to align with new enterprise precision and productivity demands (inclusive of process operation performance improvements) that are far more dynamic and demand responsive. In OT and IT terms this means new ways for OT/IT integration to address data interconnectedness and much greater data availability among many data/modeling and control/execution systems, applications, and platforms together. Smart Manufacturing calls this data/decision centric manufacturing. Data availability and reusability need to support multiple methods and software products (i.e. vendor agnostic data provisioning). Reuse is significantly amplified if there can be repeated use of the ways data and software applications are configured for different applications (i.e., data and application configuration reuse).
Data availability needs to be combined with the ability to manage business agreements about selected data, forms of data access, and the trust and security to execute (i.e., granular business data management) – copying data is not adequate. Importantly, OT/IT integration needs to support a richer definition of the right worker, e.g., operator, engineer, integrator, vendor, etc., integrated into the data and operations loop at the right time with the right access. As data are extended and used within and across enterprises, machines and people need to do what they do best.
Manufacturing has established product and process lifecycle structures and processes, but it does not have analogous structures for data. A new way to think about OT/IT integration then is in terms of the lifecycle of a data item – the data item from generation to end-of-life. In Smart Manufacturing we refer to this as the data/decision centric lifecycle and we use it to organize integrated OT and IT properties.
In OT, digital controls and execution systems typically use IT in a tightly-coupled, OT-modeling form without defining the symbols or modeling constructs so that data can be readily processed in an IT space. In the data/decision-lifecycle view, the formation of parts and materials uses energy and materials in and across line and factory operations, and supply/value chains use data that are orchestrated as flows and transformations in and across discernable events or activities.
Orchestrated data transformations that are integrated with sensor, control and execution systems occur within a repeatable data lifecycle that includes: (1) generation from multiple and heterogeneous data sources, (2) data interconnectivity and its ingestion into a data management structure, (3) data contextualization and inclusion in operational data banks supporting useful reusable data views, (4) business application access and data exchange granularity, (5) composable enterprise workflow applications, (6) end-to-end enterprise workflow execution, and (7) post end-to-end enterprise workflow execution analysis.
Careful OT/IT blending with a data/decision lifecycle view not only addresses these integrated operational data functions, it also transforms OT and IT applications defined by a massive diversity of physical manufacturing assets and operations into a much smaller set of reusable data-model-execution configurations that are similarly applied. OT/IT blending directly aids in distributing controls and operational management across enterprises and naturally provides the constructs in which the smart worker can become integral to enterprise control.
Careful blending also mitigates the challenges of OT and IT as separate approaches – for example, mitigating IT cyber security risk with OT selective data requirements. As a thought-provoking end comment, this data/decision-centric OT/IT integration opens the door to emergent cyber-physical system behaviors that become possible when multiple data and operational systems are more loosely coupled, acting together proactively and reactively.
Comments
that is a very powerful lecture on the advancement of chemical engineering. sir how will the recent materials and technology like nanptechnology and optice affect or relate to chemical enginering? www.chemicalengineeringnob.com