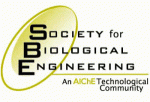
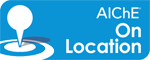
2011 Spring Meeting
The production of clean, potable water is an increasingly critical issue on the planet, and membranes have become a key tool for challenging separations problems. As the level of challenge rises, however, so does the issue of membrane fouling, the coating of membrane surfaces with impurities that reduces their productivity (flux) and also affects their selectivity (rejection). Dr. Benny Freeman of the University of Texas at Austin presented some promising results of his team's efforts to coat membrane surfaces with materials that greatly reduce fouling rates and also allow for more effective cleaning when necessary.
Flexing Their Mussels
One of the first problems in developing a coating for membranes is that by design they tend to be "unsticky." So, an example was taken from one of nature's stickiest creatures, the mussel. Mussels, and their cousins the barnacle, have been the scourge of the shipping world since man first floated a log, as they stick to any underwater surface. They can even stick to Teflon. What is the "bio glue" that allows them this tenacity? It is a variation on dopamine, not quite a polymer, though not the unassociated molecule either.
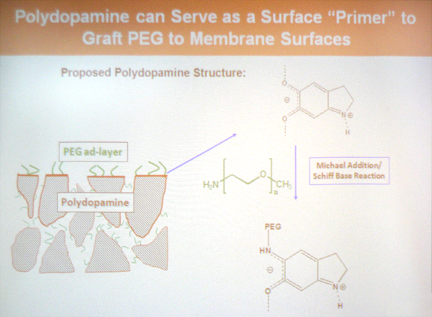
The researchers at Texas University used dopamine that had been reacted at room temperature and slightly alkaline pH in the presence of oxygen for their coating material.They found that the resulting membrane surface was very hydrophilic (water loving). What's more, preliminary tests showed that the coated membrane outperformed uncoated samples when used to treat oily waters such as bilge water, produced water (from hydrocarbon drilling operations), and harbor water.
The Results
The research team has performed scores of experiments over the past few years and has generated very promising results
- Membrane elements of all pore sizes and materials have been coated with very few (if any) failures.
- The coating conforms to existing surface area (no change in surface roughness) and has a surface charge slightly more neutral.
- Pure water flux rates (L/m2) are greater for uncoated membranes at the start of use, but fall off dramatically with hydrocarbon fouling, whereas the coated examples hold their flux rates much more constant. They allow a much higher average flux, and much longer life (and hence production) before fouling.
- Membranes can be coated in situ. This may actually be preferred, as the spacers and other membrane system components will also be coated.
- Additional surface components such as polyethylene glycol (PEG) can be added after coating to further increase the fouling resistance.
- Often, a simple clean hot water rinse and/or backwash can be effective in returning the coated membranes to their original state.
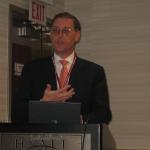
More to Be Done
Research continues to document anti-fouling characteristics for biomaterials and microorganisms themselves (good results so far). Tests are also underway to determine the coating's effect on preventing hardness (calcium) scaling. One of the applications currently in beta testing is with the back washable disc filter of Arkal Filters. There is also the significant challenge of using dopamine itself, which has some nasty toxicity characteristics.
For more information, contact Dr. Benny Freeman at the University of Texas, Austin.