High costs have constantly bedeviled lithium-ion battery developers, making fossil fuels cheaper than alternatives for so long that most people thought the industry had hit a wall and faced the ignominy of a mature technology spending its golden years limping along as yesterday's hot doctoral dissertation. In the past, any researcher who wanted to avoid a failed career left to create a new battery chemistry, leaving lithium-ion to live on in semi-retirement.
Five years ago, during that malaise, 24M Technologies was spun out from parent company A123, and it had the typically low-key MIT and Silicon Valley goal of revolutionizing how lithium-ion batteries were designed and built. Nothing lofty about that.
At the time, co-founder and MIT professor Yet-Ming Chiang said the company would take a “clean sheet” approach and ask the $64,000 question: regardless today's technology, how should you build the perfect lithium-ion battery. After that announcement, the company went into stealth mode and stopped communicating. The tech press was forced to speculate like Cold War Kremlin watchers. That generated lots of speculation — some pretty silly — that went unanswered.
But when 24M decloaked last week and unveiled its new lithium-ion cell, the big surprise was that the chemistry hadn't changed. But the manufacturing process had been altered beyond recognition. So much so that the company confidently said that it had surmounted all of the the long-standing challenges and was now able to make cheap lithium-ion energy storage (see the press release).
The most ground breaking achievement: the battery's electrodes had been completely re-engineered as tiny particles suspended in a liquid, a semi-solid, colloidal suspension that 24M calls a “semisolid battery.” This made other changes possible.
"We’ve reinvented the process,” Yet-Ming Chiang, the Kyocera Professor of Ceramics at MIT and a co-founder of 24M explained in MIT News.
Deeply entrenched problems
What problems did 24M overcome? First of all, lithium-ion battery research had been mired in a legacy trap, which began when Sony created today's technology from its older magnetic tape technology in the 1980s and 1990s, when, after a period of abrupt technological change, it was being phased out and replaced by more sophisticated CDs. Seeing similar process analogies, engineers salvaged the old magnetic tape equipment and adapted it to make the first consumer lithium-ion batteries, which went on to power Sony's blockbuster handheld video cameras. But the problem grew and festered as many of these processes remained deeply entrenched in battery production to this day.
The unnecessary bottlenecks seem obvious now, and according to Chiang, battery production suffered from being too complex, too energy-intensive and too time consuming; ultimately this trifecta of problems blocked any innovation other than simply making the manufacturing line longer. This "big ticket, deep-pockets" solution requires so much upfront capital that small, scrappy startups get stiffed. So it's no surpise that now we're living in the era of the gigafactory (see a sneak peak of the Tesla gigafactory here).
This legacy process — which Tesla's gigafactory will strive to improve — goes like this: a plant spins out long strips of metal foil, and then adds layers of liquid “ink or paint” to form electrodes, Chiang told Greentech Media. That coated foil is dried in not one but a series of ovens before it’s sent off for further processing, including expensive solvents that have to be recovered for reuse on the next foil strip. Although applying the wet slurry is quick, it takes 22 hours to completely dry. Then afterwards, somewhat nonsensically, which always should have been a red flag, a liquid electrolyte is injected into the battery cell, making it wet all over again.
According to Chiang, 24M bypassed all that:
[we started] with a wet electrode that has everything you need in it, all of the steps you'd normally use to make a battery electrode that would take a full day, we can do it in an hour.”
This step allowed 24M to solve an an inter-related problem. Chiang and his team determined that a third of every traditional battery is filled with material that doesn't generate electricity. That includes a binder holding the slurry onto the film, and a large portion of inactive, non-charge materials layered one-on-top of the other inside a cell. They created an architecture that dumped the layering for two adjacent electrodes.
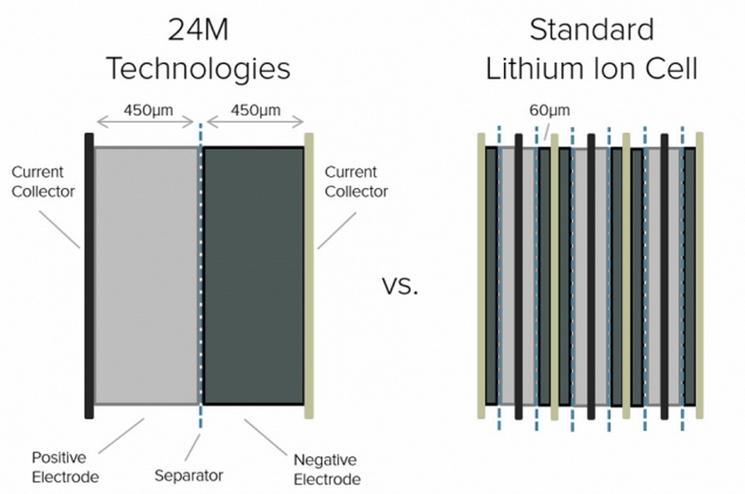
Until now, it hadn't been possible to create electrodes that were thick and would still allow the lithium to be transported fast enough to provide fast charge-discharge characteristics. 24M solved that problem through a a complete reimagining of the size of the charge material within the electrodes.
According to Chiang, “The key concept is reducing tortuosity, ”the state of diffusion in porous materials, like forming the semi-solid materials into complete anodes and cathodes. What we do is provide more line-of-sight paths for the lithium ions to get out of the electrode, rather than provide a tortuous path through a maze of inactive material.”
That’s accomplished in the single-step process by which 24M layers its anode and cathode materials together, with only one electrolyte material in between. It not only lies between the two layers, but it also permeates both of the electrodes. It’s infused into both the cathode and the anode. That’s necessary for the lithium ions to get out of the back of the battery.
Once layered together, these intertwined materials are fixed in permanent position — something that’s possible because 24M’s material isn’t a true liquid. Instead, it has a consistency that, under its own weight, doesn’t deform. It’s foldable, but it’s actually quite dense, like caulk.
The end result is a battery cell that combines high energy capacity and high current density in the same set of materials. At the same time, because all the materials that 24M puts into the process end up in the final product, there’s no need for costly solvents.
When fully implemented, this new process will cut costs by 50% and knock out a battery cell in two and a half minutes. That machine won't take up much space on a factory floor, having been shrunk to the size of a refrigerator.
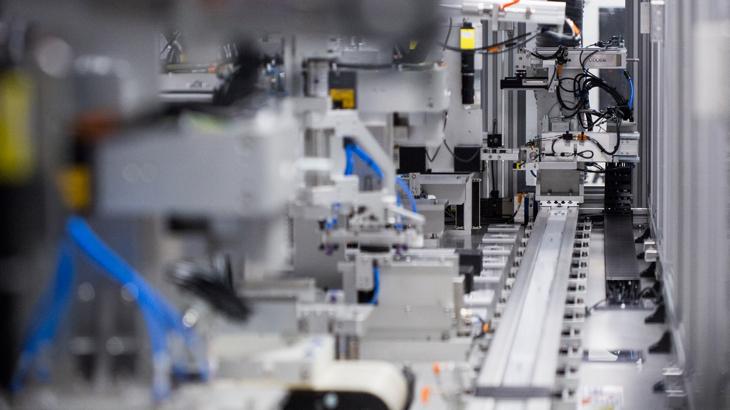
Nobody has ever made a battery this way,” Chiang said to GreentechMedia. 24M has made about 10,000 test cells so far using a “single wet process from beginning to end,” he said. Compared to the multi-stage process used in today’s lithium-ion batteries, it’s “simplified, streamlined, with a lot of metrology, to make it as reliable and bulletproof as we can.”
Increased innovation
Chiang has big plans for 24M. He's looking to raise another $30 million in a third investment round. That money will be used to scale up an even faster fabricator, which is designed to make a cell every ten seconds and drop costs even lower. It will also be dedicated to manufacturing stationary batteries, which will be deployed in power businesses, micro-grids, and utilities.
Chiang sees this newest machine improving to the point where it will produce batteries for $160 a kilowatt-hour. Then, eventually by 2020, prices should fall to $85. The machine will be priced very modestly at $11 million, which will mean that lithium-ion batteries will no longer be a game restricted to deep-pocketed corporations. Smaller startups will finally be able to disrupt the game with newer cutting-edge innovations, fundamentally changing the utility and transporation businesses forever.
Is this a disruptive innovation for renewable energy?
Photos: 24M